Справочник теплоэнергетика предприятий цветной металлургии
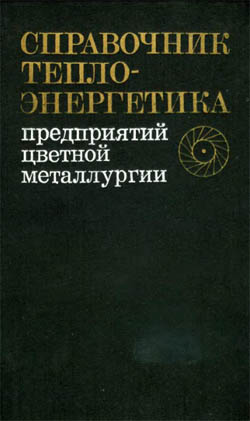
Под ред. О. Н, Багрова, 3. Л. Берлина
Металлургия, 1982 г.
1, Агломерационные машины
Агломерационные машины являются наиболее производительным оборудованием для окусковывания (спекания) рудной шихты в черной и цветнойметаллургии [1, с. 387—395]. В цветнойметаллургииспекание сопровождается выжиганием из шихты серы. Поэтому спекание с одновременной десульфуризацией рудной шихты называют агломерирующим обжигом.
В цветнойметаллургииработают агломерационные машиныплощадью 50 и 75 м2. В Советском Союзе в 1964 г. пущена машинаплощадью 312 м2, созданная на Уралмашзаводе. Характеристики выпускаемых отечественной промышленностью агломерационных машин приведены в табл. 11.1.
В последние годы за рубежом введены в строй машиныплощадью 500 м2 с тележкамишириной 5 м; длина машины 100 м. На Уралмашзаводе создается агломерационная машинаплощадью 600 м2, шириной 6 и длиной 100 м.
На отечественных предприятиях цветнойметаллургииработают агломерационные машины двух видов: с прососом воздуха сверху вниз через слой шихты и с продувом шихты воздухом снизу вверх (рис. 11.1).
Основой агломерационной машины является каркас и укрепленный на нем замкнутый рельсовый путь, верхняя (рабочая) ветвь которого горизонтальна, нижняя (холостая) — наклонна. Головная, и загрузочная части рельсового пути образованы дугами окружностей. спеканиеагломерата происходит на колосниковой решетке, состоящей из колосников, расположенных на отдельных спекательных тележках (паллетах), механически не соединенных между собой, но передвигающихся по рабочей ветви от головной части к разгрузочной вплотную одна за другой под воздействием усилия толкания приводных звездочек.
Спекательная тележка (рис. 11.2) представляет собой прямоугольный стальной литой корпус, опирающийся на четыре ходовых ролика. Боковые стороны паллеты ограничены съемными бортами. Между ребрами корпуса поверхность выложена из колосников. В начале рабочей ветви на колосники загружается питателями тонкий
(до 20 мм) слой постели, закрывающий щели между колосниками, затем основная шихта слоем до 350 мм. После этого паллетыпроходят под зажигательным горном S (см. рис. 11.1), где начинается процесс спекания. Через слой шихты просасывается или продувается воздух, для этого используются камеры рабочей ветви и тяго-дутьевые средства. В момент окончания спекания всего слоя шихтыпаллеты подходят к разгрузочной части, переворачиваются колосниками вниз и спекшаяся шихта (агломерат) разгружается с паллет. По холостой ветви паллеты движутся под действием собственной массы. В головной части приводные звездочки поднимают паллеты, захватывая за специальные кулачки на корпусах, и перемещают на рабочую ветвь, по которой и проталкивают их.
При работеагломашины с прососами воздуха до 50—60% производительностиэксгаустера расходуется на вредные прососы воздуха, который не участвует в процессе спекания. Поэтому конструкции и состояниюуплотнений зазоров между паллетами и вакуум-камерами уделяется повышенное внимание.
Агломерационные машины имеют гидравлическое уплотнительное устройство (одно-или двухрукавное). Это устройство не обеспечивает надежного уплотнения при длительной работе. В Чехословакии используют пластинчатое пружинное уплотнение (рис. 11.3), которое стали применять и на отечественных аглофабриках. Материалом пружин служит сталь 65Г толщиной 0,5— 0,75 мм. Целесообразно применять и другие пружинные стали, сохраняющие упругость при длительной работе в условиях повышенной температуры: хромованадиевую 50ХФА и вольфрамокремниевую 65С2ВА.
В дутьевых агломашинах (см. рис. 11.1) применено жесткое шинное уплотнение, на которое полностью передается весовая нагрузкашихты и паллет. В этом случае рабочая ветвь машины не имеет ходовых рельсов, паллеты скользят по уплотнительным шинам. При таком старом способе хотя и требуется повышенный расход энергии, в значительной степени изнашиваются детали и необходима надежная смазка, но обеспечивается надежное уплотнение. Конструкции с упругим резинометаллическим рельсом, рассчитанные на передачу жесткому уплотнению ¼ части весовой нагрузки, себя не зарекомендовали.
Зарубежные и отечественные машиныплощадью 75—100 м2 имеют в разгрузочной части звездочки для устранения взаимных ударов паллет торцами. Звездочки могут быть неприводными и приводными. Электродвигатель привода звездочек разгрузочной части работает в режиме торможения, удерживая паллеты от падения в
момент входа на направляющие разгрузочной части.
Для загрузки постели и двухслойной шихты применяют три самостоятельных питателя, что улучшает показателипроцесса агломерации. Такие же раздельные питатели устанавливают и на дутьевых машинах для загрузки постели, слоя зажигания и основного слоя.
Отражательные печи
На заводах цветнойметаллургии применяют отражательную плавку сырой (подсушенной) и обожженной шихты. Выбор способаплавки зависит от состава перерабатываемых материалов и прежде всего от содержания меди в шихте. Если при плавке необожженной шихтыштейны содержат <20% Си, то применяют предварительный обжиг шихты.
