Лабораторные работы по технологии литейного производства
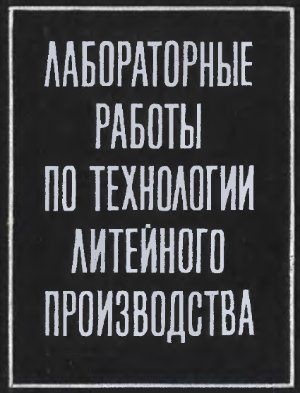
А.В. Курдюмов
Машиностроение, 1990 г.
При центробежном литье применяют самые разнообразные литейные формы, но наиболее часто используют металлическую форму—изложницу. Ее предварительно подогревают до ~300 °С, затем на рабочую поверхность наносят слой смазки или огнеупорное покрытие, которые предотвращают приваривание отливки к форме, снижают скорость охлаждения отливки и повышают стойкость изложницы. Изменяя толщину покрытия, регулируют скорость охлаждения, снижают отбел чугунных отливок, предупреждают образование спаев, трещин. Покрытие может содержать модифицирующие и легирующие добавки. В этом случае оно служит также для регулирования структуры и состава поверхностных слоев отливки. Покрытиями служат краски, облицовки или сыпучие материалы. Последние применяют при изготовлении цилиндрических отливок (труб, втулок, гильз и т. п.) в формах, вращающихся вокруг горизонтальной оси, совпадающей с осью отливки (см. рис. 36, с). Сыпучие покрытия наносят на форму во время вращения. Мелкодисперсный материал покрытия удерживается на поверхности формы центробежной силой. Затем во вращающуюся форму через специальный желоб заливают жидкий металл. После затвердевания и частичного остывания отливки вращение формы прекращают, горячую отливку извлекают из формы и в дальнейшем ее охлаждают на воздухе или в охладительной камере. При изготовлении отливок из сплавов цветных металлов в целях измельчения структуры и повышения их механических свойств металлические формы подвергают интенсивному охлаждению водой. При центробежном литье важным параметром управления технологическим процессом является частота вращения формы.
И СТЕРЖНЕВЫХ СМЕСЕЙ
Общие сведения
Для изготовления разовых форм применяют единые, облицовочные и наполнительные формовочные смеси. Единые смеси, как правило, используют для формовки по-сырому, т. е. когда заливка металла производится во влажные формы. Облицовочные смеси служат для выполнения поверхности формы, непосредственно контактирующей с металлом. Их применяют при изготовлении средних и крупных форм, которые подвергают сушке или поверхностной подсушке. Облицовочную смесь наносят на модель слоем 50—60 мм, остальной объем опоки заполняют наполнительной смесью. Очень часто в качестве облицовочных смесей крупных форм используют самотвердеющие смеси, позволяющие исключить операцию сушки. В настоящее время для изготовления стержней и малогабаритных форм применяют песчаносмоляные смеси, отвердевающие в холодной или нагреваемой оснастке.
Обладая низкой вязкостью, смолы равномерно распределяются по объему смеси, обеспечивая высокие технологические и прочностные свойства. Использование таких смесей позволяет автоматизировать процессы изготовления стержней, повысить их размерную точность, уменьшить площади стержневых отделений за счет ликвидации операции сушки. Осуществление этих процессов требует применения обогащенных кварцевых песков, в которых содержание глинистых составляющих не превышает 0,5 %, а также меньшего количества минералогических примесей, чем это допускается ГОСТ 2138—84. Увеличение содержания глины свыше 0,5 % потребует для сохранения физико-механических свойств смесей повышенного расхода связующего и отвердителя, что увеличит стоимость смеси и ухудшит санитарно-гигиенические условия труда. Примеси в песках могут вступать во взаимодействие с компонентами связующего и отвердителя, что вызовет ухудшение технологических свойств смесей. Поэтому для приготовления песчано-смоляных смесей рекомендуется использовать пески марок О61К02 и О61К016. Типовые составы формовочных и стержневых смесей приведены в прилож. 1.
В литейных цехах контроль качества формовочных и стержневых смесей сводится к определению следующих физико-механических характеристик: содержание глинистой составляющей, влажность, газопроницаемость, предел прочности при сжатии во влажном и сухом состояниях, предел прочности при растяжении, а иногда при срезе и изгибе. Кроме того, при разработке новых составов смесей определяют газотворность, осыпаемость, поверхно¬стную твердость, долговечность, текучесть, выбиваемость и живучесть.
Влажность. Под влажностью формовочной смеси понимается содержание в ней свободной и гигроскопической влаги, выраженное в процентах к массе смеси. Содержание влаги в смесях определяется нормальным или ускоренным методом.
