Металлические порошки и порошковые материалы. Справочник
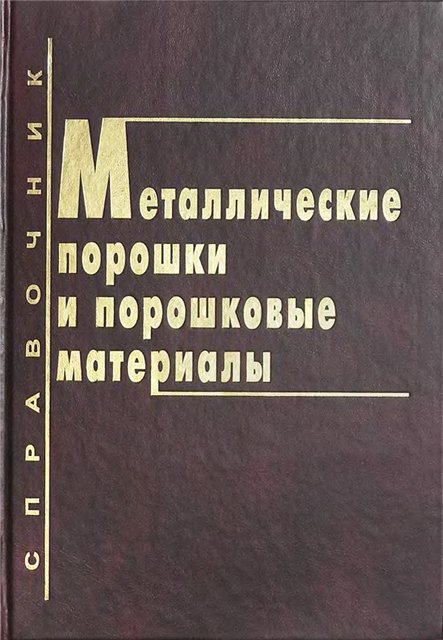
Бабич Б.Н. и др.
ЭКОМЕТ, 2005 г.
3.1.2. Железные порошки
Качество порошка железа регламентируется ГОСТ 9849-86 (с двумя изменениями). Этот ГОСТ распространяется на железный порошок, получаемый методамивосстановления и распылениярасплава водой высокого давления или сжатым воздухом.
Порошок подразделяют по:
способу изготовления - на восстановленный (В), распыленный (Р);
химическому составу - на марки ПЖВ1, ПЖВ2, ПЖВЗ, ПЖВ4, ПЖВ5, ПЖР1, ПЖРЗ и ПЖР5;
наспыпной плотности - на 22; 24; 26; 28; 30.
В условном обозначении порошка указывают: П — порошок, Ж — железо; В, Р — способ изготовления; марку по химическому составу - 1; 2; 3; 4; 5; гранулометрический состав-450; 315; 200; 160; 71; насыпную плотность - 22; 24; 26; 28; 30.
Примеры условного обозначения:
порошок железный восстановленный, марки ПЖВ1, по гранулометрическому составу 450, с насыпной массой 26:
ПЖВ 1.450.26 ГОСТ 9849-86;
порошок железный распыленный, марки ПЖР2, по гранулометрическому составу 200, с насыпной массой 26:
ПЖР2.200.26 ГОСТ 9849-86.
Химический состав порошков указан в табл. 3.2, а гранулометрический - в табл. 3.3.
3.1.3. Легированные порошки на основе железа
В настоящее время в мировой практике освоен и широко используется выпуск двух основных видов легированных порошков конструкционных сталей: гомогенно-и частично-легированных (диффузионно-легированных) порошков, спрос на которые постоянно растет.
Гомогенно-легированные (Diffusionalloyed powders) порошки, получаемые распылением, применяют в основном, для изготовления тяжелонагруженных деталей методом горячей переработки из-за их низкой уплотняемости и прочности сырых прессовок.
Частично-легированные (Prealloyed powder) порошки предназначены для изготовления конструкционных среднегруженных деталей традиционным и наиболее широко используемым методом порошковой металлургии: прессованием формовок необходимой конфигурации с последующим спеканием. В качестве основы для получения частично-легированных порошков используют восстановленные или распыленные железные порошки.
Метод частичного легирования состоит в припекании дисперсных частиц легирующих добавок к поверхности частиц железного порошка в процессе диффузионно-восстановленного отжига их механической смеси. Например, никель и медь добавляют к железному порошку основы в виде тонкого порошка сплава Ni-Cu, а молибден -в виде порошка молибдена, что обусловлено как обеспечением потребительских свойств спеченных изделий, так и экономическими факторами.
Достаточно широко используется метод «псевдолегирования» (дисперсного упрочнения), позволяющий избежать недостатков как метода механического смешивания, так и получения гомогенно-легированных порошков. Суть предложенной технологии состоит в размолесмеси железного и легирующего порошков (преимущественно оксидов А12О3, TiO2, карбонитридов Ti (С, N)) в течение времени, достаточного для внедрения легирующих частиц в мягкие частицы железа, и последующем отжиге полученного продукта.
В Российской Федерации такие порошки производят уже упомянутые крупные заводы-производители железных порошков - СМЗ и «Северсталь», а также ряд специализированных научно-производственных предприятий - ООО «Полема», Тулачермет, ЦНИИчермет.
