Справочник молодого электросварщика по ручной сварке.
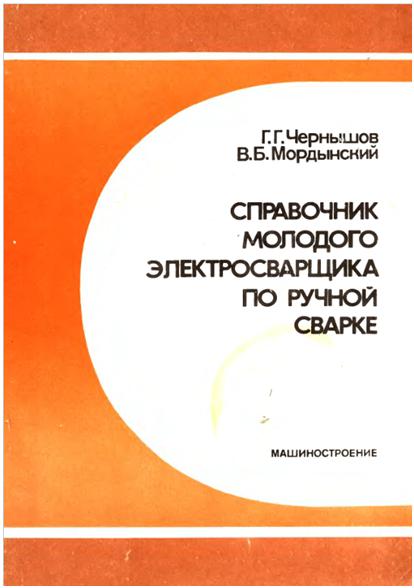
Г.Г.Чернышов, В.Б.Мордынский.
Машиностроение, 1987 г.
Газовая сварка основана на плавлении свариваемого и присадочного металлов высокотемпературным газокислородным пламенем. В качестве горючего для сгорания в кислороде применяют ацетилен, водород, пропан-бутановую смесь, пары керосина, бензина, природный, светильный, нефтяной, коксовый и другие газы.
Термитная сварка состоит в том, что свариваемые детали помещают в огнеупорную форму, а в установленный сверху тигель засыпают термит — порошкообразную смесь алюминия с железной окалиной. При горениитермита развивается высокая температура (более 2000 °С), образуется жидкий металл, который при заполнении формы оплавляет кромки свариваемых изделий, заполняет зазор, образуя сварной шов.
Электрошлаковая сварка основана на плавлении свариваемого и присадочного металлов теплотой, выделяемой при прохождении электрического тока через расплавленный шлак в период установившегося процесса сварки.
В начале процесса возникает дуга, которая, расплавив небольшое количество флюса, шунтируется, прекращается горение дуги и начинается прохождение тока через расплавленный шлак
Электрошлаковую сварку классифицируют по виду электрода, наличию колебаний электрода, числу электродов с общим подводом сварочного тока.
По виду электрода электрошлаковая сварка делится на сварку проволочным, пластинчатым электродом и плавящимся мундштуком; по наличию колебанийэлектрода — без колебаний и с колебаниями электрода; по числу электродов с общим подводом сварочного тока — одноэлектродную, двухэлектродную и много электродную.
Плазменная сварка основана на пропускании электрического тока большой плотности через газовую среду, находящуюся под некоторым давлением, в результате чего газ получает ионизированное состояние, называемое плазмой. температура плазменной струи достигает 50 ООО °С. Плазменную сварку можно выполнять с поперечными, продольными и сложными колебаниями плазменной
струи, а также без колебаний плазменной струи.
Электронно-лучевую сварку выполняют в камерах с разрежением до 133Х (10~4—10~6) Па. Теплота выделяется в результате бомбардировки поверхностиметалла электронами, имеющими большие скорости; анодом служит свариваемая деталь, катодом — вольфрамовая спираль.
Электронно-лучевую сварку можно выполнять без колебаний и с колебаниями электронного луча. По направлению колебаний различают электронно-лучевую сварку с продольными, поперечными, вертикальными и сложными колебаниями электронного луча.
Лазерная сварка осуществляется мощным световым лучом, получаемым от специальных твердых и газовых излучателей. Вакуум при сваркелазером не нужен, и ее можно выполнять на воздухе даже на значительном расстоянии от генератора.
Контактная сварка состоит в разогреве и расплавлении места соединения теплотой, выделяемой при прохождении электрического тока через контактируемые места свариваемых деталей; при приложении в этом месте сжимающего усилия образуется сварное соединение. По форме сварного соединения различают точечную, шовную, стыковую, рельефную, шовно-стыковую контактную сварку. Точечная сварка в свою очередь подразделяется на одно-, двух- и многоточечную. Стыковая сварка по характеру протекания процесса делится на сварку с прерывистым и непрерывным оплавлением и сварку сопротивлением.
