Справочник литейщика. Фасонное литье из сплавов тяжелых цветных металлов.
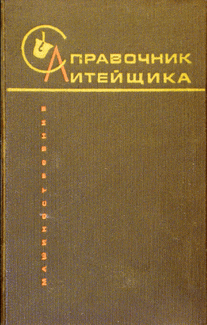
Орлов Н.Д., Чурсин В.М.
Машиностроение, 1971 г.
Глава 1. ШИХТОВЫЕ МАТЕРИАЛЫ
В фасоннолитейном производстве для изготовления сплавов тяжелых цветныхметаллов применяют:
1) первичные цветные металлы, которые используют в качестве основных и легирующих компонентов сплавов; к этой группе шихтовых материалов относятся медь, никель, цинк, олово, свинец, алюминий, кадмий, кобальт, кремний, марганец, сурьма и др.;
2) чушки медных сплавов, получаемые с заводов вторичных цветных металлов;
3) отходы литейных и механических цехов (литники, выпоры, прибыли, бракованные отливки и детали, стружка и пр.);
4) отходы, поступающие со стороны, в том числе железо в виде обрезков проволоки, высечки и т. п.
Химические составы первичных цветныхметаллов и чушек медных сплавов должны соответствовать ГОСТу или ТУ.
Отходы собственного производства и со стороны должны поступать на шихтовку не перемешанными по сплавам, известного химического состава.
МЕТАЛЛЫ
МЕДЬ
Технически чистая медь обладает высокой электропроводностью, теплопроводностью, пластичностью, коррозионной стойкостью в атмосферных условиях, в пресной и морской воде.
Медь имеет низкие литейные свойства, что затрудняет изготовление из нее фасонных отливок. В исключительных случаях отливки, простые по конфигурации, получают из чистой меди или из меди с небольшими присадками олова или цинка, которые улучшают ее литейные свойства, но значительно снижают электропроводность.
Медь (марки М4 и реже марки МЗ) в виде сплавов с другими металлами используют для изготовления самых разнообразных отливок.
Медь поставляют в виде катодныхлистов (пластин), которые должны быть плотные, свободные от остатков электролита.
влияние примесей на свойства меди. Кислород практически не растворим в твердой меди; при затвердевании выделяется из раствора в виде эвтектики Си—Си2О, располагающейся по границам зерен; снижает пластичность и коррозионную стойкость меди; вызывает пористость отливок.
Водород растворим в жидком (8,1 см3 в 100 г при 1200 °С) и твердом (0,06 см3 в 100 г при 400° С) металле; вызывает пористость отливок, а также хрупкость и растрескивание деформированной меди, содержащей Кислород («водородную болезнь»).
Висмут снижает пластичность меди при горячем (0,005% Bi) и холодном деформировании.
Глава II. ЛИТЕЙНЫЕ СПЛАВЫ
ОЛОВЯННЫЕ БРОНЗЫ
Оловянные бронзы — это медные сплавы, основным легирующим компонентом которых является олово. Помимо олова, в состав оловянных бронз входят цинк, свинец, фосфор, никель. Оловянные бронзы, применяемые в промышленности, как правило, содержат олова не более 10—12% и редко 18—20%. На диаграммесостояния (рис. 6) в условияхравновесияграница области а-твердого раствора показана сплошной линией, согласно которой при температурах ниже 520° С растворимость олова в а-твердом растворе очень снижается и происходит распад последнего с образованием новой г-фазы на основе интерметаллического соединения Cu3Sn. Однако последнее возможно только в результате длительного отжига сильно деформированного сплава. Структуру отожженных после литьясплавов следует определять по верхней части сплошной линии и ниже 520° С — по пунктирной. Левая пунктирная линия является границей области а-твердого раствора литых сплавов (так же как и линия солидус). В структуресплавов при температурах ниже 520°С должна присутствовать наряду с а-твердым раствором и Е-фаза, образовавшаяся в результате распада б-фазы (Cu3iSn8) на а и Cu3Sn.
Структура литых сплавов обычно состоит из а и б-фаз вследствие медленного процессараспада последней; 6-фаза обладает высокой твердостью.
Отклонения структуры оловянных бронз от равновесной объясняются высокой склонностью сплавов к ликвации и медленностью процесса диффузии.
Широкий температурныйинтервал затвердевания оловянных бронз является причиной их склонности давать в отливках рассредоточенные усадочные пустоты (пористость).
