Исследование свойств металлургического кокса
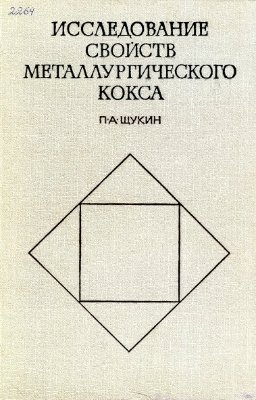
Щукин П. А.
Металлургия, 1971 г.
Прежде на коксохимических и металлургических заводах отбор пробкокса для различных испытаний производили вручную вилами и лопатами. Пробы отбирали от сменной выработки малыми порциями через определенные интервалы времени из железнодорожных вагонов или из насыпной массы, лежащей на движущихся транспортерах. Выполненные экспериментальные работы, однако, показали, что при применении такого метода необходимая точность определения физико-механических, химических и физико-химических свойствкокса не достигается. Для правильного технического контроля за производством металлургического кокса, естественно, необходимо выяснить происхождение различия показателей оценки качества кокса в действительности и на основании взятой пробы. При изучении этого вопроса выяснилось, что, несмотря на одинаковый исходный состав угольной шихты, при неравных тепловых условияхкоксования по высоте и ширинекамер куски кокса получаются различной крупности, обладают отличной друг от друга прочностью, выходом летучих веществ и другими свойствами. В связи с этим стало ясно, что надежным признаком, обусловливающим нужную согласованность качества кокса в партии и во взятой от нее пробы, может и должно служить одинаковое соотношение кусков кокса по крупности. Установленное правило, однако, само по себе не давало еще практических результатов. Нужен был метод, пользуясь которым можно гарантировать согласование ситового составакокса в пробе и партии, отправляемой потребителю. Многие исследователи в нашей стране и за рубежом пытались решить эту задачу путем усовершенствования ручного способа отбора проб кокса. Но, несмотря на большие усилия, в этом направлении положительных результатов до настоящего времени получить не удалось. Чтобы убедиться в несостоятельности такого совершенствования, рассмотрим явления, происходящие при отборе пробкокса ручным способом. Разделкапроб для технического анализа может быть также представлена в виде новой, более рациональной схемы. Учитывая высокую точность результатов при применении принципа пропорционального отбора малых порций от первичных больших проб, совершенно нецелесообразны отбор и трудоемкая Разделка 250 кг кокса для технического анализа. В этом случае порция коксамассой 25 кгу взятая из единой первичной пробы в 300—500 кг пропорционально ее гранулометрическому составу, по всем свойствам будет давать результаты не с меньшей, а с большей степенью точности, чем отдельно взятая проба от партии массой 250 кг. Новая схемаразделкипроб на технический анализ более проста (рис. 4). Вместо пятикратного в этом случае предусматривается трехкратное дробление и двукратное квартование при объеме кокса, меньшем в 10 раз. В результате проведенных исследований можно констатировать следующее. Новая система технического контроля направлена на уменьшение объема работ, сбережение металлургического кокса, улучшение условий труда пробоотборщиков. Она создаст возможность расширить круг испытаний на базе единой первичной пробы и повысить точность определений физико-механических, физико-химических и химических свойств металлургического кокса. Вне доменной печи кокс подвергается только механическому, а внутри ее одновременно механическому, термическому и химическому воздействиям. На разных стадиях перемещения к доменному цеху на разрушение кокса затрачивается различное количество энергии, которая складывается из энергий, расходуемых на дробление, трение и сжатие. Когда кокс надает в железнодорожный вагон, в бункер, в силос, на передаточный желоб, на конус, на засыпь домны он подвергается главным образом воздействию дробящих усилий. Во время прохождения бункера и силоса, а также внутри доменной печи на него больше всего действуют силы сжатия, скалывания, излома и трения. На наших заводах существуют различные системы коксоподачи. Они различаются по числу и высоте падений кокса, по конструктивному оформлению, техническому состоянию и другим особенностям. Все многообразие этих условий отражается на ситовомсоставе кокса. Реакционная способность твердых топлив Под реакционной способностью твердых топлив понимается активность их к реакции СОг+С-»-2СО. Эта реакция начинается при таких температурах, когда скорость обратной реакции 2СО-*-С02+С практически ничтожно мала. Например, Рид и Уиллер нашли, что при 850° С скорость обратной реакции в 166 раз меньше прямой и что с повышением температуры это отношение возрастает. Н. В. Лавров исследовал скоростигорения угля и восстановления СО2. Для опытов использовали угольные стержни диаметром 5,5 мм и длиной 156 мм, которые помещали пучками в кварцевую трубкудиаметром 41 мм, обогреваемую электрическим током. Температура опытов изменялась от 900 до 1200° С, скоростьдутья составляла 8 м/сек. В. С. Альтшулер [92] по той же методике изучал скоростиреакциивосстановления С02 при применении пучков электродного угля диаметром от 5,5 до 12 мм и длиной от 60 до 200 мм. При этом определялось влияние различных концентраций С02 при температурах угля 1000 и 1100° С. Была проведена