Высокочастотная сварка металлов
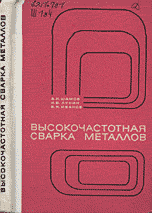
Шамов А.Н.
Металлургия, Array г.
ТЕОРЕТИЧЕСКИЕ ОСНОВЫ ВЫСОКОЧАСТОТНОЙ СВАРКИ Впервые идея применения токов высокой частоты (т. в. ч.) для сваркиметаллов была предложена в 1946 г. советскими специалистами во главе с А. В. Улитовским. В 50-е годы в Советском Союзе и за рубежом начались интенсивные исследования по созданию технологии и оборудования для высокочастотной сварки труб, а несколько позже и для оболочек кабеля и профилей. Был создан способ промышленного применения высокочастотной сварки, при котором изделие перед сварочным узлом формуется в виде заготовки с V-образной щелью между свариваемыми кромками. К кромкам посредством скользящих контактов или индуктором подводится т. в. ч. таким образом, чтобы он проходил от одной кромки к другой через место их схождения. Вследствие поверхностного эффекта и эффекта близости, который по мере сближения кромок усиливается, достигается высокая концентрация тока в месте схождения кромок. Благоприятное распределение тока, высокая степень концентрации мощности обеспечивают возможность ведения процесса с оплавлением тонкого слоя на поверхности свариваемых кромок и получение прочного качественного сварного соединения. Нагретые кромкиизделия обжимаются с помощью валков и свариваются. Качество сварного соединения и расходэлектроэнергии тесным образом связаны с особенностями протекания т. в. ч. по проводникам. 1. Законы и явления, лежащие в основе процесса высокочастотной сварки Высокочастотная сваркаметаллов основана на использовании законов электромагнитнойиндукции и полного тока, а также следующих явлений: поверхностного эффекта, эффекта близости, кольцевого или катушечного эффекта, влияния магнитопроводов и медных экранов на распределение тока в проводнике, изменения свойствметаллов при изменении температуры и напряженности магнитного поля, возникновения электромагнитных сил [4, 6, 21, 22, 35, 391. Эти законы и явления необходимо учитывать при выборе параметров процесса и конструировании устройств для передачи сварочного тока к изделиям. 4. Механизмпроцесса высокочастотной сварки Исходя из современных представлений о сварке металлов, процессы высокочастотной сварки можно разделить па три группы. 1. сваркадавлением с оплавлением. Осуществляется при предварительном нагреве и местном расплавлении свариваемых поверхностей. Расплавленный металл удаляется из зоны соединения при осадке; сварное соединение образуется между поверхностями, находящимися в твердом состоянии. Скорость нагрева достигает 150-103 °С/с; осадка — 0,15—1,5 мм; Скоростьосадки — 2000 мм/с. 2. сваркадавлением без оплавления. Осуществляется с предварительным нагревом свариваемых поверхностей до температуры ниже точкиплавления свариваемого металла. Скорость нагрева не превышает 400 °С/с; осадка — 2,5—6,0 мм; Скоростьосадки — 20 мм/с. 3. сваркаплавлением без давления. Осуществляется при нагреве свариваемых элементов до оплавления. Ванна расплавленного металла застывает, образуя сварной шов без приложения давления. Скорость нагрева доходит до 8000 °С/с. сваркадавлением с оплавлением. Этот процесс наиболее широко распространен при производстве сварных изделий и полуфабрикатов с непрерывным швом из черных и цветных металлов. Схема свариваемых элементов представлена на рис. 7 и 8. Свариваемые элементы, показанные на рис. 8, а, имеют одинаковые геометрические размеры и материал и расположены симметрично относительно вертикальной плоскости. При симметричном подводе тока к свариваемым элементам обеспечивается полная идентичность нагрева. Такую схему будем называть симметричной. Когда свариваемые элементы имеют неодинаковую геометрию (рис. 8, б), даже при симметричном подводе тока к элементам плотность тока на них неодинакова. Различны и условия теплоотвода. Обеспечить одинаковый нагрев обоих элементов без принятия специальных мер невозможно. Такую схему будем называть несимметричной. При сварке элементов с различными теплофизическими свойствами схема, приведенная на рис. 8, а, будет также несимметричной. Выбор оптимальных параметров сварочных устройств. Свариваемый сортамент труб ограничивается отношением D/2d. Максимальное значение D/2d определяется условиемустойчивости заготовки данного диаметра при осадке с оптимальным давлением, т. е. тонкостенность свариваемой трубной заготовки зависит от свариваемого диаметра и материала заготовки (табл. 28). Максимальное значение толщины стенки при заданном диаметретрубы