Порошковая металлургия
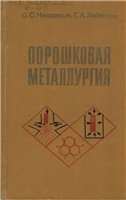
Кипарисов С.С., Либенсон Г.А.
Металлургия, 1980 г.
Вольфрам
Принципиальная технологическая схема производства спеченного вольфрама состоит из получения металлического порошка, прессования заготовок, спекания и обработки спеченной заготовки в изделия.
На заводах, производящих ковкий вольфрам, исходным сырьем для его получения служат чистая вольфра. мовая кислота или паравольфрамат аммония, которыеподвергают прокалке с получением WO3:
H2WO4 →WO3 + H2O
или
5(NH4)2O*12WQ*xH2O→ 12WO3 + 10NH3+(x+5)H2O.
Вольфрамовая кислота полностью теряет воду при 500° С; паравольфрамат аммония разлагается при температуре выше 250° С.
Для получения металлического вольфрама, помимо чистоты вольфрамового ангидрида, важную роль играет величина его частиц. Между температурой прокаливания вольфрамовой кислоты и насыпной плотностьюW03 существует определенная зависимость:
Температура прокаливания, °С . . . 550 600 700 800
Насыпная плотность, г/см3 .... 0,40 0,46 0,52 0,76
Вольфрамовую кислоту или паравольфрамат аммония прокаливают в электрических вращающихся или муфельных печах. Температура прокаливания составляет 600—800° С (в зависимости от требований, предъявляемых к зернистости порошка). Полученный вольфрамовый ангидрид далее поступает на восстановление причем для производства ковкого компактного вольфрама применяют исключительно водородное восстановление. Теория и практика процессоввосстановленияWO3водородом рассмотрена в разделе получения металлических порошков.
Полученный вольфрамовый порошок поступает на прессование, которое проводят обычно в разборных стальных прессформах на гидравлических прессах при давлении 200—500 МПа.
Кристаллы вольфрама отличаются малой пластичностью, поэтому в процессепрессования порошка они практически почти не изменяют своей основной формы и размеров и уплотнение порошка происходит главным образом в результате относительного перемещения частиц. Обычно пористостьштабиковвольфрама после прессования составляет 30—40%.
Для предотвращения расслоя к порошку перед прессованием добавляют какое-либо улетучивающееся при дальнейшем спекании склеивающее и смазывающее вещество, например раствор глицерина в спирте, раствор парафина в бензине и т. п. Эти растворы, выдавливаясь при прессовании на стенки прессформы и смазывая их, уменьшают трение частиц порошка о стенки прессформ и тем самым способствуют более равномерному уплотнению и распределению давления по объему брикета.
Вольфрамовые штабикипрессуют различных размеров; наиболее часто встречаются следующие: 9X9X400, 12X12X400, 15X15X400 мм. Спрессованные из вольфрамового порошка брикеты подвергают спеканию, которое осуществляют в две стадии.
Первая стадия — предварительное спекание при 1150—1300° С с выдержкой штабиков при этой температуре в атмосфереводорода в течение 30—120 мин. Для предварительного спекания используют печи с алундовой трубой или муфелем с молибденовыми нагревателями. штабики группами укладывают на тонкие молибденовые подкладки в никелевые лодочки, которые затем непрерывно проталкивают через печь при помощи механического толкателя.
Предварительное низкотемпературное спекание проводят с целью повышения прочности спрессованных брикетов, необходимой при последующем высокотемпературном спекании. Кроме того, при предварительном спеканииштабик имеет значительную пористость, что облегчает диффузиюводорода в брикет. Последнее обстоятельство приводит к довосстановлению окисных пленок, в результате чего улучшается металлический контакт между частицами и повышается электропроводность штабика, необходимая для второй стадии спекания (сварки).
Для достижения максимального уплотненияштабика и достаточного развития процесса роста зерен, обеспечивающего создание необходимой структуры, последнюю стадию спеканиявольфрама нужно проводить при температурах порядка 3000° С. Такую высокую техмпературу наиболее удобно создавать путем непосредственного пропускания электрического тока через спрессованный штабик, упрочненный предварительным спеканием. Эту стадию спекания — сварку — осуществляют в специальных печах, известных под названием сварочных аппаратов (см. рис. 158). Сварку штабиков, как и предварительное спекание, проводят в атмосфере водорода.
Режим спекания в производственных условиях контролируют обычно не - измерениемтемпературы штабика, а по величине тока. Для этого первоначально на нескольких образцах определяют ток, необходимый для переплавки штабика. Например, для штабиковразмером9x9x400 мм ток переплавки составляет 2400— 2500 А.
При спекании через штабикпропускают ток (примерно 90% от тока переплавки), который обеспечивает нагрев штабика до 3000—3100° С. Плотность сваренного штабика зависит от режима сварки, главным образом от максимальной температуры, от зернистости исходного порошка и отчасти от давления прессования. Выдержка в течение15 мин при силе тока 90% от тока переплавки оказывается достаточной для того, чтобы в основном были завершены процессыусадки и рекристаллизации и было достигнуто кажущееся равновесие, после которого дальнейшая выдержка при той же температуре только весьма медленно изменяет пористость и величину зерна штабика. Усадка при спекании достигает 15—18% по длине штабика и Плотность становится равной 17—18,5 г/см3, что соответствует остаточной пористости15—5%.
Многочисленными наблюдениями установлено, что штабик вольфрама, изготовленный из мелкозернистого порошка (размер частиц в среднем2 мкм), обладает более плотной и более грубозернистой структурой, чем штабик из крупнозернистого порошка (размер частиц в среднем4—5 мкм). Это обстоятельство указывает на то, что при сваркештабика из мелкозернистого порошка происходит более интенсивный рост зерен.
Практика показывает, что наилучшей обрабатываемостью при последующей горячей ковке обладают вольфрамовые сваренные штабики, характеризующиеся однородной структурой с числом зерен 2000—5000 на 1 мм2, т. е. со средней величиной зерен 22—14 мкм. штабики с числом зерен до 8—10 тыс. на 1 мм2 также удается проковывать, но при более высокой температуре.