Сталь для магистральных трубопроводов
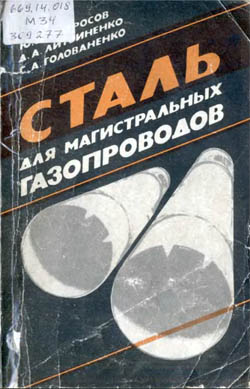
Матросов Ю.И. Литвиненко Д. А., Голованенко С.А.,
Металлургия, 1989 г.
Глава II. НОРМАЛИЗОВАННЫЕ И ГОРЯЧЕКАТАНЫЕ СТАЛИ
НА ОСНОВЕ ТВЕРДОРАСТВОРНОГО И
КАРБОНИТРИДНОГО УПРОЧНЕНИЯ ДЛЯ ТРУБ БОЛЬШОГО ДИАМЕТРА
Разработка новых конструкционных материалов осуществлялась поэтапно по мере изменения технических требований к металлу, совершенствования оборудования и технологических параметров производства на металлургических и трубных заводах.
Низколегированные стали, относящиеся к первому поколению сталей для газопроводных труб большого диаметра, содержали в качестве основных легирующих элементов марганец и кремний, образующие с железом твердые растворы замещения. Степеньупрочнения от легирования указанными элементами в пределах, не допускающих существенного ухудшения пластичности, вязкости и свариваемости, относительно невелика. На низколегированных сталях подобного типа достигли уровень прочности 500 - 520 Н/мм2 в сочетании с удовлетворительной пластичностью. Температура их эксплуатации составляет (0) (-5)°С. В дальнейшем строители газо-нефтепроводных магистралей выдвинули требования о создании сварных труб большого диаметра, сначала диаметром 1020 - 1220 мм, позднее диаметром 1420 мм, с более высокой прочностью - до. Н/мм2 и существенно более стойких к низким температурам (температура строительства -60 °С и эксплуатации -15 .°С).
Основные легирующие элементы (углерод, марганец, кремний)
оказывают монотонно упрочняющее влияние, причем интенсивность влияния углерода выше (0,1 % С повышает прочность на 40 Н/мм2), чем у марганца и кремния ( 20 Н/мм3). При повышенном содержании углерод выделяется в виде карбидной фазы [3]. углерод оказывает значительно большее влияние на временное сопротивление, чем на предел текучести. При содержании углерода более 0,25 % наблюдается обратная тенденция и зерно феррита несколько укрупняется. Повышение содержания углерода сопровождается уменьшением значений ударной вязкости при комнатной и минусовых температурах, повышением порога хладноломкости. При содержании углерода более 0,23 % наблюдается существенное повышение порогахладноломкости стали. Такое влияние углерода на ударную вязкость и хладостойкостьстали следует объяснить тем, что в определенных условиях превалирует фактор повышения количества перлита, а в других - измельчения зерна. Чаще наблюдается проявление неблагоприятного влияния повышенного количества перлита. Степень влияния перлита на повышение переходнойтемпературы зависит также от величины зерна стали: с ее уменьшением усиливается Степень влияния перлита на переходную температуру. Отсюда следует, что использование сталей с низким содержанием углерода при наличии крупнозернистой структуры в отношении переходнойтемпературы менее эффективно, чем в сталях с мелкозернистой структурой, в которых снижение содержания углерода сопровождается понижением переходимой температуры. В сталях с очень низким содержанием углерода критическая Температурахрупкости зависит от формы и характера Распределения перлитной составляющей. Обычно снижение содержания углерода до низкого уровня (0,05 % и ниже) в марганцовых горячекатаных сталях сопровождается существенным сдвигомпереходнойтемпературы в сторону более низких температур.
уровень механических свойств зависит от сочетания легирующих микролегирующих элементов, а также условий проведения операции нормализации. В горячекатаном состояниисталь характеризуется дисперсной феррито-перлитной структурой с резко выраженной перлитной полосчатостью с участками бейнитной составляющей (рис. 16). Средний балл ферритного зерна составляет 11 по ГОСТ 5639-82. Перлит располагается преимущественно в полосах. Микротвердостьферрита 1980 Н/мм2.Нормализация сопровождается существенным изменением микроструктуры: уменьшается перлитная полосчатость, зерна феррита приобретают равноосную форму и измельчаются до 12-го балла. Микротвердостьферрита снижается до 1880 Н/мм2. Количество бейнитной составляющей уменьшается и сохраняется только в центральных зернах. Уменьшается количество выделенийцементита по границам зерен феррита и увеличиваются размерыперлитных зон.
Изучением тонкой структурыметодами экстракционных реплик и трансмиссионной электронноймикроскопии установлено, что в горячекатаном состоянии перлит имеет грубопластинчатую форму (рис. 16, г), количество выделений дисперсных частиц округлой формы (размер 10-30 нм) незначительно. Электронографическим анализом показано, что эти частицы - карбонитриды ванадия. Цементитные пластины в перлитныхполосах утоняются. Наблюдается процессочисткиграниц зерен от выделений цементита. Количество выделившихся частиц карбонитридаванадия увеличивается; они становятся несколько крупнее 10 - 60 нм (рис. 16, е). Плотностьдислокаций снижается до 1,4 •10-10 см-1. В ферритных зернах начинается процесс формирования субзеренной структуры - примерно в объеме 5 -10 % зерен (рис. 16, ж).
Положительное влияние ниобия, ванадия и титана на механических свойства и сопротивление хрупкому разрушению низколегированных сталейсвязано в значительной степени с измельчением зеренной структуры при введении их небольших добавок. Важным механизмомизмельченияструктуры при микролегировании является торможение роста зерна аустенита при нагреве. Присутствие труднорастворимых частиц избыточной фазы тормозит огрубление зерна аустенита при нагреве благодаря взаимодействию их с границамиаустенитных зерен. При этом происходит поглощение энергии движущихся границ на огибание частиц Движениеграниц зерен по отношению к частицам второй фазы приводит к локальному росту энергии и тормозит миграцию границ Энергия, расходуемая на преодоление барьеров, должна быть возмещена из другого источника, например из энергии, освобождающейся в результате роста зерна. Мелкие частицы более эффективно, чем грубые, сдерживают рост зерна. Максимальный размер частиц, которые противодействуют движениюграницаустенита со средним радиусом зерна R0, можно определить по формуле [20]: