Справочник кузнеца-штамповщика
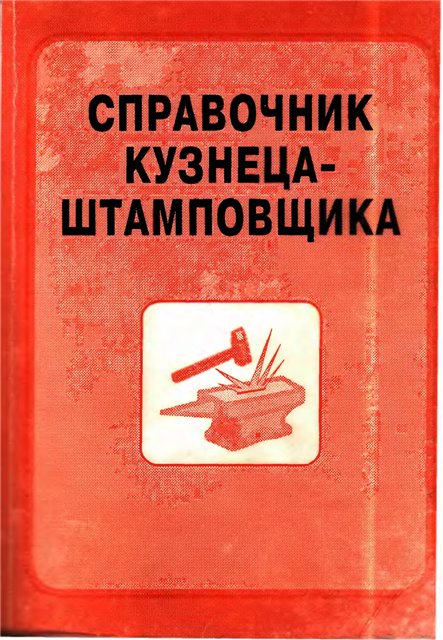
В.И. Ершов, В.В. Уваров, А.С., Чумадин, Б.Н. Марьин, A.M. Петров, ЮЛ. Иванов
МАИ, 1996 г.
Глава 2. ЗАГОТОВКИ ДЛЯ КОВКИ И ШТАМПОВКИ
В зависимости от конструкции детали, марки материала, требований, предъявляемых к материалу, серийности производства и сроков его подготовки, экономических показателей и других факторов в качестве заготовок для КОВКИ и штамповки используют слитки и заготовки, полученные литьем, сортовой прокат, включая листы и плиты, прессованные профили. Основной материал для изготовления поковок — сталь. Ковкой и штамповкой изготавливают также детали из цветных сплавов.
Поступающие партии заготовок сопровождаются документом, так называемым сертификатом, в котором указывается марка материала, номер плавки, клеймо ОТК. Каждая партия подвергается контролю для выявления внешних дефектов, подтверждения марки материала.
2.1. Слитки
Стальные слитки являются исходными заготовками для КОВКИ и штамповки, в основном крупных поковок, а также материалом для прокатки и прессования различных полуфабрикатов (профилей, листов, труб и т.п.).
Наиболее часто используют слитки массой 1—25 т с минимальной площадью поперечного сечения, превышающей 1200 см2. Для КОВКИ крупных изделий используют слитки массой до 350 т. Поперечное сечение слитка может быть круглым, квадратным, прямоугольным, многоугольным (шести-, восьми-, двенадцатиугольным). Для облегчения извлечения слитка из литейной формыслиток обычно имеет уклоны (форма продольного сечения — трапециевидная).
Строение слитка не является однородным в продольном и поперечном направлениях, что обусловлено условиями кристаллизации, изменяющимися во времени (рис. 2.1).
У холодных стенок литейной формы (изложницы) быстро образуется тонкая корочка 2 из мелких зерен. От этой корочки к центру слитка растут столбчатые кристаллы — дендриты 3, вытянутые в направлении, противоположном потоку тепла к стенкам изложницы. При литье в кокиль или при непрерывной разливке зоны столбчатых кристаллов достигают центра слитка. При отливании крупных слитков, когда скорость отвода тепла из центральной зоны по различным направлениям примерно одинакова, в центре слитка образуется зона крупных равноосных кристаллов 4. Крупнокристаллическое строение слитка ведет к уменьшению пластичности материала. В донной части 5 слитка, соприкасавшейся с дном изложницы, кристаллы имеют малые размеры. В верхней части слитка образуется так называемая усадочная раковина /.Химический состав слитка неоднороден (так называемая ликвация), поскольку в первую очередь затвердевают тугоплавкие соединения. Ликвация в пределах одного кристаллита и по зонам слитка является нежелательной, так как ухудшает пластичность материала.
Основные дефекты слитков: глубокое залегание усадочной раковины и усадочная пористость, сильная ликвация, повышенное включение неметаллических включений, пузыри и раковины вблизи поверхности, плены, завороты, трещины. Глубину расположения раковины и рыхлости уменьшают замедлением охлаждения верхней части слитка.
Раковины и газовые пузыри являются нежелательными, так как при проникновении в них воздуха происходит окисление их поверхности, что препятствует завариванию раковин и пузырей в процессе пластической деформации.
