Электродуговая сварка сталей. Справочник.
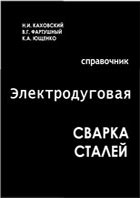
Н.И. Каховский, В.Г. Фартушный, К.А. Ющенко
Наукова думка, 1975 г.
Легированные конструкционные стали
Легирующие элементы образуют с железом и другими элементами твердые растворы и химические соединения, свойства которых в значительной мере определяют свойства стали. Основная цель легирования — придание конструкционным сталям высоких механических свойств» повышение стойкости против хрупкого разрушения, а также обеспечение специальных свойств (например, жаропрочности).
По принятой в сварочной технике классификации легированные стали разделяют на низколегированные, среднелегированные и высоколегированные. Если содержание каждого из легирующих элементов не превышает 2%, а суммарное их содержание — 5%, то сталь называется низколегированной. Если содержание каждого из легирующих элементов находится в пределах от 2 до 5%, а суммарное их содержание не превышает 10%, сталь называется среднелегированной. Высоколегированной называется сталь, содержащая не менее 5% одного из легирующих элементов или не менее 10% суммы легирующих элементов.
Твердые растворы легирующих элементов в железе могут быть образованы по типу замещения или внедрения. Такие элементы, как водород, углерод, азот и бор, растворяются в железе и его сплавах по типу внедрения. При этом растворенные элементы располагаются между узлами решетки растворителя. Все прочие элементы растворяются в железе и его сплавах по типу замещения. В этом случае атомы легирующего элемента располагаются в узлах решеток, заменяя собой атомы растворителя.
Влияние легирующих элементов на свойства сталей. Легирующие элементы существенно влияют на степень совершенства кристаллической решетки. Искажение решетки тем больше, чем больше рознятся диаметрыатомов растворяющего и растворяющегося элементов. В результате легирования происходит упрочение стали, увеличение ее твердости, изменение ряда физико-химических свойспв. Многочисленными исследованиями, проведенными за два последних десятилетия, было установлено, что упрочение а- и у-растворов происходит при легировании не только за счет изменения параметра кристаллической решетки, но и вследствие различия валентностей растворителя и растворяемого элемента. Однако количественная оценка этого фактора весьма затруднена так как не установлена валентность некоторых элементов.
Углерод повышает прочность, снижает пластичность и вязкость легированной стали; он также повышает чувствительность к перегреву и закаливаемости стали и поэтому оказывает отрицательное влияние на ее свариваемость. Увеличение содержания углерода в стали при обычных условияхсварки способствует образованию трещин в околошовной зоне и шве. В современных низколегированных сталях содержание углерода находится в пределах 0,18—0,25%. В сталях, к свариваемости которых предъявляют повышенные требования, содержание углерода не должно превышать 0,12—0,14%. Низко- и средне-легированные конструкционные стали повышенной прочности, содержащие до 0,45% углерода, сваривают с предварительным подогревом, подвергая сварные соединения последующей термической обработке. Влияние углерода усиливается при повышенном содержании в стали марганца, хрома и ряда других элементов.
Марганец — наиболее распространенный элемент в легированных сталях. Он повышает прочностьстали и мало влияет на ее пластичность. При содержании углерода до 0,20% марганец в количестве до 1,2% повышает ударную вязкость низколегированной стали. Повышение содержания марганца до 1,8% рационально с точки зрения улучшения свойствстали при условии ограничения в ней содержания углерода 0,14%. Если встали содержится более 2% марганца, наблюдается ухудшение ее свойств.
Кремний значительно повышает пределпрочностистали и в несколько меньшей степени увеличивает ее предел текучести. Влияние кремния на хладноломкостьстали неоднозначно. Так, введение 0,15— 0,35% кремния в кипящую стальприводит к снижению ее порогахладноломкости на 20—25° (в отсутствие алюминия) и на 40° (при совместном раскислении кремнием и алюминием [13]). С увеличением содержания кремния ухудшается свариваемость стали.
Хром усиливает восприимчивость стали к закалке, особенно при увеличении содержания углерода и других легирующих элементов. Он несколько снижает склонность легированной стали к старению и в небольших количествах способствует некоторому повышению ударной вязкости при комнатной и повышенной температурах [46, 63]. Кроме того, хром, нейтрализуя отрицательное влияние фосфора на ударную вязкость стали, уменьшает ее хладноломкость. При низком содержании углерода и в присутствии марганца и кремнияхром (при содержании до 1%) не ухудшает свариваемости стали. Влияние никеля на свойствастали неоднозначно, В ферритных и низкоуглеродистых сталяхникель повышает запас вязкости, причем тем сильнее, чем выше его содержание и чем ниже содержание углерода. При этом уменьшается порогхладноломкости стали. Имеются данные [11, 14, 63], что при повышении содержания углерода, а также увеличении суммарного содержания легирующих элементов в стали благоприятное влияние никеля быстро нивелируется и даже сменяется отрицательным. В количествах, встречающихся при легировании низколегированных сталей, никель мало влияет на свариваемость последних. Несмотря на положительное влияние никеля на свойства стали, в целом ряде случаев расход его стремятся ограничить из-за дефицитности.
