Справочник молодого термиста.
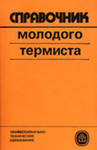
Ю.Е. Седов, А. М. Адаскин.
Высшая школа, 1986 г.
Термическая обработка — процесс тепловой обработкиизделий из металлов и сплавов с целью изменения их структуры и свойств, заключающийся в нагреве до определенной температуры, выдержке и последующем охлаждении с заданной скоростью. Тепловое воздействие может сочетаться с химическим (химико-термическая обработка, см. п. 1.7) и деформационным (термомеханическая обработка, см. п. 1.8). Термической обработке подвергают заготовки (прокат, поковки, отливки к т. п.) для улучшения технологических свойств (обрабатываемости давлением, резанием и др.) и готовые изделия (детали, инструменты) с целью обеспечения требуемых эксплуатационных свойств.
Превращения в стали при нагреве. При температуре Ас1 перлит превращается в аустенит. Нагрев доэвтектоидной стали и интервале Лс —Асг вызывает превращениеферрита в аустенит; в заэвтектоидной стали в интервалетемператур Ас—Асм происходит растворение вторичного цементита в аустените. Одновременно нагрев доэвтектоидной стали выше Асг, а эвтектонднсй и заэвтектоидной выше Ас1 ведет к росту зерна аустенита. При этом снижаются прочность и ударная вязкость (особенно сильно), повышаются порог хладноломкости, склонность к закалочным трещинам и деформациям. Чтобы предупредить рост зерна аустенита, температуры нагрева при термической обработке ограничивают, величину зерна контролируют.
Превращения стали при охлаждении. При охлаждениистали со структуройаустенита до температур ниже Art аустенит становится неустойчивым и претерпевает превращение. Получаемые при этом структура и свойства зависят от скорости охлаждения. Ее влияние отражают диаграммы изотермического превращенияаустенита (строятся для конкретных сталей с определенным содержанием углерода, рис. 1.4). Эти диаграммы имеют важное значение для практики термической обработки стали, так как структура и свойстваПродуктовраспада аустенита, полученные в результате изотермической выдержки после переохлаждения до заданной темпе ратуры или же после непрерывного охлаждения до этой температуры, практически одинаковы. В зависимости от степенипереохлажденияаустенита различают перлитное, промежуточное или мартенсит-нос превращения (табл. 1.4).
Термическая обработка стали, заключающаяся в нагреве выше критических температур и охлаждении, в результате которого образуется мартенсит, называется закалкой. Охлаждение должно осуществляться со скоростью больше критической. Критическая скорость закалки—минимальная скорость охлаждения, при которой подавляются диффузионные превращения и аустенит превращается в мартенсит.
Закаливаемость — свойствостали приобретать высокую твердость в результате закалки. Она зависит от содержания углерода. Чем его больше, тем выше твердостьстали после закалки.
П р ок а л и в а е м ост ь — свойствостали воспринимать закалку па определенную глубину. За глубину закаленного слоя условно принимают расстояние от поверхности до зоны, в структуре которой содержится 50 или 90 % мартенсита (остальное троостит). Прокаливаемость обычно оценивают критическим диаметром d» — диаметром (размером) сечения изделия, прокаливающегося насквозь (в центре 50 или 90 % мартенсита). Она тем выше, чем больше устойчивость переохлажденного аустенита и, следовательно, меньше критическая скорость закалки. Наименьшую Прокаливаемость имеют углеродистые стали (dK=l0-r-l5 мм), у которых минимальная устойчивость переохлажденного аустенита (1—2 с) и очень высокая икр.
Внутренние напряжения возникают в основном в процессе закалки и разделяются на тепловые и структурные. Тепловые (или термические) напряжения появляются вследствие неравномерного охлаждения различных частей (поверхности и сердцевины) изделия. Структурные напряжения являются результатом превращенияаустенита в мартенсит, который имеет больший объем, чем аустенит. Тепловые и структурные напряжения возникают одновременно и суммируются. Знак остаточных напряжений определяется соотношением их абсолютных величин. Наиболее опасными являются растягивающие напряжения на поверхности.
Превращения в стали, закаленной на мартенсит, при нагреве. После закалки сталь получает типичную структуру, состоящую из мартенсита и остаточного аустеннта, которые являются неравновесными фазами и при последующем нагреве претерпевают превращения. Количество остаточного аустенита тем больше, чем выше содержание углерода в стали. Кроме того, в закаленных заэвтектоидных сталях присутствует вторичный цементит, который яе испытывает превращений.
В процессе нагрева закаленной стали (отпуска) до 500—550 °С происходит распадмартенсита на феррито-цементитную смесь, прев. ращение остаточного аустенита по бейнитному механизму, снятие внутренних напряжений.
1.4. Влияние легирующих компонентов
Легирующие компоненты — элементы, которые специально вводят в сталь для изменения се структуры и свойств. Стали, содержащие легирующие компоненты (элементы), называют легированными. Легирующими могут быть элементы, взаимодействующие с основными компонентами стали: железом (табл. 1.5) и углеродом (табл. 1.6), С железом легирующие элементы, как правило, образуют твердые растворы замещения, оказывая влияние на полиморфное превращение.
Основное влияние легирующих компонентов в конструкционных сталях заключается в том, что, растворяясь при нагреве в аустените, они замедляют диффузионные превращения, задерживая распадаустенита при охлаждении и уменьшая критическую скорость закалки. Это повышает Прокаливаемостьстали в позволяет охлаждать изделия при закалке более медленно. В результате легирование конструкционных сталей повышает прочностныесвойстваизделий большого сечения, уменьшает деформацию при закалке изделий сложной конфигурации. При этом нерастворившиеся при нагреве карбиды задерживают рост зернааустенита и дополнительно повышают прочность. Замедляя диффузионные процессы, легирующие компоненты задерживают также распадмартенсита при отпуске закаленной стали, что обеспечивает сохранение высокой твердости и прочности при нагреве.
Легирование инструментальных и специальных сталей и сплавов позволяет получать требуемые механические, физические и химические свойства (см. соответствующие разделы справочника).