Нормальный метод. Навеску 50 dt 0,01 г исследуемой смеси помещают в предварительно высушенные и взвешенные фарфоровые чашки и переносят в сушильную печь. Температура в печи должна быть 105—ПО °С. По истечении 30 мин чашку с навеской вынимают из печи и взвешивают, затем опять помещают в печь. Каждое последующее взвешивание производят после высушивания в течение 15 мин до постоянной массы. После этого чашки с навеской помещают в эксикатор, где охлаждают до нормальной температуры. Охлажденную навеску взвешивают.
ИЗГОТОВЛЕНИЕ СТЕРЖНЕЙ
С УПРОЧНЕНИЕМ ТЕПЛОВОЙ СУШКОЙ
Общие сведения
Стержни являются элементами литейных форм. Их применяют для выполнения в отливках внутренних полостей и отверстий. С помощью стержней частично или полностью формируют и наружные поверхности отливок. Стержень состоит из рабочей и знаковой частей. Рабочая часть непосредственно контактирует с металлом и формирует требуемую геометрию полостей, отверстий и наружных поверхностей отливки. Знаковая часть стержня не контактирует с заливаемым в форму жидким металлом. Она обеспечивает фиксацию стержня в литейной форме. Знаковая часть стержня опирается на знаковую часть формы. Ее прочность должна быть достаточной, чтобы выдерживать нагрузку, обусловленную собственным весом стержня и давлением жидкого металла на стержень. Через знаки также удаляются газы, образующиеся в стержне под тепловым воздействием металла.
К стержням предъявляют более высокие, чем к формам, требования по огнеупорности, газопроницаемости, термохимической устойчивости, прочности, податливости, выбиваемости, газо-творности и осыпаемости. Обеспечить выполнение всех этих требований очень трудно, но к этому нужно стремиться. Для этого стержни, как правило, изготовляют из кондиционных свежих формовочных песков с использованием связующих материалов с высокой удельной прочностью. Усложняют и конструкцию стержней — устанавливают в них металлическую арматуру и выполняют специальные вентиляционные каналы. Это обеспечивает дополнительное упрочнение стержней и направленный отвод из них газов через знаковые части. Кроме того, стержни подвергают тепловой сушке.
Технология изготовления стержней с упрочнением тепловой сушкой вне оснастки имеет давнюю историю. Она универсальнее технологии изготовления стержней отверждением в нагретой и холодной оснастке, разработанной уже в XX веке, так как позволяет получать стержни любого класса сложности, любой массы и размеров. Недостатком этой технологии является продолжительный цикл изготовления, обусловленный необходимостью длительной тепловой сушки. Кроме того, стержни имеют меньшую размерную точность, так как могут деформироваться в процессе извлечения их из стержневых .ящиков, транспортирования в сыром состоянии и тепловой сушки. Для предотвращения деформирования и разрушения крупные стержни изготовляют из смесей с высокой прочностью в сыром состоянии.
ОПРЕДЕЛЕНИЕ ВЕЛИЧИНЫ ОБЪЕМНОЙ УСАДКИ СПЛАВА
Общие сведения
Плотность большей части металлов и сплавов при охлаждении возрастает, соответственно уменьшается удельный объем — величина, обратная плотности. В связи с этим наблюдается непрерывное уменьшение объема расплава, залитого в литейную форму, постепенно затвердевающей отливки и твердой отливки при изменении температуры от температуры заливки до нормальной. Если принять, что охлаждение заданной массы расплава в литейной форме происходит только по боковой и донной поверхностям, то изменение объема будет сопровождаться понижением уровня расплава в форме. Уровень расплава после образования твердой корки на поверхности будущей отливки до момента полной кристаллизации может понижаться только в глубинных слоях, где еще не началось затвердевание. Изменение объема в этот период проявляется в образовании концентрированных усадочных раковин и усадочных пор. Изменение объема, происходящее при охлаждении затвердевшей отливки, проявляется в уменьшении ее линейных размеров. Таким образом, общая объемная усадка металла складывается из усадки в жидком состоянии, усадки в процессе кристаллизации и усадки в твердом состоянии.
Количество раковин и пор (усадка в процессе кристаллизации) в отливках зависит от характера кристаллизации сплава, прежде всего интервала кристаллизации, и условий затвердевания.
Рассмотрим затвердевание отливки из сплава К, кристаллизующегося при постоянной температуре (рис. 46). Примем, что заполнение формы закончено до кристаллизации сплава в каком-либо месте отливки и что после заполнения добавочного количества сплава в форму не поступает, а охлаждение идет равномерно со всех сторон, кроме верха. Примем также, что объемная усадка в жидком и твердом состояниях пропорциональна температуре и что при кристаллизации объем сплава уменьшается.
