Резание металлов.
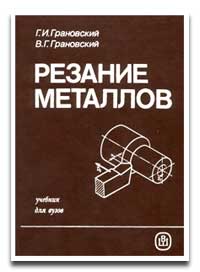
Г.И.Грановский, В.Г.Грановский.
Высш. школа,, 1985 г.
ПОДГОТОВКА КОНСТРУКЦИОННЫХ МЕТАЛЛОВ К ОПЕРАЦИЯМОБРАБОТКИ РЕЗАНИЕМ. Выпускаемый металлургической промышленностью стальной прокат разных профилей и сечений поставляется машиностроительным заводам в виде прутков, полос и листов. Перед тем как приступить к изготовлению деталей машин, поступивший стальной прокат разделяют в заготовительных цехах на мерные куски. Часть заготовленных мерных кусков стального проката поступает непосредственно в механические цехи. Другую часть в кузнечно-прессовых цехах перерабатывают в поковки и штамповки, которые по форме и размерам более близки к готовым деталям. Это позволяет в значительной степени сократить трудоемкость операций, связанных с обработкой резанием. Часто из мерных кусков стального проката разных марок сваривают неразъемную заготовку, которую затем подвергают механической обработке резанием. При необходимости мерные куски стального проката перед механической обработкой поступают в термический цех для предварительной термической обработки. Чугун, алюминий и частично сталь перерабатывают в фасонное литье нужных форм и размеров, например при изготовлении корпусных деталей. Продукцию заготовительных производств — кузнечно-прессовых, литейных, сварочных, термических и механических цехов,— предназначенную для последующей механической ОБРАБОТКИ резанием с целью изготовления из них необходимых деталей, принято называть заготовками. Масса заготовок всегда больше массы изготовленных из них готовых деталей. Избыток массы, определяющий размер припуска, надлежит срезать с заготовок в процессе механической обработки. Удаление общего припуска с поверхностей заготовок осуществляется обычно за несколько технологических операций режущими инструментами разного вида путем деления его на межоперационные припуски. В теории и практике резания МЕТАЛЛОВ межоперационные припуски на обработку предопределяют глубину резания. § 1.3. ЭЛЕМЕНТЫ РЕЗАНИЯ. ОСНОВНЫЕ ПОНЯТИЯ И ОПРЕДЕЛЕНИЯ ПОВЕРХНОСТИ НА ОБРАБАТЫВАЕМЫХ ЗАГОТОВКАХ. Заготовки, предназначенные для изготовления деталей машин, имеют исходные поверхности. В процессеОБРАБОТКИ резанием с заготовки, слой за слоем, срезается припуск на обработку, в большинстве случаев прилегающий к имеющимся на заготовке поверхностям. За первый проход режущего инструмента вместе с поверхностным слоем с заготовки срезается и ее исходная поверхность. При этом на заготовке образуется новая поверхность. За второй проход того же или другого режущего инструмента с заготовки срезается второй слой металла и вместе с ним поверхность, образованная во время первого прохода инструмента. После второго прохода на заготовке опять образуется новая поверхность. В сплошном металле заготовок с помощью сверл могут быть изготовлены отверстия. При сверлении срезается ограниченная площадь исходной поверхности заготовки, равная площади поперечного сечения просверливаемого отверстия. По мере углубления сверла в металл в заготовке образуется новая цилиндрическая поверхность. ПОВЕРХНОСТИ на заготовках, срезаемые за каждый очередной проход инструмента, принято называть обрабатываемыми поверхностями. Поверхности на заготовках, вновь образуемые во время очередного прохода инструмента, называют обработанными поверхностями. Промежуточную поверхность, временно существующую в процессе резания между обрабатываемой и обработанной поверхностями, принято называть поверхностью резания (рис. 1.1). ГЛУБИНА РЕЗАНИЯ. Чтобы срезать слой металла, оставленный на заготовке как припуск на обработку, лезвия инструмента должны проникнуть в металл на глубину, равную этому припуску. В этом случае весь припуск срезается за один проход инструмента. Если припуск велик, то его срезают за два прохода или более. Величину проникновения лезвий инструмента в металл заготовки во время каждого прохода принято называть глубиной резания. ГЛУБИНА резания обозначается буквой t и выражается в миллиметрах. В большинстве случаев ОБРАБОТКИ металлов резанием ГЛУБИНА резания определяется как расстояние между обрабатываемой и обработанной поверхностями, измеряемое в