Справочник термиста ремонтной службы
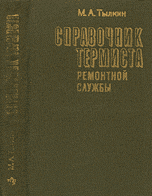
Тылкин М.А.
Металлургия, 1981 г.
Особенности износа деталей металлургического оборудования
Оборудование агломерационных цехов
Среди оборудования агломерационных цехов, подверженного интенсивному изнашиванию, следует в первую очередь назвать элементы ротора эксгаустера, спекательных и обжиговых тележек, питателей, дробильного оборудования и др. Как правило, износ вызывается истиранием рудой и агломератом, обладающими высокими абразивными свойствами. Большое влияние на истирание оказывают насыщенные абразивной пылью газ и воздух и повышенные температуры.
Ротор эксгаустера. Основными изнашивающимися элементами ротораэксгаустера являются рабочие лопатки и прилегающие к ним плоскости основного и покрывающего* дисков Износ лопаток наблюдается со стороны входа потока насыщенного твердыми
частицами газа в месте прилегания их к основному диску. В этих участках образуются сквозные свищи, расположенные вдоль лопатки и плавно сужающиеся вдоль потока. Основной диск изнашивается в участках прилегания к нему полок лопаток. В теле диска образуются выемки, сечение которых уменьшается в направлении от входа к выходу потока. Наиболее интенсивному изнашиванию подвержена часть диска, заключенная между лопаткой и ступицей. Вследствие одновременного действия двустороннего потока газов Износ вызывает резкое утонение тела диска и снижение его прочности. Покрывающий диск изнашивается в участках прилегания тыльной стороны лопатки с увеличением выработки к выходу потока. Входящий поток газа изнашивает также ступицу и защитное кольцо вала.
Агломерационная и обжиговая машины. Интенсивному изнашиванию подвергаются детали спекательных и обжиговых тележек агломерационных машин — корпус, надставка, колосники, ходовые ролики, уплотнительные пластины. Условия эксплуатации корпусов, надставок и колосников осложняются нестационарным тепловым режимом.
Износу и развитию трещин способствует газовая коррозия, особенно при наличии в среде сернистых соединений. Как правило, причинами замены спекательных и обжиговых тележек являются прогиб корпуса, обгорание полок и появление многочисленных мелких разгарных трещин. У колосников наибольшему изнашиванию подвергаются верхние рабочие приливы. Вся поверхностьколосников испытывает интенсивное окисление. Если в первый период эксплуатации поверхность под окалиной изнашивается равномерно, то в последующем она становится неровной, изъеденной. Ходовые ролики и уплотнительные пластины эксплуатируются в основном в стационарном температурном режиме. Износ их связан с трениемметалла о металл. Износ уплотни-тельных пластин равномерен по всей поверхности. Величина предельного износа не превышает 5 мм. Срок службы достигает трех лет. Износ ходовых роликов менее равномерен. поверхность катания изнашивается на величину до 5 мм. Изнашивание реборд отмечается лишь на участках, примыкающих к поверхности катания, причем величина износа мала (<1 мм). Износ
носика ножа для срезания агломерата достигает 50 мм. По остальной длине ножа величина износа менее значительна, однако превышает 5 мм. Срок службы ножей обычно составляет 2—3 мес.
Дробильное оборудование. Изнашивание деталей дробильного оборудования происходит в результате истирающего воздействия измельчаемых руды или известняка. В ряде случаев изнашивание сопровождает износ нижнего бандажа четырехвалковой коксовой дробилки более значителен в средней части по длине; здесь его величина достигает 10 мм по диаметру до переточки и 160 мм с учетом переточек. На участках, близких к торцам, Износ относительно невелик. В квадрате отбойного фартука одновалковой дробилки отмечается интенсивный равномерный Износ рабочей плоскости. Величина износа достигает 6—8 мм.
В молотковых дробилках наибольший Износ наблюдается на молотках, колосниках, дробящих плитах, а также уплотняющем диске ротора. Величина износамолотков достигает 50 мм. Износ неравномерен. Более интенсивно изнашиваются участки, примыкающие к боковой поверхности рабочей части молотка. Неравномерно изнашиваются и колосники. Максимальный износ, достигающий 40 мм, наблюдается в средней части длины колосника. Ближе к торцам интенсивность изнашивания резко уменьшается и на участках, не соприкасающихся с дробимым материалом, Износ практически отсутствует. Износ уплотняющего диска ротора вызывается в основном потоками запыленного воздуха. Изнашивается преимущественно наружная коническая поверхность на длине 100 мм. Как правило, величина износа не превышает 3 мм. Дробящие броневые плиты испытывают интенсивные удары кусков известняка. Износ их неравномерен и весьма значителен.
