Применение смазочно-охлаждающих технологических жидкостей
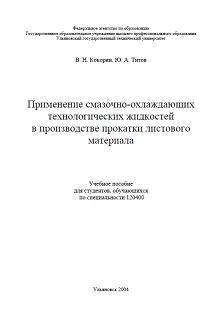
В.Н. Кокорин, Ю.А. Титов
Ульяновск, 2004 г.
1. ФУНКЦИОНАЛЬНОЕ НАЗНАЧЕНИЕ СОТС
1.1. ХОЛОДНАЯ ПРОКАТКА
Применение технологических смазок и смазочно-охлаждающих жидкостей (СОЖ)
при прокатке обеспечивает снижение трения между валками и полосой и их охлаждение.
Прокатка является основным, но далеко не единственным местом их применения. Со смаз
кой в прокатном производстве связаны предварительное промасливание, отжиг, защитная
смазка готовой продукции и т. д. По существу весь комплекс процессов, определяющих физико-химические явления на поверхности металла, обусловлен трением, смазкой и другими внешними средами, воздействующими на поверхность металла. Поэтому вопросы, связанные с эксплуатацией технологических смазок и смазочно-охлаждающих жидкостей, следует рассматривать только в комплексе со всеми элементами производственного цикла холодной
прокатки. Определяющим звеном в этой цепи является процесс в очаге деформации.
Рассматривая трение при холодной прокатке, в первую очередь следует определить
его место в теориипроцесса и технологии. Затем необходимо выявить основные закономерности и характер трения для рассматриваемого случая. После этого можно выбрать составы
и способы применения технологических смазок и эмульсий.
Рис. 1 иллюстрирует взаимосвязь процессатрения с технологическими факторами
прокатки, а также качеством и сортаментом готовой продукции. трение определяет силовые условия процесса, формирование микрогеометрии поверхности, износ и охлаждение валков. Силовые условияпрокатки определяются фрикционными параметрами трения, от которых зависит толщина прокатываемой полосы, точность прокатки и требуемая мощность оборудования.
Пока станвыпускает определенную продукцию, в большинстве случаев нет необхо-
димости снижать трение, которое обеспечивается применяемой смазкой. Однако, если улучшить характеристики трения, то на четырехклетевом стане можно прокатывать лист, для обжатия которого требуется пятиклетевой стан, или даже осуществить то же обжатие за три прохода на реверсивном стане [1]. Максимально возможное обжатие и минимально возможная толщина определяются для каждого стана применением той или иной смазки. Поэтому многоклетевые современные станы холодной прокатки, имеющие обычно диаметр рабочих валков около 500 мм, в зависимости от вида продукции (лист, жесть, высокопрочные стали)
используют разные типы смазочно-охлаждающих жидкостей [2].
Точность прокатки по длине и ширинеленты зависит от постоянства условий трения
наряду с такими факторами, как равномерность охлаждения, стабильность механических
свойств полосы и т. д. [1]. Вид смазки должен быть учтен при расчете возможной разнотолщинности полосы; соответствующим подбором смазки можно добиться получения минимальной разнотолщинности полосы.
Формирование поверхностиполосы в самом широком смысле определяется смазкой и
инструментом (валки) [3]. Микрогеометрия поверхностипроката формируется совместным воздействием на полосуинструмента и смазки. В значительной мере смазка определяет те изменения, которые происходят на поверхностиметалла в процессе его отжига. Образование сажистых налетов, пятен, цветов побежалости определяется остатками смазки и продуктовизноса на поверхностиметалла после прокатки. Образование многих дефектовповерхностисвязано с применением смазки, которая может как предотвращать, так и способствовать их появлению. Дефекты могут возникать собственно при прокатке (риски, царапины), после отжига (сажа, пятна) и до прокатки — в результате травмирования поверхностиполосы при травлении, смотке и размотке рулонов, транспортировке. Эти Дефекты тоже связаны со смазкой и трением, но не столько на самом прокатном стане, сколько при других производственных операциях, где тоже используются различные смазки (например, промасливание подката) и другие жидкости (моющие средства, вода с добавками ПАВ в петлевых ямах).
