Материаловедение на автомобильном транспорте
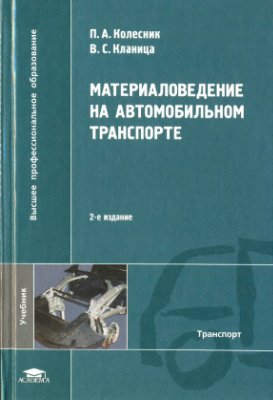
Колесник П.А.
Академия, 2007 г.
3.2. Основные способы производства стали
Сталь — это деформируемый сплав железа с углеродом (менее 2,14%) и другими элементами (марганцем, кремнием, серой, фосфором).
По механическим свойствам и химическому составусталь значительно отличается от чугуна. Она обладает высокими прочностью, вязкостью, пластичностью, легко поддается механической и термической обработкам.
Главным компонентом стали, определяющим ее свойства, является углерод. С увеличением содержания углеродапрочностьстали повышается, а способность к пластической деформации снижается. Исходными материалами для получения стали служит металло-шихта (передельный чугун, металлический лом, металлодобавки), а также добавочные материалы — флюсы (известь, известняк, боксит для наведения шлака), окислители (воздух, кислород, окалина, железная руда как источник монооксида железа FeO).
Раннее было рассмотрено первое звено общего производственного цикла — получение чугуна. Завершают этот циклпроцессы получения стали, которые основаны на окислении (выжигании) в чугуне избытка углерода и других примесей в специальных агрегатах. В начале процесса под действием кислорода образуется монооксид железа FeO, который, реагируя с кремнием, марганцем, фосфором чугуна, образует продукты, переходящие в шлак либо удаляемые с газами. Серу переводят в шлак в виде соединенийCaSи MnS. С углеродом монооксид железа взаимодействует по реакциивосстановления железа и образования С02.
После окислительного процесса проводят раскисление (уменьшают содержание в сталиFeO) с целью снижения окончательной хрупкости металла. Для этого в жидкий металл добавляют раскис-лители — ферросилиций, ферромарганец и алюминий.
Для выплавки стали применяют конвертерный, мартеновский и электросталеплавильный процессы.
Конвертерные способыпроизводства стали подразделяются на бессемеровский и кислородно-конвертерный. Эти способы основаны на использовании конвертера — стального сосуда, футерованного огнеупором и установленного на двух цапфах, которые дают возможность наклонять его для заливки чугуна и выпуска стали.
Процесс получения стали в бессемеровском конвертере заключается в заполнении конвертера жидким чугуном и продувке его воздухом через днище. Преимуществом этого способа и дальнейших его аналогов (томасовский способ, русское бессемерование и т.д.) является высокая производительность при отсутствии потребности в дополнительном топливе. В то же время полученная этим способомсталь имеет повышенное содержание фосфора, серы и азота из воздуха, что делает ее наименее качественной.
При кислородно-конвертерном способепродувка жидкого чугуна осуществляется технически чистым кислородом.
Кислород подают в конвертер через вертикальную трубчатую водоохлаждаемую фурму, не доходящую до металлической ванны. При этом развивается высокая температура, что дает возможность перерабатывать чугун практически любого химического состава, а также добавлять в чугунскрап (железный лом).
Весь процесс — загрузка (лома, чугуна, флюсов), продувка, раскисление, слившлака и выпускметалла — занимает менее 1 ч.
Выплавка стали в кислородномконвертере отличается достаточно высокой точностью получения заданного содержания углерода при низком содержании вредных примесей фосфора и серы. Этот способ является наиболее перспективным. Он позволяет снизить затраты энергии на 27 % по сравнению с мартеновским способом.
Мартеновским способомсталь выплавляют в пламенных печах, в которые загружают чугун, стальной лом (скрап), железную руду и известняк (скрап-процесс) либо жидкий чугун, железную руду и известняк (рудный процесс). Топливом служат мазут и горючие газы.
Процесс плавки в мартеновской печи сводится к окислительному взаимодействию при высокой температуре материалов, загруженных в печь, и газовой среды.
