Карбид Титана: получение, свойства, применение
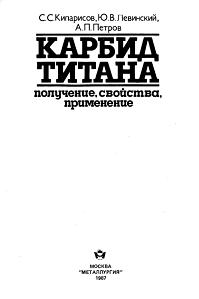
Кипарисов С.С., Левинский Ю. В., Петров А.П.
Металлургия, 1987 г.
Более 80 % карбидатитана в производственных условиях получают из диоксида титана (в основном в связи со сравнительно низкой стоимостью и доступностью до последнего времени TO2). В течении 30 последних лет углетермический метод сохраняет доминирующее положение в производстве карбида титана. Отработанная технология, стандартное и недорогое оборудование, сравнительно дешевое сырье - главные причины этого. Процесс образования карбида гитана из диоксида титана и твердых науглероживающих материалов, а также факторы, влияющие на состав продукта, подробно исследованы и представлены в многочисленных работах [1; 4; 6-11], поэтому кратко остановимся только на основных. В промышленном отечественном производстве обычно используется диоксид титана следующих составов, %: 1) 99,8 ТiO2; 0,06 S; 0,5 Р; 2) 98,8 TiO»; 0,1 SiO2; 0,05 Fe; 0,1 S; 0,1 P (ТУБ-10-1394-78).Смесь, состоящая из 68,5 % TiO2 и 31,5 % сажи, подвергается продолжительному и тщательному перемешиванию в жидкой среде. Для снижения времени приготовления смеси в четыре раза рекомендуется проводить Процесс в вакууме [10]. Смесь TiO2 с сажей набивается в графитовый патрон либо прессуется под давлением 1,5 -107 Па в брикеты, которые загружаются в графитовые лодочки или тигли. Карбидизация смеси проводится в атмосфереводорода в угольно-трубчатых печах сопротивления; в собственной защитной атмосфере в вертикальных или вакуумных садочных печах. В угольно-трубчатых печах графитовые лодочки непрерывно продвигаются в печи, температура которой 2000 °С. Измельченный и просеянный карбидтитана содержит 20-20,5 % общего углерода, из которых 1,0—2,0 % находится в виде свободного углерода. При вакуумной карбидизации реакция образования TiC начинается уже при 800 °С и быстро протекает при 12О0-14ОО°С. Окончательная выдержка продолжительностью 0,5 ч проводится при 1900-1950 °С. карбидтитана после измельчения и просева содержит 19,5—20,3 % обще¬го и 0,1 —0,8 % свободного углерода, На одном из заводов внедрена в производство серия печей, позволившая полностью механизировать и автоматизировать Процесс получения карбидатитана (рис. 2) [12]. Использование при карбидизации электровибратора дает возможность сочетать технологические процессы с непрерывным перемещением шихты в рабочей камере. Для улучшения подвижности и сыпучести шихты проводится ее агломерация в таблетки диаметром 12—13 мм и высотой 5 мм или шарики диаметром 15… состав и свойства безвольфрамовых твердых сплавов на основе карбидатитанасостав и основные физико-механические свойства безвольфрамовых твердых сплавов на основе карбидатитана и для сравнения свойства вольфрамсодержащего сплава Т15К6 представлены В/табл. 30 [101-104]. Сравнение прочностныхсвойств и твердости зарубежных безвольфрамовых твердых сплавов и других твердых материалов приведено на рис. 34 [105]. Основной недостаток безвольфрамовьис твердых сплавов—низкие прочность и вязкость по сравнению с другими твердыми сплавами. Отрицательную роль играет и хрупкость тугоплавкой составляющей сплавов TiC—Ni—Mo. При резании твердыми сплавами "неподатливость" карбидных зерен вызывает возникновение существенных напряжений в обрабатываемой поверхности, приводящих к выходу из строя инструмента. Поэтому отчетливо проявляются преимущества карбида вольфрама, обладающего небольшой пластичностью. Основным направлением исследовательских работ является создание безвольфрамовьис твердых сплавов с повышенными прочностными свойствами и некоторой пластичностью. прочность твердых сплавов определяется прочностьюкарбидной составляющей, связующей фазы и прочностью сцепления между ними, причем перепад величин прочностныххарактеристик на границе карбид — связующая фаза должен быть по возможности минимальным. Образование "кольцевой" структуры зерен карбидной фазы с введением Мо позволило в значительной степени выполнить третье условие. Актуальными задачами, стоящими перед исследователями, остаются проблемы повышения пластичности и прочности хрупкого центра карбидной фазы и упрочнениесвязки [106]. На свойства безвольфрамовых твердых сплавов оказывает влияние метод получения карбида титана. В табл. 31 представлены свойства твердого сплава ТН20, изготовленного из углетеомического и плазменного карбидатитана [107]. Использование плазменных порошков TiC вместо углетермических приводит к падению прочности и повышению твердости сплава. Несмотря на более мелкозернистую структурусплава на основе плазменного TiC, происходит снижение прочностныхсвойствсплава ТН20, что, очевидно, связано с высоким содержанием кислорода в исходном