Материаловедение и технология металлов
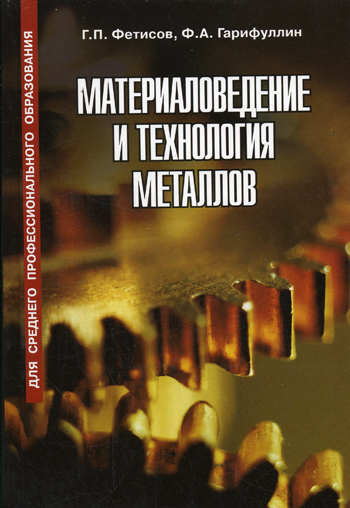
Г.П. Фетисов и др.
Высшая школа , 2001 г.
6.1. Жаростойкость и методы ее повышения
Жаростойкость — способностьметаллов и сплавов сопротивляться окислению и газовой коррозии при высоких температурах. Жаростойкость зависит от многих внешних и внутренних факторов. В основном за жаростойкость отвечают поверхностьметалла и чистота ее обработки. Полированные поверхности окисляются медленнее, так как оксиды распределены равномерно и более прочно сцеплены с поверхностью металла. Формирующаяся на поверхностиоксиднаяпленка достаточно хорошо защищает металл от дальнейшего окисления в том случае, если она плотная и не пропускает ионы кислорода, хорошо сцеплена с подложкой и не отслаивается при механических испытаниях. К металлам, которые образуют такие пленки, относятся хром и алюминий. Оксидныепленки типа шпинели Сг203 и А1203 хорошо защищают от окисления при высоких температурах. Если на поверхности образуется рыхлый оксид, как у магния, то он не стоек и не защищает металл от дальнейшего окисления.
Повышение жаростойкостисплавов достигается легированием элементами (хром, алюминий, кремний), образующими на поверхности непроницаемые для ионов основного металла и кислородаОксидные пленки. Также для этих целей используются защитные покрытия, состав которых выбирается с учетом условийработыизделия и состава агрессивной среды. Структура жаростойкого материала должна быть однородной и однофазной (чистые металлы, твердые растворы).
Термическая обработка меняет строение сплавов и, следовательно, их коррозионную стойкость. Отжиг и нормализацияприводят к формированию однофазной структуры и способствуют увеличению жаростойкости материала.
Пластическая деформация ухудшает жаростойкость, так как приводит к появлению градиента напряжений в структуре металла. Величина зерна для жаростойкого материала не существенна, поэтому эта характеристика является структурно нечувствительной.
Характеристики сплавов, стойких к коррозии при повышенных температурах, могут быть даны лишь к конкретным агрессивным средам и выбор материала решается с учетом условийработы данного изделия.
6.2. Жаропрочность и методы ее повышения. Явление ползучести
Жаропрочностью называют способностьматериала длительное время сопротивляться деформированию и разрушению при повышенных температурах. Жаропрочность важна при выборе материала, когда рабочие температурыизделий выше 0,3 Тт. Многие детали современных паросиловых установок, металлургических печей, двигателей внутреннего сгорания, газовых турбин и других машин разогреваются до высоких температур и несут большие нагрузки. Условияработы деталей различны: основное значение при выборе материала имеют температура, длительность работы под нагрузкой и значение напряжения.
При высоких температурах ускоряются диффузионные процессы, изменяются исходная микроструктура и механические свойства материалов. С повышением температуры значительно возрастает число вакансий, увеличивается подвижность точечных дефектов. Кроме того, диффузия способствует перемещению дислокаций (линейный дефект) путем переползания, что дает им большую «степень свободы», но также наблюдаются частичная аннигиляциядислокаций (дислокации разного знака взаимно уничтожаются), перераспределение их, что коренным образом меняет первоначальную дислокационную структуру металла.
Длительное время воздействия температурыприводит к существенным структурным изменениям: теряется прочность, полученная при термической обработке (закалка, старение), а также происходит потеря упрочнения, вызванного пластической деформацией, из-за таких процессов, как возврат и рекристаллизация.
Как уже было сказано, при высоких температурах ослабевают межатомные связи у металлов, уменьшаются модуль упругости, временное сопротивление и предел текучести.
деформации и скоростиползучести от времени" width="159" height="170" />
Чем ниже температураплавления сплава, тем ниже и рабочая температура. При нагружении материала длительное время в условиях повышенных температур наблюдаются процессы ползучести.
