Производство заготовок в машиностроении
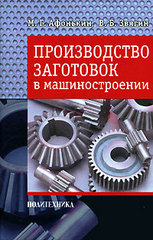
Афонькин М.Г., Магницкая М.В.
Машиностроение, 1987 г.
Материалы и требования, предъявляемые к качеству детали.
Основная тенденция современного машиностроения — применение материалов, обеспечивающих необходимые конструктивные и эксплуатационные свойства, имеющих повышенную обрабатываемость на всех стадиях передела. Иными словами, материалы должны обладать необходимым запасом определенных технологических свойств — ковкостью, штампуемостью, жидкотеку-честью, свариваемостью, обрабатываемостью.
Необходимым технологическим свойством для деформируемых материалов является технологическая пластичность. Чем ниже пластичность материала, тем сложнее получить качественную заготовку методом обработки металлов давлением, тем сложнее технологический процесс, тем выше себестоимость детали. Так, при изготовлении поковок из труднодеформируемых высокопрочных сплавов осуществить необходимую степень деформации за один нагрев не всегда удается, поэтому необходимо введение дополнительных промежуточных нагревов, что значительно повышает себестоимость и трудоемкость изготовления поковок. Особенно жесткие требования по технологической пластичности предъявляют к тем сплавам, изделия из которых подвергают холодной обработке металлов давлением — выдавливанию, вытяжке, гибке, формовке.
При выборе способа получения отливок также необходимо учитывать технологические свойства сплавов. Например, если материал обладает пониженными литейными свойствами (низкая жидкотекучесть, высокая склонность к усадке и т.п.), не рекомендуется применять для получения отливок из этого материала такие способы, как литье в кокиль или литье под давлением, так как из-за низкой податливости металлических форм могут возникнуть литейные напряжения, короблениеотливки и трещины. В таких случаях целесообразно применение способов: оболочковое литье и литье в песчано-глинистые формы.
Сплавы, склонные к повышенному поглощению газов (многие литейные сплавы на основе алюминия), нежелательно применять для получения заготовок литьем под давлением; для центробежного литья исключено применение сплавов, склонных к ликвации.
В технических условиях для ответственных, тяжело нагруженных деталей, для деталей, работающих в условиях переменных нагрузок, в специальных средах (детали турбостроения, энергомашиностроения, такие, как валы, шестерни, зубчатые колеса, роторы, турбинные и компрессорные диски и т.п.), указывают определенные требования к качеству материала, к физико-механическим свойствам.
Процесс изготовления стальных отливок значительно сложнее, чем чугунных, так как литейные свойства у стали ниже, чем у чугуна. Для предупреждения образования усадочной пористости необходимы большие прибыли, обтаем которых может достигать 60 % объема отливки, что приводит к увеличению расхода материала в 1,6 раза. Учитывая пониженную жидкотекучесть стали, сечения литниковых каналов необходимо увеличивать в 1,5—3,0 раза. Все это, естественно, снижает коэффициент использования металла, повышает себестоимость деталей.
В табл. 2.10 приведены оптовые цены за тонну стальных отливок для некоторых весовых групп [33] . Сравнивая табл. 2.7 и 2.10 для отливок одних и тех же массы и группы сложности, изготовленных из чугуна и стали, можно отметить, что оптовые цены на отливки из конструкционных нелегированных и низколегированных сталей близки к ценам аналогичных отливок из высокопрочного чугуна.
Учитывая более высокие литейные свойства высокопрочных чугунов, их прочность и пластичность, необходимо оценивать возможность замены стального литья на литье из высокопрочного чугуна.
В структуре литейного производства СССР литье из цветных металлов, и сплавов составляет около 4 %. Однако в последние годы наблюдается тенденция к более широкому использованию цветных сплавов для получения фасонных отливок. Этому способствует наличие ряда особых физико-химических и физико-механических свойств, присущих сплавам из цветных металлов, и прежде всего высокая удельная прочность. В табл. 2.11 представлены значения удельной прочности некоторых материалов, которые определяются как отношение предела прочности материала к его плотности. Как видно из данных таблицы, такие материалы, как алюминиевый и титановый сплавы, имеют более высокую удельную прочность, что позволяет при их применении значительно снизить массу изделий.
Среди литейных материалов из сплавов цветных металлов наиболее широкое применение нашли алюминиевые сплавы. Отливки из алюминиевых сплавов составляют около 70 % общего выпуска цветного литья; 25 % составляют отливки из медных сплавов. В последние годы достигнуты значительные успехи в освоении использования тугоплавких металлов, в частности титана, что значительно расширило область их применения, в том числе и для получения фасонных отливок.
Наиболее высокими литейными свойствами обладают сплавы системы алюминий-кремний, так называемые силумины. Эти сплавы широко применяют в автомобильной, авиационной, приборо-, машино-, судостроительной и электротехнической промышленности, так как они обладают высокими литейными свойствами, достаточными пластичностью и механической прочностью, удовлетворительной коррозионной стойкостью. Из силуминов получают отливки деталей сложной конфигурации, работающие при средних и значительных нагрузках.