карбидетитана (известно, что присутствие даже менее 0,2 % кислорода в TiC в значительной степени снижает прочностныесвойства твердых сплавов на основе TiC [108]). Хрупкое разрушениесплавов TiC—Ni—Mo происходит в местах наличия структурных дефектов, расположение и размеры которых оказывают существенное влияние на прочность сплавов. Максимальная прочностьсплавовсистемы TiC—Ni-Mo может составить ~ 3 Г Па, что значительно ниже экстремальной прочностисплава WC - 10 % Со (~ 8 ГПа). Основной причиной такого положения является низкий модульупругостикарбидатитана по сравнению с карбидомвольфрама [95]. Безвольфрамовые твердые сплавы на основе карбидатитана имеют в некоторых случаях более высокие значения вязкости разрушения, которая является мерой сопротивления зарождению и развитию трещин, чем твердые сплавы на основе системы WC—Со (рис. 41) [111]. Поэтому эти безвольфрамовые твердые сплавы могут успешно эксплуатироваться при обработке резанием вязких материалов [111]. Характер износа режущего инструмента из твердых сплавов на основе карбидатитана отличается от характера износа традидионных твердых сплавов. Например, режущий инструмент из безвольфрамового твердого сплава ( КТС эксплуатируется без наростообразования, а абразивныйизнос происходит по задней грани резца. Шероховатость обработанной резцами из сплава КТС поверхности снижается на два класса чистоты по сравнению с обработанной режущим инструментом из сплавов ВК8 и ТНМ [103]. Перспективным направлением в улучшении свойств безвольфрамовых твердых сплавов на основе TiC является введение в их состав легирующих элементов, дисперсионно упрочняющих связующую фазу и увеличивающих пластичностькарбидной фазы. В состав твердых сплавов вводятся V, Nb, Al, W, TiN, В и другие компоненты. Среди специалистов нет единой точки зрения по вопросу влияния добавок ниобия на свойства твердых сплавовсистемы TiC—Ni— Mo. Так, при введении ниобия в твердый сплав TiC-Mo со сложной Ni-Со—Сг связкойпрочностныесвойства и твердостьсплава снижаются (табл.32) [114]. Ишибаши считает, что введение 8—20 % ниобия не оказывает влияния на пределпрочности при изгибе и твердость сплава, в то время как трещиностойкость по Палмквисту максимальна в сплавах с 14—17 % Nb [115]. Большинство исследователей высказывают мнение, что введение ниобия в сплав TiC—Ni-Mo благоприятно сказывается на его физико-механических свойствах* [116]. Из карбидостали марки М6 (см. табл. 35) изготавливаются звенья винтовых питателей, используемых для подачи пластической массы, содержащей 30 % стекловолокна. Звено винта из TiC - стали, эксплуатируемое в условиях сильного коррозионного и абразивного износа, проработало без видимых изменений, тогда как соседнее стальное звено потеряло 17 % от исходного объема [171]. Более высокая стоимость карбидосталей по сравнению с обычными сталями не играет большой роли, если сплавы TiC — сталь применяются в виде армирующих вставок, секторов, облицовок. При оценке экономической целесообразности изготовления деталей из карбидосталей следует учитывать следующие факторы: 1) стоимость порошков карбидатитана и стальной связки; 2) стоимость и технологичность процесса получения карбидосталей и изделий из них; 3) повышение эксплуатационных свойств, которое достигается за счет применения карбидостали [168]. В случае, когда использование карбидостали затруднего по экономическим соображениям, целесообразно применять этот материал для нанесения покрытий на стали различных классов (см. гл. III). Несмотря на довольно широкий круг применения карбидостали, несомненно, что этот материал далеко не исчерпал себя и в будущем масштабы его использования возрастут. 3. Покрытия из карбидатитана С начала 60-х годов широкое распространение получили износостойкие материалы с нанесенными на них покрытиями. Покрытия нашли применение в аэрокосмической промышленности, атомной энергетике, автомобилестроении, при изготовлении инструментальных материалов. Использование покрытий позволяет увеличить в несколько раз срок службы изделий, сэкономить дорогостоящие и дефицитные материалы. карбидтитана является одним из самых эффективных материалов, используемых в качестве износостойкого покрытиями это связано прежде всего с тем, что TiC в наибольшей мере удовлетворяет требованиям, предъявляемым к покрытиям: высокие износостойкость и твердость при высоких и низких температурах; хорошая химическая стабильность; небольшой коэффициент трения, хорошее сцепление с поверхностью материала — основы; окалиностойкость; малая склонность к схватыванию и холодной сварке; способность не разрушаться под воздействием механических и тепловых нагрузок. В настоящее время имеется целая гамма методов нанесения покрытия, причем число новых