Коррозионное растрескивание и защита высокопрочных сталей
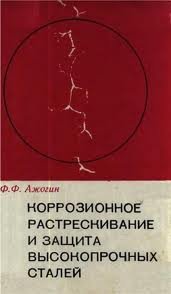
Ажогин Ф.Ф.
Металлургия, 1974 г.
СОСТАВ И СВОЙСТВА ВЫСОКОПРОЧНЫХ СТАЛЕЙ
Высокопрочными конструкционными сталями называют стали, термически обрабатываемые на прочность 1400 МН/м2 (140 кгс/мм2) и выше.
При содержании 0,45% С после закалки и низкого отпуска можно достичь прочности стали —2200 МН/м2 (—220 гс/мм2), но такая сталь обладает низкой пластичностью и вязкостью. С дальнейшим увеличением количества углерода прочность при разрыве закаленной и низкоотпущенной стали не увеличивается, а уменьшается при одновременном снижении пластичности и вязкости.
Необходимые значения вязкости и пластичности, а также прокаливаемость высокопрочной конструкционной стали достигаются легированием хромом, никелем, кремнием, марганцем я некоторыми другими элементами. Со¬держание вредных примесей — серы и фосфора должно быть минимальным.
Впервые высокопрочная сталь с определенным комплексом механических свойств была создана в СССР. В 1949 г. под руководством С. Т. Кишкма была разработана сталь ЗОХГСНА, содержащая 0,30% С. Отличи¬тельной особенностью стали ЗОХГСНА является сочетание хрома, марганца и кремния в пределах 1% каждого я 1,6 % Ni, что позволяет получать благоприятное сочетание свойств прочности, пластичности и вязкости. Максимальная прочность этой стали 1600—1800 МН/м2 (160—180кгс/мм2) при удовлетворительной пластичности и вязкости обеспечивается закалкой и низким отпуском .три 200—300"С. Сочетание легирующих элементов позволяет получать после изотермической закалки при высокой прочности, 0В= 1400ч-1800 МН'м2 (140— 180 кгс/мм2), высокую вязкость. Повышение температуры изотермической закалки до 300°С приводит к росту у «арной вязкости до 1,0 МН-м/м2 (10 кгс-м/см21; дальнейшее повышение температуры изотермической закалки резко уменьшает ударную вязкость, вследствие чего изотермическая закалка при температуре >330сС не рекомендуется. В табл. 1 приведен химический состав наиболее широко применяемых высокопрочных сталей .
Сталь ЭИ643, в отличие от стали ЗОХГСНА, содержит большее количество углерода (0,36—0,43%) и никеля (2,5—3,0%); кроме того, в эту сталь вводится 0,8—1,2% W п для измельчения зерна и понижения чувствительности к хрупкому разрушению при постоянной нагрузке — титан. Оптимальное сочетание механических свойств ста¬ли ЭИ643, максимальная прочность при высокой пластичности и вязкости достигаются чосле закалки « отпуска при 240—260°С,
Высокая прочность всех этих сталей обеспечивается мартенситной структурой. Мартенсит представляет собой пересыщенный твердый раствор углерода в а-железе. Эта структурная составляющая стали образуется при быстром охлаждении после напрева выше критической точки. В каждом зерне бывшего аустенита образуется большое количество кристаллов мартенсита, которые имеют тетрагональную структуру.
С повышением содержания углерода постоянные ре-щетки мартенсита изменяются: величина а слегка уменьшается, а величина с и отношение с/а увеличиваются [7]. Мартенсит имеет форму вытянутых пластин. Высокая твердость и сопротивление деформации стали с мартенситной структурой обусловлены образованием в процессе термической обработки тонкой мозаичности зерен и высоким пределом упругости кристаллов мартенсита.
