Переработка шлаков и безотходная технология в металлургии
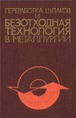
М.И Панфилов, Я. Ш. Школьник, Н. В. Орининский, В. А. Коломиец, Ю. В. Сорокин, А. А. Грабеклис
Металлургия, 1987 г.
Основу металлургических шлаков составляют оксиды CaO, SiO2, MgO и FeO. Повышенное содержание SiO2 в шлаках приближает их к кислым, а извести — к основным. По содержанию оксидов железа, в частности FeO, шлаки разделяют на окислительные и восстановительные. Значительное количество FeO делает шлак окислительным. Металлургические шлаки являются сложными системами, в которых присутст¬вуют также оксиды Мп, Ва, Сг, Р. Кроме FeO, шлаки содержат и высшие оксиды железа Fe3O4 и FeaO,. Сера в шлаках находится в виде сульфидов или сульфатов Са, Мп и Fe. В отдельных случаях шлаки содержат оксиды Ti, В, V и ряд других соединений. Оксиды, входящие в шлак, разделяют на три группы: кислотные (SiO3, P2O5, SO2, SO4), образующие с основными оксидами соответственно силикаты, фосфаты и сульфаты; основные (CaO, MgO, FeO), образующие с кислотными оксидами соответствующие соли; амфотерные (Аl2O3), которые в зависимости от содержания других компонентов ведут себя и как кислотные, и как основные. В шлаках наиболее важным кислотным оксидом является SiO2. Металлургические шлаки обычно представляют сплавы основных оксидов с SiO,, которые составляют преимущественно силикатные образования и потому их иногда классифицируют по величине отношения числа атомов кислорода, содержащегося в SiO2, к числу атомов кислорода, входящего в основные оксиды. Для характеристики доменных шлаков широко применяют отношение CaO/SiOa. Но в связи со значительным содержанием А12О3 и MgO в шлаке используют также отношения (CaO + MgO)/SiO2; (CaO + MgO)/(SiO3 + Аl2О3) и другие, более сложные. Изучение свойств многокомпонентной системы представляет большие трудности, поэтому такую систему условно сводят к трех- или четырех компонентной. Результаты исследований трех компонентной системы пополняют сведениями о вли¬янии на нее других компонентов. Металлургические шлаки разделяют по видам выплавляемого металла на доменные, мартеновские, конвертерные, электросталeплавильные, ферросплавные, ваграночные. Их можно объединить в две группы: шлаки первичных металлургических процессов — доменные и ферросплавные, шлаки вторичных процессов — сталеплавильные и ваграночные. 1. Состав шлаков и их классификация Основу металлургических шлаков составляют оксиды CaO, SiЩO2, MgO и FeO. Повышенное содержание Si02 в шлаках приближает их к кислым, а извести — к основным. По содержанию оксидов железа, в частности FeO, шлаки разделяют на окислительные и восстановительные. Значительное количество FeO делает шлак окислительным. Металлургические шлаки являются сложными системами, в которых присутствуют также оксиды Мп, Ва, Сr Р. Кроме FeO, шлаки содержат и высшие оксиды железа FeSO4 и Fe2O,. Сера в шлаках находится в виде сульфидов или сульфатов Са, Мgи Fe. В отдельных случаях шлаки содержат оксиды 71, В, V и ряд других соединений. Оксиды, входящие в шлак, разделяют на три группы: кислотные (SiO2, P2Os, S03, S04), образующие с основными оксидами соответственно силикаты, фосфаты и сульфаты; основные (CaO, MgO, FeO), образующие с кислотными оксидами соответствующие соли; амфотерные (А12 О3), которые в зависимости от содержания других компонентов ведут себя' и как кислотные, и как основные. В шлаках наиболее важным кислотным оксидом является SiO2. Металлургические шлаки обычно представляют сплавы основных оксидов с SiO2, которые составляют преимущественно силикатные образования и потому их иногда классифицируют по величине отношения числа атомов кислорода, содержащегося в SiO2, к числу атомов кислорода, входящего в основные оксиды. Для характеристики доменных шлаков широко применяют отношение CaO/Si02. Но в связи со значительным содержанием А12O3 и MgO в шлаке используют также отношения (CaO + MgO)/Si02; (CaO + MgO)/(Si02 + А12О3) и другие, более сложные. Изучение свойств многокомпонентной системы представляет большие трудности, поэтому такую систему условно сводят к трех- или четырехкомпонентной. Результаты исследований трехкомпонентной системы пополняют сведениями о влиянии на нее других компонентов. Металлургические шлаки разделяют по видам выплавляемого металла на