Металлообрабатывающий твердосплавный инструмент
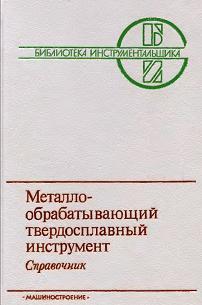
Самойлов В.С., Эйхманс Э.Ф., Фальковский В.А.
Машиностроение, 1988 г.
1.2. Свойства и области применения вольфрамокобальтовых твердых сплавов
Вольфрамокобальтовые сплавы (ВК) состоят из карбидавольфрама и кобальта. сплавы этой группы различаются содержанием в них кобальта, размерами зерен карбидавольфрама (WC) и технологией изготовления. Для оснащения режущего инструмента применяют сплавы с содержанием кобальта 3—10 %.
В табл. 1.5 приведены состав и характеристик» основных физико-механических свойствсплавов в соответствии с ГОСТ 3882—74.
Характеристики физико-механических свойствсплавов на основе WC—Со с различным содержанием кобальта приведены в табл. 1.6.
При увеличении в сплавах содержания кобальта в диапазоне от 3 до 10 % пределпрочности при поперечном изгибе, ударная вязкость и пластическая деформация возрастают, в то время как твердость и модульупругости уменьшаются. С ростом содержания кобальта повышаются теплопроводностьсплавов и их коэффициент термического расширения, при одновременном снижении удельного электрического сопротивления.
Из магнитныхсвойствсплавов для контроля наиболее широко используют коэрцитивную силу. Она обусловливается степенью напряженности кобальтовой фазы; чем тоньше прослойки этой фазы, тем выше значения коэрцитивной силы.
Сплав ВК6-0М обладает высокой стойкостью при тонком точении и растачивании жаропрочных и коррозионно-стойких сталей и сплавов некоторых марок, чугунов высокой твердости, в том числе ковких, закаленных сталей и алюминиевых сплавов. Особенно эффективен этот сплав при обработкевольфрама и молибдена, а также при развертывании и шабрении стальных и чугунных заготовок.
Сплав ВКЮ-ОМ предназначен для черновой и получерновой обработки коррозионно-стойких сталей, титановых и никелевых сплавов некоторых марок и особенно сплавов на основе вольфрама и молибдена.
Благодаря особо мелкозернистой плотной структуресплавов можно при заточке и доводке инструментов, оснащенных сплавом типа «ОМ», достигать наименьших радиусов скругления режущих кромок. Это обеспечивает получение меньших шероховатости обработанной поверхности и отклонения размеров.
С целью экономии дефицитного тантала и снижения стоимости, разработаны сплавы, в которых карбидтантала заменен карбидом хрома. карбидхроматормозитрост зернакарбидавольфрама при спекании и при добавлении его получаются сплавы с весьма мелкозернистой однородной структурой и высокой износостойкостью. Что касается прочности, то добавка карбидахрома неоднозначно влияет на пределпрочности при изгибесплавов с разным содержанием кобальта: в сплаве с 6 % кобальта введение карбидахрома до 1 % по массе снижает пределпрочности при изгибе (при комнатной температуре), в сплаве с 10 % кобальта добавка хрома не вызывает изменения прочности, а в сплаве с 15 % кобальта добавка карбидахрома даже повышает предел прочности по сравнению с аналогичным сплавом типа «ОМ».
Во всех случаях легированиесплавовкарбидомхрома увеличивает их твердость и прочность при повышенных температурах.
Характеристики основных физико-механических свойствсплавов типа «ХОМ» приведены в табл. 1.8, а примеры применения сплавов типа «ОМ» и «ХОМ» —в табл. 1.9. Наряду с содержанием кобальта и зернистостью фазы WC, большое влияние на режущие Свойствасплавов на основе WC—Со оказывает содержание углерода в сплаве.
1.3. Свойства и области применения титановольфрамокобальтовых твердых сплавов
Сплавы второй группы (на основе WC—TiC—Co) предназначены главным образом для оснащения инструментов при обработке резанием сталей, дающих сливную стружку. По сравнению со сплавами на основе WC—Со они обладают большей стойкостью к окислению, твердостью и жаропрочностью и в то же время меньшими теплопроводностью и электропроводностью, а также модулем упругости.
Способность сплавов на основе WC—TiC—Со сопротивляться изнашиванию под воздействием скользящей стружки объясняется также и тем, что температура схватывания со сталью у сплавов этого типа выше, чем у сплавов на основе WC—Со, что позволяет применять более высокие скорости резания при обработкестали и существенно повышать стойкость инструмента.
В табл. 1.10 приведены состав и характеристики основных физико-механических свойствсплавов в соответствии с ГОСТ 3882—74.
Характеристики физико-механических свойствсплавов на основе WC—TiC—Со с различным содержанием кобальта приведены в табл. 1.11.