направлении, перпендикулярном обработанной поверхности (рис. 1.1). При сплошном сверленииотверстийГЛУБИНА резания равна радиусу сверла. При торцовом фрезеровании ГЛУБИНА фрезерования равна ширине обрабатываемой заготовки, если она меньше диаметра фрезы. При точении, расточке, рассверливании, развертывании отверстийГЛУБИНА резания выражается уравнением t = (D — d)/2, где D и d при наружной обточке — соответственно диаметр обрабатываемой и обработанной поверхностей, а при внутренней обработке, наоборот, D — диаметр обработанной поверхности и d — диаметр обрабатываемой поверхности. ДВИЖЕНИЯ, ОСУЩЕСТВЛЯЕМЫЕ МЕХАНИЗМАМИ МЕТАЛЛОРЕЖУЩИХ СТАНКОВ. Рабочий процесс резания возможен только при непрерывном относительном взаимном перемещении обрабатываемой заготовки и лезвий режущего инструмента. Обрабатываемые заготовки и режущие инструменты приводятся во взаимосогласованные движения МЕХАНИЗМАМИ металлорежущих станков в соответствии с настройкой их кинематических цепей. Движения могут быть сообщены заготовке и инструменту одновременно, в последовательном порядке, чередуя Движения каждого из них, а также только одному из них — инструменту или заготовке. Кинематика станков основана на использовании механизмов, сообщающих исполнительным органам только два простейших Движения — вращательное и поступательное. Сочетания и количественные соотношения этих двух движений определяют все известные виды ОБРАБОТКИМЕТАЛЛОВ резанием. В процессе резания поступательное или вращательное движение одного из исполнительных органов станка сообщает заготовке или режущему инструменту главное движение резания Dr, происходящее с наибольшей скоростью по сравнению с движениями других органов. § 2.4. БЫСТРОРЕЖУЩИЕ ИНСТРУМЕНТАЛЬНЫЕ СТАЛИ ХИМИЧЕСКИЙ СОСТАВ И МАРКИРОВКА. Количество марок быстрорежущих сталей велико. При этом характерным для этой группы инструментальных сталей является высокая степень легирования. Принципы маркировки быстрорежущих сталей аналогичны конструкционным сталям, за исключением того, что вольфрам в них закодирован буквой Р, а не буквой В, в марках также опушены данные о содержании углерода и хрома. Основным легирующим элементом многих марок быстрорежущих сталей является вольфрам, который входит в состав всех марок в количестве 5,5... 19,5 %. Вольфрам, взаимодействуя с углеродом, образует карбиды вольфрама, которые при термообработке равномерно распределяются по всему объему и не склонны к концентрации на границах зерен или в виде конгломератов. Присутствие в сталивольфрама в указанных количествах приводит к тому, что углеродцеликом оказывается связанным в сложные карбиды и благодаря этому сталь приобретает высокую твердость, температурой износостойкость. К недостаткам легирования вольфрамом можно отнести лишь некоторое уменьшение теплопроводности стали. Кроме вольфрама быстрорежущие стали легируют молибденом, ванадием и кобальтом. Действие молибдена на свойствастали аналогично вольфраму, но проявляется в более активной форме. Введение молибдена позволяет уменьшить содержание в стали дефицитного вольфрама. Однако в связи с охрупчивающим воздействием содержание молибдена в быстрорежущих сталях не превышает 5 %. Присутствие молибдена способствует повышению теплопроводных свойствсталей и тем самым снижению температуры лезвий инструментов. Легированиеванадиемприводит к заметному увеличению контактной твердости стали, но уменьшает ее теплопроводность. В процессе термообработкиванадий способствует образованию мелкозернистой мартенситнойструктуры и несколько снижает хрупкость. Поэтому ванадиевые быстрорежущие стали успешно работают при обработкематериалов повышенной прочности и твердости, хотя и с ограниченными скоростями резания. Недостатком ванадиевых быстрорежущих сталей является склонность к появлению прижогов при шлифовании и заточке. Присутствие в сталикобальта повышает ее износостойкость и теплопроводность. Благодаря последнему свойству инструментами из кобальтовых сталей можно производить обработку резанием конструкционных сталей с более высокими по сравнению с другими быстрорежущими сталямискоростями резания, а также использовать их для ОБРАБОТКИсталей повышенной твердости и