Титан
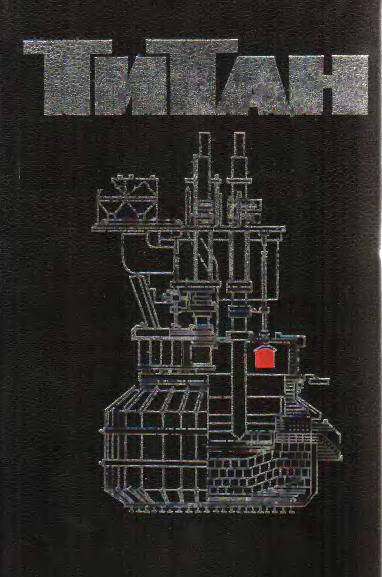
Гармата В. Л.. Петрунько А. Н, Галицкий Н. В., Олесов Ю. Г., Сандлер Р. А.
Металлургия, 1983 г.
Плавка и литьетитана и сплавов на его основе
Плавка в вакуумно-дуговых печах
Основные виды конструкционных титановых материалов — деформируемые полуфабрикаты. Поэтому титановую губку перерабатывают на компактный титан главным образом путем выплавки слитков, хотя в последнее время существенное развитие получают и другие прогрессивные методы изготовления изделий — фасонное литье, порошковая и гранульная металлургия. Расплавленный титан интенсивно горит на воздухе и взаимодействует со всеми известными огнеупорами, поэтому плавку необходимо осуществлять в вакууме или в атмосфере инертных газов и металлическом кристаллизаторе или в тигле с гарниссажем из титана. Вакуумныйпереплав обеспечивает лучшее качество металла, так как в вакууме более активно происходит десорбция и удаление из шихты газов (особенно водорода) и влаги, а также остатков магния и солей из титановой губки. Шихту чаще всего расплавляют электрической дугой постоянного тока, которая горит между расплавленным металлом и расходуемым электродом. Применяются также дуговые печи с нерасходуемым электродом. Кроме дуговых печей, используются плазменные, электрошлаковые и электронно-лучевые плавильные агрегаты.
Наибольшее распространение получила технология производства слитков, включающая следующие основные операции: приготовление шихты, прессование расходуемого электрода, первую вакуумно-дуговую плавку в водоохлаждаемом кристаллизаторе, вторую вакуумно-дуговую плавку в кристаллизаторе большего диаметра, механическую обработку слитков, контроль химического состава, механических свойств и наличия внутренних дефектов.
Шихта, состоящая из смеси титановой губки, легирующих компонентов и оборотных отходов в заданных количествах, после усреднения формируется в расходуемые электроды на специальных прессах горизонтального или вертикального типа. Наилучшие результаты дает непрерывный методпрессования на вертикальных прессах, который обеспечивает получение более однородного в поперечном сечении и достаточно длинного электрода. Специализированные гидравлические прессы с усилием 100 МН дают возможность получать расходуемые электродыдиаметром 350—650 им.
Схема технологического процесса выплавки слитков в вакуумно-дуговых печах (ВДП) представлена на рис. 138 [1]. Первый и второй переплав осуществляются в одинаковых по конструкции печах, различающихся только размерамикристаллизатора и источниками тока. Применяемые в настоящее время в промышленности печи позволяют получать слитки первого переплавадиаметром 560—850 мм, массой 2500—5000 кг и длиной 2000 — 2600 мм. Диаметр слитков второго переплава 650— 950 мм, масса 2500—10000 кг. Для первого переплава используются источники с силой тока 25 кА, для второго 37 кА [1].
Согласно сообщениям на IV Международной конференции по титану (Киото, Япония) [2], технология вакуумно-дуговой плавки с расходуемым электродом с общей тенденцией к увеличению массы слитков является доминирующей в мировой практике. Обычно слитки выплавляются массой 5—8 т. Проводятся работы по конструированию более производительных плавильных печей. Однако для получения легированных сплавов должен быть, по-видимому, определенный пределмассы слитка, выше которого увеличение степенисегрегации легирующих компонентов и примесей, а также более грубая структураметалла большого слитка, несмотря на последующие процессыковки и термообработки, будет оказывать отрицательное влияние на качество изделий. Существенным недостатком приведенной технологии
выплавки слитков является ограниченная возможность ввода титановых отходов в Шихту (~30 %) [3]. Вовлечение отходов выше указанного предела уменьшает прочность расходуемых электродов и создает опасность их разрушения при транспортировке и плавке. Ограниченная возможность вовлечения в плавку оборотных отходов в значительной степени определяет высокий расход первичной титановой губки и соответственно высокую стоимость изделий из титана. Сейчас созданы печные агрегаты, позволяющие при плавке с расходуемым электродом периодически добавлять кусковые отходы из бункера (рис. 139). Однако плавка в печах вакуумно-дугового переплава с подачейшихты в зону плавки (зону дуги) имеет ряд трудностей.