Сплавы системы алюминий — медь обладают пониженными литейными свойствами, низкими пластичностью и коррозионной стойкостью, но хорошо обрабатываются резанием. Вследствие широкого интервала кристаллизации сплавы этой системы склонны к образованию усадочных трещин и рассеянной усадочной пористости. Отличительная особенность этих сплавов — теплопрочность. Основная область применения — самолетостроение.
Сложные алюминиевые сплавы, содержащие медь и кремний, обладают высокой жидкотекучестью, коррозионной стойкостью, хорошей свариваемостью. Их применяют для изготовления корпусов различных приборов, автомобильных и тракторных поршней, деталей авиационных двигателей.
Алюминиево-магниевые сплавы из всех литейных алюминиевых сплавов обладают наиболее высокими механическими свойствами, пониженной плотностью, высокими коррозионной стойкостью и прочностью. Их используют при изготовлении отливок, испытывающих большие вибрационные нагрузки или подвергающихся воздействию морской воды. Вследствие большой склонности к окислению, образованию усадочных трещин и рыхлостей, взаимодействию с влагой литейной формы, пониженной жидкотекучести изготовление отливок из этих сплавов вызывает значительные технологические трудности.
Сплавы, не вошедшие в рассмотренные системы, относятся к сложнолегированным; их применяют для отливок, работающих при повышенных температурах и давлениях, требующих повышенной стабильности размеров, для изготовления сварных конструкций и деталей, хорошо обрабатываемых резанием [38] .
Наибольший эффект в снижении себестоимости получается при увеличении коэффициента весовой точности, так как статья расходов на металл во много раз превышает любую другую статью расхода при производстве деталей машин. Как изменяются коэффициент весовой точности и коэффициент использования металла при изготовлении поковки штуцера, показано на рис. 3.33.
В некоторых случаях для выбора оптимальной заготовки целесообразно сопоставлять между собой литье и обработку металлов давлением. Если деталь может быть получена как из отливки, так и из поковки, то прежде всего необходимо оценивать требования, предъявляемые к детали условиями эксплуатации (характер нагрузок, значения механических свойств, требования к плотности, размеру и расположению зерен и т.д.). Обычно эти требования заданы конструктором и изложены в чертеже готовой детали. Ответственные детали, к которым предъявляют повышенные требования по механическим свойствам, особенно по ударной вязкости, рекомендуется изготавливать из кованых или штампованных заготовок. Горячую объемную штамповку наиболее целесообразно сопоставлять с литьем под давлением, с литьем в кокиль и со штамповкой из жидкого металла.
Если деталь по своей конструкции пригодна для штамповки и для литья под давлением, то при выборе способа изготовления необходимо учитывать следующее.
Температуру плавления сплава. Например, деталь изготавливают из медного сплава. Стойкость форм при литье под давлением медных сплавов в среднем 5—10 тыс. шт. отливок, стойкость штампа 10—20 тыс. шт. поковок. Кроме того, стоимость форм в 1,5—2 раза выше стоимости штампа. Следует помнить, что параметр шероховатости поверхности деталей из медных сплавов, изготавливаемых литьем под давлением, ухудшается по мере изнашивания формы, так как на поверхности формы появляется сетка трещин разгара;
Характерной особенностью порошковой металлургии как промышленного метода изготовления различного рода заготовок является применение исходного сырья в виде порошков, которые затем прессуют или формуют в изделия заданных размеров и подвергают термической обработке (спеканию), проводимой при температурах ниже температуры плавления
основного компонента шихты.
Основные элементы технологии порошковой металлургии следующие:
получение и подготовка порошков исходных материалов, которые могут представлять собой чистые металлы или их
сплавы, металлоиды, соединения металлов с неметаллами и другие химические соединения;
прессование из 'подготовленной шихты изделий необходимой формы в специальных пресс-формах, т.е. формование будущего изделия;
термическая обработка (или спекание) спрессованных изделий, обеспечивающая им окончательные физико-механические и другие свойства. В производственной практике иногда встречаются отклонения от типового технологического процесса, например совмещение операции прессования и спекания, пропитка пористого брикета расплавленным металлом, допрессовка или калибровка спеченного полуфабриката, дополнительная механическая обработка спеченных изделий и т.д.
Достоинства порошковой металлургии следующие:
возможность изготовления деталей из тугоплавких материалов, псевдосплавов (например, медь — вольфрам, железо — графит), пористых материалов с заранее заданной пористостью (фильтры, самосмазывающиеся подшипники);
значительная экономия материалов в связи с возможностью прессования изделий с окончательными размерами, не нуждающихся (или почти не нуждающихся) в последующей механической обработке; отходы производства в этом случае не превышают 1—5 %;
возможность получения изделий из материалов высокой чистоты, так как при изготовлении деталей методом порошковой металлургии (в отличие от литья) исключается внесение каких-либо загрязнений в перерабатываемый материал;