Медь (до 0,5%) вводят в состав некоторых низколегированных сталей для повышения стойкости против коррозии. В таком количестве она не оказывает существенного влияния на свариваемость стали. Как и никель, медь является дефицитным металлом. Молибден в значительной степени влияет на свойства сталей, упрочняя ферритную фазу. Его эффективность понижается с увеличением суммарного содержания легирующих элементов. Молибден устраняет отпускнуюхрупкость стали. Оптимальное его содержание в конструкционных сталях находится в пределах 0,20—0,45%, а дальнейшее увеличение может привести к охрупчиваниюстали [21, 65].
Государственным стандартом предусмотрено специальное буквенное обозначение легирующих элементов (табл. 1,7) с указанием среднего содержания этого элемента. Первые цифры марок стали указывают среднее содержание в ней углерода (в сотых долях процента). Цифра, стоящая после буквы, указывает среднее содержание соответствующего элемента (в процентах). Если после буквы цифра отсутствует, значит данного элемента содержится около 1%. Буква А, стоящая в конце марки легированной стали, свидетельствует об ограничении содержания серы и фосфора (в отличие от маркировки высоколегированных сталей, где буквой А обозначают повышенное содержание азота). В табл. I. 8, 1.9 приведены химический состав и механические свойства низколегированных, а в табл. 1.10 — химический состав легированных конструкционных сталей.
Металлургические особенности сварки покрытыми электродами
При сварке толстопокрытыми электродами защита жидкого металла от воздуха обеспечивается за счет шлако- и газообразующих компонентов покрытия. К шлакообразующим относятся полевой шпат, мрамор, глинозем, титановый концентрат, песок, плавиковый шпат, гематит, двуокись титана; к газообразующим — мрамор, декстрин или крахмал, пищевая мука, целлюлоза к другие органические вещества.
Кроме того, в покрытия входят раскислители, иногда легирующие элементы, а также ионизирующие и вяжущие компоненты. В качестве раскислителей используют ферросилиций, ферромарганец, ферротитан, алюминиевый порошок.
Для легирования или делегирования металла шва с целью придания ему соответствующих свойств в покрытияэлектродов вводят элементы Cr, Ni, Mo, Nb и др. Такая необходимость возникает в случае, если в электроднойпроволоке отсутствует тот или иной легирующий элемент или его количество в ней недостаточно.
К ионизирующим веществам относятся поташ, полевой шпат, гранит; к связующим — жидкое стекло.
В зависимости от вида основного защитного компонента (компонентов) электродныепокрытия в соответствии с ГОСТом 9467—60 делят на следующие группы.
Рудно-кислые покрытия (Р), состоящие из окислов железа, марганца, титана и кремния, представляющие шлаковую основу. В качестве газообразующих чаще вводят крахмал или декстрин, которые при нагревании и плавленииэлектрода образуют газы. Раскисление металла осуществляется путем введения в покрытие ферромарганца. Такие покрытия имеют, например, электроды марок ОММ-5, ЦМ-7, МЭЗ-04.
Фтористо-кальциевые покрытия (Ф), основу которых составляют карбонаткальция (мрамор) и плавиковый шпат. Для раскисления используют ферротитан, ферромарганец, ферросилиций. Наиболее характерную группу электродов с такими покрытиями представляют электроды типа УОНИ-13, применяемые для сварки малоуглеродистых и легированных конструкционных сталей, а также большое количество электродов, применяемых для сварки высоколегированных сталей, в том числе с покрытиями, отличающимися малым отношением количеств мрамора
Глава IV. ДЕФЕКТЫ МЕТАЛЛУРГИЧЕСКОГО ПРОИСХОЖДЕНИЙ
В СВАРНЫХ ШВАХ И СОЕДИНЕНИЯХ
К дефектам металлургического происхождения в сварных соединениях относятся горячие и холодные трещины, газовые пузыри (поры) и неметаллические включения. Поры и неметаллические включения в процессесварки могут образовываться только в металле сварных швов, а трещины — как в сварных швах, так и в околошовной зоне свариваемого (основного) металла, чаще в участке, непосредственно примыкающем к шву.
Образование всех рассматриваемых дефектов зависит не от квалификации сварщика, а главным образом от структуры свариваемой стали, ее химического состава и толщины, метода и режима сварки, а также от состава сварочных материалов (присадочной проволоки, флюсов, защитных газов, электродов и их покрытий).