В валковых дробилках наибольшему изнашиванию подвергаются бандажи гладких валков и зубья зубчатых валков. бандажи гладких валков в процессе эксплуатации испытывают давление и истирающее воздействие породы, зубья зубчатых валков работают на удар и истирание. Характер износа дробильной плиты и зубьев звездочки одновалковой дробилки показан на рис. 1.24. Износплиты распространяется на глубину до 8 мм по выступам и до 5 мм по впадинам. В звездочках изнашивается выступающая часть зубьев на глубину 5 мм.
В конусныхдробилках интенсивному изнашиванию подвергаются в основном футеровочные плиты подвижного и неподвижного конусов, приемная воронка и другие элементы. Нагрузки носят, как правило, ударный характер. Максимальный Износ рабочей поверхности неподвижного дробящего конуса отмечается в узкой части, а подвижного — в широкой. Износ боковой поверхности приемной воронки крайне неравномерен. Величина износа по высоте колеблется в широких пределах и в центральной части превышает 25—30 мм, т. е. более 50% полной толщины стенки воронки. Срок службы воронки при изготовлении ее из стали 110Г13Л достигает 1,5 года.
Питатели. Элементы ленточных и пластинчатых питателей подвергаются интенсивному абразивному изнашиванию. Более других деталей изнашиваются броневые плиты пластинчатых и тарельчатых питателей, ножи тарельчатых питателей, приводные и холостые звездочки, ходовые колеса. Изнашивание приводной звездочки пластинчатого питателя происходит в основном по впадине; Износ характеризуется значительной неравномерностью и интенсивностью. Так, Износ участков, прилегающих к выступам, достигает 15 мм; в то же время величина износа центра впадины не превышает 3 мм. Более равномерен Износ обода ходового колеса. Износ отмечается лишь по поверхности катания; величина его составляет 10 мм. Реборды практически не изнашиваются (за исключением участков, непосредственно примыкающих к поверхности катания, которые изнашиваются на небольшую вели-
скипов, атмосферных клапанов, броневых плит тракта перемещения шихтовых материалов, подбункерного оборудования, фурменных приборов, машин для обслуживания чугунной и шлаковой леток и фурм Как правило, Износоборудования здесь, как и в агломерационных цехах, вызывается истирающим действием руды и агломерата Однако большая роль принадлежит и насыщенному абразивной пылью колошниковому газу, вырывающемуся из рабочего пространства доменной печи Повышенные температуры, нестационарный тепловой режим, газовая эрозия — все эти факторы также стимулируют Износ элементов оборудованиядоменных цехов
Загрузочное устройство Загрузочное устройстводоменной печи работает в очень тяжелых условиях Одним из первых выходит из строя засыпной аппарат Работочаши, которое происходит в результате воздействия шихты, ссыпающейся при загрузке доменной печи
Возникновения сквозных продувов конусов и чаш в участках, расположенных значительно выше контактных поверхностей
Образования неплотностей, выщербин, трещин, свищей и, как следствие этого, продувов на контактных поверхностях и связанных с ними сквозных отверстий в теле конусов и чаш
На рис 1 25—I 27 показан Износ отдельных деталей загрузочного устройства доменной печи На отдельных участках, расположенных выше контактной поверхности (у места падения шихты), толщина тела большого конуса уменьшилась более чем на 60% В еще большей степени износилась контактная поверхность. Во многих участках по ее окружности образовались в контакте рабочего и опорного валков. Кроме того, рабочие валки находятся в контакте значительно дольше, чем опорные валки. Величина износа рабочих и опорных валков определяется главным образом давлением прокатки. Как правило, величина износа валков по клетям следует за изменением давления прокатки.
Важным фактором, определяющим величину износа рабочих валков, является температура прокатываемых полос и длительность контакта полосы с поверхностью валков. Часто наблюдается разгар поверхности. Дефекты валков станов холодной прокатки делят на две группы: дефекты, возникающие при изготовлении, и дефекты, возникающие при эксплуатации. В табл. 1.7 указан ряд характерных дефектов, известных из практики изготовления и эксплуатации валков холодной прокатки.
При рассмотрении причин выхода валков станов холодной прокатки из строя анализируют качественное состояние валков, условия, при которых возникают повреждения, и режимы эксплуатации валков на станах.
7. Технология и режимы термической обработки со сквозным прогревом деталей машин
Детали оборудования металлургических цехов и станочного оборудования
Термической обработке со сквозным прогревом подвергают большое число деталей металлургических, горных, строительных и других машин: разнообразные валы и оси, шестерни, зубчатые муфты и втулки, ролики и звенья цепей, ножи, правильные ролики, элементы подшипников и т. д. Срок службы подавляющего большинства деталей за счет применения термической обработки со сквозным прогревом возрастает в несколько раз.
В табл. VII.36—VI1.42 приведены режимы термической обработки ряда деталей оборудования агломерационных, доменных, сталеплавильных и прокатных цехов, деталей станков, элементов горныхмашин и др.