серия опытов, в которых температура угля изменялась от 800 до 1100° С. В этом случае истинная линейная скорость газового потока составляла от 0,1 до 10 м/сек. По методике Н. В. Лаврова оказалось возможным достаточно точно определить скоростьвосстановления С02 на единицу поверхности угля в зависимости от скоростидутья и температуры поверхности. Под руководством профессора В. И. Блинова Н. М. Савинов изучал скоростиреакции на поверхности сферической частицы электродного угля диаметром 15 мм, смываемой потоком С02 в электрической печи при температуре от 743 до 927° С. скоростьреакции определяли по снижению массы угля, пользуясь весами специальной конструкции. Необходимо отметить, что скоростиреакциивосстановления двуокиси углерода, полученные различными исследователями, неодинаковы и отличаются от тех, которые наблюдались в вакууме. Очевидно, здесь большую роль играет внутренняя поверхность топлив, а также их структурные особенности и каталитический характер минеральных примесей. На реакцию восстановления С02 влияет процесс диффузии. Роль диффузионного процесса в реакциивосстановления углекислоты особенно глубоко изучали А. С. Предводителев и О. А. Цуханова [93—95]. Указанные авторы провели многочисленные опыты с угольными трубкамидиаметром 7 мм и длиной 270 мм из электродного угля. Температура угля изменялась от 800 до 1400°С, а концентрация С02 — от 8 до 96,5% при истинных скоростях газа от 1 до 13 м/сек. В результате было установлено, что скоростьвосстановления С02 зависит от состояния реагируемой поверхности. По мере разрыхления поверхностискоростьвосстановления увеличивается, но, достигнув определенного состояния разрыхления (на глубину несколько менее 3 мм), стабилизируется. скоростьвосстановления С02 возрастает пропорционально первой степениконцентрации углекислоты. Таким образом, промышленные коксы начинают реагировать •с СОг только при температурах выше 800° С. Более того, в температурном интервале от 740 до 1130° С больших различий в реакционной способности разных коксов не наблюдается. Коксы, полученные в лабораторной печи из типовой угольной шихты Донбасса с добавками железной руды и мела, являются наиболее реакционноспособными топливами. Кокс, полученный из какого-либо определенного угля с углекислотой, реагирует при пониженных температурах, но при 1040—1130° С реакция проходит так же, как в промышленных условиях, что объясняется их повышенной пористостью. Предварительная термическая обработка образцов промышленного кокса, древесного угля и антрацитаприводит к понижению их реакционной способности. По мере повышения температуры в доменной печи реакционная способность топлив возрастает, но при 1130° С еще не достигает предельного значения. Для доменных печей нужно топливо с умеренной реакционной способностью, тогда будут обеспечены оптимальные размеры зон горения и расходуглерода на единицу выплавляемого металла. Крупность кокса значительно влияет на размерыкислородной и восстановительной зон. По мере ее увеличения зона горения увеличивается. При этом максимальное содержание СОг в газе уже наблюдается дальше от устья истечения дутья, а средняяТемпературагорения слоя повышается. Различия физических и физико-химических свойств топлив существенным образом влияют на характер процессагорения в воздушном дутье. Температурагорения кускового антрацита в слое выше, чем у кокса, и тем более чем у древесного угля. Древесный уголь по отношению к кислороду обладает наибольшей, а антрацит — наименьшей горючестью. кокс по горючести занимает промежуточное положение. Увеличение концентрациикислорода в дутье влечет за собой сокращение кислородной и восстановительной зон и повышает температуругорения топлив. В ряду многочисленных свойств доменного кокса равномерность по размеру кусков является одной из самых существенных характеристик. Чем больше равномерность кокса по крупности, тем выше его качество, тем вероятней всего можно ожидать наиболее высоких технико-экономических результатов работы доменных печей. Увеличение в составе рядового металлургического кокса содержания очень крупных (>80 мм) и мелких кусков (<40 мм) понижает его качество и влечет за собой ухудшение работыдоменной печи. До настоящего времени для улучшения качества кокса употребляют дефицитные коксующиеся угли марок Ж, К и ОС. До некоторой степени та же цель достигалась обогащением и подготовкой углей, а также регулированием теплового режима коксовых печей. В последнее время исследователи прежде всего занимаются усреднением углей, а также их избирательным дроблением, так как это наиболее эффективные способы улучшения качества кокса. И тем не менее нельзя отрицать того, что действенность всех этих факторов по сравнению с равномерностью кокса по крупности все же сравнительно незначительна. В рядовом металлургическом коксе всегда содержится большое количество мелких и крупных классов. Соотношение этих классов после выдачи кокса из печей не остается постоянным и в процессе транспортировки изменяется. Таким образом, для рядового металлургического кокса характерна не только исходная неравномерность по крупности, но и непрерывное ее изменение.