Аналогичный механизм образования другого дефекта — появление плен. При заливке металла в изложницу сверху образующиеся брызги быстро охлаждаются на холодных стенках, а их поверхность окисляется. Образовавшаяся окисная пленка препятствует свариванию корочки брызг с телом слитка.
8.5. Штамповка на горячештамповочных автоматах
Автоматы для горячей объемнойштамповки применяют в серийном, крупносерийном и массовом производстве. Их производительность достигает 200 и более изделий в минуту, что во много раз превышает производительность универсального горячештамповочного оборудования. При штамповке на автоматах достигается высокая стабильность размеров поковок с небольшими (0,5—1 мм на сторону) припусками на последующую обработку при отсутствии заусенцев и штамповочных уклонов на поковках, что приводит к экономии металла и трудозатрат. Себестоимость получаемых изделий относительно низкая.
Серийно выпускаютавтоматыусилием 400—15000 кН, а по специальным заказам и до 28000 кН. Масса штампуемых на автоматах поковок обычно не превышает 3—5 кг.
Горячештамповочные автоматыработают как самостоятельные машины либо входят как составная часть в автоматические линии. Их применяют также в сочетании с холодноштамповочными для комбинированной штамповки, что позволяет повысить точность поковок.
Поковки, получаемые на горячештамповочных автоматах, можно разделить на две группы.
К первой группе относятся удлиненные поковки типа стержня с головкой. Это в основном болты большого диаметра.
Вторую группу поковок составляют короткие цилиндрические изделия типа гаек (шестигранных, квадратных, специальных): шестерен и колец, высота которых, как правило, меньше диаметра. Сюда же относятся более сложные, в том числе асимметричные поковки, штампуемые на автоматах с применением процессов прямого и обратного выдавливания.
8.6. Штамповка на высокоскоростных молотах
Штамповкой на высокоскоростных молотах (ВСМ) получают поковки различной конфигурации с тонкими ребрами, стенками, полотнами, четким оформлением торцового рельефа, в ряде случаев без обработки части поверхностей на металлорежущих станках.
Классификация штамповочных поковок ВСМ включает следующие типы: стержни с утолщением (лопатки, клапаны); стержни с глухой полостью (стаканы, полусферы, крышки); диски (гладкие, со ступицей, с валом); детали с продольным и торцовым оребрением (стержни, стаканы, крыльчатки, шестерни с оформлением зубчатого контура); рычаги, кронштейны, фиттинги, корпуса, угольники и др.
Высокоскоростные молотывыпускают серийно с наибольшей энергией удара 25; 63; 160 и 250 кДж, а по особому заказу — 400 и 630 кДж.
Технологические особенности серийно выпускаемых ВСМ: наличие нижнего выталкивателя; минимальная скорость удара 6 м/с; минимальный рабочий ход при наибольшей энергии удара 160 кДж в пределах 3—5 мм; отклонение энергии последовательных ударов составляет не более 2—5 % от номинального значения; рабочие циклы составляют 5—15 с.
Высокоскоростная штамповка, как правило, одноударная, но при обработке заготовок большой массы возможна Штамповка и за два-три удара.
8.7. Электровысадка
Электровысадка достигается при совмещении операцийэлектронагреваметодомсопротивления и деформирования нагреваемой части заготовки. Схемапроцесса показана на рис. 8.12.
Заготовка 3 зажимается радиальным электродом 2 с определенным усилием Р i. При этом часть заготовки, подлежащая электровысадке, находится между радиальным электродом 2 и упорным электродом 1, подключенными ко вторичной обмотке понижающего трансформатора 4 переменного тока промышленной частоты. Часть заготовки между электродами / и 2 разогревается до температуры штамповки. Одновременно с нагревом в осевом направлении на заготовку действует усилие Р, которое деформирует нагретую часть заготовки. В процессе электровысадка упорный электрод / перемещается с определенной скоростью, при этом холодная часть заготовки под действием усилия прижима проскальзывает между радиальным электродом 2, а длина высаживаемой части заготовки увеличивается.
Процесс электровысадки дает возможность непрерывно деформировать нагретую часть заготовки при соблюдении соотношения / < 3 d, где / — первоначальная длина высаживаемой части, d — начальный диаметр заготовки. При этом осаживаемая часть заготовки имеет хорошую продольную устойчивость, а суммарное утолщение (набор металла) в высаживаемой части может достигать значительных величин.