В соответствии с распределением температуры по сечению отливки сплав будет затвердевать и его объем будет изменяться. В момент окончания заливки (кривая Г) форма полностью заполнена жидким сплавом /, Охлаждение сплава до температуры, распределение которой характеризуется кривой //, сопровождается уменьшением объема расплава, которое проявляется в понижении его уровня в форме. С этого момента начинается кристаллизация сплава. При достижении температуры, распределение которой характеризуется кривой ///, на поверхности отливки образуется твердый слой 3, а в центральной части сохраняется расплав. Уменьшение объема при переходе сплава из жидкого в твердое состояние обусловливает понижение уровня расплава. В отливке образуется усадочная раковина 2, размеры которой увеличиваются по мере охлаждения до полного затвердевания. При достижении распределения температуры, показанного кривой IV, отливка будет иметь окончательные размеры.
ГЛАВА 6. ПЛАВКА, РАФИНИРОВАНИЕ
И МОДИФИЦИРОВАНИЕ ЧУГУНА
В последние годы для плавки чугуна все более широкое применение находят индукционные печи. Основными преимуществами использования индукционной плавки являются следующие: расширение возможности получения высококачественных чугунов, обеспечение точного химического состава, низкого угара элементов, повышение однородности чугуна благодаря электродинамическому перемешиванию, обеспечение оптимальных условий модифицирования, использование более дешевых шихтовых материалов, улучшение условии труда в плавильных отделениях, уменьшение вредных выбросов в атмосферу.
В современных чугунолитейных цехах чаще всего применяют индукционные тигельные печи промышленной частоты. Высокая производительность печей и эффективное использование электроэнергии достигается при плавке на «болоте», когда после каждого выпуска жидкого металла в печи оставляют 30—40 % расплава и в него загружают соответствующее количество твердой шихты.
Надежная эксплуатация индукционных печей в значительной степени зависит от стойкости футеровки тигля, которая испытывает термические, химические и механические воздействия. Для изготовления тиглей применяют кислую сухую массу из молотых кварцитов или высококремнеземистых песков (более 97 % SiOa). Для спекания футеровки добавляют 1,5—2,0 % борной кислоты. При этом стойкость тигля для печей вместимостью 6—10 т составляет 250—300 плавок. В ряде случаев для изготовления тиглей используют нейтральные огнеупорные массы на основе дистенсиллиманита или муллитокорунда. Полагают, что несмотря на относительно высокую стоимость, они обеспечивают меньший угар легирующих элементов, высокую и надежную стойкость футеровки и снижение себестоимости жидкого чугуна. Высокоглиноземистая набивная футеровка состоит из 35—40 % электроплавленного корунда, 6O--65 % дистенсиллиманита и 1,0—1,5 % борной кислоты. На стойкость тигля влияют также технология подготовки, уплотнения и спекания футеровочной массы, сушки и условия эксплуатации тигля.
ВЛИЯНИЕ КАРБИДООБРАЗУЮЩИХ ЭЛЕМЕНТОВ НА СТРУКТУРУ БЕЛЫХ ИЗНОСОСТОЙКИХ ЧУГУНОВ
Общие сведения
Белые износостойкие чугуны представляют большую группу сложнолегированных сплавов на основе системы железо—хром—углерод. Они предназначены для изготовления деталей, подвергающихся в процессе эксплуатации интенсивному воздействию абразивных и коррозионно-абразивных сред. Разнообразна номенклатура отливок, получаемых из них: брони рудо-размалывающих мельниц, детали дробеметных и дробеструйных аппаратов, багерных и химических насосов и т. д.
Основным легирующим элементом износостойких чугунов является хром. Современные промышленные сплавы в зависимости от назначения содержат от 12 до 35 % Сг. Одна часть его присутствует в твердом растворе на основе железа, а другая связана в карбиды типа .Наличие в структуре твердых карбидов, прочно связанных с аустенитной или с аустенитно-мартенситной матрицей, придает сплавам высокую износостойкость, примерно в 5—15 раз большую, чем у сталей.
Улучшения некоторых свойств чугунов достигают введением целого ряда различных легирующих элементов. Например, для повышения прокаливаемости чугуны дополнительно легируют марганцем, молибденом, никелем, медью. Добавка этих же элементов повышает удароабразивную и коррозионную стойкость чугунов. Ванадий, ниобий, титан, цирконий, бор изменяют форму, размер и количество карбидов, способствуя одновременному улучшению как прочностных, так и пластических характеристик.
