Справочник волочильщика проволоки
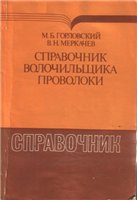
М.Б. Горловский, В.Н. Меркачев
Металлургия, 1993 г.
Основной способ производства катанки— горячая прокатка. Для производства мелкосортной катанки высокой точности и катанки фасонного сечения применяются также методы холодной прокатки и прессование. Некоторые виды катанки из цветных металлов (меди, алюминия) получают комбинированным способом: непрерывным литьем с последующей прокаткой.
По способу охлаждения после прокатки стальная катанка подразделяется на:
а) охлажденную на воздухе (обозначается "ОВ");
б) ускоренно-охлажденную (обозначается "УО").
Катанка УО содержит на поверхности меньшее количество окалины (на 30-40 %), нежели катанка ОВ, что значительно облегчает процесс ее травления и снижает отходы металла на эту операцию (табл. 5).
Хранение катанки
Катанка на заводе-потребителе хранится, как правило, на открытых складских площадках в штабелях. На тех производствах, где равномерность механических свойств проволоки имеет первостепенное значение (канатная, пружинная и др.), хранение катанки, а также подача ее в производство должны быть строго поплавочными.
При обслуживании склада катанки мостовым краном с поворотной тележкой грузоподъемностью 2,5-2,8 т с управлением из кабины складирование катанки осуществляется в штабелях до 4-5 ярусов при максимальной высоте укладки бунтов до 5 м. Нагрузка на 1 м2 площади склада при высоте укладки 1 м и в зависимости от массы и размеров бунтов катанки (см. табл. 2) составляет от 0,6 до 1,1 т/м2.
Нормы запаса катанки, исчисляемые в суточной потребности предприятия-потребителя, составляют1, дни:
1-3-склад на одной территории с поставщиком катанки;
5 — поставщик катанки в одном регионе с потребителем;
10 — поставщик катанки в примыкающих регионах с потребителем;
20 — поставщик катанки и потребитель в разных регионах страны.
2. ПРОВОЛОКА
Изделие сплошного сечения, полученное методом волочения из металлов или сплавов и намотанное в мотки или на катушки, принято называть проволокой в отличие от прутков, полученных также методом волочения из тех же металлов и сплавов, но поставляемых в виде прямых отрезков сравнительно небольшой длины (2—6 м).
1. МЕТОДЫ ОЦЕНКИ КАЧЕСТВА КАТАНКИ
Катанка поступает потребителю партиями. Партия должна сопровождаться сертификатом, удостоверяющим ее качество, в котором указываются: а) наименование и товарный знак предприятия-изготовителя; б) номер, размер (диаметр) и масса партии; в) марка металла (химический состав), номер плавки, а также другие данные, необходимые для характеристики конкретного типа катанки. Каждый бунт катанки должен быть снабжен маркировочной биркой, на которой указываются необходимые сведения о нем.
ГОСТ 7566-81, а также другая нормативно-техническая документация представляют потребителю право производить контрольную приемку и проверку поступившей к нему партии катанки на соответствие ее показаний требованиям ГОСТов или другой НТД, применяя при этом правила отбора проб и методы испытаний, а также методы осмотров и замеров катанки, указанные в соответствующей НТД.
Отбор проб для проведения механических испытаний, исследование микро- и макроструктуры, химического анализа, а также определения других показателей качества катанки производится, как правило, от переднего и заднего концов бунта на расстоянии не менее 1,5 м от конца или начала бунта.
Осмотр поверхности катанки, предназначенный для выявления наружных поверхностных дефектов катанки (табл. IS и рис. 1), производится визуально без применения увеличительных приборов. Для выявления дефектов катанки, скрытых пленкой окалины, образцы катанки длиной 200—250 мм могут быть подвергнуты глубокому травлению в растворе серной или соляной кислот при температуре 60—80 °С в течение 10—30 мин.
Глубина порока металла катанки может быть определена запиловкой дефектного участка поверхности напильником с последующим замером глубины этого дефекта штангенциркулем или микрометром.
В сомнительных случаях для проверки качества поверхности катанки допускается применять метод переменного скручивания образцов (ГОСТ 1545-80); метод магнитной дефектоскопии, а также другие методы, оговоренные в НТД на конкретные виды катанки.
Не являются браковочными признаками отдельные незначительные дефекты на поверхности катанки: отпечатки, неглубокие продольные швы, царапины, рябизна, волосовины, раскатанные пузыри, незначительные нарушения геометрии катанки и другие мелкие дефекты, не выводящие размеры катанки за предельные отклонения по диаметру.
При визуальном осмотре бунтов катанки могут быть установлены также следующие дефекты:
перепутанность витков бунта, затрудняющая нормальную размотку его в процессе волочения;
наличие в партии катанки легковесных бунтов больше (в процентном отношении ко всей партии), чем это допускается НТД;
наличие на поверхности катанки трудносмываемых пятен жира, смазки или других химических продуктов, затрудняющих процессы травления и волочения.
Измерение диаметра и овальности катанки производится не менее чем в двух-трех местах бунта в двух взаимно перпендикулярных направлениях одного сечения на расстоянии не менее 1,5-2,0 м от начала или конца бунта.
2. МЕТОДЫ ОЦЕНКИ КАЧЕСТВА ПРОВОЛОКИ
Готовая проволока на предприятии-изготовителе предъявляется контрольно-приемному органу (ОТК) партиями.
Партия состоит из проволоки одного номинального диаметра, одной марки металла, одного вида поверхности, а также имеющей иные однотипные свойства, характеризующие конкретный вид проволоки, и сопровождается документом о качестве (сертификатом).