Так же как у сплавов на основе WC—Со, пределпрочности при изгибе и сжатии и ударная вязкость увеличиваются с ростом содержания кобальта, в этом же направлении происходит снижение значений коэрцитивной силы.
У сплавов с одинаковыми содержанием кобальта и размером зерен карбидных фаз пределыпрочности при изгибе и сжатии, ударная вязкость, пластическая деформация и модульупругости уменьшаются при увеличении содержания карбида титана.
Твердость сплавов, имеющих одинаковую зернистость карбидных фаз и содержание карбида титана, уменьшается с ростом содержания кобальта, в то время, как при одинаковом размере зерен карбидных фаз и равном содержании кобальтатвердость практически не зависит от содержания карбидатитана в сплавах.
Теплопроводность сплавов на основе WC—TiC—Со существенно ниже, а коэффициент линейного термического расширения и электрическое сопротивление выше, чем у сплавов WC—Со. Соответственно меняются и режущие Свойства сплавов: при увеличении содержания кобальта снижается износостойкостьсплавов при резании, а при увеличении содержания карбидатитана (при постоянном объемном содержании кобальта) повышается износостойкость, но одновременно снижается эксплуатационная прочность.
Поэтому такие сплавы, как Т30К4 и Т15К6, применяют для чистовой и получистовой обработкистали с высокой скоростью резания и малыми нагрузками на инструмент. В то же зремя сплавы Т5КЮ и Т5К12 с наибольшим содержанием кобальта предназначены для работы в тяжелых условиях ударных нагрузок с пониженной скоростью резания.
Зависимость основных свойствсплавов от размера зерен карбидных фаз на основе WC—TiC—Со носит более сложный характер, так как одновременно оказывает влияние на Свойства и зернистость фазы WC и зернистость фазы WC—TiC.
Наименьшую прочность при изгибе имеют сплавы с крупнозернистой титановой фазой и мелкозернистой фазой WC.
При постоянном размере зерен титановой фазы и с увеличением среднего размера зерен фазы WC твердость и износостойкость при резании уменьшаются, а прочность растет. Изменение указанных свойств в зависимости от зернистости фазы WC на примере сплава Т5К12 приведено в табл. 1.12. При постоянном размере зерен фазы WC и при увеличении размера зерен титановой фазы твердостьсплава практически не меняется.
С увеличением содержания углерода в пределах трехфазной области пределпрочности при изгибе растет, а твердость и износостойкость при резании снижаются, наличие структурно свободного углеродаприводит одновременно к снижению прочности, твердости и износостойкости при резании. Присутствие в сплаве фазы т) (двойной карбидвольфрама и кобальта) снижает пределпрочности при изгибе, но повышает твердость и износостойкость при резании.
Для обработкисталей с ударными нагрузками твердые сплавы должны обладать не только прочностью, но и пластичностью.
Повышение пластичности достигается не только увеличением размера зерен фазы WC, но и применением высокотемпературных процессоввосстановлениявольфрама и карбидизации.
Сплавы на основе «высокотемпературного» карбидавольфрама обладают высокой сопротивляемостью ударным нагрузкам, что обусловлено сравнительно высокой пластичностью этих сплавов.
Путем введения в сплавы легирующих добавок получены сплавы, применяемые для резания стали с большими ударными нагрузками.
Разработан сплав Т4К8 для замены стандартного сплава Т5КЮ. пределпрочности его при изгибе 1600 МПа, в то время как у сплава Т5КЮ он составляет 1400 МПа. Предельная пластическая деформация Т4К8 1,6 %, а у сплава Т5КЮ —0,4 %.
Сплав Т4К8 в большей степени, чем сплав Т5КЮ, сопротивляется ударным нагрузкам и может применяться при черновой токарной обработке стальных отливок при скорости резания 30—70 м/мин, глубине резания до 40 мм и подаче 1 —1,2 мм/об. стойкость инструмента, оснащенного сплавом Т4К8 в 1,5—2,0 раза выше, чем стойкость инструмента, оснащенного сплавом Т5КЮ.
5.4. Шлифовальные круги и рекомендации по их применению
Шлифовальные круги характеризуются: материалом и размером зерен; видом и твердостью связки; структурой; формой и размером.
Для обработки твердого сплава используют шлифовальные круги из черного (5C и зеленого (6С) карбида кремния.