Для образования мартенсита определяющим фактором является скорость охлаждения. После нагрева выше критической точки необходима такая скорость охлаждения, при которой подавляются структурные превращения в перлитной и промежуточной областях. Скорость охлаждения зависит от содержания в стали углерода и легирующих элементов, а также температуры аустенитазацим В общем случае с увеличением содержания углерода и легирующих элементов, а также повышением температуры аустенитизации критическая скорость закалки уменьшается. Для получения мартенситной структуры и обеспечения комплекса механических свойств сталей 30ХГСНА, 25Х2ГНТА и ЭИ643 их охлаждают в жидких средах — маслах. Детали сложной конфигурации из этих сталей при закалке в жидких средах деформируются ((поводка). В тех случаях, когда получается мартенситная структура при охлаждении на воздухе, деформация деталей может быть значительно снижена или даже полностью устранена
Детали из сталей ВЛ-1 и ВКС-1 закаливаются на воздухе в больших сечениях, при этом обеспечиваются ми¬нимальная их поводка и возможность применения фиксирующих приспособлений
В табл. 2 приведены режимы термической обработки и основные показатели механических свойств высокопрочных конструкционных сталей.
Высокопрочные конструкционные стали отличаются повышенной чувствительностью к концентраторам напряжений пои однократном и особенно многократном нагружении. При наличии жесткого концентратора напряжений, каким является, например, трещина, высокопрочные стали выдерживают меньшие напряжения, чем стали средней прочности. Так. по данным Я Б. Фридмана и Б. А. Дроздовского Г6, с. 204—2091, образцы стали ЗОХГСА с о. = 1800 МН/мг (180 кгс/мм5) с трещиной глубиной 0,5—2,0 мм, разрушаются при испытании на изгиб при условном напряжении ~ 1000 МН/мв (100 кгс/мм21, а образцы той же стали с о„=1300 МН/м2 (130 кгс/мм2) с аналогичными трещинами разрушаются при условном напряжении ~2000 МН/м2 (200 кгс/мм2).
Разрушение деталей из высокопрочных сталей часто имеет усталостный характер. Известно, что предел выносливости не связан однозначно с пределом прочности. С. И. Кишкиной с сотрудниками показано, что сопротивление зарождению усталостной трещины, скорость ее развития и чувствительность к концентратам напряжений— важнейшие факторы, определяющие реальную конструкционную прочность материалов в условиях повторных нагрузок. Общая долговечность образцов при циклических нагрузках (N.\ определяется суммой числа циклов до образования видимой трещины (ЛМ и числа циклов, выдерживаемых образцами с трещиной .
Долговечность образцов из высокопрочной стали при циклических нагрузках в сильной степени зависит от чистоты поверхности. По данным С И. Кишкиной с сотрудниками, улучшение чистоты обработки с V7 до V9 приводит к увеличению долговечности образцов из стали ЭИ643 в 1 5—2 Раза при пульсирующем растяжении <тт„ = 13б0 MH/ms (136 кгс/ммг) с частотой 8 циклов/мин; при улучшении чистоты поверхности до VII наблюдается дальнейшее увеличение числа циклов до разрушения. Авторы считают, что влияние чистоты поверхности на долговечность образцов при циклическом нагружении в первую очередь связано с чувствительностью высокопрочных сталей к концентраторам напряжений (риски и т. п.). Уменьшение вредного влияния рисок на дол¬говечность высокопрочных сталей при повторных статических нагрузках достигается также обдувкой дробью, чугунным или корундовым песком, обкаткой роликами и др.
Наблюдаемое повышение сопротивления усталости на воздухе высокопрочных сталей после их поверхностного упрочнения наклепом дробью, вибронаклепом, об¬каткой роликами, алмазным выглаживанием обусловлено в первую очередь, по мнению С. И. Кишкиной и др., уменьшением остроты впадин и менее ориентированным их распределением. Этими авторами показано, что остаточные напряжения, вызываемые наклепом, при высоком уровне повторных напряжений, соответствующих области ограниченной выносливости, сравнительно быстро релаксируют: для стали ЭИ643, наклепанной обкаткой роликами, величина остаточных сжимающих напряжений при пульсирующем растяжении оПщх=1360 МН/'м2 (136 кгс/м(мг) через 5000 циклов уменьшается на 65— 70%, а через 11000 —на 85—90%
Развитие высокопрочных конструкционных сталей в США шло по двум путям-
а) использование уже хорошо зарекомендовавших се¬бя в авиации сталей (например, SAE 4340) с применением новых режимов термической обработки, а также с некоторой модификацией состава;
б) разработка специальных сталей, обеспечивающих после термической обработки сочетание высокой прочности и пластичности.