электровысадки можно проводить как со свободным деформированием (свободным набором металла) (см. рис. 8.12), так и с набором в матрицу, причем в последнем случае можно получать довольно точные детали, не требующие дальнейшей механической обработки. Электровысадкой можно получать изделия из труднодеформируемых сплавов (высокопрочных легированных и жаропрочных сплавов, сплавов на основе никеля, титана и т.п.). Процесс электровысадки характеризуется простотой и низкой стоимостью технологической оснастки, хорошими санитарными условиями (отсутствием дыма, пыли, шума) и возможностью полной механизации и автоматизации процесса. методом электровысадки можно получать поковки сплошного или трубчатого сечениядиаметром до 100 мм, а также асимметричные поковки. В настоящее время электровысадкой получают заготовки клапанов, полуосей автомобилей, турбинных лопаток и других деталей. Себестоимость таких деталей по сравнению с изготовлением их на ГКМ ниже на 15%, экономия металла по сравнению с обработкой резанием достигает 40%.
Особенностью электровысадки является то, что этим процессом можно получать только утолщения (наборы металла) на удлиненных заготовках. Поэтому номенклатура деталей, получаемых электровысадкой, невелика.
8.8. Штамповка с использованием сверхпластичности
Состояние сверхпластичности определяется совокупностью признаков: 1) повышенная чувствительность напряжения теченияматериала к изменению скорости деформации; 2) крайне незначительное деформационное упрочнение; 3) аномально высокий ресурс деформационной способности; 4) напряжение теченияматериала в несколько раз меньше предела текучести, характеризующего пластическое состояние данного материала.
Признаки сверхпластичности проявляются в определенных условиях, среди которых принципиальное значение имеют структурноесостояние деформируемого материала, температура-и скорость деформации.
По структурному признаку принято различать две разновидности сверхпластичности: сверхпластичность, проявляющуюся у металлов и сплавов с особо мелким (сверхмелким) зерном (d< 10 мкм) и сверхпластичность полиморфных металлов и сплавов, проявляющуюся при деформировании их в процессе фазовых превращений, при этом исходных размер зерен не имеет значения.
Первую разновидность сверхпластичности называют структурной. Ее отличительными особенностями являются зависимость эффекта от исходного размера зерен (чем меньше зерно, тем больше
склонность материала к скоростному упрочнению, соответственно больше его деформационная способность и меньше напряжение течения) и почти неизменное структурноесостояниематериала в процессе деформации. При этом необходимо, чтобы зерна имели приблизительно равноосную форму, а также в процессе нагрева до температурыдеформирования и при последующем деформировании обладали достаточной устойчивостью против роста. Наилучшие условия для предотвращения роста зерен имеются у двухфазных сплавов. В сверхмелкозернистое состояниесплавы переводят обычно предварительной термической или термомеханической обработкой.
Вторая разновидность сверхпластичности, наблюдающаяся при деформированииматериала в процессе фазового превращения, характеризуется, в отличие от структурной сверхпластичности, постоянным изменением фазового состава и структурыматериала в процессе деформирования.
Температурный интервал существования структурнойсверхпластичности для различных металлов и сплавов различный, он может находиться в пределах от температуры начала рекристаллизации (0,4 ТПЛ) до температур, близких к температуреплавления Гпл. Нижняя граница температурного интервала обусловлена диффузионными процессами в механизмедеформирования сверхмелкозернистых материалов, верхняя граница соответствует температуре начала собирательной рекристаллизации. Однако какой бы ни была температураструктурной сверхпластичности, она должна поддерживаться постоянной по объему деформированного объекта в течение всего периода деформирования, чтобы обеспечить равномерное течение материала. Поэтому структурнуюсверхпластичность иногда называют также изотермической.
Сверхпластичность, связанная с превращением, реализуется при различных температурных режимах (в процессе монотонно изменяющейся температуры, проходящей через интервал превращения; при термоциклировании в пределахтемпературной амплитуды, включающей интервалтемператур превращения; при фиксированной температуре вблизи температурного интервала превращения).
Скорость деформации для обеспечения состоянияструктурнойсверхпластичности должна быть, с одной стороны, достаточно малой, чтобы успевали в полном объеме протекать диффузионные процессы, участвующие в деформации, с другой стороны — достаточно высокой, чтобы в условиях повышенных температур не допустить роста зерен.