В составшихты отражательной плавки входят сульфиды и окислы металлов, породообразующие компоненты, силикаты, карбонаты и другие соединения.
Физико-химические изменения шихты при плавкесвязаны с действием высоких температур и химическим взаимодействием между твердыми и жидкими продуктами процесса, В нейтральной или слабоокислительной атмосфере в рабочем пространстве печи роль печных газов в химизмепроцесса незначительна. Высокая температура газов, достигающая в плавильной зоне 1550—1600 °С, а в конце печи 1250— 1300 °С, создает благоприятные условия для диссоциации высших сульфидов, окислов, сульфатов и карбонатов. Реакция диссоциации протекает в основном на откосах печи; там же начинается по мере прогрева шихты взаимодействие между твердыми веществами процесса; оно продолжается и заканчивается в жидкой ванне печи.
Цель отражательной плавки — сульфидирование меди и перевод ее в штейн при одновременном ошлаковании большей части железа. Для отопления отражательных печей используют угольную пыль, мазут, природный газ с подсветкой или без подсветки мазутом.
Отражательные печи широко применяются при рафинирований меди. Полученную после конвертирования черновую медь подвергают огневому рафинированию. Цель его — удаление примесей и получение плотных анодов для процесса электролитического рафинирования меди. процесс огневого рафинирования состоит из следующих операций: загрузки черновой меди, расплавления, окисления примесей, скачивания шлака, восстановления (включая дразнение) меди и разливки. Этот процесс зависит от целого ряда факторов — емкости печи, тепловой нагрузки, производительности загрузочных и разливочных устройств и продолжается 16—24 ч.
Огневое рафинирование черновой меди от примесей основано на различном сродстве металлов к кислороду и малой растворимости большинства окислов примесей в жидкой меди. По сродству к кислороду при 1200°С примеси можно расположить в следующем порядке: цинк, железо, олово, мышьяк, никель, сурьма, свинец, висмут, сера, медь, теллур, селен, серебро, золото. Первые девять элементов имеют большее сродство к кислороду, чем медь.
ВЕЛЬЦ -ПЕЧИ
Общие сведения
Вельцевание — широко применяемый процесс переработки полиметаллических отходов металлургического производства: шлаков свинцового, медного и оловянного производства, твердых остатков цинкового производства (раймовки, кеков) и др. с целью дополнительного извлечения ценных металлов. Перерабатываемые продукты смешивают с измельченным углеродистым топливом — восстановителем (коксик, антрацит и др.), являющимся главным источником тепла в процессе, и подвергают нагреву до 1200—1300 °С во вращающейся горизонтальной трубчатой печи (вельц-печи). При этом расходуглерода на восстановительные процессы составляет примерно 45—50 % общего его количества в шихте; остальной углерод сгорает с кислородом печных газов и создает тепло для нагрева шихты. Кроме того, избыток коксика используется для поддержания необходимой ее консистенции [1—5]-
Печи имеют длину 40—90 м, диаметр 2,5—3,5 м. Устанавливают их с уклоном 3—5 град для обеспечения транспортировки материала; скорость вращения 1— 2 об/мин. Движение газов и материала в печи противоточное; продолжительность пребывания материала в печи 2—3 ч.
Вельц-печь условно можно разделить на три зоны: подготовительную, реакционную и формирования клинкера.
В зависимости от вида сырья вельц-печь может работать полностью только за счет горючего шихты, или ее дополнительно подтапливают непрерывно или периодически. В качестве топлива для подтопки применяют горючие газы (природный, газогенераторный), жидкое или пылеугольное топливо. Для улучшения тепловой работы вельц-печей целесообразно равномерно распределять принудительное дутье по длине реакционной зоны, использовать природный газ или другое топливо с целью замены части твердого топлива-восстановителя, а также шихту и огнеупоры улучшенного качества.
ОГНЕУПОРЫ
1. Общие сведения
Огнеупорными называют материалы, изготовленные па основе минерального сырья и отличающиеся способностью сохранять без существенных нарушений функциональные свойства в разнообразных условиях службы при высоких температурах.
В промышленной практике огнеупоры используют для футеровки тепловых агрегатов, в которых обработкаматериаловсвязана с высокими температурами. Так как в цветнойметаллургии перерабатывается много разнообразных материалов, а следовательно, используется много видов тепловых агрегатов, которые существенно отличаются условиями службы (температура, газовая среда, составшлаков и т.д.), необходимо применение разных видов огнеупорных материалов. К ним относятся алюмосиликатные (низко-, средне- и высокоглиноземистые) , основные (магнезитовые, хромомагнезитовые, магнезитохроми-товыс, периклазошпннелидные и др.), дина-совые, огнеупорные бетоны и набивные массы, спеченные металлургические порошки, мертели и др. В связи с интенсификацией металлургических процессов в настоящее время происходит существенное изменение в балансе потребляемых отраслью огнеупоров. Наряду с традиционными огнеупорными материалами все шире используются новые износоустойчивые виды изделий, например карборундовые, корундовые, цирконсодержцщие, огнеупоры из чистых окислов и др.
Большое значение отводится огнеупорам в области экономии топливно-энергетических ресурсов. Известно, что 20—25 % всего тепла, выделяемого при горении топлива, теряется через ограждение тепловых агрегатов. Поэтому для экономии топлива и снижения потерь тепла широко применяют различные огнеупорные и высокоогнеупорные теплоизоляционные материалы, называемые легковесными.
Классификация огнеупорных материалов. По принятой классификации [1], огнеупорныеизделия подразделяют по следующим основным признакам: химико-минералогическому составу, огнеупорности, пористости, способу формования, термической обработке, форме и размерам.