Круги из карбидакремниявыпускают на керамической (КО; KI; КЗ; К5; К7; К8;К51) и бакелитовой (Б; Б1; Б2; БЗ; Б4; БУ) связках. Керамическая связка наиболее универсальна. Круги на керамической связке обладают высокой прочностью и кромко-стойкостью. Это самая теплостойкая связка, она обладает водостойкостью и химической стойкостью, большими, чем у других связок. Недостаток связки — повышенная хрупкость и малая упругость. Бакелитовая связка придает кругам высокие прочность и упругость, позволяя работать на скоростях до 70 м/с. Недостатки ее следующие: низкая теплостойкость (при температуре 523— 573 К зерна круга выкрашиваются вследствие выгорания связки); невысокая химическая стойкость (при применении охлаждающей жидкости, содержащей более 1,5 % кальцинированной соды, резко снижаются прочность и твердость кругов); для предотвращения этого явления круги покрывают парафином или лаком. Связка БУ предусматривает применение упрочняющих материалов (тканевые прокладки, сетки) и предназначена для работы со скоростью резания до 100 м/с.
Связка определяет одно из основных свойств кругов — твердость. твердость — это способностьсвязки удерживать абразивные зерна на поверхностиинструмента при воздействии на них сил резания. Изменение твердости кругов достигается подбором связки. Обозначение твердости и области применения при обработке твердых сплавов даны в табл. 5.4.
Круги выпускают с различным соотношением (%) зерен, связки и пор в единице объема круга, т. е. различной структуры. Круги с большим числом пор имеют более свободное пространство для размещения срезаемой стружки и продуктов их распада. Поэтому снижается вероятность образования дефектов на обрабатываемой поверхности. Обозначение структур и рекомендуемые области применения шлифовальных кругов приведены в табл. 5.5.
Шлифовальные круги выпускают различных форм и размеров. Формы и размеры шлифовальных кругов для обработки твердых сплавов приведены в табл. 5.6.
Эффективность использования инструментов одностороннего резания во многом определяется выбором рациональных значений подач и условийподачи в зону резания СОЖ.
При работе сверлами диаметром 3—30 мм одностороннего резания с внутренним подводом СОЖ значения подач, расхода и давления СОЖ следует выбирать при обработке заготовок из конструкционных сталей по табл. 3.89, а чугунов — по табл. 3.90. Значения подач, расхода и давления СОЖ для головок сверлильных с наружным подводом СОЖ и сверл с эжекторным отводом стружки следует выбирать при обработке деталей из стали по табл. 3.91 и при обработкечугуна по табл. 3.92.
Значения скорости резания и, осевой силы Р и мощности N для сверл одностороннего резания диаметром 3—30 мм с внутренним подводом СОЖ при обработкестали даны в табл. 3.93, при обработке серого чугуна — в табл. 3.94.
Значения рекомендуемой скорости резания, осевой силы и мощности для головок сверлильных диаметром 16—65 мм с наружным подводом СОЖ при обработкестали даны в табл. 3.95, при обработке серого чугуна — в табл. 3.96.
Для приведенных значений скорости резания средние значения периода стойкости и критерия затупления (ширина фаски износа по задней поверхности у периферии сверла) даны для сверл одностороннего резания диаметром 3—30 мм в табл. 3.97, для головок сверлильных диаметром 16—65 мм с наружным подводом СОЖ — в табл. 3.98.
Сверла для сверленияотверстий в печатных платах. В настоящее время широко распространена обработкаотверстий в печатных платах твердосплавными сверлами.
Эти сверла выпускают четырех видов: спиральные твердосплавные, короткая серия — по ГОСТ 22093—76; те же, длинная серия — по ГОСТ 22094—76; комбинированные твердосплавные — по ГОСТ 20686—75; сверла спиральные твердосплавные для сверленияотверстий в печатных платах на станках с ЧПУ — по ТУ 2-035-853—81.
Основные размеры выпускаемых сверл указаны в табл. 3.99.
Сверление отверстий в печатных платах, не покрытых защитным лаком, целесообразно выполнять с подачей 0,02—0,05 мм/об и со скоростью резания 40—55 м/мин при обработке стеклотекстолита и 30—45 м/мин при обработке гетинакса.
Средняя стойкость сверл составляет в этих случаях 3000 отверстий при критерии затупления по задней поверхности режущей части /i3 — 0,05 ... 0,07 мм — для сверл диаметром до 1 мм и при h, — 0,07 ... 0,08 мм — для сверл диаметром свыше 1 мм.
Зенкеры твердосплавные выпускают четырех типов: зенкеры цельные с коническим хвостовиком и насадные, оснащенные пластинами из твердого сплава, и зенкеры с коническим хвостовиком.
5.9. Электроалмазная обработка твердого сплава
Электроалмазное шлифование (заточка) — комбинированный метод обработки, при котором имеют место электрохимическое, электрофизическое и механическое воздействия на обрабатываемую поверхность заготовки. В зависимости от условийобработки могут превалировать те или другие явления.
Доля электрохимического съема должна составлять 30—50 %.
