Технология прокатного производства.
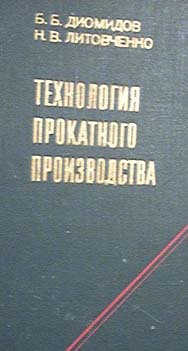
Б.Б.Диомидов, Н.В.Литовченко.
Металлургия, 1979 г.
Листовой прокат, особенно холоднокатаный, является одним из самых экономичных видов металлопродукции. Из него можно изготовлять разнообразные штампованные и сварные конструкции и изделия, отличающиеся меньшей массой по сравнению с литыми. Так, сварные трубы для газо-нефтепроводов и другие профили, изготовляемые из листового проката, имеют стенки тоньше, чем горячекатаные, и поэтому их использование снижает расходметалла на 10—15%.
Доля листового проката в общем объеме прокатного производства в промышленно развитых странах постоянно возрастает, что объясняется быстрым развитием капитального строительства, автомобильной, авиационной, электротехнической, консервной и других отраслей промышленности. В настоящее время в СССР доля листового проката в общем производстве проката составляет несколько более 40 %.
Производство листа в общем выпускепроката в СССР будет неуклонно возрастать, в связи с чем будет продолжено строительство новых высокопроизводительных листопрокатных станов.
Листовая сталь подразделяется на толстолистовую, тонколистовую горячей и холодной прокатки и универсальную. Определяющей в этой классификации является толщина. Так, по отечественным стандартамлисты толщиной от 4 до 160 мм относят к толстым; листы толщиной до 3,9 мм (включительно) относят к тонким. Универсальная сталь — горячекатаная сталь прямоугольного сеченияшириной от 160 до 1050 мм и толщиной от 4 до 60 мм — прокатывается на универсальных станах, клети которых имеют вертикальные валки, обрабатывающие боковые кромки. При этом кромки получаются после прокатки готовыми. У толсто- и тонколистовой стали боковые кромки в большинстве случаев получаются готовыми только после резки на ножницах. Деление листов на толстые и тонкие является условным. Эта условность становится все большей по мере развития непрерывной прокатки, так как на современных непрерывных листовых станах прокатывают широкий сортамент, включающий как тонкие, так и толстые листы.
ГЛАВА VIII.
ГОРЯЧАЯ ПРОКАТКА ЛИСТОВОЙ СТАЛИ
1. Сортамент
Как уже отмечалось, повышение доли листовой продукции в выпускепроката является одним из основных направлений в развитии современного отечественного и зарубежного прокатного производства. В связи с этим за последние годы резко возросли объем и сортамент горячекатаной листовой стали. Приведем в качестве примера некоторые размеры горячекатаной листовой стали:
по ГОСТ 1577—70 производится горячекатаная толстолистовая качественная углеродистая и легированная конструкционная сталь толщиной от 4 до 160 мм. Ширина толстых листов 600—3800 мм, длина 2—12 м. Сталь, прокатанная на непрерывных станах, может поставляться в рулонах;
согласно ГОСТ 5520—69 производится толстолистовая горячекатаная углеродистая и низколегированная сталь, пригодная для сварки и предназначенная для изготовления деталей и частей паровых котлов и сосудов, работающих под давлением при нормальной, повышенной и минусовой температурах. Размеры листов: толщина 4—160 и ширина 600—3800 мм, длина 2—12 м. Сталь, прокатанная на непрерывных станах, может поставляться в рулонах;
по ГОСТ 5521—76 производится свариваемая углеродистая и низколегированная толстолистовая и тонколистовая сталь, предназначенная для изготовления сварных конструкций для судостроения. Размеры толстых листов: толщина 4—160 и ширина 600—3800 мм, длина 2—12 м. Размеры тонких листов: толщина 0,5—3,9 (4,0) и ширина 600—1400 мм длина 1,2—4 м. Толсто- и тонколистовая сталь, прокатанная на непрерывных станах, может поставляться в рулонах; ГОСТ 82—70 распространяется на горячекатаную сталь прямоугольного сечения (полосовую) шириной от 160 до 1050 и толщиной от 4 до 60 мм, прокатываемую на универсальных станах. Полосы поставляются длиной от 5 до 18 м;
сталь листовая горячекатаная по ГОСТ 19903—74 изготовляется в листах и рулонах толщиной от 0,5 до 160
и от 1,2 до 12 мм соответственно. Длина листов при ширине 600—3800 мм составляет 1,2—12 м. ширина стали, поставляемой в рулонах, равна 500—2200 мм;
горячекатаная лента из углеродистой стали обыкновенного качества, согласно ГОСТ 6009—74, имеет толщину 1,2—5,0 и ширину 20—220 мм. лента получается горячей прокаткой или продольной резкой горячекатаной листовой рулоннойстали и поставляется в рулонах.
