Технология и оборудование трубного производства
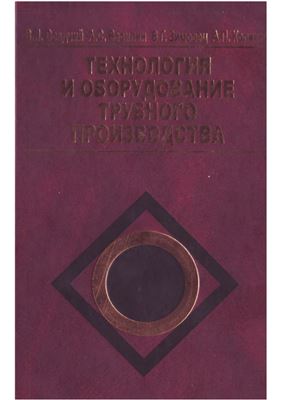
В.Я.Осадчий, А.С.Вавилин, В.Г.Зимовец, А.П.Коликов
Интермет Инжиниринг, 2001 г.
РАЗДЕЛ . ПРОИЗВОДСТВО БЕСШОВНЫХ ТРУБ
Современный уровень развития трубного производства в России и за рубежом характеризуется большим разнообразием применяемых способов и технологий для производства бесшовных труб, каждому из которых присущи свои особенности, достоинства и недостатки. Независимо от способа производства горячедеформированных труб технологическая схема включает следующие общие элементы: нагрев металла, получение полой заготовки (гильзы), получение черновой трубы (раскатка гильзы), окончательное формирование стенки и диаметра трубы (редуцирование или калибровка). При этом перед каждой технологической операцией при необходимости может осуществляться подогрев трубы.
Технология производства бесшовных труб предъявляет высокие требования к качеству исходной заготовки. По этой причине использование непрерывнолитой заготовки для производства бесшовных труб долго сдерживалось наличием ликвации и несплошностей в центральной части и на поверхности заготовки, что не обеспечивало получение качественных труб.
Однако высокая экономическая эффективность использования непрерывнолитых заготовок стимулировала проведение работ по развитию и совершенствованию технологии производства непрерывнолитых заготовок, разработку и создание новых процессов, технологий и трубопрокатного оборудования, обеспечивающих получение труб высокого качества из непрерывнолитого металла.
Применение качественной и дешевой заготовки в виде слитка непрерывной разливки является важным фактором конкурентоспособности бесшовных труб на мировом рынке.
Первые успехи были достигнуты при использовании непрерывнолитой заготовки прямоугольного сечения после обжатия ее в круг на обжимном стане. Дальнейшее совершенствование технологии трубопрокатного производства шло по пути непосредственного использования непрерывнолитой заготовки для производства труб с исключением предварительной прокатки на обжимных станах.
Способ прошивки заготовки в гильзу, применяющийся на том или ином трубопрокатном агрегате, определяет форму и размеры используемой непрерывнолитой заготовки.
3.2. Прошивка сплошных квадратных заготовок на пресс-валковых станах
В отечественной и мировой практике основным агрегатом для получения гильз из сплошной заготовки остается стан винтовой прокатки. Однако эффективность процесса прошивки на станах винтовой прокатки снижается из-за высокой стоимости катаной заготовки; использование непрерывнолитой круглой заготовки взамен катаной в 70 - 80-х годах было ограничено из-за больших трудностей получения поверхности исходной круглой заготовки удовлетворительного качества, что было связано с особенностями кристаллизации металла при охлаждении.
В последние 10 - 15 лет за рубежом в качестве исходного материала при производстве стальных бесшовных труб начали применять непрерывнолитую заготовку квадратного сечения, что наиболее эффективно благодаря ее сравнительно низкой стоимости и более высокому качеству, обусловленному технологическими особенностями разливки и кристаллизации стали. Применение непрерывнолитого металла квадратного сечения стало возможным главным образом в результате разработки и внедрения в производство процесса пресс-валковой прошивки (см. рис. 3.3).
В 70-х годах в Италии был создан способ пресс-валковой прошивки ("Press Piercing Mill-PPM") для получения гильз из квадратной непрерывнолитой заготовки. Этот процесс содержит элементы пресс-валковой прошивки и продольной прокатки в круглом калибре.