ПРОИЗВОДСТВО ОТЛИВОК
ИЗ СПЛАВОВ ЦВЕТНЫХ МЕТАЛЛОВ
ГЛАВА 8. ПЛАВКА, РАФИНИРОВАНИЕ
И МОДИФИЦИРОВАНИЕ СПЛАВОВ ЦВЕТНЫХ МЕТАЛЛОВ
Работа 35
СРАВНЕНИЕ ЭФФЕКТИВНОСТИ
РАЗЛИЧНЫХ МЕТОДОВ РАФИНИРОВАНИЯ
АЛЮМИНИЕВЫХ СПЛАВОВ
ОТ РАСТВОРЕННЫХ ГАЗОВ
И ТВЕРДЫХ НЕМЕТАЛЛИЧЕСКИХ ВКЛЮЧЕНИЙ
Общие сведения
Алюминиевые сплавы, применяемые в технике, делят на литейные и деформируемые. Первые из них предназначены для изготовления фасонных отливок, вторые — для производства полуфабрикатов (листов, лент, профилей, труб, штамповок и поковок) методами холодной или горячей обработки давлением. Основными компонентами алюминиевых сплавов являются кремний, медь, магний, марганец и цинк.
Для изготовления фасонных отливок в промышленности используют пять групп литейных алюминиевых сплавов:
I — сплавы на основе системы алюминий—кремний (АЛ2, АЛ4, АЛ9, АЛ34, АК7, АК9);
II — сплавы на основе системы алюминий—кремний—медь (АЛЗ, АЛ5, АЛ6, АЛ32, АК5М2, АК5М7, АК7М2, АК4М4);
III — сплавы на основе системы алюминий—медь (АЛ7, АЛ19, АЛЗЗ);
IV — сплавы на основе системы алюминий—магний (АЛ8, АЛ13, АЛ22, АЛ23, АЛ27, АЛ28);
V — сложнолегированные сплавы (АЛ1, АЛ11, АЛ21, АЛ25, АЛЗО).
Химический состав некоторых из литейных сплавов по ГОСТ 2685 — 75 приведен в табл.25.
Чаще других для изготовления отливок применяют сплавы системы алюминий—кремний (силумины). Сплавы этой системы обладают лучшими, по сравнению с другими сплавами, литейными свойствами — малой линейной усадкой, хорошей жидкотекучестью, не склонны к образованию трещин при затрудненной усадке. Отливки из силуминов получают литьем в песчаные и металлические формы.
ОЦЕНКА ЭФФЕКТИВНОСТИ РАЗЛИЧНЫХ СПОСОБОВ РАФИНИРОВАНИЯ МЕДНЫХ СПЛАВОВ ОТ НЕМЕТАЛЛИЧЕСКИХ ВКЛЮЧЕНИЙ
Общие сведении
Рафинирование медных расплавов осуществляют в целях снижения содержания газов и удаления взвешенных неметаллических включений. Дегазацию медных расплавов осуществляют продувкой инертными газами (аргон, азот), обработкой хлоридами и флюсами, вакуумированием. Эти же способы, наряду с фильтрованием, применяют и для очистки расплавов от взвешенных неметаллических включений. Поскольку большая часть рафинирующих средств в той или иной мере гигроскопична, необходимым условием их применения является предварительная сушка или переплавка.
Рафинирование инертными газами ведут при температуре расплава 1150—1200 QC, расход газа 0,25—0,5 м3 на 1 т расплава, длительность продувки при давлении газа 19,6—29,4 кПа составляет 5—10 мин.
Хлористый марганец вводят в количестве 0,1—0,2 % массы расплава при 1150—1200 °С с помощью колокольчика. Для удалении пузырьков рафинирующего газа расплав перед разливкой выдерживают в течение 10—15 мин.
Вакуумирование применяют в тех случаях, когда сплав не содержит компонентов с высоким давлением пара. Применительно к медным сплавам этот процесс ведут при 1150—1300 С и остаточном давлении 0,6—1,3 кПа. Длительность вакуумирования определяется массой расплава, подвергающегося обработке, и вы* сотой столба жидкого металла. В большинстве случаев продолжительность вакуумирования не превышает 25 мин.
Обработку расплавов флюсами (табл. 36) применяют в основном для очистки от взвешенных неметаллических включений.
ПОЛУЧЕНИЕ СЛИТКОВ ЛИТЬЕМ В ИЗЛОЖНИЦЫ Общие сведении
Для 'получения слитков этим способом применяют водоохлаждаемые и неводоохлаждаемые изложницы. Водоохлаждаемые изложницы используют при получении крупных слитков, а неводоохлажднемые для изготовления слитков небольших размеров (диаметр до 200, толщина ДО 50, длина до 500 мм).