ВЛИЯНИЕ НАВОДОРОЖИВАНИЯ
НА МЕХАНИЧЕСКИЕ СВОЙСТВА СТАЛЕЙ
Наводороживание стали способствует уменьшению пластичности, характеристик технологических проб на перегиб и скручивание, длительной прочности (сопротивления замедленному разрушению). С увеличением содержания водорода уменьшается поперечное сужение и удлинение стали [178, 180], причем поперечное сужение уменьшается в гораздо большей степени, чем удлинение. По данным В. Я. Дубового и В. А. Романова [1811, при увеличении содержания водорода от 2 до 10,3-10~5 м3/кг поперечное сужение стали 25ХНМА уменьшается в 10 раз, а удлинение — на 71%.
Пластичность стали 30ХГСНА в надрезе за счет наводороживания при цинковании уменьшается с 7,0 (минимальное значение 5,4%) до 4,3 (минимальное значение 1,6%) [178]. При травлении стали 40ХНМА [(Тв« «2000 МН/м2(200 кгс/мм2)] в 20%-ном растворе серной кислоты с добавкой 30 кг/м3 хлористого натрия в течение 120 мин сужение и удлинение уменьшается соответственно от t]>=47% и 6 =/10,4% до я|;=0,33 и 6=1,6%.
В результате интенсивного наводороживания в ряде случаев изменяется характер разрушения стали от вязкого к хрупкому, что свидетельствует о понижении со¬противления отрыву [178].
Растворимость водорода и его влияние на механические свойства в сильной степени зависят от структуры стали.
С. С. Носырева [1®2] нашла, что при электролитическом наводороживании сталь с различной структурой поглощает различное количество водорода, м3/кг: мар¬тенсит 6,9-10~5, троостит—15,9-10~5 и сорбит 46,5-10~5. В то же время охрупчивание стали с трооститной струк¬турой при наводороживании происходит более сильно, чем стали с сорбитной структурой [179].
Рядом исследователей [178, 179, 183] было показано, что влияние водорода на свойства сталей в сильной степени зависит от прочности и их структуры: с увеличением прочности отрицательное влияние водорода на механические свойства сталей увеличивается.
Я. М. Потак [178] установил, что наибольшее влияние наводороживания на механические свойства проявляется в случае сталей с мартенситной структурой.
Влияние водорода на механические свойства сталей зависят от условий испытаний. Большое влияние оказывают скорость нагружения и температура испытания. По данным Я. М(. Потака [178], с увеличением скорости нагружения влияние водорода на работу разрушения стальных образцов уменьшается. Уменьшение влияния наводороживания на механические свойства сталей при увеличения скорости нагружения наблюдал Р. И. Крипякевич [184]. Отмечается [178], что с понижением температуры испытаний влияние водорода на механические свойства малоуглеродистой стали существенно уменьшается и при—160° С водородная хрупкость не проявляется. Работа разрушения наводорожениых образцов сталей У10, Х4ВЗМЗФ2, 30ХГСА и Х12М при температуре —196° С близка к работе разрушения ненаводороженных образцов [185].
Особенно большое влияние наводороживание оказывает на замедленное разрушение высокопрочных сталей.
Трояно [186] показал, что влияние водорода на замедленное разрушение высокопрочных сталей особенно сильно проявляется при наличии концентраторов напряжений. Используя образцы с надрезом, он установил, что время до разрушения заневоленных образцов при уменьшении растягивающих напряжений увеличивается.
Ход кривой напряжение—время показывает наличие некоторого порогового напряжения (<тДл), ниже которого не происходит замедленного разрушения стали. Показано, что на длительную прочность (стдл) большое влияние оказывает радиус концентратора напряжений: с уменьшением радиуса надреза от 6,25 до 6,025 мм адл наводороженной стали 4340 уменьшается почти в 3 раза.
При увеличении прочности углеродистых и низколегированных сталей (ТдЛ также уменьшается [186]. Особенно низкая длительная прочность стали с мартенситной структурой.