Порошки коррозионностойких сталей и сплавов
Совместное восстановление смесей оксидовметаллов и металлических порошков гидридомкальция применяется для изготовления порошков нержавеющих сталей ау-стенитного и ферритного классов: Х18Н15, Х23Н18, Х18Н12М2Т, Х23Н28, Х23Н28МЗДЗТ, ХЗО, Х17Н2, порошков жаростойких сплавовсистемы Ni-Cr: Х20Н80, Х40Н60, систем: Fe-Cr-Al-Y, Ni-Al, Ni-Cr-Al и др. порошки хромистых, хромоникелевых сталей и нихрома имеют преимущественно неправильную (несферическую) форму частиц, состоящих из зерен размером 20-30 мкм. Насыпная плотность порошков нержавеющей стали Х18Н15 в зависимости от фракций (от мелкой к крупной) колеблется от 2,35 до 1,75 г/см3, относительная плотность брикетов при давлении 700 МПа достигает 75 %. порошки хорошо формуются при гидростатическом прессовании. Благодаря хорошей прессуемости восстановленные порошки легированных сталей, нихрома находят широкое применение в производстве проницаемых изделий из пористой прокатанной и спеченной ленты - фильтров.
Порошки коррозионностойких сталей и сплавов широко применяются в производстве фильтров для очистки смазочных масел, топлива, щелочей, воздуха и других газов и технических жидкостей, а также для изготовления пламягасителей, пористых охладителей.
Порошки нержавеющих хромоникелевых сталей
Состав и свойства распыленных порошков нержавеющих хромоникелевых сталей регламентируется ГОСТ 14086-68 «Порошки распыленные из нержавеющих хромоникелевых сталей и никеля». Он распространяется на порошки, полученные из сталей марок 0Х18Н10, Х18Н9 и никеля марок HI, H2 и НЗ распылениемвоздухом или инертным газом.
В обозначении марки буквы символизируют: П - порошок, Р - распыленный, X -хром, Н - никель. Цифры, стоящие после букв, указывают примерное содержание легирующего элемента в целых единицах.
Пример обозначения порошка из хромоникелевой стали марки ПР0Х18Н10, фракции 0,3 группы А: порошок ПР0Х18Н10-0,3-А (ГОСТ 14086-68).
Химический состав порошков указан в табл. 3.17.
Распыленные порошки поставляются в невосстановленном виде. По согласованию сторон они могут быть восстановлены.
В зависимости от гранулометрического составапорошки изготавливают семи фракций, которые определяются ситовым составом. Каждую фракцию порошка по насыпной массе поставляют двух групп: А и Б. Размеры фракций, ситовойсостав и насыпная масса указаны в табл. 3.18.
Относительная влажность порошков не должна превышать 0,2 %. Качество порошка гарантируется в течение 6 мес со времени отгрузки порошка.
Классификация способов получения порошков цветных металлов
дыми, газообразными реагентами из твердых или жидких металлосодержащих материалов, электролизрастворов и расплавов).
Классификация способов получения порошков приведена на рис. 3.1.
Наибольшее значение в промышленной практике имеют способы восстановления, распыления расплава, электролиз, карбонильный, автоклавный.
Механическое измельчение (резание, истирание, дробление) применяют для получения порошков из металлов и сплавов, обладающих повышенной хрупкостью (висмут, кремний, сурьма, марганец). Получаемые частицы порошка имеют осколочную, чешуйчатую, лепестковую формы.
При получении пирофорных порошков исходный материал измельчают в жидкой среде (бензол, спирт и др.), в среде инертных газов, в присутствии ингибиторов. Для измельчения используют шаровые, планетарные, вихревые и вибромельницы, аттриторы.
Способы механического измельчения просты технологически и аппаратурно, дешевы, эффективны для обработки отходов производства. Однако этими способами получают ограниченную номенклатуру порошков, существует опасность их загрязнения измельчающей средой, наклепа. Иногда для снятия наклепапорошки подвергают обжигу в защитной среде.
Получение порошков распылением расплава
Известны следующие способы диспергации расплава: потоком воды, на вращающейся тарелке, с использованием плазмы, в форсунке специальной конструкции с использованием внешнего энергоносителя (воздух, инертный газ, вода) под большим давлением; последний способ имеет наибольшее промышленное значение.
Способом распыления удобно получать порошки легкоплавких металлов и сплавов (Тт < 1800 К). Форма частиц порошков - сферическая или каплевидная.
3.2.3. Алюминиевые порошки и пудры Общие сведения
Порошки и пудрыалюминия и его сплавов - наиболее представительные по объему производства и номенклатуре среди порошков цветных металлов. Их отличительной чертой является повышенная пожаро- и взрывоопасность. Получают из сортовых марок алюминия и его сплавов или из их отходов, используя приемы диспергации (пульверизации) расплава. Как следствие, состав порошков и пудр во многом идентичен составу исходного сырья.