Оловянные бронзы обладают высокой коррозионной стойкостью и хорошими антифрикционными свойствами.
Глава III. ПЛАВИЛЬНЫЕ ПЕЧИ
В литейном производстве для плавкисплавов тяжелых цветныхметаллов используют топливные и электрические печи.
ТОПЛИВНЫЕ ПЕЧИ
ТИГЕЛЬНЫЕ ПЕЧИ
Тигельные печи преимущественно применяют в мелких ремонтных мастерских. Их разделяют на стационарные с одним или двумя тиглями (рис. 13) и на поворотные с одним тиглем (рис. 14). Поперечное сечениешахты печи на один тигель круглое, на два тигля эллипсовидное. Футеруют шахтушамотным или динасовым кирпичом.
В тигельных печах, работающих на мазуте или газообразном топливе, форсунку или горелку устанавливают в нижней части шахты по касательной к ее стенкам. Плавка тугоплавких сплавов (медных и никелевых) производится в графитовых (графито-шамотных) тиглях. По ГОСТу 3782—54 условную емкость этих тиглей выражают в килограммах расплавленной меди при условии заполнения объема тиглей стационарных печей 95% и поворотных 87%.
Продолжительность срока службы графитовых тиглей зависит от условий хранения их, подготовки к плавке и эксплуатации:
1. При перевозке и хранении тигли необходимо оберегать от сырости.
2. Перед плавкой тигли следует в течение нескольких суток просушить в специальной камере при 70—80° С или на своде пламенной печи; после этого хорошо прогреть на крышке тигельной печи и прокалить в течение 2—3 ч при температуре примерно 600° С.
3. При первой плавке загрузку необходимо производить в докрасна раскаленный тигель, не допуская резких ударов и плотной набивки его шихтой.
Тигельные печи обладают следующими преимуществами: универсальностью (можно плавить разнообразные сплавы); маневренностью (простота перехода с плавки.одного сплава на плавку другого), малым угаром и газонасыщаемостью металла вследствие минимальной поверхности соприкосновения его с печными газами; простотой устройства и эксплуатации. Наряду с этими преимуществами тигельные печи имеют и недостатки: малую производительность, низкий тепловой к. п. д. (0,07—0,1) и большой расход топлива на 1 т выплавляемого металла.
ПОДОВЫЕ ПЕЧИ
Большинство подовых пламенных печей строят с двумя камерами: сжигания топлива и плавильной, на подине которой и плавится металл. Подины выполняют из огнеупорного материала в виде неглубокой, но с большой поверхностью чаши. Футеруют печи обычно шамотным кирпичом и в отдельных случаях используют динасовый и магнезитовый кирпич.
Глава IV. ПРОИЗВОДСТВО СПЛАВОВ
Качество отливок в большой степени определяется качеством сплава, заливаемого в форму. Последний по химическому составу должен соответствовать нормам ГОСТа или ТУ, не содержать окислы и растворенные газы и быть нагретым до заданной температуры.
ОБЩИЕ СВЕДЕНИЯ
Необходимое качество сплава обеспечивается предварительной подготовкой шихтовых материалов, расчетом шихты и соблюдением основных правил плавки.
Подготовка шихтовых материалов. Крупные шихтовые материалы (катоды, чушки, бракованные отливки и пр.) разрезают или разбивают на более мелкие куски, удобные для загрузки их в печь.
Катодные листы (пластины) тщательно очищаются от остатков электролита, бракованные отливки и литники — от формовочной смеси. Паспортная чушка с ликвационными выпотами для производства ответственных отливок не допускается.
Сыпучую и витую стружку после ее дробления подвергают центрифугированию для удаления влаги, масла, эмульсии. стружка в процессецентрифугирования промывается раствором, содержащим 6% жидкого стекла, 4% фосфорнокислого калия 1_0,5% хромокислого калия, 1% едкого натра и 88,5% воды. Затем стружка тщательно просушивается при 200—300° С в специальных печах. Для удаления мелких железных включений сухую стружкупропускают через электромагнитныйсепаратор и после этого брикетируют.
Обрезки листового материала, проволоки, высечки и т. п. после тщательной сортировки и удаления влаги, смазки, пакетируют в пакеты, удобные для загрузки в печь.
В процессе подготовки шихты необходимо следить за тем, чтобы отходы металлов и сплавов различных марок не смешивались между собой. Отходы неизвестного химического состава обязательно предварительно переплавляют в чушки, которые после получения результатов химического анализа используют в качестве шихтового материала.