Контактную сварку можно выполнять постоянным, переменным и пульсирующим током. По виду источника энергии контактная сварка подразделяется на конденсаторную, энергией, накопленной в магнитном поле и в мотор-генераторной системе и др.
Диффузионную сварку осуществляют в вакууме за счет взаимной диффузииатомов контактирующих частей при относительно длительном воздействии повышенной температуры и при незначительной пластической деформации.
Газопрессовая сварка основана на нагреве концов стержней или труб, по всей длине окружности многопламенными горелками до пластического состояния или плавления и последующего сдавливания стержней внешним усилием.
Ультразвуковая сварка основана на совместном воздействии на свариваемые детали механических колебаний ультразвуковой частоты и небольших сжимающих усилий.
Сварку трением осуществляют при вращении одного из стержней и соприкосновении его торца с торцом закрепленного стержня; концы стержней разогреваются и с приложением осевого усилия свариваются.
Холодная сварка основана на способности схватывания металла при значительном давлении.
§ 2. ОСНОВНЫЕ ТИПЫ СВАРНЫХ СОЕДИНЕНИЙ
Сварным соединением называют участок конструкции, в котором отдельные ее элементы соединены с помощью сварки. В сварное соединение входят сварной шов, прилегающая к нему зона основного металла со структурными и другими изменениями в результате термического действия сварки (зона термического влияния) и примыкающие к ней участки основного металла.
Сварной шов представляет собой закристаллизовавшийся металл, который в процессесварки находился в расплавленном состоянии.
Свойства сварного соединения определяются свойствамиметалла самого шва и зоны основного металла, прилегающего к шву, — зоны термического влияния. Необходимо учитывать и некоторую часть основного металла, прилегающую к зоне термического влияния и определяющую концентрацию напряжений в месте перехода от металла шва к основному металлу и пластических деформаций в зоне термического влияния, что отражается на характере и распределении усилий, действующих в сварном соединении.
По форме сопряжения свариваемых элементов можно выделить следующие основные типы сварных соединений: стыковые (рис. 1,а), тавровые (рис. 1, б,в), угловые (рис. 1, г), нахлесточные (рИС. 1,0).
Сварные швы подразделяют по форме поперечного сечения на стыковые (рис. 2, а) и угловые (рис. 2,6). Разновидностью этих типов являются швы пробочные (рис. 2,в) и прорезные (рис. 2,г), выполняемые в нахлесточных соединениях. По форме в продольном направлении различают швы непрерывные и прерывистые.
С помощью стыковых швов образуют в основном стыковые соединения (см. рис. 2,а), с помощью угловых швов — тавровые, крестовые, угловые и нахлесточные соединения (см. рис. I, б—д), с помощью пробочных и прорезных швов могут быть образованы нахлесточные и иногда тавровые соединения.
Стыковые швы, как правило, выполняют непрерывными; отличительным признаком для них обычно служит формразделки кромок соединяемых деталей в поперечном сеченни. По этому признаку различают следующие основные типы стыковых швов: с отбортовкой кромок (рис. 3,а); без разделки кромок — односторонние и двусторонние (рис. 3,6); с разделкой одной кромки — односторонней, двусторонней; с прямолинейной или криволинейной формойразделки (рис. 3,в); с односторонней разделкой двух кромок; с V-образной • разделкой (рис. 3,г); с двусторонней разделкой двух кромок; Х-образной разделкой (рис. 3,д). Разделка может быть образована прямыми линиями (скос кромок) либо иметь криволинейную форму (U-образная разделка, рис. 3,е).
Угловые швы различают по форме подготовки свариваемых кромок в поперечном сечении и сплошности шва по длине.
По форме поперечного сечения швы могут быть без разделки кромок (рис. 4,а), с односторонней разделкойкромки (рис. 4,6). с двусторонней разделкой кромок (рис. 4,в). По протяженности угловые швы могут быть непрерывными и прерывистыми, с шахматным и цепным расположением отрезков шва. Тавровые, нахлесточные и угловые соединения могут быть выполнены отрезками швов небольшой протяженности — точечными швами.