Плавка в печи с гарниссажем
Технология вакуумно-дуговой плавки прессованного электрода не может в полной мере обеспечить равномерность химического состава слитка, а также не исключает возможность образования включений в слитке за счет не полностью проплавившихся тугоплавких легирующих компонентов, а также за счет брызг металла, образующихся в процессеплавки загрязненной шихты. Эти обстоятельства, а также стремление вовлечь в Шихту для плавки повышенное количество титановых отходов привели к разработке технологииплавкититана в гарниссаже.
Гарниссажная плавкатитана (рис. 140) отличается от вакуумно-дуговой тем, что при ее проведении зона плавления отделена от зоны кристаллизации слитка. Металл наплавляется в графитовом или водоохлаждаемой тигле. Дли исключения взаимодействия расплавленного металла с материалом тигля процесс ведется таким образом, что со стенками формы всегда соприкасается затвердевшая корочка (гарниссаж) титана и его сплава.
Внедрение гарниссажной плавки позволяет отливать слитки различной формы сечения, обеспечивает лучшую гомогенностьсостава сплава, предотвращает попадание в слиток тугоплавких включений, дает возможность вводить в Шихту большую долю отходов без трудоемкого их измельчения. Печи такого типа позволяют получать высокогомогенные слитки даже таких сложных в литье сплавов, как Ti + 30 Mo, Ti + 55 Ni и др.
А. Л. Андреев и А. И. Мещеряков описывают конструкцию вакуумно-дуговой гарниссажной печи для плавкититанаемкостью 600 кг . Особенность ее состоит в том, что заливочная камера в период заливки вращается вокруг своей оси. Расходуемый электрод плавится в водоохлажденном тигле, футерованном графитовыми плитами. Подачаэлектрода осуществляется грузоподъемником, плунжер которого жестко закреплен на каркасе, а цилиндр смонтирован внутри электрододержателя. Жидкий металл из тигля сливается путем наклона плавильной камеры относительно оси в лоток, по лотку передается в заливочную камеру и через воронку—в изложницу, которая установлена на поддоне на вращающемся столе.
Для печей гарниссажного типа необходима надежная система управления тепловым балансом печи.
Замедление отвода тепла или поступление тепла в очагплавления в неучтенно повышенных количествах вызывает уменьшение толщины гарниссажа или его полное проплавление. Ускоренный или неравномерный отвод тепла из зоны плавленияприводит к неоправданному увеличению толщины гарниссажа и снижению эффективности плавки.
Гарниссажная плавка предусматривает накопление необходимой массы жидкого металла и последующий слив в форму, что определяет химическую однородность сливаемого расплава, из-за высокой скоростиперемешивания в жидком состоянии и возможность получения слитков и отливок различной конфигурации.
В работе [5] намечены основные направления развития гарниссажной плавки: фасонное литье, фасонно-заготовительное литье (кольцевые и трубные заготовки для последующих раскатки, штамповки, прессования), заготовительное литье слитков сложных форм для прокатки и прессования.
Наиболее эффективным считается способ гарниссажной плавкий с использованием в качестве расходуемого электрода гарииссажа, образовавшегося при предыдущей плавке в том же тигле. Плавление расходуемого электрода-гарниссажа предыдущей плавки осуществляется электрической дугой постоянного тока в вакууме или среде нейтрального газа. После окончания плавки необходимая часть расплава сливается в изложницу, а гарниссаж с затвердевшими остатками неслитого металла извлекается из тигля и используется в виде расходуемого электрода при последующей плавке данного сплава. При массовом производстве целесообразно применять сменный гарниссаж, специализированный по наиболее распространенным сплавам или группам сплавов, что исключает брак по химическому составу при оплавлении гарниссажа в течение каждой плавки.