1.2. КЛАССИФИКАЦИЯ СОТС ПРИ ПРОКАТКЕ
1.2.1. ТРЕБОВАНИЯ, ПРЕДЪЯВЛЯЕМЫЕ К ТЕХНОЛОГИЧЕСКИМ
СМАЗКАМ И ЖИДКОСТЯМ
Технологические смазки должны удовлетворять целому ряду требований техническо-
го, экономического и санитарно-гигиенического характера. В зависимости от назначения и конструкции прокатного стана перечень требований к смазке может меняться. Однако имеются и общие, основные требования, которые указаны ниже:
- снижение сил внешнего трения (коэффициента трения);
- уменьшение износа и предотвращение налипания металла на валки;
- обеспечение чистоты и оптимальной шероховатостиповерхности проката;
- высокая теплоемкость (для смазочно-охлаждающих жидкостей);
- стабильность состава и свойств;
- удобство подачи на валки и металл;
- отсутствие вредного воздействия на металл и оборудование (коррозия и проч.);
- нетоксичность, отсутствие неприятного запаха;
- минимальное загрязнение и простота очистки сточных вод;
- дешевизна и недефицитность (для смазок широкого применения).
Некоторые из указанных требований нуждаются в дополнительном пояснении.
Снижение сил трения на контактной поверхности в очаге деформации, как уже отмечалось, является одним из основных назначений технологической смазки. Под эффективностью смазки обычно понимают именно ее антифрикционную эффективность.
Однако снижение сил трения сопровождается ухудшением захватывающей способности валков. Поэтому уменьшение коэффициентатрения ограничено пределом, определяемым условиями захвата:
В случае нарушения соотношений (1) или (2) нормальный процесспрокатки прекращается, так как возникает буксование валков по металлу.
Условия трения при прокатке являются оптимальными тогда, когда величина сил трения минимальна, но достаточна для надежного захвата полосы валками. При выборе технологической смазки необходимо учитывать это основное положение.
Требования к чистоте поверхностиметалла особенно высоки при производстве холоднокатаных листов конструкционного назначения. Такие листы (полосы) поступают на отжиг без предварительной очистки. Смазка, остающаяся на поверхности металла, не должна быть причиной образования (при отжиге) черных пятен, сажи, пригаров и других поверхностныхдефектов подобного характера. Хорошие результаты дают смазки, обладающие моющими свойствами. Они способствуют удалению с поверхностиметалла различных загрязнений, как наносимых на предыдущих переделах, так и образующихся в процессе прокатки.
Применение смазки с аналогичной целью при дрессировке отмечено выше.
При производстве жести и других видов продукции с металлическими и неметаллическими покрытиямиполосы перед поступлением на отжиг, как правило, подвергаются обезжириванию в чистильно-моющих агрегатах. В этом случае моющая способностьсмазки имеет меньшее значение.
По своим физическим свойствамсмазка должна быть удобной для подачи на валки и
металл. В этом отношении явным преимуществом обладают маловязкие смазки и смазочноохлаждающие жидкости. Применение высоковязких смазок в чистом виде, несмотря на их эффективность, практически трудно осуществимо. Температураплавлениясмазки не должна быть выше 35—40° С.
На современных высокопроизводительных станах годовой расходсмазки составляет
сотни тонн. Поэтому желательно применять смазки, которые были бы дешевле или по крайней мере не дороже рядовых минеральных масел. Нельзя признать экономичным использование в качестве смазки жиров и масел, относящихся к категории пищевых продуктов. Лишь
в случае производства особо ответственных изделий в относительно небольших количествах
вопросы стоимости и дефицитности смазки отходят на второй план.
Следует отметить, что не существует универсальных смазок, отвечающих в полной
мере всем вышеуказанным требованиям и пригодных для любых условий прокатки. В связи с этим на станах разного типа и назначения применяют разные смазки. Они различаются как по химическому составу, так и по физическому (агрегатному) состоянию.
Многообразие требований к технологическим смазкам обусловливает сложность и
трудность задачи по изысканию новых смазок и внедрению их в производство.
1.2.2. ОСНОВНЫЕ ТИПЫ ПРОКАТНЫХ СОТС
Смазки можно классифицировать по химическому составу, агрегатному состоянию,
назначению и др. По агрегатному состоянию смазки, используемые в прокатном производстве, можно разделить на три основные группы: 1 - масла и водомасляные смеси; 2 - эмульсии; 3 - твердые смазки.
Классификационная схема технологических смазок [1, 5, 19 и др.], включающая масла
и эмульсии для прокатки, приведена на рис. 2. Эта схема дает перечень типовых составов и отражает связь между ними. На ее основе общая укрупненная КЛАССИФИКАЦИЯ смазок для обработкиметалловдавлением состоит из следующих групп веществ и их сочетаний: минеральные масла, жиры, минеральные масла с добавками, эмульсии без эмульгатора, эмульсии с эмульгатором. В конечном итоге ассортимент исходных продуктов, подлежащих изучению, включает углеводороды минеральных масел, жиры, жирные кислоты, мыла и изготовленные на их основе смазки и эмульсии.
Масла и водо-масляные смеси
На прокатныхстанах применяют в основном жидкотекучие масла, удобные для нанесения на валки и металл. По химическому составу их подразделяют на следующие подгруппы:
а) минеральные масла;
б) растительные и животные жиры;
в) масла на основе синтетических жирных кислот;
г) смеси минеральных масел с растительными или синтетическими (компаунды);
д) смазки на основе отходов производства растительных масел.
Из минеральных масел при прокатке применяют трансформаторное, индустриальное
12 и 20 (веретенное 2 и 3), цилиндровое 11, цилиндровое 24 (вискозин), прокатное 28 (брайтсток) и др. Эти масла изготавливают из нефти.
Указанные масла применяют при прокатке в чистом виде или с небольшими добавка-
ми антикоррозионных, моющих, противоокислительных и других присадок. Масла с присадками иногда называют легированными. К числу наиболее распространенных растительных
масел, получивших применение в качестве технологической смазки, относятся: пальмовое,
касторовое, хлопковое, подсолнечное, кориандровое.
Растительные масла (жиры), как и животные, представляют собой сложную смесь
глицеридов, т. е. сложных эфиров глицерина (трехатомного спирта), и жирных кислот.
Входящие в состав глицеридов жирные кислоты принадлежат к классу органических
соединений, называемых карбоновыми кислотами. Они характеризуются наличием карбоксильной группы СООН и углеводородного радикала. Углеводородные радикалы СН3(СН2)n могут быть насыщенными (без двойных связей) и ненасыщенными (с одной или несколькими двойными связями).
Различие в физико-химических свойствах жирных кислот обусловливается длиной и
формой молекулярной цепи и степенью ненасыщенности углеводородного радикала. В животных жирах содержатся в значительном количестве насыщенные жирные кислоты типа стеариновой, в растительных — ненасыщенные кислоты типа олеиновой, линолевой.
Животные жиры, из-за высокой температурыплавления и дороговизны, в качестве
технологической смазки при прокатке, применяются очень редко.
Растительные масла используются как в натуральном виде (пальмовое, касторовое),
так и после специальной обработки — гидрогенизации, полимеризации, поликонденсации,
способствующей улучшению их смазочных свойств (гидрогенизированные масла: подсол-
нечное и кориандровое, полимеризованное хлопковое масло и др.).
При прокатке растительные масла подаются на металл и валки в чистом виде либо в
виде механической смеси с водой (дисперсии). Последнее осуществляется, например, на
жестепрокатных станах, где в качестве смазки часто используется пальмовое масло в смеси с водой в соотношении от 1:3 до 1:8. Как известно, натуральные масла не растворяются в воде и не образуют с ней устойчивых систем, не подверженных расслоению. Поэтому при использовании водо-масляных смесей установки для подачисмазки должны иметь емкость для интенсивного перемешиваниясреды (механического или сжатым воздухом).