Классификация размеровпрофилей листовой стали в зависимости от способа производства может быть примерно представлена в виде рис. 134.
Согласно ГОСТ 16523—70, горячекатаную и холоднокатаную углеродистую сталь толщиной до 3,9 мм включительно и шириной не менее 500 мм классифицируют по: 1) видам продукции при поставке (на листы и рулоны); 2) нормируемым характеристикам (на категории 1—5); 3) качеству отделкиповерхности (на группы: I— особо высокой отделки, II—высокой отделки; III—повышенной отделки, IV—обычной отделки);
4) способности к вытяжке (сталь категорий 1 и 5, на глубокую Г, кроме стали марки ВСт1, и нормальную—Н);
5) методамиспытаний [с контролем механических свойств, вытяжки и микроструктуры или без контроля
Согласно ГОСТ 19903—74, на сортамент листовой горячекатаной стали принята классификация по точности прокатки, плоскостности, характеру кромки и размерам.
Как видим, указанные ГОСТы в известной мере классифицируют профили листовой стали не только по толщине, ширине, маркам, но также и по назначению.
Несколько обособленно выделяется производство тонких и тончайших лент, которые по сортаменту разнообразны в силу различного их назначения. От их выпуска зависит, однако, развитие многих важных отраслей народного хозяйства таких, как радио, телевизионная и в значительной мере автомобильная промышленность. Так, в качестве примера кинескопы для цветных телевизоров требуют ленты толщиной 0,1—0,12 мм с чрезвычайно высокой точностью по ширине и длине (планшетность).
Рассмотрим отдельно производство горячекатаной толстой, тонкой и холоднокатаной листовой сталей.
2. Технологические операции при производстве листовой стали
Общепринятыми можно считать следующие варианты технологических схемпрокатки толстолистовой стали, если исходным полупродуктомстана являются слитки или слябы: 1) слиток—подготовка к нагреву, нагрев, ПРОКАТКА на подкат определенной толщины и ширины, нагрев подката, ПРОКАТКА на лист окончательных размеров, отделкалиста (обрезь переднего, заднего концов раската
и др.);
2) сляб—подготовка к нагреву, нагрев, ПРОКАТКА на стане на лист определенной ширины и толщины отделкалиста (обрезь переднего, заднего концов раската, боковых кромок и др.).
Видно, что прокатпрофилей толстолистовой стали из слитков имеет большее число технологических операций, которые усложняют полный циклпрокатки листа. Причем особое место занимает подготовка слитков к нагреву, т. е. обрезь верхней и нижней его частей.
Несомненно наиболее рациональной и экономически эффективной следует считать технологию прокатки, при которой исходной заготовкой является сляб.
На современных непрерывных тонколистовых станах принято «перекрытие» сортамента листовой стали по толщине более 4 мм. В определенных пределах толщин весь раскат готовой толстолистовой стали оформляется и поставляется в рулонах. Этот процесс включает в себя следующие технологические операции: подготовка слябов к нагреву, нагрев и ПРОКАТКА их на лист, оформление раската в рулон; в некоторых случаях при необходимости раскат разрезается на листы определенной длины.
Значительно больше технологических операций выполняется при холодной прокатке тонких листов. Примерная технологическая схема холодной прокатки тонких листов включает следующие операции: подготовка горячекатаных рулонов к прокатке (травление поверхности листа, предварительная смазка ее), холодная ПРОКАТКАрулонов на непрерывном стане, очисткаповерхностирулонов холоднокатаной листовой стали от загрязнений (масла, частично оставшейся окалины и др.), отжигрулонов в печах для снятия наклепа (упрочнения), дрессировкаметалла — ПРОКАТКА отожженного листа на дрессировочных станах. Дальнейшие операции после дрессировкисвязаны с назначением тонколистовой стали.