Если при постоянной температуре нагрузить металл постоянно действующим напряжением даже ниже пределатекучести и оставить его в этих условиях длительное время, то металл со временем будет деформироваться с определенной скоростью. Это явление получило название ползучести или крипа.
Такие понятия, как ползучесть и жаропрочность, тесно связаны между собой и отделить их друг от друга не представляется возможным.
§ 8.4. Тугоплавкие металлы и сплавы на их основе
К тугоплавким металлам относятся металлы с температуройплавления более 1800 °С. Наибольшее распространение в промышленности получили элементы VA-группы — ниобий и тантал, элементы VIA-группы — хром, молибден и вольфрам и элемент VIIA-группы — рений. Последний является весьма редким элементом, отличается значительной стоимостью и применяется в основном для легирования. Уникальные физико-механические свойства этих металлов (табл. 8.11), прежде всего высокие температурыплавления и Жаропрочностьсплавов тугоплавких металлов, позволяют использовать их для изготовления деталей и узлов, работающих в сложных экстремальных условиях: авиационной, ракетно-космической, атомной технике, приборостроении, радиоэлектронике. изделия из тугоплавких металлов и сплавов на их основе работают при температурах больше 1000—1500 °С как в кратковременном режиме, так и в условиях относительно длительной эксплуатации.
Однако Тугоплавкие металлы имеют и недостатки. Прежде всего они склонны к хрупкому разрушению, так как им присуща высокая температура хладноломкости. Примеси внедрения, такие, как С, N, Н, О, еще более повышают ее. В табл. 8.12 приведены данные по влиянию примесей внедрения на температуруперехода к хрупкому состоянию для тугоплавких металлов. Как видно, содержание примесей определяется способом получения металла. Наиболее чистые металлы, получаемые зонной очисткой, имеют порогхрупкости в области минусовых температур и хорошую пластичность при комнатной температуре. Так, если для металлокерамического молибденатемператураперехода в хрупкое состояние состояние +200 °С, то для молибдена, полученного зонной плавкой в вакууме, порогхрупкости -196 °С. Еще более значительная разница, как видно из табл. 8.12, наблюдается для вольфрама: +500 °С — порогхрупкости для металлокерамического вольфрама и -196 °С — для вольфрама зонной плавки с содержанием углерода менее 0,001%.
7.1. Влияние легирующих элементов и примесей на дислокационную структуру и свойства стали
Легированными называют стали, в которые для получения требуемых свойств специально вводят легирующие элементы. При наличии элементов в количестве примерно 0,1% такое легирование называют микролегированием.
Легирующие элементы оказывают влияние на электронную и дислокационную структуру металла. Замещая атомы в решетке основы, они создают барьеры ближнего действия на пути движущихся дислокаций. От легирования зависят характер и величина межатомного взаимодействия в сплаве, что влияет на подвижность дислокаций. Так, при легировании может увеличиваться плотность дислокаций, вызванная изменением энергиидефектов упаковки (см. § 1.5.3), меняется время релаксациивакансий и, как следствие, их избыточная концентрация. Значения константдиффузии и упругости, Условия протекания фазовых превращений и в конечном итоге прочность твердого раствора, безусловно, связаны с легированием. Часто легирование сопровождается повышением сопротивления твердого раствора пластической деформации, поскольку при его образовании более вероятным является множественное скольжениедислокаций по нескольким плоскостям вместо единичного. Так, легирование железа марганцем способствует образованию мартенситнойструктуры марганцевого феррита, повышению плотностидислокаций и, как следствие, значительному возрастанию прочности твердого раствора (рис. 7.1). Но есть и исключения: например, легирование железа хромом в определенных пределах уменьшает прочность твердого раствора. При встрече перемещающихся дислокаций с примесными атомами поля упругих напряжений вокруг них взаимодействуют между собой, что приводит к перераспределению примесей. Энергия взаимодействия Примеси с дислокацией составляет 1—0,01 эВ. Примесные атомы замещения с меньшим, чем у основы, атомным радиусом замещают атомы основы в сжатой области поля дислокации; в противоположном случае — в растянутой области. Примеси внедрения заполняют растянутые участки вокруг дислокаций. Концентрируясь у ядра дислокаций, примесные атомы внедрения образуют облака Коттрелла. Эффектупрочнения при легировании железа элементами внедрения (азот, углерод) значительно сильнее, чем элементами замещения (например, никель, марганец). Так, добавление в железо каждой очередной сотой доли процента углерода или азота (0,01%) повышает пределтекучестисплава на 40—50 МПа, в то время как введение аналогичного количества никеля — всего на 0,3 МПа, т. е. Эффектупрочнения в последнем случае на два порядка меньше.