Пробочные швы по своей форме в плане (вид сверху) обычно имеют круглую форму и получаются в результате полного проплавления верхнего и частичного проплавления нижнего листов — их часто называют электрозаклепками, либо путем проплавления верхнего листа через предварительно проделанное в верхнем листе отверстие.
Прорезные швы, обычно удлиненной формы, получают путем приварки верхнего (накрывающего) листа к нижнему угловым швом по периметру прорези. В отдельных случаях прорезь может заполняться и полностью.
При высоком отпуске сварочные напряжения снимаются вследствие того, что при температуре 600°С пределтекучестиметалла близок к нулю и материал практически не оказывает сопротивления пластической деформации, в процессе которой происходит снижение (релаксация) сварочных напряжений.
В ряде случаев можно ограничиться высоким отпуском отдельных элементов конструкции. Так, при изготовлении сферических резервуаров для хранения различных продуктов ограничиваются только отпуском лепестков с приваренными люками. Отпуск отдельных узлов применяют также при изготовлении сварных рам тележек вагонов и локомотивов. Такие операции значительно проще, чем Отпуск всей конструкции, и, как показал опыт, обеспечивают требуемую эксплуатационную надежность.
Высокий Отпуск является дорогой операцией, удлиняющей технологический процесс изготовления конструкции, и его следует применять в действительно необходимых случаях. Если механическая обработка проводится на детали, не прошедшей отпуска, то в связи с перераспределением напряжений может произойти изменение ее размеров. В большинстве случаев при сваркеизделий из стали с повышенным содержанием углерода и легирующих элементов можно ограничиться только предварительным местным или общим подогревом и не проводить последующей термообработки.
Аргонодуговая обработка. Расплавление участка перехода от шва к основному металлу неплавящимся электродом в аргоне нарушает равновесие внутренних сил напряженного поля вследствие перехода части металла в жидкое и пластическое состояние. Естественно, что при кристаллизации расплавленного металла будут вновь возникать напряжения, однако они сравнительно малы, так как количество этого металла во много раз меньше, чем количество металла шва. Расплавление небольшого количества основного металла и металла шва приводит к уменьшению напряжений на 60—70%. Получаемый при этом плавныйпереход от шва к основному
металлу способствует значительному повышению прочности сварных соединений особенно при переменных нагрузках.
Проковка металла шва и околошовной зоны. Сварочные напряжения могут быть сняты почти полностью, если в шве и околошовной зоне создать дополнительные пластические деформации. Это достигается проковкой швов. Проковку проводят в процессе остывания металла при температурах 450°С и выше либо от 150°С и ниже. В интервалетемператур 400—200°С в связи с пониженной пластичностьюметалла при его проковке возможно образование надрывов. Специальный нагрев сварного соединения для выполнения проковки, как правило, не требуется. Удары наносят вручную молоткоммассой 0,6—1,2 кг с закругленным бойком или пневматическим молотком с небольшим усилием. При многослойной сварке проковывают каждый слой, за исключением первого, в котором от удара могут возникнуть трещины. Этот прием применяют для снятия напряжений при заварке трещин и замыкающих швов в жестких конструкциях. Проковка сварного соединения также способствует повышению усталостнойпрочности конструкции.
Термическая правка. При термической правке нагрев проводят газокислородным пламенем либо электрической дугой неплавящимся электродом. температура нагрева деформированного участка при термической правке составляет 750— 850°С Нагретый участок стремится расшириться, однако окружающий его холодный металл ограничивает возможность расширения, в результате чего возникают пластические деформации сжатия. После охлаждения линейные размеры нагретого участка уменьшаются, что приводит к уменьшению или полному устранению деформаций.
Для правки сварных конструкций требуется определенный навык. Поэтому, если в производственных условиях неизбежна правка конструкций, то для выполнения термической правки необходимо специально обучать рабочих.