Серьезным недостатком мартеновского процесса получения стали является его продолжительность (7... 10 ч) и значительный расход топлива. По этой причине метод не выдерживает конкуренцию с более современными технологиями. Выплавка стали мартеновским способом в настоящее время не имеет распространения и будет сокращаться, уступая место выплавке стали кислородно-конвертерным и электросталеплавильным способами.
Получение стали в электрических печах основано на плавлениишихты при использовании электрической энергии. Отсутствие окислительного пламени и доступа воздуха в электрические печи позволяет лучше управлять процессомплавки и получать высококачественную сталь точно заданного состава.
Этот способ применяют для выплавки высококачественных углеродистых и легированных сталей, сплавов на основе никеля и кобальта, для плавки которых требуется высокая температура.
В дуговой печи электрическая дуга образуется между опущенными через свод графитовыми электродами и шихтой. Загрузка печи осуществляется через окно, а выпуск готового металла — через летку и желоб. Для наклона и сливаметалла и шлака печь оборудована роликами с электроприводом.
В электропечи загружают для переплава стальной лом, железную руду (для окисления примесей) и флюсы, а для раскисления вводят легирующие добавки. С целью экономии электроэнергии и увеличения производительностичугун применяют весьма редко.
Разливка сталив слитки различной формы является последней операцией при производстве ее перечисленными способами. Полученную стальсливают из сталеплавильной печи в разливочный ковш, имеющий в дне отверстие, закрываемое специальной огнеупорной пробкой.
Металл, залитый в ковш, выдерживают в течение 10 мин для выравнивания его состава и выделения газов и неметаллических включений. После этого ковш подают на разливку. Разливку стали ведут либо в изложницы, либо в непрерывные слитки на машине непрерывного литья заготовок (МНЛЗ).
Изложницы представляют собой чугунные или стальные сосуды определенной формы, позволяющие получать слитки квадратного, прямоугольного, многоугольного или круглого сечения в зависимости от назначения.
При непрерывной разливке сталь из разливочного ковша через промежуточный ковш равномерной струей заливается в кристаллизатор МНЛЗ, представляющий собой короб, охлаждаемый проточной водой. Здесь быстро формируются стенки слитка, откуда он вытягивается валками с определенной скоростью, равной скорости кристаллизации. Ниже валков слитоквыходит полностью затвердевшим, и от него кислороднойгорелкой отрезаются заготовки необходимой длины, которые далее автоматически направляются на транспортные тележки.
Непрерывная разливка стали обеспечивает высокое качество слитков, уменьшает потериметалла и повышает производительность труда.
Качество стали повышается при разливке ее в вакууме. Метод вакуумированиязаключается в удалении растворенных газов из стали под действием вакуума при обработкестали в специальных ковшах перед ее разливкой в изложницы или до разливочной машины. В результате сталь становится более пластичной и прочной.
Разливка стали в вакууме применяется при получении высококачественных и легированных сталей. Для реализации этого способа требуется применение дополнительного сложного оборудования.
Описанный традиционный двухстадийный способ производства стали, при котором вначале в доменной печи получают чугун, из которого затем выплавляют сталь, является трудоемким и энергоемким. Для него требуется использование кокса, стоимость которого составляет более 50 % в затратах на получение чугуна.
В последние годы разработана и осуществлена принципиально новая бездоменная технология получения стали. В нашей стране такая технология впервые освоена на Оскольском электрометаллургическом комбинате. Суть ее заключается в приготовлении из железорудного концентрата окисленных окатышей, их металлизации и последующей выплавке из металлизованных окатышей стали. Железную руду вначале обогащают — содержание железа увеличивается с 34 до 74 %. К полученному концентрату добавляется глинистое вещество, которое во вращающихся барабанах (окомкователях) склеивает частицы концентрата в комочки — сырые окатыши диаметром 1... 2 см. Для придания окатышам необходимой прочности их обжигают на конвейерной машине.
Далее окатыши направляются в шахтныеустановки металлизации, где и происходит прямое восстановление железа. Шахты представляют собой высокие (64 м) цилиндрические башни с внутренним диаметром 5 м. К нижней части башни подводится горячий (500...800 °С) восстановительный газ. Он представляет собой природный газ, очищенный от серы и подвергнутый углекислотной конверсии, в результате которой метан и другие углеводороды превращаются в монооксид углерода и водород (СО и Н2), являющиеся сильными восстановителями. При продувке СО и Н2 легко восстанавливают железо, и окисленные окатыши превращаются в металлизованные с содержанием более 90 % Fe.