Расчет шихты заключается в определении весовых соотношений различных видов шихтовых материалов, загружаемых в печь, для получения сплава заданного химического состава. Расчет шихты производят на 100 кг сплава. По заданному химическому составу определяют содержание основных компонентов в 100 кг сплава, а затем содержание их в шихте с учетом угара .
МНОГОКОМПОНЕНТНЫЕ ЛАТУНИ
Для плавки свинцовых латуней наряду с индукционными печами промышленной частоты со стальным сердечником применяют тигельные печи (топливные и индукционные), а также и подовые топливные печи. Применение последних нежелательно из-за высокого угара цинка, особенно, если в составсплава не вводят компоненты, образующие на поверхности расплавленного металла прочную защитную окисиую пленку, например алюминий.
Нецелесообразно применять для плавкилатуней электродуговые печи, так как в районе дуги будет большой угар цинка.
При изготовлении-латуней в индукционных печах промышленной частоты со стальным сердечником из шихты, состоящей из отходов и относительно небольшого количества первичных металлов, применяемых для подшихтовки, рекомендуется следующий порядок плавки. Вначале загружают и расплавляют отходы, затем вводят медь и за 5—8 мин до заливки форм предварительно подогретый цинк и последним свинец.
При приготовлении в этих же печах латуней из первичных металлов вначале одновременно загружают медь, и цинк (25% от общего, веса), затем остаток меди, потом остаток цинка и последним свинец.
При плавке в тигельных печах вначале загружают древесный уголь, тяжелые отходы и медь. После расплавления загружают предварительно подогретый цинк и последним свинец. Не допускается сильный перегревметалла перед введением в него цинка.
Плавка латуней во всех печах ведется под слоем хорошо прожженного и прокаленного древесного угля или флюса. Положительные результаты дает добавка в печь криолита, который заметно разжижает шлак и тем самым уменьшает количество металла, запутавшегося в нем.
Глава VIII. ДЕФЕКТЫ ОТЛИВОК И СПОСОБЫ ИХ ИСПРАВЛЕНИЯ
Дефекты отливок делят на допустимые и недопустимые. Недопустимые дефекты, в свою очередь, подразделяют на исправимые и неисправимые. В случае неисправимых дефектовотливки подлежат окончательной забраковке и переливке.
ДЕФЕКТЫ ОТЛИВОК
Дефекты отливок являются результатом плохого качества металла или формы, а также нарушением технологии заливки, затвердевания и выбивки отливок из форм (табл. 121).
СПОСОБЫ ИСПРАВЛЕНИЯ ДЕФЕКТОВ
Отливки с такими дефектами как трещины, раковины, засор, недолив перед исправлением подвергают специальной подготовке.
Участки отливки, подлежащие исправлению, очищают до здорового металла. Окалину, шлак, формовочную смесь и другие загрязнения удаляют вырубкой пневматическим или ручным зубилом, стальной щеткой, напильником и др.
Крупные раковины вырубают до исчезновения черновин. При скоплении раковин или засора на небольшой площади удаляется сразу вся группа дефектов на глубину их залегания. При недоливах место наплавки зачищают снятием тонкого слоя металла с поверхности отливки. Трещины вырубают на всю длину и глубину.
Чтобы трещина в процессе заварки не распространялась дальше,
необходимо на расстоянии 5—10 мм от концов ее просверлить отверстия
диаметром 6—8 мм сквозные при сквозных трещинах и при несквозных
"на глубину, превышающую глубинутрещины на 2—3 мм. Отливки
перед заваркой подогревают до 500° С.
Электродуговая заварка. Для исправления дефектов применяют электродуговую заварку по методу Бенардоса с помощью угольных электродов и по методу Словянова с помощью металлических электродов.
Присадочные прутки при заварке методом Бенардоса имеют или круглое сечениедиаметром 6—8 мм или прямоугольное сечение 8X6 мм. Диаметр угольных или графитовых электродов 8—10 мм.
Присадочные прутки и металлические электроды готовят из сплавов, близких по составу к материалу отливки.
Например, для заварки оловянных бронз применяют следующие сплавы: 1) 3,28% олова, 8,9% цинка, 0,2% фосфора, 0,31% никеля, 0,32% железа, 5,89% свинца, остальное медь; 2) 7—9% олова, 0,6— 0,8% алюминия, 0,8% марганца, 0,3% железа, до 0,03% фосфора, остальное медь.