определяется допустимыми электрическими потерями в ее теле, а при очень малых соотношениях — и возможностями процесса формовки. Как было показано в гл. I, сварка труб, толщина которых определяется отношением D/2d (табл. 28), может быть осуществлена в широком диапазоне частот тока. Поэтому решающим фактором является простота и надежность конструкции системыпередачи тока, зависящей в значительной степени от пропускаемого тока. Чем выше частота и длительнее время нагрева, тем меньше ток (рис. 82). Снижение сварочного тока за счет увеличения времени нагрева нецелесообразно, так как при этом увеличиваются тепловые потери вследствие отвода тепла в тело свариваемой заготовки. Наиболее эффективно уменьшение тока за счет повышения частоты до 200—500 кГц. Дальнейшее повышение частоты, как правило, нежелательно, так как заметного уменьшения тока это на дает и ухудшаются показатели источников питания сварочных устройств. Поэтому с учетом выделенного в СССР льготного диапазона частот для высокочастотной сваркитруб малого и среднего диаметров принята частота 440 кГц, хотя в отдельных случаях применяются частоты 70 и 10 кГц. За рубежом для сварки таких труб применяют частоты 170—500 кГц [18]. Наименьший расходэлектроэнергии при индукционном подводе тока с помощью охватывающего индуктора наблюдается при сваркетрубдиаметром 35—45 мм. Если принять мощность, потребляемую при сваркетрубдиаметром 35—45 мм за единицу, то отношение этой мощности к мощности, необходимой для сваркитрубы другого диаметра, даст коэффициент изменения мощности kM. Необходимо заметить, что при контактной системеподвода тока значение приведенной мощности для сваркитрубдиаметром 35—45 мм примерно такое же, как при индукционном подводе, и практически не меняется с изменением диаметра трубы. Поэтому при сваркетруб малого диаметра следует рекомендовать только систему индукционного подвода тока. С ростом диаметра свариваемой заготовки значительно увеличивается потребляемая мощность, и при диаметре заготовки 220 мм она удваивается по сравнению с мощностью, необходимой для сваркитрубдиаметром 35—45 мм. Однако экономичность процесса определяется не только энергетическими показателями. В табл. 29 приведены значения скорости, приведенной мощности и частоты тока при различных способахподвода тока для высокочастотной сваркитрубдиаметром 159— 220 мм. Из таблицы видно, что при сваркетрубдиаметром 159 и 168 мм потребляемые мощности при контактном способе с помощью вращающихся контактов и индукционном практически одинаковы, а по данным фирмы «Терматул», для трубдиаметром 168 мм можно уменьшить эту мощность на 10—12%, если применить скользящие контакты. Лишь при сваркетрубдиаметром 219 мм разница в мощностях становится ощутимой Помимо возможности иметь меньшую длину нагреваемых кромок и меньший расход мощности, система с контактным подводом тока удобна при перестройке стана, связанной с переходом с одного диаметратруб на другой. В то же время этой системе присущи следующие недостатки. 1. Необходимость симметричной передачи тока к свариваемым кромкам посредством контактов, симметрично расположенных относительно вертикальной плоскости. Периодическое смещение кромок относительно контактов приводит к снижению качества сварного соединения, особенно в непрерывных трубосварочных станах при прохождении через формовочную и сварочную машины стыка полос следующих друг за другом рулонов. 2. Возможность появления на поверхноститрубы локальных оплавленных участков (поджогов), возникающих вследствие образования электрической дуги в момент нарушения контакта. Нарушение контакта происходит при прохождении стыка, дефектах формовки или свариваемой ленты. 3. Необходимость периодической остановки стана при смене контактных наконечников или проточке вращающихся электродов. 16. сварка металлических оболочек электрических кабелей Целесообразность применения высокочастотной сварки в производстве кабельных оболочек обусловлена следующими факторами: 1) использованием в качестве основного материала для оболочек электрических кабелей алюминия и стали вместо дефицитного и дорогого свинца; 2) возможностью уменьшения толщины сварной оболочки по сравнению с прессованной (рис. 93) за счет отсутствия ощутимой разиотолщинности по диаметру (у прессованной оболочки разнотолщинность достигает 10—15%); 3) возможностью сварки практически любых металлов при неограниченных скоростях (при этом не выдвигаются специальные требования к качеству ленты и состоянию свариваемых