Металлургия редких металлов.
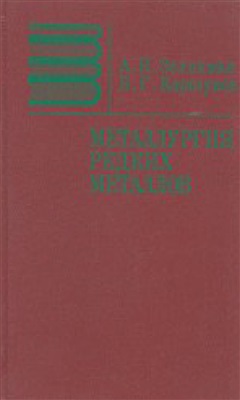
А.Н.Зеликман, Б.Г.Коршунов.
Металлургия, 1991 г.
6. ПЛАВКАМОЛИБДЕНА И ВОЛЬФРАМА
Для производства крупных заготовок (200 - 3000 кг), предназначенных для прокаталистов больших размеров, вытяжкитруб и производства изделийметодомлитья освоена ПЛАВКАМОЛИБДЕНА и вольфрама, а также сплавов на их основе в дуговых и электронно-лучевых печах.
Дуговая плавка
Во всех современных дуговых печах плавку ведут в вакууме с расходуемым молибденовым или вольфрамовым электродом и охлаждаемым медным тиглем — кристаллизатором (рис.20). Металл плавится в дуге, возникающей между верхним (расходуемым) электродом и нижним электродом — расплавленным металлом в медном кристаллизаторе. плавку ведут большей частью на постоянном токе при полярности: расходуемый электрод - катод, расплав - анод. Однако для воль-, фрама в случае плавки на переменном токе дуга вполне устойчива (в отличие от плавки менее тугоплавких металлов).
Наиболее распространены печи, в которых расходуемый электрод предварительно приготовляют из спеченных молибденовых или вольфрамовых штабиков. Стыковой сваркой шта-бики соединяют в электрод длиной 1 — 2,5 м. Затем их объединяют в пакет (4 - 16 штабиков и больше в зависимости от размеров кристаллизатора).
Перемещение расходуемого электрода при плавке и подвод к нему тока большей частью осуществляют с помощью штанги, на конце которой укреплен электрод.
7. ОБРАБОТКАВОЛЬФРАМА И МОЛИБДЕНА ДАВЛЕНИЕМ
После спекания вольфрамовые и молибденовые штабики на холоду хрупки. Однако в нагретом состоянии (1300 -1400 °С) штабики можно подвергать ковке, а затем волочению или прокатке в листы. С ростом степенидеформации пластические свойстваметаллов возрастают, а температураобработки понижается.
Ковку штабиков квадратного сечения в круглые прутки, предназначенные для волочения проволоки, осуществляют на ротационных ковочных машинах (рис.22). Принцип их действия состоит в том, что штабик, предварительно нагретый в печи (в водородной среде), получает большое число ударов (10000 - 12000 в 1 мин) от двух ковочных плашек, вращающихся с большой скоростью вокруг оси вольфрамового прутка и совершающих возвратно-поступательное движение по диаметру в пазах вращающегося вала машины. число ударов в 1 мин зависит от количества роликов и числа оборотов шпинделя. Изменяя диаметр плашек, получают прутки диаметром 2 - 3 мм, которые далее поступают на волочениепроволоки в нагретом состоянии сначала на крупных цепных и блочных волочильных станах с применением фильер из твердых сплавов (от 2 до 0,5 мм), затем на машинах многократного среднего и тончайшего волочения (от 0,5 до 0,01 мм). Для волочения вольфрамовой проволоки тоньше 0,3 мм применяют алмазные фильеры.
Температура волочения вольфрамовой проволоки изменяется по мере уменьшения диаметрапроволоки от 800 до 500 °С. В процессековки и волочения исходная равновесная структура заготовки превращается в "волокнистую", состоящую из мелких кристаллов, ориентированных вдоль оси обработки (рис.23). На всем протяжении обработкидавлением вольфрамовый пруток только один раз подвергается промежуточному отжигу выше температуры рекристаллизации. На всех последующих ступенях ковки и волочениятемпература нагрева ниже температуры рекристаллизации, так как в рекристаллизованном состояниивольфрам хрупок. Таким образом, без рекристаллизующих промежуточных отжиговвольфрам выдерживает громадную суммарную деформацию с удлинением (и соответственно с уменьшением сечения) до 100000 — 200000 раз, что без рекристаллизующих отжигов не допускает ни один металл.
Тонкая вольфрамовая проволока имеет высокую прочность - более 4 ГПа.
В отличие от ВОЛЬФРАМА рекристаллизующий отжиг обработанного МОЛИБДЕНА не приводит к повышению его хрупкости. Поэтому в процессахобработкиМОЛИБДЕНАдавлением применяют несколько рекристаллизующих отжигов. Большая пластичностьМОЛИБДЕНА позволяет проводить тонкое волочениепроволоки (а также прокатку тонкой ленты) без нагрева.
