Режимы резания труднообрабатываемых материалов. Справочник
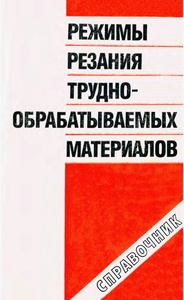
Гуревич Я.Л., Горохов М.В. и др.
Машиностроение, 1986 г.
Классификация труднообрабатываемых сталей и сплавов по обрабатываемости резанием. Развитие техники связано с созданием и освоением технологииобработки заготовок из сталей и сплавов с особыми физико-механическими свойствами, важнейшими из которых являются коррозионная стойкость в различных средах, жаропрочность и высокая прочность. В ряде случаев от материалов требуется сочетание различных свойств. Повышение указанных свойств конструкционных материалов дает возможность создавать машины с более высокими характеристиками.
Жаропрочные стали обладают достаточной прочностью до 700 °С, сплавы на никелевой основе — до П00°С, сплавы на молибденовой и ниобиевой основах — до 1500°С, сплавы на вольфрамовой основе — до 2000 °С. Широкое применение находят материалы с высокой удельной прочностью. Из труднообрабатываемых материалов к ним в основном относятся сплавы на титановой основе и высокопрочные стали. сплавы на титановой основе обладают также высокой коррозионной стойкостью в большинстве агрессивных сред, что обусловливает их большую перспективность.
Однако при обработке заготовок из жаропрочных и высокопрочных сталей и сплавов необходимо снижать, скорость резания, так как ухудшается их обрабатываемость *. Как видно из табл. 1, при обработке заготовок из жаропрочных сталей возникают силы резания, в 1,2— 1,5 раза, а при обработке деталей из деформируемых жаропрочных сплавов — в 2 раза большие, чем при обработке заготовок из стали 45. При обработке заготовок из сплавов на титановой основе возникают примерно такие же силы, что и при обработке заготовок из стали 45.
1. Вертикальные составляющие удельных сил резания
(Рг) и контактные температуры (6), возникающие при точении
различных материалов (S = 0,1 мм /об, t = 1 мм)
|
|
| Рг | в (°С) при v. | м/мин | |
Обрабатываемый |
|
|
|
|
| |
материал | МПа |
| 20 |
| 60 | |
Сталь 45 | 750 |
| 2000 | 200 |
| 300 |
12Х18Н10Т | 600 |
| 2500 | 560 |
| 800 |
ХН62МВКЮ | 1100 |
| 4000 | 720 |
| 1000 |
ЖС6-К | 900 |
| 3500 | 750 |
| 1050 |
ВТ5 | 900 |
| 2000 | 520 |
| 750 |
38Х5МСФА | 1700 |
| 7000 | 700 |
| 1000 |
При обработке заготовок из высокопрочных сталей возникают силы резания, в 2—3 раза большие, чем при обработке заготовок из стали 45. Большие силы резания, возникающие при обработке заготовок из труднообрабатываемых сталей и сплавов, обусловливают выделение большего количества теплоты в срезаемом слое металла, К тому же большинство труднообрабатываемых сталей и сплавов имеет низкую теплопроводность, что приводит к возникновению высоких температур в зоне резания— в 2—3 раза больших, чем при обработке обычных конструкционных материалов.
При обработке заготовок из сплавов на титановой основе усадкастружки мала и при определенных условиях происходит не усадка, а удлинение стружки. Причиной малой усадкистружки при резании заготовок из сплавов на титановой основе является их низкая пластичность. Малая усадка обусловливает малую площадь контакта стружки с передней поверхностьюинструмента и большую скорость перемещения стружки по передней поверхности, что вызывает высокие контактные давления и температуры.
Из-за больших сил, возникающих при резании труднообрабатываемых сталей и сплавов, необходимо, чтобы жесткостьсистемыстанок — приспособление — инструмент— заготовка была большой. Повышение контактных температур является основной причиной низкой стойкости инструмента, и во избежание их увеличения обрабатывать труднообрабатываемые материалы следует при малых скоростях резания.