3. Исходный материал и нагрев его перед прокаткой (общие положения]
Исходным материалом для производства горячекатаной листовой стали на современных станах, как правило, являются слябы. Однако в ряде случаев применяются и слитки, если нет возможности обеспечить станслябами или требуется ПРОКАТКАлистов специального назначения: большой ширины, толщины и длины. Технологические операции при применении слитков нами в общем виде рассмотрены.
На отечественных толстолистовых станах используют слитки прямоугольного сечениямассой от 6—8 до 120 т. Однако основной объемпроката получают из слит- . ков массой 22—25 т, большая их масса определяется уже специальным назначением листа. Размеры и соотношение сторон слитков, предназначенных для производства слябов и профилей толстолистовой стали, приведены в разделе о производстве полупродукта. Однако следует указать, что при определении толщины слитка надо исходить не только из условийкристаллизации жидкой стали, структуры зерен литой стали и последующих условий ее деформации, но и учитывать такое суммарное обжатие, которое обеспечило бы получение готовой листовой стали требуемого качества. В зависимости от толщины h прокатываемого листа минимальную толщину Я слитка рекомендуется принимать в следующих пределах:
Толщина диета h, мм . S—20 20—40 50—100 120—205
Минимальная толщина
слитка Я, мм..... (18—20) к (12—18) к (7—12) ft (4—7) ft
Как правило, слитки большой массы, предназначенные для производства листовой стали, отливают в изложницы, уширенные кверху и снабженные утепляющими надставками. Конусность слитков должна быть минимальной. В настоящее время конусность слитка на одну сторону принята 1,5—2,5%; чем больше масса слитка, тем больше конусность. Качество поверхности слитков и слябов определяет и качество готовой листовой стали. Поэтому их подготовке к нагреву и прокатке уделяют особое внимание.
Поверхностными дефектами и признаками неподготовленности слитка к нагреву и прокатке являются плены, продольные и поперечные трещины наличие прибыльной части, усадочной раковины и выступов на нижней части от выработки поддонов. Происхождение этих дефектов рассмотрено в первой части — при производстве полупродукта.
Прокатка толстолистовой стали из слитков требует особой и обязательной подготовки по следующим основным технологическим положениям.
Необходимо осуществить обрезь верхней и нижней частей слитка перед посадкой в печь. В усадочной раковине концентрируются различные ликваты, легкоплавкие соединения, которые при нагреве в печи превращаются в жидкую фазу и заливают подину печи или проникают на подину зон нижнего подогрева. Но удаление прибыльной (верхней) части слитка приводит к преждевременному в ряде случаев довольно часто повторяющемуся выходу нагревательной печи из строя, что связано с ее остановками, ремонтом и потерей производительности стана. Кроме того, ненужные верхнюю и нижнюю части слитка, составляющие почти 20% от его общей массы, нагревать в печи, расходуя для этого топливо, нерационально. Кроме того, после обрези верхней и нижней частей слиток оформляется в более удобную и рациональную форму, что благоприятно отражается на его продвижении вдоль подины печи и на собственно процессе прокатки.
Поверхностные трещины и плены удаляются с помощью огневой пневматической или наждачной зачистки. При удалении поверхностныхдефектов следует выдерживать соотношение между шириной Ь канавки и ее глубиной hc в месте расположения дефекта:. Если это соотношение не выдерживается, то в процессеобжатия могут образовываться наплывы металла и, таким образом, получатся новые дефекты.
На поверхностисляба могут проявляться следующие дефекты: продольные и поперечные трещины, плены. Возможно, что все эти дефекты наследственные и образовываются при прокатке слитков на слябинге. Происхождение продольных и поперечных трещин на поверхностисляба также бывает связано с температурным режимом нагрева или охлаждения. Поверхностныеплены образовываются еще при прокатке слитка, подкорковые пузыри которого располагаются близко к поверхности (малая толщина внешней стенки слитка до подкорковых