Наплавка и напыление
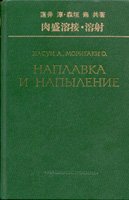
Хасуи А., Моригаки О.
Машиностроение, 1985 г.
2.1. Общие сведения.
При длительной эксплуатации машин изнашивание деталей сопровождается снижением эксплуатационных показателей, что в частности вызывает ухудшение качества изготовляемых изделий. Изнашивание рабочих поверхностей деталей нередко требует их полной замены. Это повышает себестоимость производства из-за больших амортизационных отчислений.
В ряде случаев изготовление деталей целиком из износостойкой легированной стали нерационально в связи с трудностью обработки и высокой стоимостью стали. Поэтому для решения задач повышения эксплуатационных показателей и увеличения срока службы деталей машин используют различные способы поверхностного упрочнения, в частности наплавку, нашедшую широкое применение в производстве разнообразных изделий — от крупногабаритных, таких как сосуды высокого давленияатомных реакторов, установки для десульфурациимазута (для повышения коррозионной стойкости), валкипрокатныхстанов в металлургии (для упрочнения), до мелких деталей типа выхлопных гнезд и клапанов двигателей внутреннего сгорания (с целью повышения жаропрочности и износостойкости). В последующих главах рассмотрены примеры применения технологиинаплавки при производстве строительных машин, землесосных снарядов, металлургического оборудования, железнодорожного подвижного состава и сосудов высокого давления.
В промышленности применяют разнообразные способы сварки: ручную (газовую, дуговую покрытыми электродами), полуавтоматическую (дуговую в среде защитного газа или без защитной среды) и автоматическую (дуговую под флюсом). Для наплавки выбирают экономически целесообразный способ сварки, при котором на поверхность основного металла наносят равномерный слой сплава, обладающий высокой износостойкостью, коррозионной стойкостью или жаропрочностью [1].
Появление технологиинаплавки относится к 1896 г., когда Спенсер получил патент на изобретение [1]. Однако промышленное применение началось несколько позже. В частности, в 1922 г. братья Студи впервые осуществили в США наплавку коронок нефтяного бура способом газовой сварки с использованием присадочного материала в виде стальной трубки, заполненной хромовым нвплавкой внутренней поверхности, что значительно проще, чем ^изготовление таких сосудов из плакированного стального листа, не "обладающего достаточной технологичностью.
5. Простота выполнения, не требующая высокой квалификации сварщика. Достаточно высокая квалификация сварщика необходима только при ручной наплавке покрытыми электродами, тогда как лри механизированной наплавке (например, при наплавке под флюсом) процесс значительно упрощается. Сварщик, хорошо овладевший сваркой, например, при строительстве зданий и мостов, производстве химического оборудования и других отраслях, может достаточно квалифицированно выполнять наплавку.
6. Возможность нанесения износостойкого покрытия на основной металл любого состава. При упрочнении закалкой, азотированием и другими аналогичными способами высокий эффект поверхностного упрочнения достигается лишь для металла определенного состава, тогда как при наплавкесостав и свойства основного металла не имеют большого значения. В случаях, когда основной металл имеет низкую свариваемость, предварительно наносят подслой низкоуглеродистой стали, а затем наплавляют слой твердого металла. Отсутствие ограничений по составу (типу) стали для наплавляемых изделий позволяет снизить себестоимость производства и упростить технологию изготовления изделий.
7. Возможность повышения эффективности наплавки путем ее сочетания с другими способамиповерхностной обработки. После наплавкиизделие иногда подвергают пламенной закалке или азотированию. Например, для облегчения обработки резанием валы, ролики, валки и другие изделия можно наплавлять материалом с твердостью <400 и после механической обработки упрочнять пламенной закалкой.
2.3. Недостатки технологии наплавки. 1. Ухудшение свойств наплавленного слоя из-за перехода в него элементов основного металла. При ручной наплавке покрытыми электродами или автоматической наплавке под флюсом деталей из низкоуглеродистой или низколегированной сталимонель-металлом вследствие интенсивного разбавления первого слоя наплавленного металла основным металлом и значительного увеличения содержания в составе наплавленного слоя железа коррозионная стойкость его заметно снижается.
