Справочник по металлопрокату
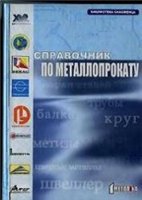
Хорольский Д.Ю.
Металлика, 2003 г.
Кратная характеристика прокатного производства
К основным видам черного проката относятся:
полупродукт, или заготовка, сортовой и листовой прокат, катаные трубы, заготовки деталей машин (особые виды проката) - колёса, кольца, оси, свёрла, шары, профили переменного сечения и др. Большая часть прокатываемых изделий стандартизована. Основное количество проката изготавливается из низкоуглеродистой стали, некоторая часть - из легированной стали и стали с повышенным (больше 0,4 % ) содержанием углерода.
Прокат цветныхметаллов производится главным образом в виде листов, ленты и проволоки. Трубы и сортовые профили из цветныхметаллов изготавливаются преимущественно прессованием.
Технология производства
Производство стального проката на современном металлургическом заводе осуществляется двумя способами:
При первом исходным материалом служат слитки (отлитые в изложницы), которые перерабатываются в готовый прокат обычно в 2 стадии. Сначала слитки нагревают и прокатывают на обжимных станах в заготовку. После осмотра заготовки и удаления поверхностныхдефектов (закатов, трещин и т.п.) производят повторный нагрев н прокатку готовой продукции на специализированных станах. Размеры и формасечения заготовки зависят от её назначения: для прокатки листового и полосового металла применяют заготовки прямоугольного сеченияшириной 400 - 2500 мм и толщиной 75 - 600 мм, называемые слябами; для сортового металла - заготовки квадратного сеченияразмером примерно от 60x60 мм до 400x400 мм, а для цельнокатаных труб - круглого сечениядиаметром 80 - 350 мм. При втором способе, используемом с середины XX в., прокатка исходной заготовки заменяется непрерывным литьем (разливкой) на специальных машинах. После осмотра и удаления дефектов заготовка, как н при первом способе, поступает на станы для прокатки готовой продукции. Благодаря применению непрерывно-литой заготовки упраздняются слябинги и блюминги, повышается качество проката, устраняются потери на обрезку головной части слитка, доходящие у слитков спокойной стали до 15 - 20%. Преимущества применения непрерывно-литой заготовки в производстве проката становятся ещё более значительными при совмещении процессов непрерывного литья и прокатки в одном неразрывном потоке. Для этой цели созданы литейно-прокатные агрегаты, в которых слиток на выходе не подвергается разрезке, проходит печь, где выравнивается температура по сечению, и затем поступает в валки прокатного стана. Таким образом осуществляется процесспрокатки бесконечного слитка, т.е. непрерывное производствопроката из жидкого металла. процесс получил широкое распространение при прокаткецветных металлов; он применяется также для производства стальной заготовки небольших сечений (менее чем 150x150 мм) повышенного качества. Основная трудность в развитии этого процесса состоит в относительно низкой скоростивыхода слитка (1-6 м/мин), что не позволяет в полной мере использовать производственные возможности непрерывного прокатного стана.
Виды проката
Прокатка сортового металла включает следующие основные операции: нагрев до 1100 - 1250 "С; подачу нагретой заготовки к рабочим клетям и прокатку в несколько проходов в калибрах, постепенно приближающих сечение исходной заготовки к сечению готового профиля; резкупроката на пилах или ножницах на части требуемой длины или сматывание в бунты; охлаждение на холодильниках; правку на роликовых правильных машинах; контроль и отправку на склад готовой продукции. Числопроходов выбирается в зависимости от размеров и формысечения исходной заготовки и готового профиля и составляет: для рельсов - обычно 9, балок - 9 - 13, угловых и других сортовых профилей, например зетообразного, - 5 - 12, проволоки - 15 - 21. Выполнение указанных технологических операций производится на специализированных сортовых прокатных станах, представляющих собой поточную автоматическую систему различных машин.
Прокатка листового металла производится из катаных или непрерывно-литых слябов и только листов толщиной свыше 50 - 100 мм - непосредственно из слитков или кованых слябов. В технологический процесс входят следующие основные операции: подачаслябов со склада к нагревательным печам; нагрев; подача к рабочей клетистана и прокатка в несколько проходов (пропусков между валками), причём в первые проходы для получения листов требуемой ширинысляб иногда подаётся в валки поперёк или под углом; правка на роликовых правильных машинах; охлаждение на холодильниках; контроль и разметка; обрезка продольных кромок; обрезка концов, разрезка на листы определённой длины; иногда термическая обработка и покраска; отправка на склад готовой продукции.
Листы толщиной от 4 до 50 мм и плиты толщиной до 350 мм прокатываются на толстолистовых или броневых станах, состоящих из одной или двух рабочих клетей, а листы толщиной от 1,2 до 20 мм - на значительно более производительных непрерывных станах, на которых листы получаются в виде длинных (более 500 м) полос; при выходе из последней клетистанаполосы сматываются в рулон. листы толщиной менее 1,5-3 мм выгоднее прокатывать в холодном состоянии, поэтому дальнейшее уменьшение толщины листа осуществляется обычно на станах холодной прокатки. Для этого рулоны после их получения на непрерывных станах горячей прокатки транспортируются в цех холодной прокатки, где с поверхностиметалла удаляется окалина (в линии непрерывного травления), затем обрезаются концы и производится стыковка (электрическая контактная сварка) для полной непрерывности дальнейшего процесса. Травленые рулоны разматываются и в несколько проходов обжимаются до требуемой толщины (общее обжатие для низкоуглеродистой стали доходит до 75 - 90%). прокатка осуществляется на непрерывных станах, состоящих из 4 или 6 четы-рёхвалковых клетей, или на одноклетевых реверсивных станах. После холодной прокаткиполосу отжигают. Затем её подвергают дрессировке - холодной прокаткеполосы с величиной относительной деформации 1% с целью улучшения поверхности стали, имеющей после горячей прокатки и травления много неровностей, а также для создания поверхностного упрочнения (наклепа), что имеет существенное значение для листов, подвергаемых в дальнейшем холодной штамповке, так как при недостаточно жесткойповерхностиметалла на ней могут появиться линии сдвига. Затем следует правка, резка на листы и упаковка. прокатка (горячая) труб состоит из 3 основных и нескольких вспомогательных операций:
Первая операция (прошивка) - образование отверстия в заготовке или слитке. В результате получается толстостенная труба, называемая гильзой.
