Термомеханическая обработка металлов и сплавов. Т.1.2
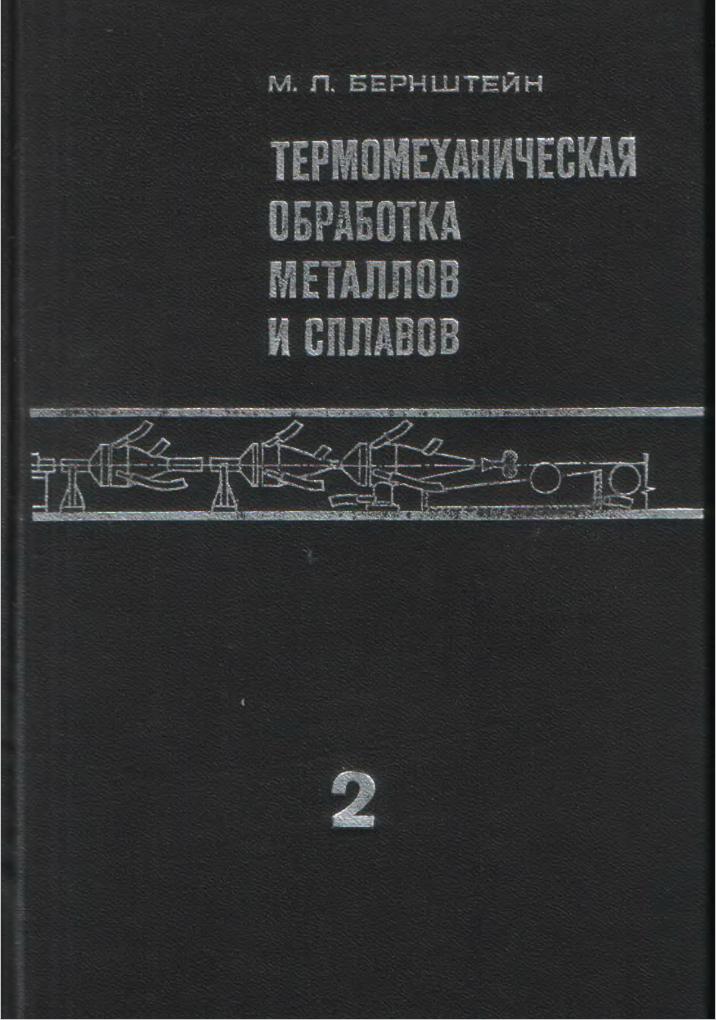
Бернштейн М.Л.
Металлургия, 1968 г.
Высокотемпературная термомеханическая обработка (ВТМО) стали представляет сочетание нагрева на температуры, отвечающие области стабильного аустенита, деформации (после определенной выдержки в аустенитной области) и немедленной закалки на мартенсит (рис 57) Обычная заключительная операция — низкий отпуск Такая обработка приобрела в последние годы сравнительно широкое распространение (особенно в СССР) в связи с необходимостью повышения механических свойств массовых сортов стали, применяемых в современном машиностроении.
Рис 57 Технологическая схема ВТМО 1, 2—начало изотермического распада недеформированного и деформированного аустенита соответственно
Температура проведения деформации при ВТМО лежит обычно выше верхней критической точки Аса, поэтому неизбежны попытки проведения аналогии между ВТМО и термической обработкой с прокатного (ковочного) нагрева. Совмещение горячей обработкиметалловдавлением с термической обработкой изучали сравнительно давно, однако рассматривали его главным образом, как средство уменьшения затрат на повторный нагрев под закалку или нормализацию. Принципиальное отличие ВТМО от термической обработки с прокатного (ковочного) нагрева заключается в создании таких условий высокотемпературной пластической деформации и последующей закалки, при которых подавляется развитие рекристаллизационных процессов и создается особое структурное состояние, характеризующееся повышенной плотностью несовершенств и особым их расположением с образованием разветвленных субграниц. Отсюда и большая мозаичность строения стали после ВТМО.
В связи с возможным влиянием ориентированности элементов субструктуры на конечное строение стали после закалки важным является выбор оптимального вида деформации при термомеханической обработке конкретных деталей — вопрос, которому до сих пор уделяется недостаточное внимание.
Из этих данных следует несомненное преимущество НТМО в смысле достижения более высоких прочностныхсвойств и преимущество ВТМО — в смысле достижения более высокой пластичности. Однако достаточно объективно сравнить полученные после ВТМО и НТМО свойства невозможно, так как различна методикаиспытаний и велик разброс получаемых значений, а главное исследования проводились на различных (несопоставимых) марках стали и при сильно различающихся степенях обжатия. Объектом НТМО являются в основном средне- и высоколегированные стали, подвергающиеся обжатию на 70—90%, а объектом ВТМО — углеродистые и низколегированные (в некоторых случаях — среднелегированные), деформация которых в большинстве случаев составляла 25—60%.