По мнению авторов данного способа прошивки квадратной трубной заготовки, преимущества данного способа заключаются в следующем :
использовании при производстве бесшовных труб более дешевой квадратной непрерывнолитой заготовки;
применении заготовки большой длины и массы;
наличии заполняющей прошивки, характеризующейся схемой всестороннего сжатия заготовки, что позволяет получить высокое качество внутренней поверхности изделий, а также осуществлять деформацию сталей с низкими пластическими свойствами;
низком расходе энергии на прошивку по сравнению с традиционными схемами;
возможности прошивки заготовок из труднодеформируемых высоколегированных марок сталей с 5 и 13% Сr.
К числу недостатков рассматриваемого процесса относятся:
повышенная разностенность стаканов, устраняемая в стане-элонгаторе;
узкий диапазон параметров, регулирующий устойчивое течение процесса;
3.3. Прошивка заготовок на прессах
Прошивку на прессах применяют при производстве труб прессованием, а также при использовании слитков или непрерывноли-той заготовки на отдельных агрегатах с пилигримовым и реечным станами. Во всех случаях, кроме первого, прошивка на прессе обычно сопровождается последующей раскаткой в стане-элонгаторе. Такое сочетание целесообразно вследствие повышения точности гильз по толщине стенки, прошивки донышка стакана, а также его удлинения в 1,5-3 раза, что в конечном итоге позволяет получать готовые трубы требуемой длины.
При производстве труб применяют следующие виды прошивки на прессах: прошивку в контейнере с матрицей; прошивку иглой (пуансоном) по методу Эрхарда (изобретение относится к 1891 г.) и прошивку на "глухой" матрице (закрытая или нарастающая прошивка, см. рис. 3.2).
Прошивка заготовок пуансоном является обычным процессом ВДавливания, которое бывает закрытым или открытым. При глубокой закрытой прошивке различают два вида образования полости: заполняющая и нарастающая прошивка. При заполняющей прошивке слитков (заготовок), поперечное сечение которых меньше Учения внутренней полости контейнера, течение металла в стороны не ограничено и вытесняемый пуансоном металл заполняет объем между боковыми поверхностями контейнера и заготовки. При закрытой нарастающей прошивке деформация осуществляется предварительно распрессованных слитков (заготовок) в глухом (закрытом) контейнере и процесс протекает с истечением металла вдоль оси прошивки навстречу движущемуся пуансону. При этом высота гильзы увеличивается соответственно объему вытесненного пуансоном металла.
На практике обычно при заполняющей прошивке многогранный слиток или квадратную заготовку прошивают в контейнере круглого сечения. При прошивке квадратной заготовки преобладает открытое вдавливание, когда металл заполняет пространство между гранями заготовки и стенками контейнера. Если объем металла, вытесняемого пуансоном, меньше объема свободного пространства, то прошивка происходит с незаполнением. Когда вытесняемый объем больше объема свободного пространства, контейнер переполняется и после соприкосновения деформируемого металла с его стенками по всему периметру осуществляется процесс закрытого вдавливания.
При прошивке многогранного слитка открытое вдавливание происходит только до момента заполнения металлом пространства между его гранями и стенками контейнера, после чего идет нарастающая прошивка.
Если происходит только заполняющая прошивка, то площадь сечения пуансона равна суммарной площади зазоров между его заготовкой и стенками контейнера, поэтому металл смещается только в радиальных направлениях и высота заготовки практически не изменяется.
4.4. Раскатка гильз на станах винтовой прокатки планетарных и реечных станах
Раскатка гильз в станах винтовой прокатки осуществляется и длинной оправке в трех валках (станы Ассела) или в двух валках приводными или неприводными направляющими дисками.
Трехвалковые станы винтовой прокатки применяют в составе агрегатов для раскатки толстостенных труб высокой точности: отклонение по наружному диаметру составляет ± 0,5%, а по толщине стенки ±6%.
Трубопрокатные агрегаты с трехвалковыми раскатными станами в основном применяются для изготовления труб из шарикоподшипниковых и других сталей, подвергающихся последующей механической обработке, так как малая их разностенность позволяет значительно снизить припуски на обточку. Достоинством этих установок является также возможность быстрой перестройки станов при переходе на новый размер, для чего не требуются частые перевалки, необходимые на других установках при разнообразном сортаменте труб.