Слитки круглого сечения получают заполнением вертикальных разъемных и неразъемных изложниц, для получения плоских слитков применяют как вертикальные, так и горизонтальные изложницы. Неводоохлаждаемые изложницы изготовляют из чугуна, реже из стали, в лабораторных условиях применяют медные, графитовые и бронзовые наложницы.
Изложницы заполняют металлом сверху, реже используют сифонную заливку. Для регулирования скорости заполнения изложницы при заливке сверху применяют литниковые воронки, представляющие собой чугунный кожух, футерованный огнеупорным материалом, часто для этой цели используют графитошамотные тигли. В дне воронок устраивают необходимое число отверстий, в которые перед заливкой устанавливают графитовые или шамотные втулки с отверстием определенного диаметра. Воронки располагают на изложнице или над нею.
И СТЕРЖНЕВЫХ СМЕСЕЙ
Общие сведения
Для изготовления разовых форм применяют единые, облицовочные и наполнительные формовочные смеси. Единые смеси, как правило, используют для формовки по-сырому, т. е. когда заливка металла производится во влажные формы. Облицовочные смеси служат для выполнения поверхности формы, непосредственно контактирующей с металлом. Их применяют при изготовлении средних и крупных форм, которые подвергают сушке или поверхностной подсушке. Облицовочную смесь наносят на модель слоем 50—60 мм, остальной объем опоки заполняют наполнительной смесью. Очень часто в качестве облицовочных смесей крупных форм используют самотвердеющие смеси, позволяющие исключить операцию сушки. В настоящее время для изготовления стержней и малогабаритных форм применяют песчаносмоляные смеси, отвердевающие в холодной или нагреваемой оснастке.
Обладая низкой вязкостью, смолы равномерно распределяются по объему смеси, обеспечивая высокие технологические и прочностные свойства. Использование таких смесей позволяет автоматизировать процессы изготовления стержней, повысить их размерную точность, уменьшить площади стержневых отделений за счет ликвидации операции сушки. Осуществление этих процессов требует применения обогащенных кварцевых песков, в которых содержание глинистых составляющих не превышает 0,5 %, а также меньшего количества минералогических примесей, чем это допускается ГОСТ 2138—84. Увеличение содержания глины свыше 0,5 % потребует для сохранения физико-механических свойств смесей повышенного расхода связующего и отвердителя, что увеличит стоимость смеси и ухудшит санитарно-гигиениче¬ские условия труда. Примеси в песках могут вступать во взаимодействие с компонентами связующего и отвердителя, что вызовет ухудшение технологических свойств смесей. Поэтому для приготовления песчано-смоляных смесей рекомендуется использовать пески марок О61К02 и О61К016. Типовые составы формовочных и стержневых смесей приведены в прилож. 1.
В литейных цехах контроль качества формовочных и стержневых смесей сводится к определению следующих физико-механических характеристик: содержание глинистой составляющей, влажность, газопроницаемость, предел прочности при сжатии во влажном и сухом состояниях, предел прочности при растяжении, а иногда при срезе и изгибе. Кроме того, при разработке новых составов смесей определяют газотворность, осыпаемость, поверхностную твердость, долговечность, текучесть, выбиваемость и живучесть.
Влажность. Под влажностью формовочной смеси понимается содержание в ней свободной и гигроскопической влаги, выраженное в процентах к массе смеси. Содержание влаги в смесях определяется нормальным или ускоренным методом.
Нормальный метод. Навеску 50 dt 0,01 г исследуемой смеси помещают в предварительно высушенные и взвешенные фарфоровые чашки и переносят в сушильную печь. Температура в печи должна быть 105—100 °С. По истечении 30 мин чашку с навеской вынимают из печи и взвешивают, затем опять помещают в печь. Каждое последующее взвешивание производят после высушивания в течение 15 мин до постоянной массы. После этого чашки с навеской помещают в эксикатор, где охлаждают до нормальной температуры. Охлажденную навеску взвешивают.