Печи гарниссажного типа используются для фасонного литья различных отливок из титана с весьма высокими коэффициентами использования металла и необрабатываемой поверхности, т. е. отливок, максимально приближенных по форме и геометрическим размерам к готовой детали. Ванну жидкого металла направляют в графитовом тигле с гарниссажем из титана. Расплавленный металлсливают в заранее собранную и установленную заливочную камеру — форму. Установки такого типа позволяют получать отливкимассой в несколько десятков килограммов.
В настоящее время серийно отливаются корпуса центробежных насосов ТН-70, ТН-100, вентилей и задвижек Ду-50, Ду-100, Ду-150, Ду-200, рабочие колеса насосов и другие изделия.
Гарниссажная плавка окажется, по-видимому, оптимальной технологией первого переплава титана. Однако высокая скорость заполнения изложницы не даст возможность получить крупные слитки без усадочных раковин, рыхлой и ликвационной неоднородности. Поэтому такие слитки не могут быть использованы непосредственно для обработки давлением.
Для второго переплава, помимо существующего процесса дуговой плавки с расходуемым электродом, весьма перспективны электрошлаковый переплав либо непрерывное литье с расплавлениемэлектродаплазмой или электронным лучом.
Плавка в электрошлаковой печи и другие виды плавки.
Электрошлаковая плавкатитана и сплавов на его основе обладает рядом достоинств. Прогрев расплавленного шлака (обычно фторид кальция) электрическим током над поверхностьюметалла в кристаллизаторе позволяет перегреватьметалл выше температуры его плавления. При этом выравнивается тепловое поле по поверхности металла, углубляется ванна жидкого металла, что улучшает однородность слитка. Более равномерный прогрев слитка по его сечению при электрошлаковой плавке позволяет получать слитки прямоугольного сечения, что удобно для их дальнейшей прокатки.
Е. И. Морозов и А. Д. Чучургокик в работе [4, с, 105] описали конструкцию электрошлаковой печи для выплавки из титановых сплавов плоских слитков размером 280X820x1200 мм. В качестве расходуемых электродов применяли литые слитки или кованые штангидиаметром 220 и длиной 2300 мм. Главным недостатком электрошлакового переплава является отсутствие дегазацииметалла в процессе плавки, поэтому его целесообразно использовать в сочетании с одним из способов первого переплава в вакууме, обеспечивающим достаточно полное удаление водорода.
Продолжаются исследования одной из разновидностей электрошлаковой, плавки — индукционной электрошлаковой плавки в медном тигле , которая, как и гарниссажная плавка, позволяет получать однородный металл и использовать неограниченное количество кондиционных отходов. Роль гарниссажа в этом случае выполняет шлаковая прослойка.
Использование плазмотронов при переплавкетитана привлекает стабильностью газового разряда, хорошей регулируемостью мощности, большой концентрацией энергии, возможностью получения высоких температур и повышенной взрывобезопасностью процесса плавки. В качестве плазмообразующсго газа используют аргон. Недостатками плазменных печей является ограниченная дегазация при плавке и возможность загрязнения титана примесями, содержащимися в плазмообразующем газе. Поэтому большой интерес представляет вакуумная плазменно-дуговая плавка, которая по сравнению с вакуумно-дуговой плавкой обладает рядом достоинств: возможностью переплава кусковой некомпактной шихты, регулированием скорости плавления, более простым вакуумнымоборудованием и возможностью использования низковольтных источников тока . Использование плазменных печей перспективно для плавки отходов титановых сплавов. В работе [8] дан анализ существующих и новых методов производства слитков титановых сплавов с точки зрения возможности обеспечения решения основных задач по улучшению качества металла к повышению технико-экономических показателей процесса,
Авторы работы [8] делают вывод, что на существующем уровне развития техники наиболее перспективна технологическая схема выплавки титановых слитков, предусматривающая на первом переплаве гарниссажную плавку с использованием гарниссажа в качестве расходуемого электрода. Полученные слитки используются в качестве расходуемых электродов при электрошлаковой плавке с переливом расплава из промежуточной емкости в кристаллизатор либо при электрошлаковой плавке в уширенном кристаллизаторе. В качестве второго переплава перспективно также использовать плазменные и электронно-лучевые печи.