В Советском Союзе разработано большое количество марок сталей и сплавов со специальными свойствами. В табл. 2 приведена классификация по обрабатываемости резанием наиболее широко применяемых из них. В основу классификации положен химический состав материалов, поскольку от него в основном зависит обрабатываемость жаропрочных сталей и сплавов. По предлагаемой классификации все рассматриваемые в справочнике стали и сплавы разделены на восемь групп, в каждой из которых объединены стали или сплавы примерно одинакового химического состава, с одинаковыми механическими свойствами и близкой обрабатываемостью резанием. Для каждой группы материалов приведены коэффициенты по скорости резания и примерные скорости резания, применяемые при обработкеинструментом из твердого сплава и быстрорежущей стали. При разработке новых марок труднообрабатываемых сталей и сплавов можно относить их по химическому составу к соответствующей группе классификации и, не проводя трудоемких экспериментальных исследований, устанавливать геометрические параметрыинструмента и примерные режимы резания. Таким образом можно приближенно определять трудоемкость механической обработки заготовок из новых материалов и обоснованно планировать производство новых изделий.
В случае необходимости установления более точных скоростей резания для обработки заготовок из новых конструкционных материалов, относящихся по химическому составу к группам III—VI классификации, их можно с достаточной для практики точностью рассчитать с помощью формулы, предложенной Н. И. Ташлицким.
В справочнике приняты следующие определения специальных сталей и сплавов:
под теплостойкими понимают стали, обладающие способностью противостоять деформированию и разрушению при механическом нагружении в области температур ниже 550 °С, когда не возникает опасности интенсивного окалинообразования;
коррозионно-стойкими считают стали, обладающие стойкостью против электрохимической коррозии (атмосферной, почвенной, щелочной, кислотной, солевой, морской и др.);
жаростойкими (окалиностойкими) называют стали и сплавы, обладающие стойкостью против химического разрушенияповерхности в газовых средах при температурах выше 550 °С и работающие в ненагруженном или слабо нагруженном состоянии;
под жаропрочными понимают стали и сплавы, обладающие способностьюработать в нагруженном со стоянии при высоких температурах (выше 700 °С) в течение определенного времени, имеющие при этом достаточную окалиностойкость;
высокопрочными считают стали с тв>1600 МПа.
Стали, отнесенные к группе I, характеризуются содержанием хрома до 6%, никеля до 3%, молибдена и ванадия до 1% каждого и кремния до 2%. Они являются теплостойкими материалами, применяются для изготовления впускных и выпускныхклапанов двигателей, лопаток и дисков турбин, а также деталей котельных установок, работающих при температурах до 500—600 °С.
Обрабатываемость сталей группы I вполне удовлетворительная, она близка к обрабатываемости углеродистых и низколегированных конструкционных сталей соответствующей прочности.
Стали группы II характеризуются высоким содержанием (более 10—12%) хрома и небольшим содержанием (до 4%) других легирующих элементов. Они применяются в основном для изготовления арматуры, корпусных деталей турбинных лопаток и дисков, работающих при температурах до 500—550 °С (12X13, 20X13, 1Х12Н2ВМФ, 11Х11Н2В2МФ и др.), хирургического инструмента, шарикоподшипников (30X13, 40X13) и других деталей с высокой коррозионной стойкостью. В эту же группу входит высокохромистая сталь 95X18, которая после закалки и соответствующего отпуска имеет пределпрочности более 1900 МПа. Обрабатываемость ее в указанном состоянии соответствует обрабатываемости высокопрочных сталей группы VIII. Однако, поскольку при обработке заготовок из этих сталей основной припуск срезается при отожженном состоянии заготовок, когда обрабатываемость их та же, что и обрабатываемость высокохромистых сталей с 0B = 9OO-f--f-1000 МПа, они отнесены к группе И.