§ 25. сварка ЧУГУНА
В современном машиностроении, станкостроении, металлургической и других отраслях промышленностичугун получил широкое распространение в качестве конструкционного материала благодаря ряду преимуществ, среди которых простая и дешевая технология изготовления чугунных изделий, хорошие литейные свойства, высокая износостойкость, малая чувствительность к концентрации напряжений, способность гасить вибрацию, невысокая стоимость, хорошая обрабатываемость режущим инструментом. К недостаткам чугуна следует отнести низкую прочность серого чугуна и практически полное отсутствие пластичности.
Состав и свойства. чугуна ми называют сплавы железа с углеродом, содержание которого превышает 2%. В этих сплавах присутствует также кремний и некоторое количество марганца, серы и фосфора, а иногда и другие элементы, вводимые в качестве легирующих добавок для придания чугуну определенных свойств (никель, хром, магний и др.).
В зависимости от структурычугуны подразделяют на белые и серые. В белых чугун ах весь углеродсвязан в химическое соединениекарбид железа РезС — цементит. В серых чугунах значительная часть углерода находится в структурно-свободном состоянии в виде графита. Если серые чугуны хорошо поддаются механической обработке, то белые обладают очень высокой твердостью и режущим инструментом обрабатываться не могут. Поэтому белые чугуны для изготовления изделий применяют крайне редко, их используют главным образом в виде полупродукта для получения так называемых ковких чугунов.
В зависимости от структурычугуны классифицируют на высокопрочные (с шаровидным графиком) и ковкие. По степенилегированиячугуны подразделяют на простые, низколегированные (до 2,5% легирующих элементов), сред нелегированные (2,5—10% легирующих элементов) и высоколегированные (свыше 10% легирующих элементов). Шире всего используют простые и низколегированные серые литейные чугуны.
Чугун относится к группе материалов, обладающих плохой технологической свариваемостью. Основные трудности при сваркесвязаны с высокой склонностью его к отбеливанию, т. е. появлению участков с выделениямицементита той или иной формы в различном количестве, и образованию трещин в шве и околошовной зоне. Кроме того, интенсивное газовыделение из сварочной ванны, которое продолжается и на стадии кристаллизации, может приводить к образованию пор в металле шва, а повышенная жидкотекучесть затрудняет удержание расплавленного металла от вытекания и формирование шва. Вследствие окисления кремния на поверхности сварочной ванны возможно образование тугоплавких Оксидов, что может приводить к непроварам.
Способы сварки чугуна. Сваркучугуна применяют при ремонтно-восстановительных работах и при исправлении дефектов в отливках. К сварным соединениямчугунных деталей в зависимости от типа и условий эксплуатации предъявляются самые разнообразные требования— от декоративной заварки наружных дефектов до получения соединений, равнопрочных с основным металлом.
Чугун можно сваривать дуговой сваркой металлическим или угольным электродами, газовой сваркой, термитной сваркой, заливкой жидким чугуном, порошковой проволокой и т. д.
Наиболее часто способысваркичугуна классифицируют по состоянию свариваемой детали. В зависимости от температуры предварительного подогрева различают сварку с подогревом до высокой температуры (горячая сварка), с небольшим подогревом (полугорячая сварка) и без подогрева (холодная сварка).
Выбор способа и методасварки вависит от требований к сварному
соединению. При выборе методасварки учитывают необходимость механической обработкиметалла шва и околошовной зоны после сварки, необходимость получения однородности • металла шва с металлом свариваемых изделий, требования к плотности шва, а также нагрузки, при которых должны работать свариваемые детали.
Горячая сварка чугуна. Изделие подогревают до температуры 600— 800 °С. Технологический процесс состоит из механической обработки под сварку, формовки свариваемых деталей, предварительного подогрева, сварки и последующего медленного охлаждения.
Подготовка под сварку зависит от вида исправляемого дефекта. Однако во всех случаях подготовка дефектного места заключается в тщательной очистке от загрязнений и в разделке для образования полостей, обеспечивающих доступность для манипулирования электродом. Для предупреждения вытекания жидкотекучего металла сварочной ванны, а в ряде случаев для придания наплавленному металлу соответствующей формы место сварки формуют. В зависимости от размеров и местоположения исправляемого дефектаформовку выполняют с помощью графитовых пластинок, скрепляемых формовочной массой, состоящей из кварцевого песка, замешанного на жидком стекле, или другими материалами, а также в опоках формовочными материалами, применяемыми в литейном производстве.