Вторая операция (раскатка) - удлинение прошитой заготовки и уменьшение толщины её стенки примерно до требуемых в готовой трубе размеров. Обе операции осуществляются с одного нагрева, но на различных прокатных станах, установленных рядом и входящих в общую системумашин трубопрокатного агрегата. Первая операция выполняется на прошивных станах винтовой прокатки между бочкообразными или дисковыми валками, вторая -на различных прокатных станах: непрерывных, пилигримовых, автоматических и трёхвалковых станах винтовой прокатки.
Третья операция - калибровка (или редуцирование) труб после раскатки. калибровка осуществляется на калибровочных станах, затем Трубы охлаждаются, правятся, контролируются и разрезаются на куски определённой длины. Трубыдиаметром менее 65 - 70 мм подвергаются дополнительной горячей прокатке на редукционных станах. С целью уменьшения толщины стенки и диаметра, получения более высоких механических свойств, гладкой поверхности и точных размеровТрубы после горячей прокатки подвергаются холодной прокатке на специальных станах, а также волочению. прокатка заготовок деталей" машин (штучных изделий) находит широкое применение главным образом в производстве различных тел вращения и профилей переменного сечения: вагонных колёс, осей, бандажей, колец для подшипников качения, шаров, зубчатых колёс, винтов, свёрл и т.д. При этом иногда прокатка используется для выполнения лишь одной операции в комбинации с ковкой или штамповкой.
Некоторые определения
Временное сопротивление (предел прочности) - характеристикапрочности материала, полученная как отношение усилия разрыва образца к площади его первоначального сечения.
Грат - наплывы металла, образующиеся при сварке стальных труб на их внутренней поверхности. Ухудшают гидравлические характеристикитрубопровода и способствуют его засорению.
Передел - процесс переработки железной руды в готовые металлические изделияпроходит четыре этапа (передела), первые три из которых осуществляются горячим способом:
1-й передел - изготовление чугуна;
2-й передел - изготовление стали;
3-й передел - изготовление стального проката;
4-й передел - волочениепроволоки и изготовление метизов.
Прокатное производство - получение путем прокатки из стали и др. металлов различных изделий и полуфабрикатов, а также дополнительная обработка их с целью повышения качества (термическая обработка, травление, нанесение покрытий).
Сортамент - перечень прокатываемых изделий с указанием размеров.
Травление - химическое или электрохимическое растворениеповерхности твердых материалов с практической целью.
1.1 КЛАССИФИКАЦИЯ МЕТАЛЛОВ
Каждый металл отличается строением и свойствами от другого, тем не менее по некоторым признакам их можно объединить в группы (рис. 1.1). Прежде всего, все металлы разделяют на две большие группы - черные и цветные металлы.
Черные металлы (во главе с железом) имеют темно-серый цвет, большой удельный вес (кроме щелочноземельных), высокую температуруплавления и относительно высокую твердость.
Цветные металлы (во главе с медью) чаще всего окрашены (красные, желтые, белые), обладают большой пластичностью, малой твердостью, и относительно низкой температурой плавления.
Черные металлы, в свою очередь, подразделяются на:
Железные металлы - железо, кобальт, никель (так называемые ферромагнетики) и близкий к ним по свойствам марганец. Кобальт, никель и марганец часто применяют как добавки к сплавам железа, а также в качестве основы для соответствующих сплавов, похожих по своим свойствам на высоколегированные стали.
Тугоплавкие металлы - металлы температура плавления которых выше, чем железа (т.е. выше 1539°С). Применяются как добавки к легированным сталям, а также в качестве основы для соответствующих сплавов. Урановые металлы - актиниды, имеющие преимущественное применение в сплавах для атомной энергетики.
Редкоземельные металлы - лантан, церий, неодим, празеодим и другие, объединяемые под названием лантаноидов, и сходные с ними по свойствам иттрий, скандий. Эти металлы обладают весьма близкими химическими свойствами, но довольно различными физическими (температура плавления и др.). Применяются они как присадки к сплавам других элементов. Щелочноземельные металлы п свободном металлическом состоянии применения не имеют, за исключением специальных случаев (например, в качестве теплоносителей в атомных реакторах).
Цветные металлы подразделяются на:
Легкие металлы - бериллий, магний, алюминий, обладающие малым удельным весом.
Благородные металлы - серебро, золото, металлы платиновой группы (платина, палладий, иридий, родий, осмий, рутений). К ним может быть отнесена и «полублагородная» медь. Обладают высокой устойчивостью к коррозии. Легкоплавкие металлы - цинк, кадмий, ртуть, индий, олово, свинец, висмут, таллий, сурьма и элементы с ослабленными металлическими свойствами - галлий, германий.