Термомеханическая обработкаприводит к повышению механических свойств не только при статическом, но и при знакопеременном нагружении: существенно возрастают усталостные характеристики, особенно циклическая прочность в зоне перегрузок (при ограниченной выносливости). В результате ВТМО значительно (в 1,5—3 раза) повышается ударная выносливость стали (чего не наблюдается после НТМО). Что касается ударной вязкости, то, как впервые было показано в известныхработах В. Д. Садовского с сотр., в результате ВТМО (в отличие от НТМО) практически устраняется развитие обратимой отпускнойхрупкости в опасном интервалетемператур отпуска, ослабляется необратимая отпускнаяхрупкость и резко повышается ударная вязкость при комнатной и низких температурах 1. После ВТМО сильно снижается температурныйпорог хладноломкости, причем переход к хрупкому разрушению в случае стали, подвергнутой ВТМО, сопровождается не междузеренным разрушением, а разрушением по телу зерна с сохранением такого характера излома до температур глубокого охлаждения (до —196" С).
ВТМО обусловливает повышение хрупкой прочности стали, а также уменьшение чувствительности к образованию трещин при термической обработке
НТМО не приводит к заметному подавлению отпускнойхрупкости стали, а ВТМО позволяет резко ослабить проявление хрупкости в опасном интервалетемператур отпуска. Поэтому значительный интерес представляет предложенная в нашей стране следующая комбинированная схема: ВТМО (для подавления охрупчивания стали) и НТМО (для резкого повышения прочности). Осуществление этой комбинированной обработки на стали 37ХНЗА привело к существенному увеличению ударной вязкости в интервале развития обратимой хрупкости по сравнению с ее значениями после НТМО (более чем в три раза). Что касается свойствпрочности и пластичности, то они по крайней мере равны свойствам, полученным после НТМО с той же степенью обжатия.
Сопоставляя НТМО и ВТМО (используя обычно в качестве критерия получаемые механические свойства), отмечают ряд их преимуществ и недостатков.
Низкотемпературная термомеханическая обработка, во-первых, обеспечивает получение более высоких свойствпрочности и предела выносливости, чем ВТМО и, во-вторых, в связи с отсутствием опасности рекристаллизации создает возможность применения разнообразных методов пластического деформирования, в том числе с малой скоростью (обычно наиболее желательной для создания оптимальной структуры), но в пределахустойчивости переохлажденного аустенита. Однако эта обработка:
а) не снижает склонности стали к отпускной хрупкости,
б) связана с необходимостью подстуживания, что усложняет технологическую схему и требует использования дополнительного термического оборудования,
в) требует применения более высоких (по сравнению с ВТМО степенейобжатия (75—95%), причем в условиях повышенного сопротивленияаустенита пластической деформации при температурах промежуточной области; это обусловливает необходимость создания и применения новых мощных деформирующих устройств;
г) пригодна лишь для средне- и высоколегированных сталей с высокой устойчивостью аустенита, причем, как указывалось на стр. 650, необходимо учитывать, что деформированиеаустенитарезко уменьшает его устойчивость в бейнитной области.
Недостатки ВТМО следующие:
а) процессы типа рекристаллизационных, неизбежно происходящие при ВТМО, снижают эффект упрочнения;
б) в связи с возможной интенсивной рекристаллизацией за счет внутреннего тепла ВТМО применима лишь для изделий определенной толщины.
В то же время ВТМО имеет и ряд преимуществ:
а) устраняет отпускную хрупкость;
б) одновременно с упрочнением определяет существенное (и большее, чем после НТМО) повышение свойств пластичности; вернее, в связи с увеличением пластичности удается реализовать высокую прочность закаленной стали после низкого отпуска,
в) не требует специального термического и, главное, деформирующего оборудования, так как обработка может быть осуществлена в процессе нормального технологического цикла горячего деформирования (прокатка, штамповка и т. п.), тем более что применяемые обжатия невелики, а сопротивление деформации аустенита при температурах выше критической точки невысокое; это, однако, не означает, что можно использовать обычные существующие в цехах режимы деформации, например горячей прокатки; необходимо корректирование температуры нагрева и темпов прокатки (последнее — для возможности осуществления последующего немедленного закалочного охлаждения);
г) определяет повышение механических свойств углеродистых, низко- и среднелегированных сталей.