Аналогичные принципы обработки спеченных заготовок вольфрама и МОЛИБДЕНАдавлением с предварительным подогревом положены в основу плоской ковки, прокатки в листы и ленты.
Заготовки плавленых МОЛИБДЕНА и ВОЛЬФРАМА вследствие крупной зернистой структуры трудно поддаются деформации. Для измельчения зерна такие заготовки подвергают обработке экструзией с нагревом (прессование заготовки через матрицу). При этом методесхема напряженного состояния (благодаря всестороннему сжатию) более равномерна, чем при ковке. Молибденовые заготовки перед экструзией нагревают до 1400 - 1700 °С, вольфрамовые до 1600 - 1900 °С. Для защиты от окисления нагретые заготовки экструдируют в металлических оболочках. После экструзии металлы становятся более пластичными, что позволяет проводить их обра-i ботку с целью получения листов; проволоки и других изделий.
7. ОБРАБОТКАТАНТАЛА И НИОБИЯ ДАВЛЕНИЕМ
Ниобиевые и танталовые спеченные заготовки деформируют на холоду. Прутки проковывают на ротационных ковочных машинах, а плоские заготовки - на рессорном или пневматическом молоте до степениобжатия ~25%. Затем проводят высокотемпературный ре кристаллизующий отжиг в вакууме. Дальнейшую обработку ведут на холоду с промежуточными (если необходимо) отжигами в вакууме.
Начальную обработку крупнокристаллических слитков проводят, применяя горячую ковку или экструзию с предварительным нагревом их до 900-1000 °С (иногда в оболочке). С прокованных заготовок обтачивают тонкий наружный окисленный слой (если они нагревались без зашиты). Хорошие результаты дает первичная горячая ОБРАБОТКА в вакууме на специальных герметизированных станах. Дальнейшую обработкудавлением проводят на холоду.
Глава 3. ВАНАДИЙ 1. ОБЩИЕ СВЕДЕНИЯ
В 1830 г. шведский химик Зефстрем открыл в железной руде из г.Таберга (Швеция) новый элемент, которому из-за цветового многообразия соединений дал название "ванадий" по имени древнескандинавской богини красоты Ванадис.
В 1867 г. английский химик Роско выделил металлический ВАНАДИЙ (чистотой около 96 %) путем восстановления VC12 водородом. В дальнейшем многие исследователи безуспешно пытались получить более чистый ванадий. ВАНАДИЙ в силу трудности его очистки от кислорода, азота, углерода и водорода получался только в виде хрупких образцов. Лишь в 1927 г. Мардену и Ричу удалось получить первые образцы ковкогованадиявосстановлением V2O5 кальцием.
производство химических соединений
ТИТАНА
Титановые минералы, руды и рудные концентраты
В ряду распространенности элементов титан занимает девятое место, содержание его в земной коре 0,61 % (по массе). титан встречается во всех изверженных и осадочных породах, а также в почве, торфе, каменном угле, растениях, крови, костях животных.
Титан встречается в земной коре в виде диоксида, титанатов и сложных комплексных титанониобатов и силикотитанатов.
Известно около 70 минералов титана, наибольшее промышленное значение имеют рутил, ильменит, перовскит и сфен, являющиеся собственно титановыми минералами.
Рутил — природный диоксид титана (другие модификации — анатаз и брукит). Обычно содержит примесь оксида железа (II) FeO. Плотность 4,18-4,28 г/см3. Цвет большей частью красно-коричневый. Крупные месторождения редки. Известны месторождения в Австралии, Канаде, Бразилии. Рутиловые концентраты содержат 90-95% TiO2.
Ильменит - титанат железа FeOTio2 наиболее распространенный минерал титана. Впервые найден на Урале в Ильменских горах. минерал бурого или буро-черного цвета. Плотность 4,56-5,21 г/см3. При длительном выветривании ильменитпереходит в аризонит (Fe2O3 - 3ТiO2) и лейкоксен (TiO2-H2O). Это объясняет более высокое содержание TiO2 в некоторых ильменитах, чем это соответствует формуле FeOTiO2 (52,66%).
Часто ильменит находится в тесной связи с магнетитом. Такие руды называют титаномагнетитами.
Катализаторы. Рений и его соединения входят в состав катализаторов для ряда процессов в химической и нефтяной промышленности. Это наиболее масшатабная область применения рения. Наибольшее значение приобрели рений-содержащие катализаторы в крекинге нефти. Применение рениевых катализаторов позволило увеличить производительность установок, повысить выход легких фракций бензина, снизить затраты на катализаторы путем замены большей части платины рением.