Изменение внутреннего диаметра труб при прокатке на установках с трехвалковым станом осуществляется подбором соответствующего размера оправки без перенастройки стана. Изменение наружного диаметра также не требует перевалки валков и производится регулировкой валков раскатного стана. Перевалки осуществляются лишь при значительном изменении наружного диаметра труб или толщины стенки, а также из-за аварий или большого износа валков. Эти перевалки при надлежащей организации планирования производства можно приурочить ко времени ремонта установки.
Характерным для трехвалковых станов винтовой прокатки является расположение валков соответственно вершинам равностороннего треугольника. Все три валка вращаются в одну сторону, причем они наклонены к оси прокатки, образуя некоторый угол, называемый углом раскатки и соответствующий обычно 7°. Кроме того, каждый валок имеет перекос относительно плоскости симметрии соответствующего проема станины. Угол скрещивания оси валка с осью прокатки называется углом подачи.
Угол раскатки определяет, в известной мере, степень поперечной раскатки трубы и регулируется в небольших пределах. Вели чиной угла подачи определяется скорость прокатки, а также отчасти и величина раскатки, поэтому угол подачи целесообразно регулировать в пределах 3 — 9°.
Глава 5. Оборудование для производства готовых труб
Для получения готовых труб применяют станы винтовой прокатки (обкатные станы) и безоправочные станы продольной прокатки которые условно подразделяют на калибровочные, редукционно-калибровочные и редукционно-растяжные.
5.1. Обкатные станы винтовой прокатки
Обкатные станы винтовой прокатки предназначены для раскатки поверхностных неровностей, рисок на гильзах после их прокатки в автоматическом стане и обеспечения требуемой точности геометрических размеров труб. При обкатке диаметр трубы несколько увеличивается, при этом труба приобретает правильную круглую форму, а толщина стенки становится более равномерной: уменьшается ее разностенность.
Двух- и трехвалковые обкатные станы (риллинг-станы) устанавливаются в составе оборудования трубопрокатных агрегатов с автоматическим станом.
Иногда риллинг-станы используют для обкатки труб и облегчения условий извлечения длинных цилиндрических оправок, на которых производилась предшествующая деформация гильзы, поскольку при риллинговании всегда увеличивается диаметр трубы.
В состав риллинг-станов входят рабочая клеть, главный привод, передний и задний столы и вспомогательные механизмы.
Конструкция рабочей клети риллинг-стана аналогична рабочей клети прошивного или раскатного станов винтовой прокатки.
Станина рабочей клети открытого типа и состоит из корпуса и крышки, которые крепятся откидными болтами на клиньях.
Рабочие валки в клети наклонены в вертикальной плоскости один к другому и образуют угол подачи в3 = 6- 8°30'. В некоторых конструкциях обкатных станов поворотом барабанов можно изменять угол подачи до 10°. Валки установлены на четырехрядных подшипниках, их наклон на угол подачи обеспечивается соответствующим расположением гнезд подшипников в подушках.
5.2. Калибровочные станы
Бесшовные трубы, прокатанные на ТПА с автоматическим, непрерывным и другими раскатными станами, еще не отвечают требованиям, предъявляемым к товарной продукции по диаметру и точности геометрических размеров, а также по качеству наружной поверхности. В связи с этим в состав агрегатов включают калибровочные и редукционные станы.
Калибровку труб осуществляют на станах винтовой прокатки -трехвалковых, безоправочных станах продольной прокатки (рис. 5.2), получивших наибольшее распространение. В состав таких калибровочных станов входят от 3 до 12 двухвалковых клетей продольной прокатки, которые устанавливают под углом 45° к горизонту и под углом 90° одну к другой. Этим обеспечивается обжатие заготовки в двух взаимно перпендикулярных направлениях.
В состав главной линии каждой клети калибровочного стана рабочая клеть закрытого типа с одноручьевыми валками и привод, полненный в виде кинематически связанных электродвигателя, минированного редуктора и универсальных шпиндельных соединений.
современных конструкциях калибровочных станов каждая имеет индивидуальный привод валков. Это делает стан более маневренным и улучшает условия его ремонта.