2. Деформация изделия, вызываемая высокой погонной энергией наплавки. Неправильный выбор режима наплавки может привести к чрезмерной деформацииизделия после наплавки и браку. Для сохранения точности формы и размеров наплавляемого изделия приходится принимать особые меры: наплавкуизделия вести в зажатом состоянии, исключающем его деформацию; создавать предварительную деформациюизделия с таким расчетом, чтобы Деформация, вызываемая наплавкой, направленная в противоположную сторону, обеспечивала возврат к исходной правильной форме изделия; осуществлять последующую механическую обработку до окончательных размеров.
ГЛАВА3
НАПЛАВОЧНЫЕ МАТЕРИАЛЫ
В процессахнаплавки в зависимости от назначения используют следующие наплавочные материалы.
Г. Покрытые электроды для дуговой наплавки используют в виде стержней с нанесенным на них покрытием, продукты сгорания ц разложения которого обеспечивают защиту дуги и ванны жидкого- металла от окружающего воздуха. Электродныйстержень изготовляют обычно из проволокидиаметром 3,2—8 мм или литьем. Если невозможно изготовить проволоку, наплавляемый материал (например, карбид вольфрама) используют в виде порошка, которым заполняют стальные трубки.
В японском промышленном стандарте Z3251 определены следующие три вида покрытий электродов, предназначенных для износостойкой наплавки: основного типа (фтористокальциевое) В, вы-сокорутиловое R и карбонатно-рутиловое BR. Главным компонентомсостава основного покрытия служит карбонат, к которому добавляютфлюорит (плавиковый шпат) и ферросилиций.
Благодаря низкому содержанию водорода в наплавленном металле, получаемом при наплавкеэлектродами с покрытием основного типа, значительно снижается опасность возникновения трещин при наплавке деталей из высокоуглеродистой и легированной стали, а также крупногабаритных стальных отливок без предварительного подогрева. Однако это покрытие уступает двум другим видам покрытия по технологичности при наплавке. Наплавкаэлектродами с высокорутиловым покрытием, содержащим до 35% диоксида титана, отличается высокой технологичностью, характеризуемой, в частности, стабильностью горения дуги, отсутствием разбрызгивания, хорошим отделением шлаковой корки от поверхности валика при небольшом проплавлении основного металла, образованием ровного валика наплавленного металла, а следовательно, простотой последующей механической обработки. Вместе с тем металл, наплавленный электродами с этим покрытием, отличается повышенным содержанием водорода, поэтому при наплавке крупногабаритных отливок или основного металла, подвергающегося закалке с охлаждением на воздухе, существует опасность возникновения трещин. электроды с карбонатно-рутиловым покрытием занимают но технологическим характеристикам промежуточное положение: отличаются сравнительно хорошей технологичостью в частности, в хорошем отделении шлака при наплавке.
Керамические флюсы получают путем смешения минерального сырья с металлическим порошком и связующим веществом с последующим гранулированием до заданной крупности. Керамические флюсы, несколько превосходящие плавленые по тугоплавкости, успешно используют для наплавки с большой погонной энергией, а возможность добавления легирующих элементов к этим флюсам создает предпосылку их широкого применения для наплавки и сварки коррозионно-стойкой и специальной стали. Смешанные флюсы (флюсовые смеси) получают путем смешения плавленых и керамических флюсов и порошкового сырья разного состава в необходимой пропорции.
5. Порошковую проволоку получают путем заполнения флюсующими и металлическими порошками тонкостенной металлической оболочки с последующей обработкой ее для придания формы проволоки.
При автоматической дуговой наплавке под флюсом используют проволоку, сердцевина которой заполнена порошковым сплавом, а при автоматической и полуавтоматической наплавке в среде углекислого газа и открытой дугой применяют проволоку, сердцевина которой содержит раскислители, шлакообразующие компоненты, стабилизаторы дуги и порошковые сплавы.