Металлизованные окатыши подают в электроплавильные дуговые печи, в которых получают высококачественную сталь. Слитая в ковшисталь подвергается вакуумированию, продувкеаргоном и обработке рафинирующими порошками, отчего ее качество еще более повышается.
Бездоменная металлургия позволяет отказаться от постоянно дорожающего и становящегося все более дефицитным кокса, от сложного хозяйства коксохимических, агломерационных и доменных цехов. Полученная сталь содержит значительно меньше серы и фосфора, попадающих в обычную сталь из руды и чугуна. Бездоменная металлургия выгодно отличается и в экологическом отношении, так как исключает загрязнение окружающей среды сернистыми газами и другими вредными веществами.
Перспективным направлением развития металлургической промышленности является порошковая металлургия, в процессе которой получают спеченные материалы. Порошковая металлургия — это совокупность методов изготовления порошков металлов и ме-таллоподобных соединений, полуфабрикатов и изделий из них без расплавления основного компонента. Методами порошковой металлургии можно получать материалы из металлов, не смешивающихся в расплавленном виде (например, порошковые сплавы железо—свинец, вольфрам—хром и др.), материалы с особой структурой и характеристиками (например, многие пористые металлы для подшипников), медно-графитовые щетки для электрогенераторов и электродвигателей.
Уже в настоящее время большую часть тугоплавких металлов производят методом порошковой металлургии. Важным преимуществом порошковой металлургии является и то, что спекаемые материалы можно производить как в виде заготовок и полуфабрикатов, так и готовых изделий, не требующих дальнейшей обработки резанием. В частности, к таким изделиям относятся шестерни для зубчатых передач автомобилей.
По сравнению со всеми другими Методами получения деталей — литьем, обработкой давлением, резанием и т.д. — изготовление деталей из спеченных материалов требует наименьших трудовых затрат, заводских площадей, оборудования. Автомобильная промышленность является одним из основных потребителей спеченных материалов.
Применение спеченных материалов позволяет повысить износостойкость, долговечность, коррозионную стойкость изделий, а также снизить трудоемкость и металлоемкость машин и механизмов.
Технология производства спеченных материалов включает в себя следующие операции: получение исходных металлических порошков и приготовление из них шихты с заданными химическим составом и технологическими характеристиками; формование порошков или их смесей в заготовки с заданными формой и размерами (главным образом прессованием); спекание, т.е. температурнуюобработку заготовок при температуре ниже плавления всего металла или основной его части. Иногда спекают порошки, засыпанные в соответствующие формы, избегая таким образом операции формования. В ряде случаев формование и спекание объединяют в одну операцию так называемого «горячего прессования» — обжатия порошков при нагреве.
Порошки получают механическим или физико-механическим методом. К первым относят измельчениеметаллов в вихревых,. вибрационных и шаровых мельницах или более производительное и экономичное распыление жидких металлов; ко второму — химическое восстановлениеметаллов из оксидов, электролиз расплавленных солей, карбонильный метод й метод гидрогенизации. Основной методформования — это прессование в пресс-формах из закаленной стали под давлением 200... 1000 МПа.
Спекание проводят в защищенной среде (водород; атмосфера, содержащая соединение углерода; вакуум; защитные засыпки) при температуре, составляющей около 70...85 % температуры плавления, а для многокомпонентных сплавов — при температуре несколько выше температурыплавления наиболее легкоплавкого компонента.
В методе горячего прессованияизделия после формовки подвергают спеканию. Ленту, проволоку и некоторые другие изделия из металлических порошков получают методом прокатки.
Методам порошковой металлургии присущи некоторые недостатки, сдерживающие ее развитие. Недостатками являются сравнительно высокая стоимость металлических порошков; необходимость спекания в защитной атмосфере; трудность изготовления в некоторых случаях изделий и заготовок больших размеров; сложность получения металлов и сплавов в компактном беспористом состоянии.