Производство окатышей
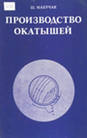
Маерчак Ш.
Металлургия, 1982 г.
ХАРАКТЕРИСТИКА КОМКУЕМЫХ МАТЕРИАЛОВ
Измельченные железорудные материалы относятся к гидрофильным дисперсным системам, для которых характерно интенсивное взаимодействие с водой. Система измельченный дисперсный железорудный концентрат — вода стремится снизить свою энергию путем уменьшения поверхностного натяжения на границе раздела фаз или степени дисперсности. Иными словами, данная Система отличается термодинамическим стремлением к окомкованию. Способность к образованию прочных гранул в процессеокомкования у железных руд и концентратов не одинаковая, эти материалы имеют различную комкуемость,
Комкуемость нельзя определить однозначно, так как она является результатом одновременного действия многих факторов, прежде всего гранулометрического состава материала, формы и свойств поверхности зерен, химико-минералогического состава.
Понятие «комкуемость» включает в себя скорости образования и роста окатышей. Так как скорости образования и роста окатышей определяются их прочностью, комкуемость можно качественно определить с помощью прочности сцепления зерен увлажненного материала.
СПОСОБЫ ОЦЕНКИ КОМКУЕМОСТИ ТОНКОИЗМЕЛЬЧЕННЫХ МАТЕРИАЛОВ
Для оценки поверхностныхсвойств комкуемых материалов и определения их способности к окомкованию прибегают к методу свободной капли (определение способности к самоокомкованию), а также к измерению капиллярного давления, высоты капиллярного всасывания и теплоты смачивания.
III. ХАРАКТЕРИСТИКА СИЛ, ДЕЙСТВУЮЩИХ В СЫРОМ ОКАТЫШЕ
Сырой окатыш обладает свойствам», типичными для твердых материалов: определенной прочностью при растяжении, изгибе и срезе, способностью сохранять форму, полученную в окомкователе. Эти свойства сырых окатышей связаны с величиной сил сцепления в сыром окатыше, а последние в свою очередь зависят от свойств комкуемого материала, типа и количества жидкости между зернами и от расстояния между поверхностями зерен комкуемого материала.
Силы, содействующие формированию сырых окатышей, можно разделить на естественные (физические) и приложенные извне (механические). Румпф и Турба [28] классифицировали разные типы связей и механизмысвязей в сыром окатыше. Отдельные типы связей характеризуют природные силы, источниками которых могут быть: а) мостики твердых материалов (взаимное сцепление частиц обеспечивается их формой); б) силы адгезии и когезии в жестких мостиках связи; в) межфазные и капиллярные силы вследствие присутствия жидкой фазы; г) притяжение между твердыми частицами, вызванное силами Ван-дер-Ваальса, магнитными или электростатическими силами.
V. МЕХАНИЗМ ОБРАЗОВАНИЯ И РОСТА СЫРЫХ ОКАТЫШЕЙ
Изучением механизма образования и роста окатышей занимаются сравнительно мало исследователей. Вероятно, первой была работа [24], в которой отмечено, что образование зародышей комков начинается после создания водной пленки на поверхности частиц. Соприкасаясь, частицы с водной пленкой объединяются, т. е. образуются зародыши комков, которые начинают расти в процессе окомкования. По данным [19], образование зародышей происходит вблизи подвода увлажнителя, где наиболее вероятно переувлажнение шихты. Эта часть тарели называется зоной образования зародышей. Остальная часть тарели называется зоной окомкования. Определенный гранулометрический состав получаемых окатышей может измениться только в том случае, если часть окатышей с низкой прочностью при ударах о стенки окомкователя или взаимных столкновениях разрушится.
К такому же заключению пришли авторы работы [34]. По этим данным, большую плотность имеют те окатыши, на которые при столкновениях действуют небольшие силы. Окатыши, подвергнутые воздействию больших сил, разрушаются, но возможен их повторный рост. Процесс роста окатышей заканчивается по достижении равновесного состояния. Ход процессаокомкования до наступления равновесного состояния зависит от гранулометрического состава смеси: если смесь содержит только тонкоизмельченные частицы, то скорость роста окатышей будет низкой. Одновременно с увеличением размеров окатышей возрастает и их плотность. Силы, которые возникают при столкновении окатышей между собой или со стенками установки, часто являются недостаточными для разрушения окатышей, но могут увеличивать их плотность. Если смесь содержит только крупные частицы, то вероятность разрушения окатышей при столкновениях возрастает. В системах с зернами разных размеров образовавшиеся крупные комки при столкновениях с мелкими разрушают их и растут за счет материала разрушенных окатышей. В результате скорость роста окатышей уменьшается, но наблюдаются уплотнение окатышей, повышение их прочности и сопротивления разрушению.