Электроосветительная и электровакуумная техника. В ряде ответственных случаев, когда необходимо обеспечить долговечностьработы электропамп и электронных приборов (особенно в условиях динамической нагрузки), в этой области вместо ВОЛЬФРАМА применяют Рений или сплавырения с вольфрамом и молибденом. Преимущества рения и его сплавов перед вольфрамом состоят в лучших прочностныххарактеристиках и сохранении пластичности в рекристаллизованном состоянии, меньшей склонности к испарению в вакууме в присутствии следов влаги (сопротивление водородно-водяному циклу), более высоком электросопротивлении. Из рения и сплавовВОЛЬФРАМА с рением (до 30% Re) изготовляют нити накала, керныкатодов и подогревателей, сетки радиоламп. В электронных приборах используют также сплав Мо-50% Re, сочетающий высокую прочность с пластичностью.
Жаропрочные сплавы — одно из важных направлений использования рения. сплавырения с другими тугоплавкими металлами (вольфрамом, молибденом и танталом) наряду с жаропрочностью и тугоплавкостью отличаются пластичностю. Их используют в авиа- и космической технике (детали термоионных двигателей, носовые насадки ракет, части ракетных сопел, лопатки газовых турбин и др.).
Сплавы для термопар. Рений и его сплавы с вольфрамом и молибденом обладают высокой и стабильной термоэлектродвижущей силой (т.э.д.с). В СССР широко используют термопары из сплавов (W-5% Re) - (W- 20% Re). Т.э.д.с. этой термопары в пределах 0-2500 °С находится в линейной зависимости от температуры. При 2000 С т.э.д.с. равна 30 мВ. Преимущество термопары — сохранение пластичности после длительного нагревания при высокой температуре.
бласти применения галлия и индия
Галлий и индий имеют сходные области применения. Ниже приведены лишь наиболее существенные из них.
Полупроводниковая электроника. В этой области в настоящее время используют основное количество производных галлия и индия.
Галлий и индий высокой чистоты применяют для производства полупроводниковых соединений 1ипа А.1ПЪУ - антимонидов, арсенидов и фосфидов (GaSb, GaAs, GaP и аналогичных соединений индия). Эти соединения сохраняют полупроводниковые свойства при повышенных температурах. Их используют в приборостроении (датчики Холла), фотоэлементах для солнечных батарей, полупроводниковых тетродах, приемниках инфракрасного излучения, лазерах.
Кроме того, галлий и индий используют как акцепторную добавку для легирования германия, сообщая ему дырочную проводимость.
Сплавы. Таллий и индий образуют легкоплавкие сплавы с рядом металлов (Bi, Pb, Sn, Cd, Zn, In, Tl), которые используют в терморегуляторах, спринклерных устройствах (противопожарные сигнальные устройства), а также для замены ртути (в выпрямителях, прерывателях тока, гидравлических затворах).
Важное значение приобрели галлиевые припои для бесфлюсовой низкотемпературной пайки.
Паяные швы, выполненные при температуре 150-200 С с использованием никель-галлиевого (60-65 % Ni, 35-40 % Ga), медногаллиевого (62-65% Си, 35-38% Ga) или алюми-ниевогаллиевого (5-65% А1, 95-35% Ga) припоев, имеют < 30-50 МПа, могут работать при температурах 350-900 °с, выдерживать термоциклические, вибрационные и ударные нагрузки.
Сплавы In-Sn—Cd—Bi и In-Pb-Sn используют в качестве припоев для соединений металлов, стекла, кварца и керамики. В вакуумной технике припои из сплаваиндия с оловом (50 % In и 50 % Sn) служаг для соединения стекла со стеклом или с металлом. Они обеспечивают вакуумнуюПлотность соединений.
Индий обладает высоким сечением захвата тепловых нейтронов. В связи с этим в ядерной технике применяют регулирующие стержни из сплавов состава: 19% In, 71% Ag, 10% Cd и 54-62% In, 8-18% Cd, остальное - висмут.
Покрытия. Покрытияиндием для защиты подшипников в мощных двигателях внутреннего сгорания (например, в авиации или автостроении) от разъедания горячим смазочным маслом. Подшипники на основе кадмия (с добавками 2,35 % и 0,25 % Си) покрывают индием электролитическим способом. Затем производят диффузионный отжиг для получения неотслаиваемого покрытия.
Индиевые покрытия обладают высокой отражательной способностью и не тускнеют. Их используют для изготовления рефлекторов.
Перспективная область применения индия - покрытие оконных стекол пленкойоксида индия, обладающей теплозащитными свойствами.