При правильно подобранных режимах шлифованияанодноерастворение происходит в слое, толщина которого соизмерима с толщиной снимаемой стружки. растворениесвязки твердого сплава облегчает резание, так как карбиды легче вырываются из связки пониженной прочности, при этом не требуется их дробления и скалывания алмазными зернами круга. Механический съем непрерывно обновляет обрабатываемую поверхность, способствуя прохождению анодного растворения в новых, более глубинных слоях заготовки. Во время обработки между заготовкой (анод) и алмазным кругом (катод) создается зазор толщиной около 0,01 мм, в который подается электролит. Плотность тока в межэлектродном зазоре достигает 150—200 А/см2.
Для стабильного прохождения процесса нужен постоянный зазор. Уменьшение зазора вследствие засаливания круга, форсирования режимов приводит к возникновению электроконтактных явлений, резко повышающих расходматериала кругов. Если форсировать режимы обработки, то алмазные зерна режут «нераство-ренный» слой заготовки, в результате чего повышается износ круга и возникают дефектыповерхности заготовки.
В настоящее время наиболее широко применяют многопроходную электроалмазную обработку, когда припуск снимают с подачей на глубину 0,02—0,10 мм за каждый рабочий ход. Перспективна глубиннаяобработка при съеме всего припуска за один или несколько рабочих ходов с глубинойшлифования 0,5 мм и более за двойной ход. обработка этих видов может осуществляться как с жесткой подачей, так и с упругим прижимом заготовки.
Одно из преимуществ электроалмазной обработки — возможность обработки твердосплавной пластины одновременно со стальной державкой. Применяя этот метод, необходимо иметь в виду следующие его особенности. Во время обработкистали снижение прочностныхсвойств поверхностного слоя в результате анодного растворения меньше, чем при обработке твердого сплава. Это приводит к тому, что соотношение толщины твердосплавной пластины и стальной державки оказывает существенное влияние на процесс и результаты шлифования (заточки), так как меняются мощность и силы резания.
Вследствие большой адгезии алмаза к сталирезко увеличивается расход алмазов, если не выдерживать рекомендуемых режимов обработки. Так, поперечная подача более 0,02 мм, а продольная — более 1,0 м/мин не желательны. При упругом шлифовании продольную подачу целесообразно снизить до 0,1— 0,4 м/мин. Повышение напряжения тока выше 6 В также приводит к повышенному износу круга. При увеличении отношения размеров стальной державки и размеров твердосплавной части от 1 : 1 до 3 : 1 шероховатость твердосплавной части повышается, а себестоимость обработки увеличивается примерно в 1,5 раза.
По сравнению с алмазной электроалмазная обработка повышает производительность в 2—2,5 раза, а однопроходная, глубинная — до 8—10 раз. Снижается шероховатость обрабатываемой поверхности, улучшаются физико-механические Свойства обрабатываемой поверхности, так как снижаются термические и динамические нагрузки в процессе резания. Почти в 2 раза уменьшается расход алмазных кругов, а режущие Свойства инструмента, после электроалмазной заточки повышаются до 1,5 раз. Необходимо иметь в виду, что при электроалмазной заточке радиус скругления режущей кромки получается несколько большим, чем при алмазной 0,008—0,015 мм, это позволяет не проводить специальной операции скругления кромок.
5.10. Выбор характеристики кругов, режимов обработки и электролита
Эффективность электроалмазной обработки зависит от качества разработки технологических процессов применительно к конкретным условиям производства. Для электроалмазной обработки применяют круги из искусственных алмазов АС15, АС6, АС4. Предпочтительнее более прочные алмазы. Лучшими режущей способностью и стойкостью обладают алмазы АС15, но область их применения ограничена, так как они не выпускаются зернистостью менее 100/80. Для повышения стойкости кругов целесообразно использовать алмазы агрегатированные и металлизированные АС6М, АС4М, АС6МА, АС4МА.
При электроалмазной обработке зернистость круга в меньшей степени влияет на производительность, чем при алмазной заточке. Для достижения параметрашероховатости Rz > 0,32 мкм следует применять круги зернистостью 250/100—100/80. Предпочтительней зернистость 125/100. Если требуется Rz = 0,16 ... 0,08 мкм, выбирают круги зернистостью 80/63—50/40.
Для электроалмазной обработки необходимы круги на токо-проводящих металлических антифрикционных, высокопористых связках. Наибольшее применение нашли связки М04; МВ1; М5-5; М5-8; М13; М13Э, МВ1П, а также специальные БЦЗ, Б8, ТМ.
Для глубинного шлифования предпочтительнее связки М13Э, МВ-1, М5-5, так как при остальных связкахрасход алмазов выше. Эти связки обеспечивают максимальную стабильность резания, хорошую самозатачиваемость. Наилучшую самозатачиваемость обеспечивают связки М13, М04. Наиболее универсальная связка МВ-1.