Обработка резанием заготовок из сталей группы II производится как после отжига (12X13, 20X13, 14Х17Н2 и др.). так и после закалки и отпуска до <тв=1000-т--М500 МПа (11Х11Н2В2МФ, 1Х12Н2ВМФ и др.). В отожженном состоянии эти стали имеют удовлетворительную обрабатываемость: применяемые скорости резания в 1,5 раза ниже скоростей резания, применяемых при обработке заготовок из стали 45. С повышением прочностныххарактеристиксталей в результате их термической обработки обрабатываемость высокохромистых сталейрезко снижается. Заготовки из сталей этой группы, термически обработанные до ов>1200 МПа, по возможности должны обрабатываться инструментом из твердых сплавов.
При обработке заготовок из сталей группы II в отожженном состоянии получить малую шероховатостьповерхности затруднительно, особенно при нарезании резьбы, протягивании, цилиндрическом фрезеровании и других операциях, когда поверхность формируется лезвиями инструментов значительной протяженности. С повышением прочностисталишероховатость обработанной поверхности уменьшается.
Аустенитные стали, отнесенные к группе III, содержат большое количество хрома (более 15%) и никеля (более 5%), а также небольшое количество других легирующих элементов (титан, кремний и др.)- К этой группе отнесены также стали аустенитно-ферритного и аустенитно-мартенситного классов. По обрабатываемости резанием сталь аустенито-ферритного класса 12Х21Н5Т близка к стали 12Х18Н10Т. Стали аустенитно-мартенситного класса (09X15Н8Ю, 08Х17Н5МЗ) по технологическим характеристикам близки к аустенит» ным, по прочностным — к мартенситным сталям. После отжига обрабатываемость сталей аустенитно-мартенситного класса близка к обрабатываемости стали 12Х18Н10Т, а после закалки и отпуска—к сталям группы II соответствующей прочности. Стали группы III получили широкое распространение как кислотостойкие, коррозионно-стойкие и жаростойкие материалы. Они применяются почти во всех отраслях промышленности для изготовления деталей сварной аппаратуры, лопаток и заклепок компрессорных машин, жаровых труб и других деталей, работающих в условиях, вызывающих коррозию металла, или в условиях высоких температур — до 800°С. Скорости резания, применяемые при обработке заготовок из сталей группы III, примерно в 2 раза ниже скоростей резания, применяемых при обработке заготовок из стали 45.
К группе IV отнесены сложнолегированные стали ау-стенитного класса, содержащие в большом количестве хром (12—25%), никель (более 10%), в несколько меньшем количестве — марганец, молибден, титан, вольфрам, ванадий и другие легирующие элементы. В ряде сталей (37Х12Н8Г8МФБ, 07Х21Г7АН5 и др.) содержание никеля снижено благодаря увеличению содержания более дешевого и менее дефицитного марганца. Из сталей этой группы изготовляют диски и лопатки газовых турбин, детали газопроводных систем и крепежные детали, работающие при температурах до 650—750 °С, а при умеренных напряжениях — до 800—950 °С. Обрабатываемость резанием сталей группы IV в 3—4 раза ниже обрабатываемости стали 45.
К группе V относятся жаропрочные деформируемые сплавы на никелевой и железоникелевой основах, легированные большим количеством хрома (10—20%) и несколько меньшим количеством титана, алюминия, вольфрама, молибдена, кобальта и других элементов. Они применяются для изготовления деталей машин, работающих при больших нагрузках и высоких температурах— от 750 до 950 °С (дисков, рабочих и направляющих лопаток и других деталей газовых турбин). Обрабатываемость резанием сплавов группы V в 6—12 раз ниже обрабатываемости стали 45.