Более подробно остановимся на особенностях термической обработкипрокатных валков, крановых колес, деталей из высокомарганцовистой стали и др.
Валки горячей прокатки
Валки горячей прокатки изготавливают из различных сталейлитьем или ковкой. Для получения необходимой твердости и структуры литые валки подвергают сложной термической обработке.
Структура металла литых валков из стали марок У12 и 150ХНМ должна состоять из тонкопластинчатого перлита и избыточных карбидов цементитного типа, из сталей 60ХГН и 80ХГН — из тонкопластинчатого перлита, а в структуре валков из сталей 50ХН и 60ХН допускается присутствие ферритной сетки по границам зерен. Режим термической обработки литых валков из стали 60ХН, по данным ММК, следующий: посадка в печь при температуре 250° С, выдержка 4 ч; нагрев до 650° С со скоростью 40° С/ч, выдержка 3—5 ч; нагрев до 950° С со скоростью 60° С/ч, выдержка 18—22 ч; охлаждение на воздухе до 550—600° С; нагрев до 850—870° С со скоростью 80° С/ч, выдержка 14—18 ч, охлаждение на воздухе до 400—500° С; нагрев до 600° С со скоростью 80° С/ч, выдержка 12 ч, охлаждение с печью до 200° С со скоростью 25° С/ч. Длительность термической обработки 110 ч.
Таким образом, для литых валков из стали 60ХН применяют двойную нормализацию с нагревом в первой ступени до 950° С, а во второй до 850—870° С. При такой термической обработке все избыточные карбиды при нагреве в первой ступени переводятся в твердый раствор, устраняется дендритная неоднородность, образовавшаяся в результате первичной кристаллизации стали, а во второй ступени в результате получения мелкого исходного аустенитного зерна обеспечивается получение сорбитной или перлито-сорбитной структуры.
Литые валки из стали марки 150ХНМ на ММК подвергают следующей термической обработке:
а) на твердость НВ300—330 —
тройная нормализация при температурах 1050, 820, У00вС с последующим отпуском при 600° С;
б) на твердость НВ260—290 — нормализация при 1050° С с последующим отжигом при 620° С.
Кованые стальные валки в зависимости от марки стали подвергают следующим видам термической обработки: из сталей 50 и 55— нормализации и отпуску; из сталей 40ХН и 9Х — закалке и отпуску; из сталей 55Х, 60ХГ, 50ХН и 60ХН — нормализации и отпуску или, по требованию заказчика, закалке и отпуску. твердостьбочки валков в зависимости от марки стали и режима термической обработки должна составлять НВ179—429.
На УЗТМ валки куют с одной осадкой при степени укова не менее 3. Горячие поковки передают на термическую обработку. Поковки из углеродистых и низколегированных сталейпроходятнормализацию с отпуском по определенному режиму. Их нагревают до температурынормализации 830—870° С и выдерживают после выравнивания температуры в течение времени, определенного из расчета 0,6 ч на 100 мм; затем охлаждают на воздухе до 250—550° С. Температураотпуска 580—660° С, продолжительность выдержки из расчета 1,2 ч на 100 мм. охлаждение после отпуска: до 400° С со скоростью 40—60° С/ч, дальнейшее охлаждение до 250—300е С со скоростью 20—30° С/ч (в зависимости от сечения поковки). В тех случаях, когда валкипроходят вторую нормализацию после обдирки, выдержку при отпуске рассчитывают следующим образом: 1 ч на 100 мм — для валков из углеродистых и низколегированных сталей и 1,9 ч на 100 мм — для валков из сталей 50ХН и 60ХН.
На НКМЗ кованые валки изготавливают в основном из сталей 50, 55, 55Х, 40ХН, 60ХН, 50ХН и 60ХГ. Ковку ведут с одной осадкой слитка при степени укова по бочке не менее 2,5—3. Поковки на термическую обработку (в основном нормализация с отпуском) поступают в горячем состоянии с температурой на поверхности минимального сечения не ниже 350° С. При первом переохлаждении до 300—350° С после выравнивания температуры их выдерживают из расчета 1 ч на 100 мм, а затем нагревают до 840—860° С. Выдержка при 840—860° С составляет 0,5 ч на 100 мм сечения. Охлаждают поковки на воздухе до температуры 300—350° С. Для равномерного охлаждения их периодически кантуют. При достижении температуры 300—350° С поковки помещают в печь и выдерживают при этой температуре из расчета 2 ч на 100 мм сечения. Температураотпуска 590—610° С, продолжительность выдержки 4 ч на 100 мм сечения. охлаждение после отпуска ведут со скоростью 40° С/ч до температуры 400° С и 20° С/ч до температуры 100° С.