ИЗГОТОВЛЕНИЕ СТЕРЖНЕЙ
С УПРОЧНЕНИЕМ ТЕПЛОВОЙ СУШКОЙ
Общие сведения
Стержни являются элементами литейных форм. Их применяют для выполнения в отливках внутренних полостей и отверстий. С помощью стержней частично или полностью формируют и наружные поверхности отливок. Стержень состоит из рабочей и знаковой частей. Рабочая часть непосредственно контактирует с металлом и формирует требуемую геометрию полостей, отверстий и наружных поверхностей отливки. Знаковая часть стержня не контактирует с заливаемым в форму жидким металлом. Она обеспечивает фиксацию стержня в литейной форме. Знаковая часть стержня опирается на знаковую часть формы. Ее прочность должна быть достаточной, чтобы выдерживать нагрузку, обусловленную собственным весом стержня и давлением жидкого металла на стержень. Через знаки также удаляются газы, образующиеся в стержне под тепловым воздействием металла.
К стержням предъявляют более высокие, чем к формам, требования по огнеупорности, газопроницаемости, термохимической устойчивости, прочности, податливости, выбиваемости, газо-творности и осыпаемости. Обеспечить выполнение всех этих требований очень трудно, но к этому нужно стремиться. Для этого стержни, как правило, изготовляют из кондиционных свежих формовочных песков с использованием связующих материалов с высокой удельной прочностью. Усложняют и конструкцию стержней — устанавливают в них металлическую арматуру и выполняют специальные вентиляционные каналы. Это обеспечивает дополнительное упрочнение стержней и направленный отвод из них газов через знаковые части. Кроме того, стержни подвергают тепловой сушке.
Технология изготовления стержней с упрочнением тепловой сушкой вне оснастки имеет давнюю историю. Она универсальнее технологии изготовления стержней отверждением в нагретой и холодной оснастке, разработанной уже в XX веке, так как позволяет получать стержни любого класса сложности, любой массы и размеров. Недостатком этой технологии является продолжиельный цикл изготовления, обусловленный необходимостью длительной тепловой сушки. Кроме того, стержни имеют меньшую размерную точность, так как могут деформироваться в процессе извлечения их из стержневых .ящиков, транспортирования в сыром состоянии и тепловой сушки. Для предотвращения деформирования и разрушения крупные стержни изготовляют из смесей с высокой прочностью в сыром состоянии.
ОПРЕДЕЛЕНИЕ ВЕЛИЧИНЫ ОБЪЕМНОЙ УСАДКИ СПЛАВА
Общие сведения
Плотность большей части металлов и сплавов при охлаждении возрастает, соответственно уменьшается удельный объем — величина, обратная плотности. В связи с этим наблюдается непрерывное уменьшение объема расплава, залитого в литейную форму, постепенно затвердевающей отливки и твердой отливки при изменении температуры от температуры заливки до нормальной. Если принять, что охлаждение заданной массы расплава в литейной форме происходит только по боковой и донной поверхностям, то изменение объема будет сопровождаться понижением уровня расплава в форме. Уровень расплава после образования твердой корки на поверхности будущей отливки до момента полной кристаллизации может понижаться только в глубинных слоях, где еще не началось затвердевание. Изменение объема в этот период проявляется в образовании концентрированных усадочных раковин и усадочных пор. Изменение объема, происходящее при охлаждении затвердевшей отливки, проявляется в уменьшении ее линейных размеров. Таким образом, общая объемная усадка металла складывается из усадки в жидком состоянии, усадки в процессе кристаллизации и усадки в твердом состоянии.
Количество раковин и пор (усадка в процессе кристаллизации) в отливках зависит от характера кристаллизации сплава, прежде всего интервала кристаллизации, и условий затвердевания.
Рассмотрим затвердевание отливки из сплава К, кристаллизующегося при постоянной температуре (рис. 46). Примем, что заполнение формы закончено до кристаллизации сплава в каком-либо месте отливки и что после заполнения добавочного количества сплава в форму не поступает, а охлаждение идет равномерно со всех сторон, кроме верха. Примем также, что объемная усадка в жидком и твердом состояниях пропорциональна температуре и что при кристаллизации объем сплава уменьшается.
В соответствии с распределением температуры по сечению отливки сплав будет затвердевать и его объем будет изменяться. В момент окончания заливки (кривая Г) форма полностью заполнена жидким сплавом /, Охлаждение сплава до температуры, распределение которой характеризуется кривой //, сопровождается уменьшением объема расплава, которое проявляется в понижении его уровня в форме. С этого момента начинается кристаллизация сплава. При достижении температуры, распределение которой характеризуется кривой ///, на поверхности отливки образуется твердый слой 3, а в центральной части сохраняется расплав. Уменьшение объема при переходе сплава из жидкого в твердое состояние обусловливает понижение уровня расплава. В отливке образуется усадочная раковина 2, размеры которой увеличиваются по мере охлаждения до полного затвердевания. При достижении распределения температуры, показанного кривой IV, отливка будет иметь окончательные размеры.