Литейные жаропрочные сплавы группы VI широко применяются для изготовления сопловых лопаток, цельнолитых роторов и других деталей газовых турбин. В них добавлено больше легирующих элементов, и вследствие этого они более жаропрочны, чем деформируемые жаропрочные сплавы. Из-за неоднородной литой структуры механические свойства их значительно различаются. По обрабатываемости резанием они отличаются от сплавов группы V. Различная обрабатываемость литейных и деформируемых жаропрочных сплавов объясняется тем, ятр литейные сплавы менее пластичны, силы резания при fix обработке значительно ниже сил резания при обработке деформируемых сплавов. В литейных жаропрочных сплавах имеется большое количество интерметаллидных и карбидных включений, из-за которых сильно изнашивается инструмент из быстрорежущей стали. Это создает более благоприятные условия для работыинструмента из твердого сплава и менее благоприятные условия для работыинструмента из быстрорежущей стали.
Почти на всех операцияхобработки резанием заготовок из литейных жаропрочных сплавов следует применять инструмент, оснащенный твердым сплавом, в то время как при обработке заготовок из деформируемых жаропрочных сплавовинструмент из твердого сплава применяют в основном при непрерывном резании. Во многих случаях прерывистого резания (торцовое и концевое фрезерование) при обработке заготовок из деформируемых жаропрочных сплавов целесообразнее применять инструмент из быстрорежущей стали, чем из твердого сплава. Одной из причин быстрого изнашивания и выкрашивания инструмента из твердого сплава при прерывистом резании заготовок из деформируемых жаропрочных сплавов является налипание частиц материала заготовки на режущие лезвия инструмента при выходе его из металла. При последующем врезании прилипшие частицы срываются с лезвий вместе с частицами твердого сплава. При обработке заготовок из литейных сплавов это явление сказывается в значительно меньшей мере вследствие их меньшей прочности и пластичности. Скорости резания при обработке заготовок из литейных жаропрочных сплавов в 12—20 раз ниже, чем при обработке заготовок из стали 45.
Сплавы на титановой основе группы VII широко применяются в различных отраслях промышленности. В ряде конструкций они вытесняют алюминиевые сплавы и коррозионно-стойкие стали. В настоящее время применяется большая группа сплавов на титановой основе (более 30 марок) с широким диапазоном обрабатываемости резанием, которая в основном зависит от пределапрочности сплава. Заготовки из сплавов на титановой основе с <Ув<1000 МПа при отсутствии окалины, корки и альфированного (насыщенного газами) слоя легко обрабатываются инструментом из быстрорежущей стали и твердого сплава. Обработка заготовок из сплавов на титановой основе с <тв>1000 МПа инструментом из быстрорежущей стали затруднительна. При работе же по окалине и альфированному слою следует применять только твердосплавный инструмент.
Точение, фрезерование и сверление заготовок из сплавов на титановой основе не вызывает затруднений. Однако вследствие большой упругости этих сплавов нарезание резьбы метчиками, развертывание и протягивание отверстий в заготовках из них затруднительны из-за защемления инструмента по задним и вспомогательным поверхностям. В связи с этим задние и вспомогательные углы инструмента для обработки заготовок на титановой основе следует выполнять на 3—5° большими, чем инструмента для обработки заготовок из конструкционных сталей. Исполнительные размеры мерного инструмента должны выполняться на верхнем пределе допусков.
Большинство сплавов на титановой основе применяются в отожженном состоянии. Однако для изготовления многих ответственных деталей машин все шире применяются сплавы, подвергаемые упрочнению путем закалки и старения, а также термомеханической обработки (ВТ14, ВТ15, ВТЗ-1, ВТ22). Обрабатываемость этих сплавов после указанных видов упрочнения на 20—25% ниже, чем после отжига.
Сплавы на титановой основе активно взаимодействуют с газами при повышенных температурах, начиная с 600 °С. Наиболее активным элементом при газонасыщении является кислород. Твердость слоя, насыщенного газами, значительно возрастает. Микротвердость насыщенных слоев превышает Микротвердость нижележащих слоев металла в 3—5 раз. Микротвердостьсоединенийтитана с кислородом достигает 1300О МПа, титана с азотом и титана с углеродом—20000 МПа при микротвердости нижележащих слоев металла 3000—3500 МПа. Толщина окалины и глубина альфированного слоя зависят от температуры и длительности ее воздействия. Поэтому на обрабатываемость заготовок из сплавов на титановой основе по корке влияет способ получения заготовки. Толщина дефектного слоя у отливок может достичь нескольких миллиметров, у поковок — 1 мм, у проката — 0,5 мм. Обрабатываемость по корке кованых прутков ниже, чем катаных. Скорости резания, применяемые при обработке заготовок из сплавов на титановой основе без корки, в зависимости от их пределапрочности в 1,5—4 раза ниже скоростей резания, применяемых при обработке деталей из стали 45. При обработке заготовок по корке скорости резания снижаются в 2 раза.