пластичности. Быстрорежущие стали могут быть как одно-, так и многокомпонентными в зависимости от числа основных легирующих элементов. Благодаря легированию одновременно несколькими компонентами можно в конкретных производственных условиях выбрать такую марку быстрорежущей стали, которая обладает наиболее благоприятным сочетанием физико-механических свойств. Химический СОСТАВ быстрорежущих сталей и деление их на группы в зависимости от легирующих элементов показаны в табл. 2.3. § 2.5. ТВЕРДЫЕ СПЛАВЫ ХИМИЧЕСКИЙ СОСТАВ И МАРКИРОВКА. Твердые СПЛАВЫ делятся на три подгруппы: волъфрамокобалътовую, условно обозначаемую буквами ВК, вольфрамотитанокобалътовую ВТК и вольфрамотитанотанталокобальтовую ВТТК. В СОСТАВ твердых сплавов той или иной подгруппы входят вольфрам, титан, тантал, кобальт и углерод. При этом вольфрам, титан и тантал входят в состав твердых сплавов в химически связанном состоянии, образуя твердые и температуростойкие карбиды вольфрама, титана и тантала. углерод в твердых сплавах также присутствует только в химически связанном в карбиды вышеуказанных элементов виде. кобальт входит в СОСТАВ твердых сплавов в химически не связанном (металлическом) состоянии, размещаясь между порошкообразными частицами карбидов и связывая их в единый монолит. Содержание кобальта в твердом сплаве определяет его механическую прочность. Увеличение кобальта в твердом сплаве уменьшает хрупкость, но вместе с этим уменьшает твердость и износостойкость (табл. 2.5). В маркировке твердых сплавов буквами В и Т обозначается наличие в составекарбидов вольфрама, титана и тантала. Цифры в марках твердых сплавов показывают содержание (в процентах) кобальта и карбидовтитана В подгруппе ВТТК за буквами ТТ указывается суммарное содержание карбидовтитана и тантала. Содержание карбидоввольфрама не указывается. МЕХАНИЧЕСКИЕ СВОЙСТВА. По механической прочности твердые СПЛАВЫ в целом уступают инструментальным сталям. Пределпрочности на растяжение у твердых сплавов настолько мал, что не позволяет им в рабочих условиях выдерживать растягивающие нагрузки, и они могут работать только на изгиб и сжатие (см. табл. 2.5). Значительно (в 2,5.. .3,2 раза) уступая инструментальным сталям по прочности на изгиб, твердые СПЛАВЫ обладают высоким пределомпрочности на сжатие и по этому параметру соответствуют или даже превосходят инструментальные стали. Из табл. 2.5 видно, что твердые СПЛАВЫ подгрупп ВК и ВТТК в 1,1... .. .3,5 раза имеют более высокие прочностные характеристики, чем твердые СПЛАВЫ подгруппы ВТК. Природная твердость твердых сплавов, т. е. твердость, полученная непосредственно при их изготовлении без дополнительной термообработки, превышает твердость термообработанных быстрорежущих сталей и, измеренная по шкале А Роквелла, колеблется в пределах HRA 87.. .91. ТЕМПЕРАТУРОСТОЙКОСТЬ. Карбиды вольфрама и титана, составляющие основу твердых сплавов, обладают высокой природной температуростойкостью. Увеличение содержания в твердом сплавекарбидов вольфрама, титана и тантала (см. табл. 2.5) при соответствующем уменьшении содержания кобальта ведет к повышению температуростойкости твердых сплавов. Особенно сильно на повышение температуростойкости влияет наличие в составе твердых сплавовкарбидовтитана и тантала. Высокая температуростойкость дает возможность вести твердосплавными инструментами обработкуМЕТАЛЛОВ с высокими скоростями резания с допускаемой на лезвиях температурой свыше 1000°С. В этом заключается преимущество твердых сплавов перед инструментальными сталями. ПРАКТИЧЕСКОЕ ИСПОЛЬЗОВАНИЕ ТВЕРДЫХ СПЛАВОВ. Из твердых сплавов разных марок промышленностью изготовляется большая номенклатура пластинок различных стандартныхформ и размеров. Твердыми, температуростойкими и износостойкими твердосплавными пластинками оснащают все виды токарных резцов и значительную часть фрез. Их устанавливают на зенкерах, развертках, протяжках, зуборезных и резьбонарезных инструментах. Номенклатура инструментов, оснащенных твердыми сплавами, продолжает расти. Для высокопроизводительной ОБРАБОТКИ специальных конструкционных материалов мелкоразмерные сверла, зенкеры, развертки и фрезыцеликом изготовляют из твердых сплавов.