доменные, мартеновские, конвертерные, электросталеплавильные, ферросплавные, ваграночные. Их можно объединить в две группы: шлаки первичных металлургических процессов — доменные и ферросплавные, шлаки вторичных процессов — сталеплавильные и ваграночные. Доменные шлаки. Шлакообразование является одним из важнейших процессов, протекающих в доменной печи и определяющих ее работу. Выход доменного шлака, его состав и свойства зависят от химического и минералогического состава пустой породы железных руд, золы кокса, содержания серы в шихте, характера процесса восстановления и теплового состояния печи, а также от марки выплавляемого чугуна [4]. Удельный выход доменного шлака на отдельных предприятиях колеблется в широких пределах. Однако почти во всех доменных цехах выход шлака снижается в результате использования все более богатого железорудного сырья и частичной замены кокса низкозольными видами топлива. В среднем по доменным печам СССР удельный выход шлака снизился с 725 в 1960 г. до 440 кг/т чугуна в 1984 г. При производстве чугунов определенного вида и постоянстве состава сырья для данного завода, а также при ровном ходе печи химический состав шлака остается сравнительно стабильным. Большинство доменных шлаков характеризуется основностью (CaO/Si02) в пределах 1,0—1,2 и содержанием, %: MgO и Аl203 соответственно 3—20 и 5—15; S 0,5—3; Fe 0,1—1 и МgО 0,2—3. В жидких шлаках содержится некоторое количество растворенных газов. Температура шлака при выходе из доменной печи 1450-1550°С. При высоком нагреве печи основность шлака увеличивается в результате восстановления и перехода в чугун большего количества Si. При холодном ходе печи основность шлака снижается с уменьшением степени восстановления Si. Застывший основной шлак в изломе имеет светлую матовую камневидную поверхность. Количество FeO в нем при высоком нагреве печи резко уменьшается, железо почти полностью восстанавливается и переходит в чугун. В кислых и низкотемпературных шлаках содержится сравнительно много FeO. В изломе такой шлак блестящий, стекловидный, серого цвета с переходом в черный. При горячем ходе печи образуется жидкоподвижный шлак, при выпуске которого выделяется много газов. В зависимости от соотношения CaO/Si02 или (CaO + MgO)/SiO2 шлаки можно подразделить на основные (преимущественно на заводах Юга) и менее основные, характерные для предприятий Урала и Сибири. С применением в шихте доменных печей офлюсованного агломерата и переходом на выплавку чугунов с более низким содержанием Мg и S на заводах Юга произошло повышение основности конечных шлаков по CaO/Si02 до 1,2-1,3 и по (CaO + MgO)/SiO2 до 1,3-1,35. Содержание AI2O3 и МпО в шлаках снизилось до 5,5—6,5 и 0,5—2,5 % соответственно, a MgO возросло до 3—5 %. Содержание Si02 в шлаках уменьшилось в связи с изменением состава пустой породы криворожских руд и снижением удельного расхода кокса. С использованием соколовско-сарбайских руд и исключением из шихты марганцевой руды состав шлаков ряда завода Урала и Востока изменился в сторону уменьшения содержания AI2O3 до 10—16,5 % и MgO до 0.2—1,0 %: На Череповецком металлургическом комбинате (ЧерМК) при выплавке низкосернистых чугунов содержание MgO составляет 10—12 %, отношение CaO/S»02 и (CaO + MgO) /Si02 соответственно 1 и 1,3. Западно-Сибирский металлургический комбинат (ЗСМК) работает на рудах с магнезиальной пустой породой и повышенным содержанием А!203. Содержание MgO в шлаках этого предприятия составляет 14—16 %, А1203 - до 18 %, отношение CaO/Si02 =0,82-f0,85. В шлаках Карагандинского металлургического комбината (КарМК) содержится до 4,6 % ВаО. При выплавке природно-легированного чугуна на Орско-Халиловском металлургическом комбинате (ОХМК) шлаки имели повышенное содержание А1203 (до 28 %). При плавке железистых бокситов на Пашийском металлургическо-цементном (ПМЦЗ) и Алапаевском металлургичес ом (АМЗ) заводах образуются высокоглиноземистые шлаки, содержащие, %: 46-50 Аl2О3, 7-10 SiO2 и 38-43 СаО. Выплавка ванадиевого чугуна из качканарских и кусинских титано-магнетитов сопровождается получением шлаков с содержанием 8—10 % ТiO2, 15-16 % А12O3 и отношением CaO/SiO2 = 0,95-М 15. На состав и выход шлака значительное влияние оказывает зола кокса. На предприятиях Урала и Востока в коксе содержится больше золы (11,2—12,1 %), чем на заводах Юга (9,5 %). Поэтому в первом случае зола кокса оказывает большее влияние на состав и количество шлака. На состав и количество шлака существенно влияет сера кокса, содержание которой в донецком коксе составляет 1,7—2,2 %, в коксе кузнецких и смеси кузнецких и карагандинских или печорских углей 0,4— 0,6 %. Сталеплавильные шлаки. Побочный продукт сталеплавильных процессов представляет собой расплав оксидов, образующихся при взаимодействии с кислородом примесей, содержащихся в чугуне и металлургическом ломе, компонентов ферросплавов, шлак ©образующих, вносимых в сталеплавильную ванну для корректировки состава, миксерного и доменного шлака, поступающих с чугуном, а также от футеровки плавильных агрегатов. Сталеплавильные шлаки обладают рафинирующим действием и очищают сталь от таких вредных примесей, как фосфор и сера. Одновременно с этим они защищают металл от окисления газовой фазой. В электрометаллургических процессах шлак дополнительно выполняет роль нагрузочного сопротивления. Находясь в плавильном агрегате в непрерывном движении, высокотемпературный расплав разрушает футеровку за счет механического размывания ее, а также за счет химического растворения компонентов футеровки. Известно, что всякая система стремится достичь равновесного состояния. В. результате этого из металла в шлак переходит ряд ценных, необходимых металлу элементов, что вызывает повышенный расход раскисляющих легирующих добавок. Кроме того, в шлаке запутывается определенное количество металла, что не только снижает общий выход годного металла, но и существенно затрудняет дальнейшую переработку шлака в продукцию, используемую в других отраслях промышленности и сельском хозяйстве. В связи с назначением шлаков и их функциями в сталеплавильных процессах к ним предъявляют определенные требования по физико-химическим свойствам. Как правило, сталеплавильные шлаки должны быть жидкоподвижными, обладать высокими рафинирующими способностями и низкой вязкостью, а также быть инертными или минимально агрессивными по отношению к футеровке печи. Учитывая, что объем производства стали в агрегатах с кислой футеровкой незначителен, в дальнейшем будут рассмотрены только основные шлаки. В настоящее время сталеплавильные шлаки классифицируют по видам производства стали (мартеновские, конвертерные и электросталелла вильные), а также по периодам плавки (первичные и конечные). Наибольшее количество шлаков сталеплавильного производства в стране составляют мартеновские, которые подразделяются на первичные (скачиваемые в процессе плавки после подачи в агрегаты чугуна) и конечные, выпускаемые из печи в конце плавки. Удельный выход мартеновских шлаков составляет в среднем 180 кг/т стали. Относительное количество первичных и конечных шлаков зависит от вида и массы подаваемого в мартеновскую печь чугуна и колеблется в довольно широких пределах (соответственно 50—70 и 30—50 %). Первичные мартеновские шлаки имеют более низкую основность (СаО + +MgO)/(Si02 + А1203), которая составляет 1—2 (основность конечных шлаков 2—4). Кроме того, первичные шлаки содержат повышенное количество оксидов железа (до 27 %) и фосфора (до 3,5 %) . Содержание оксидов фосфора в первичных шлаках на комбинате "Азовсталь" достигает 18 %. Удельный выход конвертерных шлаков составляет около 150 кг/т стали. От мартеновских шлаков они отличаются повышенным содержанием оксидов Са, Mg, Fe и более высокой основностью. Конвертерные шлаки меньше различаются между собой по составу и удельному выходу. В качестве исключения можно выделить конвертерные шлаки Карагандинского, Нижне-Тагильского и Череповецкого комбинатов. На Карагандинском металлургическом комбинате конвертерные шлаки, получаемые от переработки высокофосфористого чугуна, отличаются повышенным содержанием фосфора. Процесс осуществляется со скачиванием высокофосфористого первичного шлака, в котором P2Os может достигать 14 % при удельном выходе 84 кг/т стали, и выпуском конечного шлака с содержанием P2Os 3—6 %. Удельный выход конечного шлака составляет около 97 кг/т стали. При переработке ванадийсодержащих чугунов на НТМК образуются два вида шлака: ванадиевый (содержание ванадия достигает 9 %), представляющий собой полупродукт для получения ванадия, и "стальной", получаемый при производстве конвертерной стали. Выход этого шлака небольшой и