К группе VIII отнесены высокопрочные стали. Ранее в качестве высокопрочных сталей в основном применялись легированные стали 28ХЗСНМФА, 30Х2ГСН2ВМ, ЗЭХ5МСФА, 42Х2ГСНМ и др., отнесенные к группе VTIIA, которые в зависимости от содержания углерода и термической обработки имеют пределпрочности 1600— 2300 МПа. Однако вследствие низкой пластичности эти стали имеют низкое сопротивление возникновению и распространению трещин, что делает их малопригодными для изготовления ответственных деталей машин. Для этой цели в последнее время находят применение дисперсионно-твердеющие стали типа Н18К9М5Т, отнесенные к группе VIIIB. Дисперсионно-твердеющие стали имеют более высокое сопротивление хрупкому разрушению и, в особенности, более высокое сопротивление развитию трещин. Это обеспечивает их малую чувствительность к наличию концентраторов напряжений (микротрещин, рисок и др.), что обусловливает более высокую эксплуатационную надежность изготовленных из них деталей.
На долговечность деталей из высокопрочных материалов (сталей, сплавов на титановой основе с высоким пределом прочности) в большой степени влияют способ и условия их чистовой обработки. Так, при испытаниях в условиях циклического нагружения образцы из высокопрочных сталей и сплавов, шлифованные после термического или термомеханического упрочнения, выдерживали значительно большее число нагружений, чем идентичные образцы, шлифованные до упрочнения. Образцы, обработанные после упрочняющей обработки точением, выдерживали большее число нагружений, чем образцы, обработанные после той же упрочняющей обработки шлифованием.
Обрабатываемость легированных высокопрочных сталей в состоянииотжига такая же, как обычных конструкционных сталей. После закалки и отпуска в зависимости от пределапрочности их обрабатываемость снижается в 5—8 раз. В связи с этим заготовки из этих сталей должны обрабатываться таким образом, чтобы под закалку и отпуск оставался минимальный припуск, необходимый для устранения возможного деформирования и чистовой обработки.
Обрабатываемость дисперсионно-твердеющих высокопрочных сталей в состоянии закалки примерно в 2 раза, а после старения — в 4 раза ниже обрабатываемости стали 45, поэтому при обработке заготовок из них целесообразно основной припусксрезать после закалки, а после старения производить только чистовую обработку, Обрабатываемость дисперсионно-твердеющих высокопрочных сталей с пределомпрочности 2100—2200 МПа, отнесенных к группе VIIIB, в 2 раза выше обрабатываемости легированных высокопрочных сталей группы VIIIA такой же прочности. Это объясняется тем, что при резании дисперсионно-твердеющих сталей у режущей кромкиинструмента образуется застойная зона, которая способствует уменьшению возникающих напряжений на передней поверхности у режущей кромки инструмента, а также защищает последнюю от изнашивания, тогда как при резании легированных высокопрочных сталей застойная зона отсутствует.
Заготовки из высокопрочных сталей с о>в>1600 МПа следует обрабатывать инструментом, оснащенным твердыми сплавами. При чистовом точении и растачивании заготовок из сталей группы VIIIA целесообразно применять резцы, оснащенные пластинами оксидно-карбидной минералокерамики, поликристаллами твердого нитрида бора (ПТНБ), эльбора-Р и гексанита-Р. При чистовом точении и растачивании заготовок из сталей группы VIIIB применять минералокерамику и сверхтвердые синтетические материалы нецелесообразно.