В большинстве случаев растительные масла используются при прокатке без введения при-
садок. Иногда к более вязким маслам добавляют в небольших количествах моющие присадки. В настоящее время усилия исследователей направлены на то, чтобы изъять пищевые растительные жиры из сферы технологического потребления, заменив их синтетическими продуктами. Основными жирозаменителями, используемыми при прокатке, являются эфиры синтетических жирных кислот. Синтетические жирные кислоты (СЖК) получают жидкофазным окислением нефтяного парафина кислородомвоздуха в присутствии катализатора [7].
Для приготовления прокатных смазок в основном используют синтетические жирные кислоты фракций С17— С20 и С10 – С16.
Ряд синтетических технологических смазок: триэтиленгликолевый эфир СЖК фрак-
ции С17 — С20 (ЛЗ-142), бутиловый эфир СЖК той же фракции (ЛЗ-193), смазка СТП-1 (триэтиленгликолевый эфир СЖК с добавкой 20%-ного триэтиленгликолевого эфира олеиновой кислоты) и другие. Известны также синтетические смазки. Однако эти смазки, за исключением СТП-1, широкого применения при прокатке черных металлов пока не получили из-за их высокой температуры плавления, большой испаряемости, а при снижении температурыплавления — недостаточной смазочной способности.
В некоторых случаях для прокатки рекомендуются смеси минеральных масел с расти-
тельными или синтетическими продуктами в различных соотношениях (компаунды). Введение растительных масел или синтетических продуктов в минеральное масло преследует цель повышения эффективности смазки без значительного увеличения вязкости. Указанные добавки заметно изменяют физические и смазочные свойства основного компонента лишь тогда, когда они сравнительно велики (не менее 10%). В качестве примера можно назвать смазки, известные под марками ТПС-К10 и ТПС-К3О. Они представляют собой минеральное масло индустриальное 20 или 12 с добавкой, соответственно, 10 и 30% продуктаконденсации синтетических жирных кислот фракции С21 и выше с триэтаноламином.
В последние годы в нашей стране ведутся работы по созданию смазок на основе отхо-
дов производства растительных масел и органических кислот. Эти смазки выгодно отличаются от натуральных растительных масел не только меньшей стоимостью, но часто также и лучшими смазочными свойствами. К этой категории смазок относятся: смазка ОПСК, представляющая собой продуктпиролиза касторового масла, получаемый при производстве себациновой кислоты [8]; касторин — жирные кислоты и жиры, выделенные из касторового соапстока; смазка «Металлургическая» — полиэтирифицированные жирные кислоты, выделенные из отходов производства растительных масел, и другие.
Эмульсии
Эмульсией называется достаточно устойчивая система из двух жидких фаз, одна из
которых распределена в виде мельчайших капелек в другой. Ту жидкость, которая образует
капельки, называют дисперсной фазой. Остальная часть эмульсии — это дисперсионная (непрерывная) среда.
Эмульсии нашли широкое применение во всех процессах прокатки. Они выгодно отличаются от масел высокой охлаждающей способностью, возможностью длительного использования в циркуляционных системах, сравнительно низким расходом смазки, а иногда и лучшими антифрикционными свойствами.
Получение устойчивых эмульсий типа масло — вода возможно только при наличии в
растворе третьего компонента — эмульгатора. В качестве последнего часто применяются натриевые и калиевые мыла — соли жирных и нафтеновых кислот.
При попадании масла в воду, из-за большого поверхностного натяжения на границе
их раздела, вода не смачивает масло, и поэтому последнее сосредоточивается на поверхности воды в виде отдельной фазы. Если в воду ввести мыло, то оно растворяется, уменьшая поверхностное натяжение воды. Мыльный раствор смачивает гидрофобные частицы масла. В результате на поверхности капелек масла образуется коллоидно-адсорбционная пленка мыл с достаточно высокой вязкостью и прочностью. Таким образом, капельки масла оказываются изолированными одна от другой и при механическом перемешивании равномерно распределяются в воде, образуя стабильную эмульсию.