Пористая конструкционная керамика
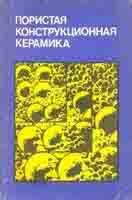
Красулин Ю. Л., Тимофеев В. Н., Баринов С. М. и др.
Металлургия, 1980 г.
Для изготовления пористой конструкционной керамики выбран стабилизированный диоксид циркония. Стабилизирующими добавками для диоксида циркония являются CaO, MgO, Y2O3 и некоторые другие оксиды [4, 59]. Стабилизация ZrO2 основана на образовании с одним из указанных оксидов твердого раствора кубической системы (структурный тип флюорита), устойчивого в широком диапазоне температур. В зависимости от вида и концентрации добавляемого оксидастепень стабильности образующегося твердого раствора различна. Наиболее часто для стабилизации диоксида циркония используют 5—7% СаО. Однако оксидкальция обладает большой упругостью пара, и это приводит к изменению стабильности системыZr02—СаО при высоких температурах (~ 2000°С) [60, 61]. Наибольшая стабильность диоксида циркония достигается при введении > 15% Y203. Но применение системыZrO* — У203 ограничивается экономическими факторами. Поэтому наиболее распространены в промышленностиогнеупорныеизделия из диоксида циркония, стабилизированного оксидом кальция.
В данной работе получение указанных материалов осуществлялось из диоксида циркония, стабилизированного оксидами как кальция, так и иттрия. Сфероидизации подвергали электроплавленый порошок (дробленку) из технического диоксида циркония, стабилизированного оксидамикальция (~ 6%) и иттрия (~ 11%) производства опытного завода УкрНИИО. Порошок перед сфероидизацией рассеивали на фракции от 40 до 315 мкм с шагом, размер которого определялся возможностями ситового анализа с применением прибора 029-М. Рассеянный на фракции порошок сфероидизировали на высокочастотных плазменных установках, изготовленных на основе генераторов ЛЗ-13 и ЛИГ1-60. В качестве плазмообразующего газа использовали воздух, его расходсоставлял (3—6) • 10"4 м3/с, порошок подавался через шихтопровод по схеме, показанной на рис. 9.
Исследование структуры, химического и фазового состава микросфер проводили методами оптической и электронной микроскопии, химического и рентгеноструктурного анализа. Методом оптической микроскопии исследовали прозрачные и полированные шлифы. Последние подвергали травлению в течение 15 мин в кипящем слое плавиковой кислоты. Определяли также показатели преломления составляющих структуру микросфер элементов в высокопреломляющих жидкостях (ОВИЖ) и при помощи сплавов серы и селена с показателями преломления п > .2. Методом сканирующей электпонной микроскопии на приборе "Стереоскан S4-10" проводили исследование структурыповерхности и сколов микросфер. Рентгеноструктурный анализ применяли для исследования фазового состава микросфер. Дифрактограммы снимали аппаратом "Дрон-0,5" с использованием фильтрованного медного излучения.
Поскольку задачей настоящей работы является выяснение возможности улучшения механических свойств пористой керамики в результате упорядочения структуры, то основные исследования выполнены на системеZr02-CaOкак наиболее дешевой. Технология микросфер и материала из микросфер диоксида циркония, стабилизированного оксидом иттрия, разрабатывалась одновременно, но с использованием полученной информации на системеZr02-CaO. Поэтому ниже прежде всего приведены результаты разработки и исследования свойствматериала из диоксида циркония, стабилизированного оксидом кальция.
Исходные порошкисоставаZr02—СаО, полученные путем дробления электроплавленой массы, представляют собой частицы неправильной формы с раковистым изломом. Примерно 50% частиц имеют матовую поверхность и непрозрачны, 20% — прозрачны и бесцветны1, 30% - прозрачны и окрашены примеЬями в зеленые и желтые тона. Показатель преломления частиц, слагающих основную массу порошка, равен 2,2, что соответствует показателю преломления кубического твердого раствораоксидакальция в диоксиде циркония. Но на прозрачных шлифах в частицах обнаруживаются зоны (до 10% площади), поляризующие в высоких тонах, что в этой системе характерно для диоксида циркония моноклинной модификации. Это свидетельствует о том, что керамические порошки, полученные электроплавкой на блок с последующим дроблением, не обладают гомогенным фазовым составом.
После обработки в высокочастотном разряде порошки приобретают сферическую форму (рис. 18). По внешнему виду их можно разделить на три группы: прозрачные, полупрозрачные и матовые. Прозрачные микросферы получаются в случае полного проплавления в плазме исходных частиц, полупрозрачные — в случае частичного, а матовые — в случае поверхностного оплавления. Доля тех или других микросфер в массе зависит от их диаметра. Наибольшее количество Прозрачных микросфер (до 70%) получается при обработке мелких частиц (< 50 мкм); частицы с диаметром > 100 мкм, как правило, превращаются в микросферы матового вида. Причина этого заключается в том, что, с одной стороны, теплофизические условияобработки неодинаковы по объему плазменного факела, а с другой — частицы большего диаметра за время пролета плазменного факела не успевают полностью расплавиться. Продолжительность пребывания частиц в плазме составляет доли секунды. В результате плавления, сфероидизации и частичного испаренияразмер (условный диаметр) исходных частиц уменьшается, по данным ситового анализа, в 1,1—1,25 раза. Выход сферических частиц при обработке в плазме порошков фракций от 40 до 315 мкм достигает 90-95%. Среди микросфер присутствуют частицы исходного порошка, а также агломерированные (спекшиеся в плазме) микросферы. На фотографии порошка после плазменной обработки (рис. 18) видны отмеченные дефекты
сфероидизации. При последующем рассеве микросферы приобретают однородный гранулометрический состав в пределах монофракции.
На поверхности матовых микросфер при их исследовании на сканирующем электронноммикроскопе выявляется микрорельеф (рис. 19, а). На сколах и шлифах матовых микросфер видны две структурные зоны: поликристаллический слой в области, примыкающей к поверхности, и ядро в центре. Поликристаллический слой сложен из блоков различного размера, разделенных глубокими и ветвистыми границами раздела (рис. 19, б). Размер блоков на поверхности микросфер диаметром ~ 300 мкм колеблется в пределах 25-90 мкм. Блоки сложены из зерен, размер которых в зависимости от расположения составляет 2—20 мкм.