способов непрерывно увеличивается. В зависимости от требуемых прочности, толщины и пористости покрытий, Применение более жестких режимов приводит к резкому возрастанию количества оксидов в покрытии, что повышает его хрупкость. В ФРГ разработана целая гамма композиций TiC — сплав на основе железа для нанесения покрытийметодом плазменного напыления, прочность которых превышает прочностьпокрытий на основе карбидавольфрама (табл. 64). Наибольший прирост срока службы покрытий TiC - сплав на основе железа по сравнению с покрытиями на основе карбидавольфрама наблюдается при истирании по схеме "металл против песка", например при перемешиваниивзвеси в фосфатном руднике (табл. 65) [216]. Плотные покрытия с пластинчатой структурой получают напылением твердых растворов WC-TiC (чаще всего сплавов 50 % WC - 50 % TiC и 70 % WC — 30 % TiC) или их смесей с кобальтом. твердостьпокрытиясостава 85 % твердого раствора 50 % WC - 50 % TiC и 15 % Со HV = = 700 МПа [210,211]. Для специальных целей получают покрытия плазменным напылением порошков TiC-Mo2C nTiC-TiN. Дальнейшее увеличение использования плазменного напыления покрытий сдерживается низкой производительностью установок, работа которых сопровождается шумом и сильным ультрафиолетовым излучением, значительной пористостьюпокрытий (7—15 %), недостаточно прочной их связью с основой, повышенным содержанием в покрытияхкислорода и азота. Детонационное напыление [217-219] Основное преимущество детонационного газового напыления по сравнению с другими методами — возможность получения покрытий при меньших затратах тепловой энергии. Высокоскоростное соударение напыляемых частиц (до 800-1000 м/с) с поверхностьюизделий обеспечивает образование плотных (пористость меньше 1 %) покрытий, имеющих хорошее сцепление с основой (до 180 МПа) [217]. Температура основы при этом не превышает 200 °С. При детонационном напылении покрытия формируются из твердых пластичных, а не расплавленных частиц. Этот метод используется для нанесения покрытий толщиной 0,03-0,4 мм на материалы с твердостью не выше 40 HRC. На рис. 82 представлена схема детонационного устройства и детонационной установки [218]. Стационарная детонационная установка (пушка) представляет собой реакционную камеру, выполненную в виде трубы, в которую через определенные интервалы вводят точно дозированное количество кислорода, ацетилена и порошкового напыляемого материала. Электроискра вызывает детонацию этой смеси; образующаяся газовая струя доставляет напыляемый материал к поверхности обрабатываемой детали. Катоды на основе карбидатитана с добавками титана могут одновременно служить геттером, так как при высоких температурах из этих катодов происходит интенсивное испарение хорошего геттерирующего материала — титана. карбидтитана также используется в качестве материала контактных катодов при электролизе криолита. Хорошая устойчивость к воздействию жидкого алюминия позволяет значительно снизить контактное сопротивление между графитом и расплавленным алюминием. Для графитовых электродов электрических печей применяют покрытия из TiC-TiN-Cr. Применение TiC в высокотемпературных материалахкарбидтитана является основным компонентом наконечников (защитных чехлов), используемых для изоляции термоэлектродов металлических термопар от химического, эрозионного и механического воздействия окружающей среды. В условияхплавкицветныхметаллов и их сплавов (меди, бронзы, латуни) в индукционных печах наконечник из сплава TiC — 20 % Со, используемый совместно с платинородий-платиновой термопарой, имеет более высокую стойкость в расплаве, термо- и окалиностойкость при температурах 1100°С по сравнению с наконечниками из молибдена и керамики [1]. Высокая стойкостькарбидатитана в расплавахметаллов и их сплавах привлекла пристальное внимание материаловедов. Тигли на основе системы TiC—TiB2 получили широкое распространение для плавки металлов. карбид титана, являющийся перспективным материалом для высокотемпературной электроники, нашел применение в качестве проводящей фазы в керметных резистивных пленках для интегральных схем [270, 271 ]. Пленки, содержащие А12 03 и TiC в соотношении 1 : 1 по массе, осаждают ионно-плазменным распылением на нагретые до 600 °С поликоровые подложки. Пленки TiC—А120з, толщина которых составляет 20—300 нм, имеют электронографически аморфную структуру, сохраняющуюся до 1000 °С. Эти Пленки значительно превосходят по стабильности структурыПленки традиционньгх резисторов Ti-Al203, в которых при 1000 °С наблюдается увеличение размера зерен до 50 нм и изменение фазового состава. Высокая структурная стабильность пленоксистемы TiC—А120з обеспечивает хорошую стабильность электросопротивления при высоких температурах (рис. ПО) [271].