Порошки различаются гранулометрическим составом, удельной поверхностью, насыпной плотностью. Как правило, это продукт серого или серовато-серебристого цвета; содержание в нем примесей, видимых невооруженным глазом, или комочков, не рассыпающихся от легкого прикосновения (надавливания), не допускается.
Пудры представляют собой мажущийся порошок серого или серебристо-серого цвета.
Алюминиевые пудры применяют для производства пигментов, красок, эмалей, лаков, шпатлевок, газобетона.
В этом разделе рассмотрены общие требования по упаковке, отбору проб, маркировке, перевозке и хранению порошков и пудр алюминия, а также правила техники безопасности и противопожарные мероприятия. При описании конкретных типов порошков и пудралюминия будут указаны только их особенности.
5.2.5. Вольфрамовые порошки
Вольфрам металлический в виде порошка (ТУ 48-19-101-84 с изменениями 1-3)
Вольфрамовый порошок марок ПВЗК, ПВ-0 и ПВ-1 получают водороднымвосстановлениемоксидов вольфрама. Химический состав марок вольфрамовых порошков приведен в табл. 3.31.
Порошок не должен содержать посторонних включений и крупных конгломератов.
Дисперсность порошка, определяемая по поглощению паров метанола, составляет, мг/г:
0,02-0,07 - для изготовления твердых сплавов;
0,04-0,07 - для изготовления изделий разного назначения. Назначение порошка и его дисперсность оговариваются в наряде-заказе.
Насыпная плотность порошка составляет 2,0—5,5 г/см-*.Порошок упаковывают в банки из белой жести или (по согласованию с потребителем) в запаянные двойные полиэтиленовые мешки; масса порошка в банке или мешке не должна превышать 25 кг. Две банки или два мешка упаковывают в деревянные ящики; свободное пространство заполняют ватой или ставят деревянные прокладки. Допускается упаковка в картонные барабаны: в этом случае 40 кг порошка засыпают в одинарный полиэтиленовый мешок, его герметизируют. В тару вкладывают упаковочный лист, сертификат (в первый ящик или барабан) установленного образца.
Вольфрамовый порошок поставляют партиями массой не менее 700-1500 кг.
Порошок транспортируют авиационным, автомобильным, железнодорожным транспортом в соответствии с отраслевыми правилами.
Порошок хранят в упаковке в сухом отапливаемом помещении в условиях, исключающих механическое повреждение тары и попадание на вольфрам влаги и активных химических веществ. Гарантийный срок хранения 6 мес с момента приема ОТК завода.
Вольфрамовый порошок по токсичности относится к 4 классу опасности по ГОСТ 12.1.005. Пыль его вызывает раздражение глаз, кожи, верхних и глубоких дыхательных путей, бронхиальную астму, нарушение со стороны желудочно-кишечного тракта. ПДК аэрозоливольфрама в рабочей зоне 6 мг/м^, в воде водоема 0,05 мг/дм3.
Вольфрамовый порошок пожаро-взрывобезопасен, не образует токсических соединений в воздушной среде и сточных водах.
Вольфрамовый порошок применяют для изготовления отдельных марок твердых сплавов, специальных изделий порошковой металлургии.
Порошок медный электролитический общего назначения (ПМО ТУ 48-0318-057-89)
Порошок используют для производства товаров народного потребления.
Массовая доля меди в медном порошке должна быть не менее 99,5 %. Порошок должен проходить через сито с сеткой 01К в количестве не более 30 %; Форма частиц порошка - дендритная.
Насыпная плотность порошка 2,0-4,0 г/см3. Допускается наличие посторонних металлических включений и окисленных частиц порошка.
Порошок упаковывают в стальные барабаны типа II, исполнение В|, широкогорлые по ГОСТ 5044-79 с внутренним полиэтиленовым мешком по ГОСТ 17811-78 или в мягкие резинокордные контейнеры по ТУ 6-52-04-89 с внутренним полиэтиленовым вкладышем. Порошок поставляют партиями не более 2000 кг. Гарантийный срок 6 мес с момента изготовления.
Порошок медный электролитический для предприятий химической промышленности (ТУ 48-0318-067-91)
Порошки марок ПМС-Х, ПМ-Х и их смесь используют для производства оксидов меди (I) и (II), солей на основе меди.