Глава 7. Технологические расчеты трубопрокатных станов и прессов
7.1. Принципы расчета таблиц прокатки и прессования труб
Расчет технологических параметров производства бесшовных труб на трубных агрегатах начинается с распределения деформации между станами и определения геометрических размеров заготовки и трубы на всех стадиях передела. Все эти данные заносятся в таблицу прокатки, которая является основой установленного технологического процесса. Расчет таблицы прокатки производят с учетом специфики формоизменения заготовки, ее химического состава и рекомендуемых практикой определенных закономерностей параметров прокатки заготовки - трубы на том или ином стане, а также технологических возможностей основного оборудования агрегата.
Алгоритм выбора оптимального варианта распределения деформации между станами и расчета соответствующих ему параметров настройки станов заключается в следующем. Альтернативные варианты прокатки каждого типоразмера труб строятся с учетом всех ограничений. Для каждого возможного варианта (сочетание варьируемых параметров) определяют максимально возможную длину заготовки исходя из максимально допускаемых длин гильзы и труб после станов, коэффициентов вытяжки на прошивном и последующих станах, а также допускаемой длины заготовки для данного агрегата. Каждый возможный вариант прокатки оценивают исходя из производительности агрегата по годному либо по минимуму стоимостных затрат.
В. Я. Остренко, В. М. Фридманом и Ю. М. Мироновым предложен метод расчета, при котором оптимальному из всех возможных вариантов распределения суммарной деформации между станами соответствует минимальное значение такта наиболее загруженного агрегата, т. е. оптимизация режимов деформации осуществляется по такту прокатки. При этом определяется наиболее производительный режим прокатки с учетом технологических ограничений и ограничений по механическому и электрическому оборудованию.
Для ТПА с редукционными станами, работающими с натяжением, необходимо учитывать массу утолщенных концов, идущих в обрезь.
12.5. Совершенствование процесса и оборудования для производства холоднокатаных труб
Дальнейшее развитие процесса холодной прокатки труб направлено на улучшение качества труб, повышение производительности и надежности станов, увеличение величины обжатия за цикл за счет максимального использования ресурса пластичности металлов, поскольку станы периодической прокатки обладают низкой производительностью.
Для изготовления холодно- и теплокатаных труб высокой точности диаметром 19 - 4100 мм со стенкой толщиной 0,1 - 28 мм и длиной 30 м и более из сталей и сплавов применяют станы наружной и внутренней поперечной прокатки (ППТ) (рис. 12.18)
На станах наружной поперечной прокатки заготовку, надетую на оправку, обжимают снаружи валками, коническими роликами или шарами. На станах внутренней поперечной прокатки заготовку, помещенную в матрицу-обойму, деформируют изнутри роликами или шарами.
Конструктивное использование станов ППТ весьма разнообразно. Применяют станы с вертикальным и горизонтальным расположением приводных валков, с двумя рабочими и двумя поддерживающими цилиндрическими валками, с натяжением заготовки при прокатке на неподвижной оправке, с раздачей на неподвижной коническо-цилиндрической оправке заготовки перед деформацией стенки и др.
Фирмой "Лодж Энд Шипляй" (США) изготовлен горизонтальный трехроликовый стан для прокатки труб диаметром 76 - 673 мм, со стенками толщиной 0 ,28 - 28 мм и длиной 30,5 м из коррозионностойких сталей, сплавов, алюминия и титана. Рабочие ролики установлены на суппорте вокруг оправки через 120°. Гидравлическими цилиндрами, развивающими усилие 90 т, они устанавливаются раздельно в рабочее положение. Кулачковая система управления цилиндрами позволяет прокатывать изделия конической формы. Суппорт, приводимый от двигателя мощностью 50 кВт, перемещает ролики вдоль оправки. Сплошная оправка длиной 8 м вместе с закрепленной на ней заготовкой приводится во вращение при прокатке от электродвигателя мощностью 149 кВт. Заготовку надевают на оправку 15-тонным портальным краном поддерживают при деформации люнетами.