Детали нагревают в специальных нагревательных печах, колодцах, горнах или с помощью индукционных нагревателей. Для •сварки используют плавящиеся электроды и прутки чугуна (см. § 7).
Горячую сваркучугуна выполняют на больших сварочных токах без перерывов до конца заварки дефекта при большой сварочной ванне.
Для горячей сваркичугуна можно использовать дуговую сварку угольным электродом, которая занимает промежуточное положение между плавящимся электродом и газовой сваркой, на постоянном токе прямой полярности при диаметреэлектрода 8—20 мм.
Диаметр угольного электрода, мм......8—10 10—12
Сварочный ток, А . . . 280—350 300—400 Диаметр угольного электрода, мм......12—16 16—18
Сварочный ток, А . . 350—500 350—600
Для защиты и раскисления ванны применяют флюсы на борной основе, чаще всего техническую безводную (прокаленную при температуре ~400°С)
буру-
Основными недостатками горячей сваркичугуна являются большая трудоемкость и тяжелые условия труда сварщиков. Однако высокое качество металла делает этот способ в ряде случаев единственно возможным при исправлении дефектов.
Полугорячая сварка. Подогрев свариваемой детали до 300—400 °С способствует замедленному охлаждениюметалла шва и прилежащих к нему зон после сварки. Замедленное охлаждение в значительной степени предотвращает получение отбеленных зон, что позволяет применять механическую обработку сварных соединений. Детали перед сваркой нагревают в термических печах, горнах или с помощью газовых горелок ацетилено-кислородным пламенем. При подогреве газовой горелкой необходимо следить за равномерностью нагрева подогреваемой поверхности.
Полугорячую сваркучугуна можно осуществлять . низкоуглеродистыми стальными электродами с покрытиями типа МР-3, УОНИ-13, стальными электродами со специальным покрытием, чугунными электродами и ацетилено-кислородным пламенем с применением чугунных присадочных прутков. При сварке сквозных трещин или при заварке дефектов, находящихся на краю деталей, необходимо применять графитовые формы, предотвращающие вытекание жидкого • металла из сварочной ванны.
Во время сварки следует непрерывно поддерживать значительный объем расплавленного металла в сварочной ванне и тщательно его перемешивать концом » электрода или присадочного стержня. Для замедленного охлаждения заваренные детали засыпают мелким древесным углем или сухим песком.
Холодная сварка. Этот способсварки имеет несколько разновидностей: стальными электродами, стальными электродами со специальными покрытиями, стальными электродами с помощью шпилек, чугунными электродами, медными электродами, электродами из монель-металла, электродами из никелевого аустенитного чугуна, газовая (ацетилено-кислородным пламенем).
Сварку стальными электродами применяют при ремонте неответственных чугунныхизделий небольших размеров с малым объемом наплавки, не требующих после сварки механической обработки. Сварное соединение неоднородно по структуре, часто не обладает достаточной плотностью и имеет низкую прочность.
Сварку электродами с защитно-легирующими покрытиями выполняют с V-или X-образной разделкой кромок. Для устранения неравномерного разогрева детали сваривают отдельными участками вразбивку. Длина отдельных наплавленных участков сварного шва не должна превышать 100—120 мм. После наплавки отдельных участков им дают возможность остыть до температуры 60—80 °С. Наилучшие результаты получают при сваркеэлектродами с покрытием У ОНИ-13/45 на постоянном токе обратной полярности.
Сварка с помощью шпилек требует специальной подготовки изделий под сварку. Этим способом восстанавливают ответственные изделия как малых, так и больших размеров (гидравлические и воздушные цилиндры, станины прессов, станков и др.), работающие при значительных нагрузках и не требующие обработки после сварки.
Для сваркичугуна получили распространение медно-железные. медно- никелевые и железоникелевые электроды.