Порошок должен на 99,5 % проходить через сито с сеткой 01К по ГОСТ 6613-86, с сеткой 0045К - на 73-85 %. Порошок не должен иметь посторонних включений; насыпная плотность его 1,25-2,0 г/см3.
Порошок поставляют партиями не более 1000 кг. Гарантийный срок хранения порошка марки ПМС-Х составляет 6 мес, марки ПМ-Х - 2 мес, смеси ПМС-Х/ПМ-Х -4 мес с момента изготовления.
Порошок медный электролитический
для предприятий лакокрасочной промышленности (ТУ 48-0318-070-93)
3.2.12. Молибденовые порошки
Молибденовый порошок высокой чистоты (МПЧ) (ТУ 48-19-69-80 с изменениями 1-6).
Химический состав порошка, %: не менее 99,67 Мо, не более по 0,0001 Sn, Pb, Cd, Bi, по 0,001 Al, Mg, As, Cu, Zn, 0,003 Si, no 0,004 S и P, no 0,005 Fe, Ni, Ca, 0,009 C, 0,01 Na, 0,08 K, 0,2 W, 0,25 O.
Порошок имеет серый цвет, не содержит посторонних включений; содержание фракции -5 мкм до 92 %. Порошок отгружают партиями массой не менее 200 кг каждая.
Порошок упаковывают в банки из белой жести с пропаянными швами и закатанной крышкой; масса порошка в банке не более 20 кг. Банки помещают в деревянные ящики (масса нетто не более 40 кг), а в первый ящик партии — сертификат качества. Допускается упаковка порошка в двойные полиэтиленовые мешки массой не более 25 кг, помещаемые в возвратный контейнер.
Ящики с банками порошка транспортируют любым видом закрытого транспорта, исключая их перемещение и попадание влаги. Порошок хранят в таре, в сухом закрытом помещении, не содержащем аэрозолей кислот и щелочей.
Гарантийный срок хранения 6 мес с момента приемки продукции ОТК завода-изготовителя.
Молибденовый порошок (МПУ) используют для производства специальных сплавов.
3.2.24. Циркониевые порошки
Циркониевый порошок электролитический (ТУ 95259-99ЛУ)
Порошок получают методом электролиза; в зависимости от условий получения устанавливаются следующие марки порошка: ПЦЭ-ЗР, ПЦЭ-ЗРо.ч., ПЦЭ-ЗРБМ, ПЦ-ОР, ПЦЭ-ОРо.ч., в которых буквы означают: ЗР или ОР - режим работыэлектролизера — соответственно «закрытый» или «открытый»;
БМ — для производства биметаллических изделий;
о.ч. — особо чистый по гафнию.
Порошок имеет серовато-серебристый цвет с металлическим блеском, не содержит посторонних включений, видимых невооруженным глазом, допускается наличие темных углеродсодержащих включений, обусловленных технологией производства. Химический состав приведен в табл. 3.105.
Порошок упаковывают во фляги, изготовленные из нержавеющей стали, вполиэти-леновые мешки и далее - в алюминиевые или оцинкованные фляги. масса нетто одной упаковочной единицы не должна превышать 100 кг.
Порошок транспортируют в упакованном виде всеми видами крытого транспорта в соответствии с правилами перевозок, действующими на данном виде транспорта.
Часть II. Металлические порошковые материалы
Раздел 4. ПОРОШКОВЫЕ МАТЕРИАЛЫ
4.1. Твердые сплавы Введение
В 1926 г. впервые на рынке появились режущие пластины из твердого сплава Ви-диа N (Widia N, фирма «Видиа-Крупп», Германия).
К. Шротеру (Schroter) был выдан 30.03.1923 г. патент DRP 420.689. Действие этого патента, который рассматривается сегодня как основной патент по твердым сплавам, было продлено до 30.12.1925 г. Позднее Ф. Скаупу (F. Skaupy) был признан автором изобретения по использованию металлов группы железа, таких как железо, никель или кобальт, для твердого сплава.
Первые твердые сплавы в нашей стране были получены в 1929 г. под руководством Г.А. Меерсона и Л.П. Малькова на Электроламповом заводе (Москва). Изделия из твердого сплава под маркой «Победит» содержали 10 % Со.
В 2000 г., по данным Г. Гилле (ФРГ), в мире, исключая Китай, было произведено около 30000 т твердых сплавов. Потребность в новых разработках видна на примере производства тонкодисперсных твердых сплавов: в 2000 г. было произведено от 11500 до 12500 т субмикронных твердых сплавов, что составляет 40 % от общего объемавыпуска твердых сплавов. Реальный прогресс в расширении выпуска тонкодисперсных сплавов виден на примере роста производства микросверл: 140 т в 1985 г. из субмикронных сплавов с величиной зерна карбидавольфрама 1,2 мкм и 570 т в 2000 г. из ультрадисперсных сплавов с величиной зерна карбидавольфрама 0,4 мкм.