ГЛАВА 6. ПЛАВКА, РАФИНИРОВАНИЕ
И МОДИФИЦИРОВАНИЕ ЧУГУНА
В последние годы для плавки чугуна все более широкое применение находят индукционные печи. Основными преимуществами использования индукционной плавки являются следующие: расширение возможности получения высококачественных чугунов, обеспечение точного химического состава, низкого угара элементов, повышение однородности чугуна благодаря электродинамическому перемешиванию, обеспечение оптимальных условий модифицирования, использование более дешевых шихтовых материалов, улучшение условии труда в плавильных отделе¬ниях, уменьшение вредных выбросов в атмосферу.
В современных чугунолитейных цехах чаще всего применяют индукционные тигельные печи промышленной частоты. Высокая производительность печей и эффективное использование электроэнергии достигается при плавке на «болоте», когда после каждого выпуска жидкого металла в печи оставляют 30—40 % расплава и в него загружают соответствующее количество твердой шихты.
Надежная эксплуатация индукционных печей в значительной степени зависит от стойкости футеровки тигля, которая испытывает термические, химические и механические воздействия. Для изготовления тиглей применяют кислую сухую массу из молотых кварцитов или высококремнеземистых песков (более 97 % SiOa). Для спекания футеровки добавляют 1,5—2,0 % борной кислоты. При этом стойкость тигля для печей вместимостью 6—10 т составляет 250—300 плавок. В ряде случаев для изготовления тиглей используют нейтральные огнеупорные массы на основе дистенсиллиманита или муллитокорунда. Полагают, что несмотря на относительно высокую стоимость, они обеспечивают меньший угар легирующих элементов, высокую и надежную стойкость футеровки и снижение себестоимости жидкого чугуна. Высокоглиноземистая набивная футеровка состоит из 35—40 % электроплавленого корунда, 6O--65 % дистенсиллиманита и 1,0—1,5 % борной кислоты. На стойкость тигля влияют также технология подготовки, уплотнения и спекания футеровочной массы, сушки и условия эксплуатации тигля.
ВЛИЯНИЕ КАРБИДООБРАЗУЮЩИХ ЭЛЕМЕНТОВ НА СТРУКТУРУ БЕЛЫХ ИЗНОСОСТОЙКИХ ЧУГУНОВ
Общие сведения
Белые износостойкие чугуны представляют большую группу сложнолегированных сплавов на основе системы железо—хром—углерод. Они предназначены для изготовления деталей, подвергающихся в процессе эксплуатации интенсивному воздействию абразивных и коррозионно-абразивных сред. Разнообразна номенклатура отливок, получаемых из них: брони рудо-размалывающих мельниц, детали дробеметных и дробеструйных аппаратов, багерных и химических насосов и т. д.
Основным легирующим элементом износостойких чугунов является хром. Современные промышленные сплавы в зависимости от назначения содержат от 12 до 35 % Сг. Одна часть его присутствует в твердом растворе на основе железа, а другая связана в карбиды типа .Наличие в структуре твердых карбидов, прочно связанных с аустенитной или с аустенитно-мартенситной матрицей, придает сплавам высокую износостойкость, примерно в 5—15 раз большую, чем у сталей.
Улучшения некоторых свойств чугунов достигают введением целого ряда различных легирующих элементов. Например, для повышения прокаливаемости чугуны дополнительно легируют марганцем, молибденом, никелем, медью. Добавка этих же элементов повышает удароабразивную и коррозионную стойкость чугунов. Ванадий, ниобий, титан, цирконий, бор изменяют форму, размер и количество карбидов, способствуя одновременному улучшению как прочностных, так и пластических характеристик.
ПРОИЗВОДСТВО ОТЛИВОК
ИЗ СПЛАВОВ ЦВЕТНЫХ МЕТАЛЛОВ
ГЛАВА 8. ПЛАВКА, РАФИНИРОВАНИЕ
И МОДИФИЦИРОВАНИЕ СПЛАВОВ ЦВЕТНЫХ МЕТАЛЛОВ
Работа 35
СРАВНЕНИЕ ЭФФЕКТИВНОСТИ
РАЗЛИЧНЫХ МЕТОДОВ РАФИНИРОВАНИЯ
АЛЮМИНИЕВЫХ СПЛАВОВ
ОТ РАСТВОРЕННЫХ ГАЗОВ
И ТВЕРДЫХ НЕМЕТАЛЛИЧЕСКИХ ВКЛЮЧЕНИЙ
Общие сведения
Алюминиевые сплавы, применяемые в технике, делят на литейные и деформируемые. Первые из них предназна¬чены для изготовления фасонных отливок, вторые — для производства полуфабрикатов (листов, лент, профилей, труб, штампо¬вок и поковок) методами холодной или горячей обработки давлением. Основными компонентами алюминиевых сплавов являются кремний, медь, магний, марганец и цинк.
