Серебро
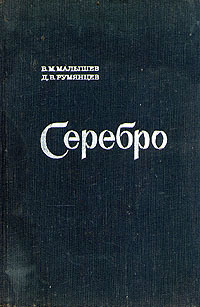
Малышев В. М., Румянцев Д. В.
Металлургия, 1987 г.
ПРОИЗВОДСТВО ПОЛУФАБРИКАТОВ ИЗ СЕРЕБРА И ЕГО СПЛАВОВ
Из серебра, его сплавов, а также сплавов с добавками серебра производят полуфабрикаты в виде полос, лент, фольги, труб, всевозможных профилей, штампованных деталей и различные детали, получаемые методами порошковой металлургии. Проведено значительное количество исследований с целью создания и внедрения в производство биметаллических полуфабрикатов в виде полос, груб, проволоки, профилей различной конфигурации, контактов заклепочного типа и др. производствобиметаллов направлено не только на экономию серебра; в ряде случаев серебряные биметаллы применяют для получения свойств, которыми не обладает однородный металл. В области производства и применения биметаллов существуют огромные возможности и по экономии серебра, и по созданию материалов с новыми свойствами.
В настоящее время очень перспективны исследования с целью создания на основе серебра композиционных материалов, армированных волокнами металлов, оксидов, гидридов и пр. [81]. Работы по производству композиционных материалов, армированных волокнами, находятся в стадии лабораторных исследований, но испытания образцов показывают очень хорошие результаты. Широкого промышленного применения эти материалы пока не нашли. К полуфабрикатам из серебра и его сплавов предъявляются жесткие требования по допускаемым отклонениям от химического состава, плотности, наличия газовых включений, чистоты по примесям, чистоты поверхности, геометрическим размерам и тд.
1. Технологияплавки и литья
Основы качества металла закладываются при плавке и литье слитков.
Для обеспечения высокого качества слитка необходимыми условиями являются строгое соблюдение технологической дисциплины и правильный выбор методаплавки и литья.
В предыдущем издании подробно описаны методыплавки и литья серебра и его сплавов. В настоящей работе рассматриваются последние достижения в области плавки в литья, особенности производства слитков некоторых сложных сплавов.
Шихту подготавливают в специальном помещении — «шихтовом дворе» и передают в плавильно— литейное отделение. Кроме основных компонентовсплава в шихту вводят раскислители: Р, Li, Zn.
Назначение раскислителей — восстановление окисленных компонентовшихты до металлов для повышения их жидкотекучести и качества отливаемых слитков, а также обеспечение минимальных потерь металлов от угара и в отходы. В основе процесса раскисления лежат реакции вытеснения кислорода из оксидовкомпонентовшихты приведенными выше раскислителями.
Фосфор вводят в виде фосфористой меди марок МФ1 или МФ2 для раскисления сплавов Ag—Сu, Аи—Ag—Сu, Ag—Сu—Ni, Pd—Ag—Сu, а также припоев Ag—Сu—Sn, Ag—Си—Ni, Аи—Ag—Сu—Cd и др., содержащих медь, никель, олово, кадмий, кобальт, свинец.
Литий вводят в чистом виде или в сплаве с медью для раскисления и дегазацииводородасплавов Ag—Си, Аи—Ag—Си и др., а также припоев на основе серебра из неокисленных или слабоокисленных шихт.
Цинк вводят в виде чистого металла, а кадмий в виде меднокадмиевой лигатуры для раскисления сплавов и припоев, содержащих в качестве компонентов медь и кадмий. Кроме того, кадмий вводят как специальный раскислитель в серебряные сплавы, содержащие никель и медь, например, в сплавы Pd—Ag—Си и Pd—Ag—Ni.
Большое значение имеет точная дозировка раскислителей. Так, при недостаточном количестве фосфора, вводимого в качестве раскислителя в сплав Ag—Сu, в последнем остается гемиоксид меди Сu2О, вследствие чего в нем появляются плены. Такой сплав подвержен «водородной болезни» при светлом отжиге в атмосфере даже с небольшим содержанием водорода, а также внутреннему окислению, если отжиг ведут на воздухе или в атмосфере с небольшим содержанием кислорода. Слишком большое количество фосфораприводит к красноломкости при температуре выше 650°С. Применение фосфора для сплавов, идущих на электротехнические цели, вообще нежелательно, так как остающийся в сплавахфосфор снижает их электропроводность.