кромок); 4) отсутствием специальной тепловой изоляции кабельного сердечника ввиду малого объема разогреваемого металла и высокой скоростиохлаждения сварного шва [17]. Основное требование к кабельным оболочкам — герметичность. Как правило, кабельные магистрали работают в тяжелых условиях. В процессе эксплуатации подземные кабели помимо давления грунта испытывают дополнительную нагрузку от проходящего транспорта, а на мостах и в местах пересечения дорог подвергаются знакопеременным нагрузкам вследствие вибраций. При высокочастотной сварке свариваемые встык оболочки (особенно из стали) имеют тонкие стенки (до 0,3 мм), Скоростьсварки периодически уменьшается в 2—3 раза по сравнению с рабочей скоростью, для свариваемых оболочек применяется стандартнаялента нормальной точности. Рассмотрим вариант наложения сварной оболочки на сердечник с экраном из алюминия или меди. Этот вариант наиболее характерен для кабелей со стальной оболочкой. Как и при сваркетруб малого диаметра, необходимыми условиями для реализации процесса высокочастотной сварки тонкостенных изделий являются стабильность угла схождения, постоянство толщины оплавленного слоя кромок и их устойчивость при осадке. В конструкции агрегата предусмотрены механизмы и устройства, обеспечивающие стабильность режима сварки при наличии возмущений, вносимых спецификой свариваемого изделия. К таким механизмам относится формующее устройство, в котором формуется оболочка при прохождении ленты между приводными и неприводиыми вращающимися валками. Криволинейные поверхности валков в сопряжении образуют калибры открытого типа с проходными сечениями, соответствующими толщине изгибаемой заготовки (см. рис. 94). Вследствие колебаний толщины ленты и погрешностей инструмента наряду с пластическим изгибомленты могут возникнуть местные изменения ее толщины, которые, как правило, ведут к образованию гофров на кромках и, следовательно, к нарушению режима сварки. В формующем устройстве применена система слежения валков открытых калибров 3 и 4 за геометрическими и силовыми изменениями, происходящими в этих калибрах, благодаря чему удалось полностью устранить возможность образования гофров г. процесссваркиоболочки осуществляется в сварочной машине, схема которой показана на рис. 86. Машина обеспечивает получение качественного сварного соединения тонкостенных оболочек. сварка оребренных труб В теплообменныхаппаратах применяются трубы с развитой наружной поверхностью, т. е. с прямыми и спиральными ребрами. Такие трубы изготавливаются методом прессования. При этом способе низка производительность и высоки капитальные затраты, невозможно получить трубы с тонкостенными ребрами. Приварка ребер к трубам дуговой сваркой иод слоем флюса в среде углекислого газа малопроизводительна и, кроме того, зона термического влияния в теле трубы настолько велика, что создается опасность разупрочнения трубы. При высокочастотной приварке ребер к трубам обеспечивается высокая производительность, минимальная зона термического влияния, высокое качество сварного соединения при использовании различных материалов. В связи с этим в СССР и за рубежом ведутся работы по использованию высокочастотного нагрева при приварке ребер к трубам. сварка стальных тонкостенных спиральношовных труб Тонкостенные трубы, для которых D/2d > 100^-250, нужны, например, для сельского хозяйства, нефтепромыслов, промышленной вентиляции и др. Обычно такие трубы изготавливались на станах спиральношовнои сварки с соединением кромок встык или внахлестку дуговой или контактной роликовой сваркой. При этом Скоростьсварки невелика: при дуговой сварке она не превышает 2,5 м/мин, а при контактной — 4 м/мин. Контактной сваркой можно получать качественные трубы только из холоднокатаной травленой ленты без следов ржавчины или смазки. Такая подготовка ленты значительно удорожает процесс производства и препятствует широкому применению его в промышленности. Технология высокочастотной сварки спиральношовных тонкостенных труб с контактным подводом тока (рис. 105) разработана в 1963—1965 гг. [121. Как и при сварке спиральношовных труб большого диаметра, качество соединения зависит от геометрии свариваемых кромок на участках нагрева и осадки. При сварке спиральношовных тонкостенных труб геометрия кромок регулироваться не может, и поэтому для обеспечения оптимальных условий сварки необходимо особое внимание уделять выбору исходных параметров формовки: углу формовки и ширине ленты, используемой для изготовления труб.