Эти дефекты в той или иной мере снижают работоспособность и эксплуатационную надежность сварного узла или изделия в целом, поэтому анализу причин, условий их образования и мерам их предотвращения уделяется большое внимание.
Образование трещин, пор и неметаллических включений в сварных швах тесно связано с характером кристаллизацииметалла сварочной ванны, развитием в нем зональной и дендритной химической, а также физической неоднородности и, в конечном счете, с образованием той или иной микроструктуры. Поэтому в первую очередь кратко остановимся на существующих представлениях о механизме и особенностях кристаллизацииметалла сварочной ванны.
IV.1. Кристаллизацияметалла сварочной ванны
и его химическая и физическая неоднородность
Условия кристаллизацииметалла сварных швов значительно отличаются от условийкристаллизацииметалла в отливках и слитках. Характерными особенностями кристаллизацииметалла шва являются: а) сравнительно малый объем жидкого металла сварочной ванны, его высокая температура и интенсивное охлаждение; б) наличие на дне, по бокам и в хвостовой части сварочной ванны готовых центров кристаллизации в виде крупных полуоплавленньгх зерен основного металла, выросших вследствие воздействия высокой температуры дуги; в) одновременные нагрев металла передней части сварочной ванны перемещающейся дугой и охлаждение хвостовой ее части со стороны твердого металла, что обусловливает прямую зависимость скоростикристаллизацииванны от скорости сварки; г) зависимость направленности кристаллизацииметалла сварочной ванны от формы криволинейной поверхности раздела расплавленного и твердого металлов (т. е. от формы провара), что в свою очередь зависит от режима сварки; д) замедленное охлаждение верхней части сварочной ванны при сварке под флюсом и в некоторой степени при сварке толстопокрытыми электродами; е) воздействие на кристаллизую-
щийся и остывающий (затвердевший) металл более значительных собственных (сварочных) поперечных и продольных напряжений.
Некоторые из этих особенностей являются благоприятными, а некоторые — отрицательными с точки зрения структуры и свойствметалла шва. Так, например, в противоположность слиткам и отливкам, сварные швы вследствие большей скоростикристаллизации имеют более тонкую структуру (мельче дендриты и кристаллиты) и, что весьма важно, отличаются меньшей зональной и внутрикристаллитной (дендритной) ликвацией (химической неоднородностью). Благодаря этому, а также вследствие меньшего содержания газов и вредных примесей сварные швы в большинстве случаев обладают более высокими механическими свойствами, чем металл отливок и слитков такого же состава.
Наряду с этим, из-за ряда специфических условий сварки, в частности из-за воздействия сварочных напряжений, не всегда удается получить качественные швы без дефектов металлургического происхождения (например, трещин), не прибегая к специальному легированию наплавленного металла, а иногда и к специальным приемам сварки. С особыми трудностями приходится сталкиваться при сварке ряда сталей, когда необходимо обеспечить свойства литого и нетермообработанного металла шва, равные или близкие к свойствам основного катаного и термообра-ботанного металла. В обоих этих случаях, наряду с оптимальным химическим составом, характер кристаллизацииметалла шва и связанные с этим та или иная его структура и химическая дендритная неоднородность играют значительную роль в получении швов, отвечающих предъявляемым требованиям.
На рис. IV. 1 представлена схема плавильного пространства, кристаллизующейся сварочной ванны и распределения температур впереди и позади дуги при сварке под флюсом. По мере перемещения электрической дуги металл сварочной ванны в ее хвостовой части и по бокам быстро охлаждается благодаря отводу тепла в основной металл и при достижении температурыплавления (точнее, температуры кристаллизации) затвердевает (кристаллизуется). Фронт кристаллизации продвигается вслед за перемещающейся дугой с кратковременными остановками, обусловленными периодичностью охлаждения. Кристаллы растут в направлении, обратном криволинейной поверхности теплоотво-да, разделяющей нерасплавленный основной металл и жидкий металл ванны. Периодичность процесса кристаллизации, по мнению большинства исследователей, обусловлена тем, что после затвердевания первого слоя охлаждение жидкого металла на некоторое время задерживается в связи с выделением скрытой теплоты плавления. Непрекращающийся отвод тепла в глубь основного металла обусловливает кристаллизацию второго слоя и т. д. В связи с этим в шве обнаруживаются слои кристаллизации (выявляемые специальным травлением), имеющие поверхность, соответствующую поверхности теплоотвода. Толщина каждого кристаллизационного слоя не превышает десятых долей миллиметра и находится в прямой зависимости от размера сварочной ванны и в обратной зависимости от скорости теплоотвода.
Сварные швы имеют транскристаллитную (направленную) макроструктуру. Столбчатые кристаллиты каждого последующего слоя кристаллизации и каждого последующего валика шва при многопроходной (многослойной) сварке являются продолжением кристаллитов нижележащего слоя.