Для изготовления фасонных отливок в промышленности используют пять групп литейных алюминиевых сплавов:
I — сплавы на основе системы алюминий—кремний (АЛ2, АЛ4, АЛ9, АЛ34, АК7, АК9);
II — сплавы на основе системы алюминий—кремний—медь (АЛЗ, АЛ5, АЛ6, АЛ32, АК5М2, АК5М7, АК7М2, АК4М4);
III — сплавы на основе системы алюминий—медь (АЛ7, АЛ19, АЛЗЗ);
IV — сплавы на основе системы алюминий—магний (АЛ8, АЛ13, АЛ22, АЛ23, АЛ27, АЛ28);
V — сложнолегированные сплавы (АЛ1, АЛ11, АЛ21, АЛ25, АЛЗО).
Химический состав некоторых из литейных сплавов по ГОСТ 2685 — 75 приведен в табл.25.
Чаще других для изготовления отливок применяют сплавы системы алюминий—кремний (силумины). Сплавы этой системы обладают лучшими, по сравнению с другими сплавами, литейными свойствами — малой линейной усадкой, хорошей жидкотекучестью, не склонны к образованию трещин при затрудненной усадке. Отливки из силуминов получают литьем в песчаные и металлические формы.
ОЦЕНКА ЭФФЕКТИВНОСТИ РАЗЛИЧНЫХ СПОСОБОВ РАФИНИРОВАНИЯ МЕДНЫХ СПЛАВОВ ОТ НЕМЕТАЛЛИЧЕСКИХ ВКЛЮЧЕНИЙ
Общие сведении
Рафинирование медных расплавов осуществляют в целях снижения содержания газов и удаления взвешенных неметаллических включений. Дегазацию медных расплавов осуществляют продувкой инертными газами (аргон, азот), обработкой хлоридами и флюсами, вакуумированием. Эти же способы, наряду с фильтрованием, применяют и для очистки расплавов от взвешенных неметаллических включений. Поскольку большая часть рафинирующих средств в той или иной мере гигроскопична, необходимым условием их применения является предварительная сушка или переплавка.
Рафинирование инертными газами ведут при температуре расплава 1150—1200 QC, расход газа 0,25—0,5 м3 на 1 т расплава, длительность продувки при давлении газа 19,6—29,4 кПа составляет 5—10 мин.
Хлористый марганец вводят в количестве 0,1—0,2 % массы расплава при 1150—1200 °С с помощью колокольчика. Для удалении пузырьков рафинирующего газа расплав перед разливкой выдерживают в течение 10—15 мин.
Вакуумирование применяют в тех случаях, когда сплав не содержит компонентов с высоким давлением пара. Применительно к медным сплавам этот процесс ведут при 1150—1300 С и остаточном давлении 0,6—1,3 кПа. Длительность вакуумирования определяется массой расплава, подвергающегося обработке, и вы* сотой столба жидкого металла. В большинстве случаев продолжительность вакуумирования не превышает 25 мин.
Обработку расплавов флюсами (табл. 36) применяют в основном для очистки от взвешенных неметаллических включений.
ПОЛУЧЕНИЕ СЛИТКОВ ЛИТЬЕМ В ИЗЛОЖНИЦЫ Общие сведении
Для 'получения слитков этим способом применяют водоохлаждаемые и неводоохлаждаемые изложницы. Водоохлаждаемые изложницы используют при получении крупных слитков, а неводоохлажднемые для изготовления слитков небольших размеров (диаметр до 200, толщина ДО 50, длина до 500 мм).
Слитки круглого сечения получают заполнением вертикальных разъемных и неразъемных изложниц, для получения плоских слитков применяют как вертикальные, так и горизонтальные изложницы. Неводоохлаждаемые изложницы изготовляют из чугуна, реже из стали, в лабораторных условиях применяют медные, графитовые и бронзовые наложницы.
Изложницы заполняют металлом сверху, реже используют сифонную заливку. Для регулирования скорости заполнения изложницы при заливке сверху применяют литниковые воронки, представляющие собой чугунный кожух, футерованный огнеупорным материалом, часто для этой цели используют графитошамотные тигли. В дне воронок устраивают необходимое число отверстий, в которые перед заливкой устанавливают графитовые или шамотные втулки с отверстием определенного диаметра. Воронки располагают на изложнице или над нею.