Термокинетические и изотермические диаграммы порошковых сталей: Справочник
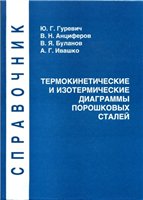
Ю. Г. Гуревич, В. Н. Анциферов, В. Я. Буланов, А. Г. Ивашко
Екатеринбург, 2001 г.
Наиболее широко при исследовании распада переохлажденного аустенита применяют дилатометрический метод [4, 7, 13]. Внутренние превращения в металлах и сплавах характеризуются изменением объема и коэффициента линейного расширения. На изучении этих изменений основан дилатометрический метод. Различие моделей дилатометров, применяемых в металлографии, обусловлено методикой определения изменения линейных размеров образцов. В практике исследования фазовых и структурныхпревращенийметаллов и сплавов нашел применение дифференциальный дилатометр Шевенара. Схема прибора приведена на рис. 1. Поворот зеркала 1 определялся перемещением кварцевых штанг 2, которые в свою очередь опирались на исследуемый образец 3 и эталон 4. Угол поворота зеркала фиксировался перемещением светового луча 5 по фотографической бумаге 6. В качестве эталона использовался образец из хромоникелькобальтового сплава (пирос) с известнымкоэффициентом расширения. Поворот зеркала осуществляется по оси А—В, если изменяется размер образца, и по оси А—С, если изменяется размер эталона. Недостаток дилатометра Шевенара и ему подобных оптических дилатометров (Веффера—Еллингхауза, Кантора и т. д.) заключается в том, что процесс не поддается автоматизации. Поэтому в современных дилатометрах используется, как правило, регистрация абсолютного измерениядеформаций с помощью электронных устройств, основанных на применении емкостных индукционных датчиков, а также тензодатчиков.
Этот метод позволяет определять начало и конец распадааустенита с малой устойчивостью. В связи с тем, что задача разделения объемного эффектапревращения и термического изменения размеров очень сложна [1], количественная оценка кинетикираспадааустенита трудно осуществима.
В работах [1—3, 8—11] описаны магнитныеметоды исследования превращений при термической обработке. Достаточно высокая чувствительностьмагнитныхсвойств к изменению фазового составастали обеспечивает необходимую надежность. Кроме того, намагниченность удобна при измерениихарактеристик пористой стали, поскольку ее изменение — линейная функция пористости. Намагниченность насыщения однородных сплавов определяется их составом, а гетерогенных — составом и количеством ферромагнитной фазы.
2.3.2. ПК45Н2
Сталь изготавливали на основе железного порошка ПЖ4М2 [22—24]. Для получения стали с пористостью 5—7 % использовали двукратное прессование с промежуточным отжигом, а с пористостью 14—16 % — однократное двухстороннее прессование. Спекание проводили при температуре 1150 °С.
Воздействие никеля на кинетикупревращенияаустенита порошковых сталей аналогично его влиянию в литых и кованых сталях. За счет изменения подвижности атомов железа, скоростидиффузииуглерода в а- и у-железе, свободной энергии фаз никель повышает устойчивость аустенита. Как и в порошковых углеродистых сталях, увеличение пористости понижает устойчивость аустенита, смещает температуру его минимальной устойчивости в область повышенных температур. Увеличение содержания углерода в никелевых сталях повышает устойчивость аустенита. Изотермические диаграммыстали ПК45Н2 с различной пористостью приведены на рис. 78 и 79. Для сравнения на рис. 80 представлены С-образные кривые распада переохлажденного аустенита в кованой стали 45Н2. В отличие от углеродистых сталей из-за неравномерного распределения никеля в порошковой смеси в никелевых сталях остаточный аустенит обнаруживается даже после спекания. В результате этого в никелевых сталях количество нераспавшегося аустенита при охлаждении больше, чем в высокоуглеродистых. Наибольшее содержание остаточного аустенита наблюдается при превращениях в области температур минимальной устойчивости аустенита, что понижает твердостьпродуктовпревращения в интервале 600— 450 °С При понижении содержания углерода в никелевых сталях количество остаточного углерода уменьшается.
2.3.5. ПК50Н6
Технология получения соответствует описанной в разделе 2.3.4 для стали ПК50Н4. Критические точки А,, А3, температуру начала Мн и конца Мк мартенситного превращения определяли дилатометрическим методом на порошковых никелевых сталях с наименьшей пористостью и близкой к оптимальной для трип сталей концентрационной неоднородностью (Мк — расчетное значение по [54]). Содержание элементов, %: С — 0,45—0,55, Ni — 6; Т, °С: Aq — 660, Ас3 — 730, Ми — 190, )
Температура аустенитизации 840—860 °С Для порошковой
стали ПК50Н6 наблюдается ускорение перлитного превращения
при повышении ее пористости (рис. 88—91).