Осмотр и замер проволоки. Визуальный осмотр и замер предъявленной к сдаче проволоки производится с целью:
определения качества намотки мотка (катушки) и обвязки его;
установления соответствия массы мотков и габаритных размеров принятой норме для данной партии проволоки;
Многократные волочильные машины с синхронизацией скоростей промежуточных барабанов
Существует две системы синхронизации скоростей промежуточных барабанов и соответственно два вила машин этого типа:
а) петлевые (роликовые) машины, у которых процесс синхронизации скоростей промежуточных барабанов происходит за счет изменения длины петли проволоки между смежными барабанами Б„ и Б„_, под воздействием износа волоки, например на барабане Б„ (рис. 31, а), и поворота вследствие этого на определенный угол рычага 1, которые через сектор 2 и шестерню 3 воздействует на электрический механизм регулирования скорости барабана Б„_, и приводит его скорость в соответствие с фактической вытяжкой между этими барабанами в данный момент времени;
б) беспетлевые (прямоточные)' волочильные машины, у которых процесс синхронизации скоростей промежуточных барабанов, например барабана Бл_, (рис. 31, 6) осуществляется за счет изменения крутящего момента на валу этого барабана под действием изменения натяжения протягиваемой проволоки вследствие износа волоки на барабане Б„ и изменения фактической кинематической вытяжки между барабанами Б„ и Бл_, в данный момент времени.
Волочильные машины прямоточного типа создают в процессе волочения регулируемое усилие противонатяжения Ря, которое составляет 15—30 % от усилия волочения Р.
Сам принцип синхронизации скоростей промежуточных барабанов достаточно привлекателен, так как обладают целым рядом достоинств, но из-за недостаточной надежности систем автоматической синхронизации волочильные машины этого типа в отечественном проволочно-волочильном производстве не нашли широкого распространения.
Вспомогательное оборудование и инструмент для заправки волочильных машин
Заправка волочильных машин производится:
при замене волок вследствие их поломки или физического износа;
при замене всего перехода волочения в связи с перенастройкой волочильной машины на изготовление проволоки другого диаметра или качества;
при обрывах проволоки во время волочения.
Заправка волочильной машины трудоемкая, как правило, неперекрываемая машинным временем операция, для выполнения которой применяется специальное вспомогательное оборудование и инструмент.
Острильные, острильно-затяжные и затяжные станки
Острение проволоки диаметром свыше 0,8—1,0 мм для протяжки ее через волочильный инструмент при заправке волочильной машины (или же для протяжки через волоки с целью контроля ее размеров и геометрии) производится вальцеванием концов проволоки между валками острильных станков, канавки которых имеют переменное сечение по окружности (рис. 39 и табл. 82).
ВОЛОЧИЛЬНЫЙ ИНСТРУМЕНТ
Волока — инструмент для обработки металлов давлением методом волочения. Для волочения проволоки из черных и цветных металлов и их сплавов применяют волоки следующих видов: монолитные (рис. 58, а, б), сборные (рис. 58, в), роликовые (рис. 6, в).
Канал монолитной волоки имеет четыре основные зоны (см. рис. 58):
входную зону 1 — наиболее широкую часть канала волоки, предназначенную для облегчения ввода заготовки в волоку и подачи технологической смазки в рабочую зону;
смазочную и рабочую зону 2 — часть канала волоки, предназначенную для осуществления деформации протягиваемого металла;
калибрующую зону 3 — часть канала волоки, предназначенную для придания поперечному сечению протягиваемой заготовки заранее заданных размеров точности;
выходную зону 4 — часть канала волоки с постепенно увеличивающимся в направлении волочения поперечным сечением, предназначенную для исключения возможности образования поверхностных повреждений: задиров, царапин, рисок при выходе проволоки из волоки.
Рабочий угол волоки а. — угол, составленный образующей рабочего конуса волоки осью канала.
У радиальных волок за рабочий угол волоки принимается угол, образованный касательной к образующей канала волоки при входе в рабочую зону и осью канала волоки (см. рис. 58, б).
Форма и размеры отдельных зон канала волоки зависят от качества и диаметра протягиваемого металла, величины обжатия, условий волочения и выбираются по следующим общим соображениям:
1. Входная зона обычно соответствует форме и размерам этого участка в исходной волоке - заготовке.
2. Рабочая зона может иметь коническую форму и значительно реже радиальную форму.
Стойкость и износ волочильного инструмента
Под стойкостью волочильного инструмента подразумевается свойство волоки противостоять изменению формы, размеров и качества поверхности канала под действием протягиваемой проволоки.
Показатели стойкости волок (кг или м протянутой проволоки) приведены ниже:
стойкость до износа Си - стойкость до выхода размера и формы канала волоки из поля допуска;
Расчетная стойкость до изменения размеров на 0,1; 0,01; 0,001 мм -отношение количества проволоки, протянутой через данную волоку, к числу условных долей износа;
Стойкость до налипания стойкость волоки до появления на поверхности проволоки недопустимых царапин, рисок, задиров или налипания металла;
Стойкость до разрушения - стойкость волоки до ее разрушения (раскалывания);
Эксплуатационная стойкость -стойкость волоки до выхода ее из эксплуатации независимо от причин.
Показатель стойкости волоки, выраженный в метрах, более удобен, так как позволяет сравнивать стойкость волок различных диаметров.
Формулы для расчета эксплуатационной стойкости волочильного инструмента при волочении проволоки из цветных металлов и сплавов приведены в табл. 117, а эксплуатационная стойкость волок при волочении стальной, медной и алюминиевой проволоки - в табл. 118, 119.