В целях обеспечения минимальных потерь серебра от угара и в отходы и получения слитков хорошего качества надо соблюдать при планке следующие условия:
шихта не должна быть порошкообразной, она должна состоять из компактных кусков, брикетов, обрезков, которые имеют наименьшую поверхность взаимодействия с атмосферой плавильного пространства;
составляющие шихты нужно загружать в плавильный агрегат и плавить в порядке возрастания температур плавления, сродства кислороду и летучести;
обязательно применять защитные среды, покровы и флюсы. Для защиты от окисления и с целью теплоизоляции, а также дегазациишихту при плавке и литье серебра и сплавов Ag—Сu, Аu—Ag, Аu—Ag—Сu, а также припоев Аи—Ag—Pd, Ag—Pd, Ag—Sn и Ag—Pd—Sn рекомендуется покрывать березовым, обязательно предварительно прокаленным в вакууме, углем.
Плавленую буру применяют при плавке и литье серебрянокадмиевых сплавов Ag—Cd и припоев Ag—Си, содержащих кадмий, цинк, марганец, никель, олово.
Смесь березового (прокаленного) угля с плавленой бурой (1:1) применяют для ошлакованияоксидов при плавке и литьеприпоев Ag—Сu, а также сплавов серебра, содержащих наряду с медью и цинкомкадмий и олово.
Смесь березового угля, буры и мела (1: 1; 1) в прокаленном состоянии применяют для защиты от окисления с целью теплоизоляции и ошлакованияоксидов при плавке и литьесплавов Ag—Сu, Аu—Ag—Сu, Ag—Cd, Ag—Zn.
Для промежуточных защитно - рафинировочных плавокшихты из серебра с медью, загрязненных небольшим количеством алюминия, магния, кремния, цинка, олова, железа, марганца, кадмия, никеля, кобальта, селена, сурьмы, свинца, висмута, мышьяка, теллура и др., рекомендуются смеси кальцинированной соды с бурой (l-1-1,4:1), поташа с бурой (1: 1), калиенатриевого карбоната с бурой (1:1), кальцинированной соды с бурой, мелом и толченый березовым углем (2:3:1:1).
Если шихта значительно загрязнена указанными примесями, то следует применять смесь кальцинированной соды с бурой, гашеной известью и толченым березовым углем (4:4:1:1) или смесь селитры (натриевой или калиевой) с бурой.
Для примера приведем порядок приготовления сплавов Аu—Ag, содержащих до 25 % Ag: сначала загружают слитки и брикеты только золота пли сплавов из золота, причем, сплавы — па дно тигля; по мере расплавления добавляют серебро, затем обрезкисплавов и золота; нагревают расплав до 1200—1250 °С для сплавов, содержащих до 10 % Ag, и до 1210—1260°С для сплавов с 10—25 % Ag.
Широко применяют в производстве промежуточные сплавы-лигатуры с целью уменьшения потерь металлов с высокой упругостью паров, таких как кадмий, цинк, магний, или для введения в сплавметалла с ограниченной растворимостью в основном металле.
Точка кипениякадмия 768°С, при добавлении 19 и 31,5% (по массе) меди температуракипения соответственно повышается до 801 и 820 °С. При введении кадмия в расплав серебра, меди или сплава Ag—Сu он интенсивно окисляется, превращаясь в бурые хлопья. В расплавленную медь кадмий практически ввести невозможно. На практике в таких случаях применяют лигатуру. Для сплава Сu—Ag—Cd применяют лигатуру Сu—Cd с содержанием кадмия 45—50% (по массе). Последовательность операций следующая: в прокаленном графито-шамотном тигле под защитой древесного угля расплавляют кадмий (321 °С), перегревают до 700 °С, затем порциями вводят медь. температура полного расплавления такой лигатуры 650—720 "С и при соблюдении режима кадмий весь остается в сплаве. лигатуру отливают в отдельный СЛИТОК и вводят в основной расплав, покрытый слоем жидкой буры. Таким образом достигается максимальная скоростьрастворениякадмия в расплаве и минимальный угар кадмия. Для припоев Ag—Cd и сплавов Ag—Cd для внутриокисленных контактных материалов применяют лигатуру Ag—Cd (50— 80 % (по массе) Cd). температура полного расплавлениялигатур составляет 730—660°С, т.е. ниже точкикипения кадмия. Как и в сплав Сu—Ag, в чистое сереброкадмий вводят в виде лигатуры. Таким образом достигается аналогичный эффект.