При пористости 4—10 % проведение закалки деталей уже не представляет сложности, поскольку инкубационный период составляет 6—15 с. Окончание распада в исследуемом интервалепористости удлиняется более чем на порядок по мере снижения последней.
Микроструктура образцов из сталей ПК50Н4 в термообработанном (закалка 860 °С, масло + отпуск 180 °С, 2 ч) состоянии представляет собой бейнит с небольшими включениямиаустенита — до 10 %, микротвердость HV 300—500 (рис. 92).
2.3,6. ПК50Н9
Технология получения соответствует описанной в разделе 2.3.4 для стали ПК50Н4.
Критические точки А,, А3, температуру начала Мн и конца Мк мартенситного превращения определяли дилатометрическим методом на порошковых никелевых сталях с наименьшей пористостью и близкой к оптимальной для трип сталей концентрационной неоднородностью (Мк — расчетное значение по [54]). Содержание элементов, %: С — 0,45—0,55, Ni — 9; Т, °С: Ас, — 630, Ас3 — 690, Мн — 120, Мк — (-180).
Изотермическая диаграммараспада переохлажденного аустенита горячештампованной стали ПК40Н2М приведена на рис. 148. Она состоит из ферритной, бейнитной и мартенситной областей превращения. Па диаграмме не показана перлитная область превращения в связи с трудностью разделения бейнита и сорбита по микроструктурам стали. При температуре ниже Мк сначала происходило превращениеаустенита в мартенсит, а затем аустенита в бейнит. Время начала образования бейнита фиксировали по увеличению скоростираспада аустенита. Минимальную устойчивость переохлажденного аустенита наблюдали при температуре 500 °С — 2,5 с. Ферритноепревращение отмечено при температурах выше 530 °С
На рис. 149 приведена диаграммаскоростейраспада переохлажденного аустенитастали ПК40Н2М. Как видно, скоростираспадааустенита имеют два максимума в бейнитной области, один из которых находится при температуре 500 °С, а другой — 300 °С. Появление второго максимума скоростей образования бейнита при температурах ниже Мн можно объяснить инициирующим действием на процессраспадааустенита предварительного мартенситного превращения. Наибольшая скоростьраспадааустенитасоставила 9,89 %/с. Необходимо отметить, что температура наибольшей скоростипревращения ниже температуры минимальной устойчивости аустенита. Это явление можно объяснить тем, что максимум скоростей образования центров зарождения новой фазы не совпадает с максимумом скоростей ее роста [66].
Как было замечено, при ступенчатой закалке по режиму — аустенитизация, изотермическая выдержка — при температурах выше 530 °С в течение 300—900 с охлаждения на воздухе, с одной стороны, получали неоднородную структуру, обусловленную неравномерным распределением легирующих элементов. С другой стороны, после изотермической выдержки при температурах ниже 500 °С этого не наблюдается.
Сравнение рис. 149 и рис.145 показывает, что скоростьраспадааустенита в изотермических условиях в несколько раз выше, чем при непрерывном охлаждении. Так, максимальная скоростьпревращения в изотермических условиях в пять раз выше таковой при непрерывном охлаждении.
2.10.4. ПК100Х5М5 [107]
В качестве исходных компонентов использовали отожженное карбонильное железо 6—2, коллоидальный графит и восстановленные хром и молибден. Образцы, спрессованные при давлении 780 МПа, спекали в атмосфере осушенного водорода с точкой росы -40 °С в интервалетемператур 1050—1280° С в течение 2 ч, а также при температуре 1200 °С в течение 40 мин, 2, 3 и 4 ч.
Характер однородности твердого раствора спеченных сталей оценивали по разбросу параметров кристаллической решетки а-твердого раствора, определенному по ширине рентгеновской линии (211), а также по распределению концентрации легирующих элементов в разных участках твердого раствора, определенному с помощью рентгеновского микроанализатора МАР-2.
Разброс содержания хрома и молибдена в твердом растворестали ПК100Х5М5, спеченной при разных температурах, приведен в табл. 51.
Из приведенных данных следует, что с повышением температурыспекания распределение легирующих элементов в матрице становится более равномерным. Однако даже после спекания при температуре 1280 °С процесс полностью не завершается. Увеличение продолжительности спекания до 4 ч почти не изменяет характер формирующейся структуры.
В процессеспекания вследствие непосредственного взаимодействия между атомами углерода, хрома и молибдена происходит образование первичных труднорастворимых сложных карбидов. Все это приводит к возникновению структурной неоднородности спеченных сталей, которая проявляется заметнее в более легированных сталях.