составляет всего 5—7 % от выхода стали. Конвертерные шлаки Череповецкого металлургического комбината (ЧерМК) отличаются более высоким содержанием оксидов железа, поскольку комбинат перерабатывает низкомарганцовистые чугуны. Электросталеплавильных шлаков образуется значительно меньше, чем мартеновских и конвертерных. Как и мартеновские, они различаются на первичные и конечные, удельный выход которых в среднем составляет соответственно 6 и 8 %. Первичные электросталеплавильные и мартеновские шлаки сходны между собой по химическому составу, конечные отличаются более высоким содержанием оксидов кальция и низкой концентрацией оксидов железа. Составы конечных шлаков кислородно-конвертерного, мартеновского и электросталеплавильного производств несколько отличаются друг от друга по содержанию основных элементов. 4. Фазовый состав шлаков Доменные шлаки. В основных доменных шлаках преобладающими кристаллическими фазами является мелилит, представляющий твердый раствор окерманита 2 CaO-MgO-2Si02 и геленита 2 СаО А1203-Si02, а также двухкальциевый силикат 2 CaO . Si02. В кислых шлаках, кроме мелилита, содержатся волластонит 3 CaO-SiO2 и анортит СаО. Однако и в основных доменных шлаках возможно присутствие минералогических образований типа СаО - SiO2 или CaO -Al2O3 -2SiO2 и, наоборот, в кислых шлаках обнаруживают минералы с большим содержанием СаО, например 2 СаО- SiO2 и 2 СаО- Al2O3-SiO2- Алюминаты встречаются редко, только в сильно основных шлаках при низком силикатном модуле, и обнаруживаются главным образом в виде алюминатов кальция. Шпинель Mg0-AI2O3 встречается только в шлаках с повышенным содержанием MgO и глинозема. Доменные шлаки, особенно основные, содержат также серу в виде сульфидов, главным образом CaS, MnS, FeS, реже MgS. Минералогический состав доменных шлаков сильно изменяется в зависимости от их основности. Существенные изменения в минералогическом составе отмечают в шлаках, получаемых при выплавке чугуна из руд различных месторождений. С учетом особенностей шлака авторами систематизированы и сведены в табл. 4 основные минеральные фазы. За последние годы в доменных шлаках некоторых предприятий повысилось содержание MgO, а при выплавке титаномагнетитовых руд содержание ТЮ2 в шлаках достигает 10 %. Особенности изменения фазового состава этих шлаков при их охлаждении не нашли должного отражения в литературе. Для шлаков с высоким содержанием MgO весьма важным является вопрос о возможности кристаллизации в шлаках периклаза. Считается, что шлаки, в которых периклаз является первичной фазой, чаще всего имеют химический состав, лежащий близ границы фазы периклаза. В случаях, когда это не имеет места, температуры ликвидуса оказываются сравнительно высокими. Шлаки подобного состава не выполняют своих металлургических функций в доменном процессе, поскольку их действительная вязкость слишком высока при нормальной температуре доменного процесса. 1. Теоретические основы поризации шлаковых расплавов В основе технологии производства шлаковой пемзы лежит поризaция расплавленных доменных шлаков. Для получения пемзы с низкой объемной массой необходимо обеспечить сохранность их пенной структуры до затвердевания, точнее до густолластичного состояния. 6 момент своего образования шлаковая пена представляет собой метастaбильную многофазную неравновесную систему, в состав которой входит оксидный шлаковый расплав и газовые включения в виде пузырьков различной величины. Пена, как и любая дисперсная система, является агрегативно неустойчивой. Нестабильность пены объясняется наличием избытка поверхностной энергии, пропорциональной поверхности раздела фаз жидкость — газ. Стабильность пен изучали многие отечественные и зарубежные исследователи. Выдвинуто несколько теорий, объясняющих устойчивость пен. Однако эти теории не исключают, а скорее взаимно дополняют друг друга, рассматривая процесс стабилизации пен в различных условиях. Чистые жидкости не способны образовывать сколько-нибудь устойчивую пену. Для получения пены в жидкой фазе, кроме растворителя, должен находиться, по крайней мере, один поверхностно-активный компонент — пенообразователь, адсорбирующийся на межфазной поверхности. Стабилизация пленок пенообразователями обусловлена кинетическим, термодинамическим (расклинивающим давлением) и структурно-механическим факторами.