Легирующие элементы по-разному влияют на энергию взаимодействия примесей внедрения с дислокациями. Так, введение в решетку а-железа 3% никеляприводит к снижению энергиисвязиуглерода с дислокациями с 0,5 до 0,2 эВ; легирование же железа кремнием вызывает противоположный эффект. Неравномерное распределение ионов вокруг дислокации проявляется также и в неравномерном распределении электронов: уплотненные участки решетки вокруг дислокации приобретают положительный заряд вследствие недостатка электронов; в то же время области растяжения в связи с избытком электронов заряжаются отрицательно. Между положительным зарядом примесного иона и отрицательно заряженной областью дислокации возникают кулоновские силы притяжения, приводящие к перераспределению примесей. Энергия электрического (кулоновского) взаимодействия в металлах невелика (для двухвалентных примесей она составляет -0,02 эВ). Электрическое взаимодействие значительно слабее упругого, но вклад первого может стать существенным в случае отсутствия в твердом растворе упругого взаимодействия (т. е. при равенстве радиусов основного и примесного атомов), а также при их большой разнице в валентностях.
В металлах с ГЦК решеткой имеет место химическое взаимодействие дислокаций с примесями с образованием атмосфер Сузуки. Это взаимодействие обусловлено тем, что при возникновении дефектов упаковки с гексагональной решеткойрастворимость в них примесного атома может быть больше, а Энергия меньше, чем в бездефектной зоне (в объеме основного металла). Легирующие элементы в сталях обычно снижают энергиюдефекта упаковки и тем самым увеличивают его ширину. В свою очередь, чем больше ширинадефекта упаковки, тем труднее реализуется процесс преодоления винтовыми дислокациями барьеров посредством их поперечного скольжения. Этот процесс может реализоваться при деформационном упрочнении. Энергиядефектов упаковки существенно влияет на механические свойства легированного аустенита в широком диапазоне температур. Одними из основных аустени-тообразующих элементов в стали являются никель и марганец. Исследования показали, что марганцевый аустенит (стабильный) значительно сильнее подвержен деформационному упрочнению (в -1,7 раза при степенидеформации 50%), чем никелевый (рис. 7.2). хром повышает Жаростойкость и коррозионную стойкость стали, увеличивает ее электрическое сопротивление и уменьшает коэффициент линейного расширения. легированиесталихромомприводит к уменьшению склонности аустенитного зерна к росту при нагреве, существенному увеличению ее прокаливаемости, а также к замедлению процессараспада мартенсита.
Кремний широко используется при выплавке стали как раскислитель. легированиекремнием углеродистых и хромистых сталей увеличивает их жаростойкость. Например, сталь с 5% Сг и 1% Si в среде печных газов равнозначна по жаростойкостистали с 12% Сг. Уменьшая подвижность углерода в феррите, кремний тем самым затрудняет формирование и рост цементитных частиц, что проявляется в повышении устойчивостиструктурыстали при отпуске. Содержание кремния в стали ограничивают, поскольку он повышает склонность стали к тепловой хрупкости.
Марганец, подобно никелю, снижает критическую скорость охлаждения, но в отличие от последнего уменьшает и вязкость феррита. Марганец используется для частичной замены никеля с целью получения нужного сочетания механических свойств стали, а также с учетом меньшей стоимости марганца.
Вольфрам, молибден, ванадий, титан, бор и другие вводят в сталь совместно с хромом, никелем и марганцем для дополнительного улучшения ее свойств.
Молибден и вольфрам повышают прокаливаемостьстали (особенно в присутствии никеля), способствуют измельчению зерна и подавлению отпускной хрупкости. легированиесталимолибденомприводит к значительному улучшению ее механических свойств после цементации и нитроцементации.
При введении в сталь ванадия, титана, ниобия и циркония образуются труднорастворимые в аустените карбиды. Эффективность воздействия этих элементов (измельчение зерна, снижение порога хладноломкости, уменьшение чувствительностистали к концентраторам напряжений) проявляется лишь при их малом содержании в стали (до 0,15%); при большем количестве они вызывают снижение прокаливаемости и сопротивлениястали хрупкому разрушению, что обусловлено выделением по границам зерен значительного количества карбидов типа МеС (VC, TiC и др.).