ВТМО — более технологичная схема обработки, чем НТМО, и ее можно без больших трудностей использовать для получения лучшего сочетания высоких значений прочности и пластичности широко применяемых машиностроительных сталей
Однако следует подчеркнуть неправомерность такого, имеющего характер противопоставления сравнения этих двух обработок, в основе которых лежат, вероятно, несколько различные механизмы упрочнения. Так, после НТМО получают более высокую плотностьдислокаций и более напряженные их конфигурации, чем после ВТМО. Последняя обусловливает меньшую, чем после НТМО, плотностьдислокаций (но большую, чем после обычной закалки), причем в результате рекомбинации при высокой температуре образуются и иные, более устойчивые дислокационные построения. Поэтому ту или иную схему термомеханической обработки (а число их вариантов определяется, в частности, многообразием возможных превращений) следует выбирать в зависимости от природы и назначения сплава.
Естественно, эффективность упрочняющей обработки следует оценивать по комплексу механических свойств. Когда в современной технике говорят о повышении прочности, то под этим понимают в широком смысле повышение сопротивлениядеформации и разрушению в различных напряженных состояниях, в том числе и таком, которое может вызвать образование хрупкой трещины, преждевременного разрушения и др. Само собой разумеется, что необходимым условием обеспечения прочности является определенный запас пластичности и вязкости, характеристикипластичности и вязкости представляют как бы составные элементы прочности при действительно физической трактовке этого термина. Очевидно, что понятие прочности никогда не может исчерпываться только такими характеристиками, как пределпрочности или предел текучести. Поэтому представляется необходимым проводить сравнение эффективности различных упрочняющих обработок не по приросту пределапрочности (текучести), а по комплексу механических свойств, в том числе по порогу хладноломкости, хрупкой прочности, работеразрушения и др.
РЕКРИСТАЛЛИЗАЦИЯ В процессе ВТМО
При сравнении ВТМО и НТМО часто подчеркивают, что при использовании первой схемы трудно предотвратить развитие рекристаллизации при высоких температурах, в связи с чем необходимо принятие ряда специальных технологических мер.
Несомненно, развитие рекристаллизационных явлений, особенно на стадиях собирательной или вторичной рекристаллизации, в процессе упрочняющих обработок недопустимо. Однако когда говорят о создании высокопрочного состояния металлических сплавов, пригодных для технического использования, имеют в виду, что эти сплавы должны обладать одновременно высокой прочностью и пластичностью (см. выше).
Такие стадии перестройки дислокационной структуры под влиянием нагрева, как «рекристаллизация на месте», или самые начальные этапы рекристаллизацииобработкисвязаны с созданием тонкого субзеренного строения. При этом пластичность возрастает в связи со снятием в определенной степени напряженного состояния, характерного для наклепанной структуры и одновременно сохраняется высокий уровень прочности в связи с общим измельчением структуры.
Следовательно, для получения оптимального сочетания механических свойств после ТМО следует проводить наклепаустенита до закалки в условиях, когда одновременно с увеличением плотностидислокаций происходит их перестройка, лучше всего по типу полигонизации. Тогда мартенситноепревращение идет не только в измельченной исходной структуре с высокой плотностьюдислокаций (что определяет повышение прочности), но и в структуре, характеризующейся более равномерным распределением дислокаций (меньшей концентрацией напряжений), благодаря чему закаленный высокопрочный металл отличается также и повышенной пластичностью. Иными словами, для получения высокого комплекса механических свойств важна не только определенная высокая плотность дислокаций, но и оптимальная их конфигурация (распределение).
В связи со всем сказанным закономерен вопрос, можно ли вообще считать способным к длительной и надежной службе металл, в структуре которого зафиксировано то расположение несовершенств строения, которое создано наклепом? Известно, что уже при деформации в несколько процентов возникает крайне неравномерное распределение несовершенств, характерное для так называемой ячеистой структуры. Такая неравномерность обусловливает высокую напряженность металла, весьма малый запас пластичности и большую склонность к хрупкому разрушению. Отсюда очевидно, что наклепанный металл, в котором не прошла хотя бы частичная перестройка дислокационной структуры, мало пригоден для использования в конструкциях, работающих в условиях разнообразного и длительного нагружения. По-видимому, и в случае НТМО происходят явления, близкие к полигонизации (возврату), о чем свидетельствует наличие некоторого запаса пластичности после этой обработки. Это подтверждается также повышением механических свойств в результате НТМО, проводимой с медленной деформацией или в случае дробной деформации, или при некоторой выдержке при изотерме (но не до распада) перед закалкой, или (как в опытах С. И. Сахина и О. Г Соколова) в случае кратковременного высокотемпературного нагрева при дробной деформации.