Около 67 % от всего количества твердых сплавов используется в мире в режущем инструменте. Следующая большая область применения твердых сплавов - это горнобуровая индустрия, бурение на нефть и газ, проход туннелей, плоское резание дорожного полотна, камнеобработка (13 %), деревообработка (11 %), бесстружковая обработкаметаллов и конструкционные детали (9 %). Динамика развития производства твердых сплавов может быть проиллюстрирована следующим фактом: в период 1979-1991 гг., т.е. за 12 лет, спрос в мире на режущий инструмент удвоился.
Таким образом, область порошковой металлургии — спеченные твердые сплавы -динамически развивается, и потребность промышленности в таких материалах постоянно растет.
4.1.2.11. сплавы для обработкиметалловдавлениемКлассификация сплавов
Твердосплавный инструмент при различных видах обработкиметалловдавлением (прокатке, объемной штамповке, высадке, волочении, вырубке) обеспечивает повышение производительности и качества изготовляемых деталей. Наиболее широко для оснащения инструмента при обработкеметалловдавлением применяют вольфрамокобальтовые твердые сплавы, обладающие рядом преимуществ: повышенным сопротивлениемразрушению в сочетании с высокими прочностью и износостойкостью.
В зависимости от напряженного состояния, возникающего в процессе нагружения, твердые сплавы можно классифицировать по трем группам: двум основным и третьей - дополнительной. сплавы первой основной группы, предназначенные для оснащения инструмента, при эксплуатации которого преобладает износ, характеризуются повышенным сопротивлением изнашиванию и умеренным сопротивлением разрушению. сплавы второй основной группы, используемые для изготовления инструмента, воспринимающего при обработкеметалловдавлением в основном динамические нагрузки, обладают повышенным сопротивлениемразрушению и умеренной износостойкостью. сплавы этой группы имеют и более высокое сопротивление локальному разрушению Kic (табл. 4.69). К третьей группе отнесены сплавы, применяемые в специальных условиях, например для изготовления деталей, работающих в агрессивных коррозионно-активных средах, или формообразующего инструмента, работающего при повышенных температурах. В каждой группе с увеличением содержания кобальта в сплавеизносостойкость уменьшается, а сопротивление как разрушению, так и распространению трещины, увеличивается. Интенсивность изменения свойств наглядно показана в табл. 4.1.
4.3. Пористые проницаемые материалы 4.3.1. свойства материалов
Важным направлением порошковой металлургии, представляющим специфическую ее часть, является создание пористых проницаемых материалов, работоспособность и области применения которых определяются наличием взаимосвязанной системы пор. Эта система обеспечивает им такие свойства, как проницаемость для газов и жидкостей, способность задерживать инородные включения, транспортировать жидкость по капиллярам и удерживать ее в порах, способность поглощать энергию одиночных ударов и вибрации в широком диапазоне частот, рассеивать открытое пламя и др.
По сравнению с аналогичными войлочными, бумажными, тканевыми материалами порошковые материалы, изготовленные из металлов, сплавов, металлоподобных соединений и оксидов, характеризуются большей проницаемостью, устойчивостью к тепловым ударам, возможностью полностью или частично восстанавливать фильтровальные свойства, и самое главное, возможностью управлять их свойствами в широких пределах.
Свойства пористых проницаемых материалов разделяют на две большие группы: структурные и каркасные, причем в каждой из этих групп выделяется основная подгруппа (собственно структурные и каркасные свойства), а также несколько подгрупп свойств, зависящих соответственно от структурных и каркасных.
Структурные свойства включают в себя пористость (и ее распределение), размер пор (и их распределение), форму пор и степень их извилистости. К структурно-зависимым свойствам относятся свойствапроницаемости (собственно проницаемость и распределение локальной проницаемости), фильтрующие свойства (тонкость очистки и грязеемкость) и капиллярные свойства (капиллярное давление и капиллярный потенциал).
К каркаснымсвойствам относятся плотность (и ее распределение) и характеристики межчастичных контактов. От каркасныхсвойств зависят свойства проводимости (электро- и теплопроводность), механические свойства (предел прочности, предел текучести, предел упругости, относительное удлинение) и свойства, определяющие коррозионную стойкость материала.