Опытами с песком разного цвета [41] было установлено, что начало роста окатышей обусловлено образованием сгустков, а последующий рост происходит путем накатывания слоев. При окомковании часть белого .песка (15%) заменили темным песком. По достижении окатышами диаметра 4 мм Процесс прекращали. Полученные окатыши имели светлую сердцевину, а выше располагался темный песок. Количество темного песка в направлении к поверхности окатыша уменьшалось. Это позволило заключить, что окатыши с низкой прочностью разрушаются и образующийся в результате материал наслаивается на более крупные и прочные окатыши. Если к окатышам из белого песка диаметром 2 мм прибавить некоторое количество окатышей из темного песка, но больших размеров, то количество последних практически не изменится, причем на окатыши из темного песка накатывается слой белого песка из счет разрушения менее прочных белых окатышей.
VII. свойства СЫРЫХ ОКАТЫШЕЙ
Сырые окатыши из различных концентратов, полученные в неодинаковых условиях, имеют соответственно неисходные свойства. Для их сравнения наиболее часто используются такие характеристики сырых окатышей, как форма и размер, механическая прочность, пористость и величина поверхности, стойкость при быстром нагреве.
Ниже приводится анализ этих параметров, рассматриваются факторы, влияющие на них, и методики, применяемые для определения этих параметров.
X. СУШКА ОКАТЫШЕЙ
Сырые окатыши обладают низкой прочностью и их прямое применение ограничено; например, их можно переплавлять в конверторах и нельзя в доменных печах. Поэтому окатыши упрочняют при высокой температуре или путем использования связующего вещества с последующим упрочнением без воздействия высокой температуры. До сих пор в большинстве случаев применяется высокотемпературное упрочнение. Этот Процесс протекает в два этапа: сначала СУШКА окатышей, затем нагрев и обжиг при 1250—1350° С.
Установки для высокотемпературного упрочнения окатышей
Производство сырых окатышей хотя и является важной частью технологического цикла производства окатышей, но наиболее ответственным является этап высокотемпературного их упрочнения — обжиг окатышей. Этап высокотемпературного упрочнения окатышей складывается из процессов подсушки, сушки, подогрева, обжига и охлаждения окатышей. Каждый из этих процессов может в значительной степени повлиять на ход процессаобжига и на свойства готовых окатышей. Во время подсушки происходит медленное удаление воды. Если обжиговой агрегатработает по схемепродувки сверху, то возникает опасность образования переувлажненного слоя непосредственно над колосниковой решеткой. При быстрой сушке возможно растрескивание окатышей. Для процесса подогрева характерным является низкая прочность окатышей. Наиболее важной является стадия обжига, протекающая при наиболее высоких температурах. В результате происходит связывание рудных зерен расплавом. Важным является соблюдение интервалатемператур обжига, характерного для каждого концентрата. При низких температурахобжига количество соединений рудных зерен недостаточно и, как следствие этого, обожженные окатыши имеют низкую прочность. При слишком высокой температуреобжига образуются грозди и конгломераты из окатышей, в результате чего их металлургические свойства ухудшаются.
Охлаждение окатышей не вызывает особых проблем, за исключением большого количества воздуха.
Отдельные операцииобжига окатышей могут осуществляться в одной обжиговой установке на конвейерноймашине или в шахтной печи. При обжиге окатышей необходимо обеспечивать оптимальную температуру и скоростьпроцесса в соответствии с природой материала и его влажностью. До сих пор окатыши получают путем их высокотемпературной обработки в шахтных печах, на .прямых или кольцевых обжиговых конвейерныхмашинах или на комбинированных установках, которые включают прямую обжиговую конвейернуюмашину и трубчатую вращающуюся печь; прямую и карусельную конвейерныемашины и шахтную печь (процесс «Surface Combustion); кольцевую и шахтную печи (процесс Хантингтона—Геберлейна). Существуют и другие комбинации установок, которые в настоящее время находятся в стадии проектирования или опробования в форме моделей.