Справочник рабочего-литейщика
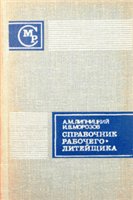
Липницкий А. М., Морозов И. В.
Машиностроение, 1976 г.
2. ЛИТЕЙНЫЕ СВОЙСТВА СПЛАВОВ
Важнейшие СВОЙСТВА сплавов: высокая жидкотекучесть, малая усадка, небольшая склонность к образованию литейных напряжений, незначительная ликвация примесей, мелкокристаллическое строение.
Жидкотекучесть. Способностьсплава в жидком состоянии заполнять литейную форму и воспроизводить контуры полостейформы и стержней называют жидкотекучестью.
Жидкотекучесть чугуна, бронзы и алюминиевых сплавов принято определять с помощью спиральной пробы трапецеидального сечения (рис. 1), которая состоит из спирали /, имеющей на верхней поверхности выступы 4 на расстоянии, равном 50 мм, стояка 2 и выпора 3.
Жидкотекучесть стали, магниевых и других сплавов определяется по прутковой пробе. На рис, 2 приведена сухая форма для заливки прутковой пробы, состоящая из собственно формы / с каналом 3, заполняемым жидким сплавом, и литниковой воронки 2.
О жпдкотекучести сплавов судят по длине (в см) заполненной части формы. Жидкотекучесть сплавов увеличивается с повышением температурыперегрева сплава. Однако во избежание появления брака по усадке, пригару формовочной смеси и трещи нам^ температурасплава при заливке форм должна быть умеренно высокой.
Жидкотекучесть чугуна возрастает при повышении содержания (до известных пределов) углерода, кремния и фосфора. Марганец не оказывает заметного влияния на жидкотекучесть. При содержании серы в количестве более 0,15% жидкотекучесть чугуна понижается.
Существенное влияние на жидкотекучесть бронзы оказывают олово и цинк: чем больше содержание этих элементов, тем выше жидкотекучесть.
Жидкотекучесть алюминиевых сплавов повышается при увеличении содержания кремния, а магниевых сплавов — при увеличении содержания алюминия.
Усадка. Процесс уменьшения линейных размеров и объема жидкого сплава в форме при охлаждении называют усадкой. В литейном производстве различают объемную и линейную усадку сплавов.
Объемной усадкой называют разность между объемомполостиформы и объемомотливки после ее охлаждения. Линейной усадкой называют разность между линейными размерамиформы и остывшей отливки.
В практике литейного производства усадку обычно выражают в процентах по отношению к первоначальному объему жидкого сплава - (объемная усадка) или к первоначальным линейным размерам в полостиформы (линейная усадка).
При остывании отливок выступающие части формы, болваны и стержни препятствуют свободной усадке отливок и усадка будет затрудненной; такая усадка называется литейной. Значения усадкисплавов приведены в табл. 2.
Величина усадки зависит от химического состава сплава. Так, • повышение содержания углерода и кремния н уменьшение содержания марганца и серы в чугунеприводят к уменьшению усадки. В алюминиевых сплавах повышение содержания кремния уменьшает усадку; медь и магний, наоборот, увеличивают усадку этих сплавов. В магниевых сплавахусадка понижается при повышении содержания в них алюминия и цинка.
Затвердевание сплавов в форме (переход от жидкого "к твердому состоянию) кроме изменения линейных размеров и объемаотливки для ряда сплавов сопровождается образованием в отливке внутренних полостей — усадочных раковин и пористости.
Для борьбы с линейной усадкой следует размерымодели делать больше размеровотливки на величину литейной усадки. Борьба же с усадочными раковинами и пористостью более трудна, К основным мерам предупреждения усадочных раковин и пористости относятся: достаточное питание отливки путем увеличения сечения литниковой системы, установка прибылей, применение холодильников, улучшение конструкции отливки.
Устранение как горячих, так и холодных трещин достигается созданием равномерных сечений без резкихпереходов между отдельными частями отливок. С этой целью рекомендуется заменять сечения отливок с затрудненной усадкой ив сечения со свободной усадкой.
Внутренние напряжения в отливках могут быть устранены термической обработкой, состоящей из медленного нагрева отливок в печи до определенной температуры и последующего охлаждения.
Ликвация. При затвердевании сплава, залитого в форму, на протяжении всего времени его остывания происходит Процесс выравнивания химического состава по всему сечению отливки. Однако этот Процесс протекает медленно, вследствие чего в отдельных частях отливки, а также в отдельных зернах сплава, наблюдается химическая неоднородность, называемая ликвацией. Обычно ликвация обусловливается тем, что отдельные составляющие сплава, имеющие неодинаковую плотность и различные температуры затвердевания, отделяются от основной массысплава как в жидком состоянии, так и при его затвердевании.
Ликвация уменьшается при понижении температуры и скорости заливки, а также при ускорении затвердевания отливки. Наибольшей склонностью к ликвации отличаются сплавы с большим содержанием свинца.
Строение (структура) сплавов. Наилучшие СВОЙСТВА имеют сплавы в том случае, когда их структура получается мелкокристаллической и без промежуточных пленок, ослабляющих связь между отдельными кристаллами (или группами кристаллов). Обычно в литейных сплавах рассматриваются не отдельные кристаллы, которые очень малы, а группы кристаллов, образующие кристаллиты или зерна.
Уменьшение размеров зерен сплава достигается понижением температуры и скорости заливки и в особенности увеличением скоростиохлаждения при затвердевании отливки. Для того чтобы придать сплаву мелкозернистую структуру, в него вводят особые добавки — модификаторы. Наибольшее распространение имеют следующие добавки: для полусерого чугуна — кремний, для серого чугуна — магний, для стали — титан, алюминий, силикокальций, для силумина — натрий.
3. КЛАССИФИКАЦИЯ ЛИТЕЙНЫХ СПЛАВОВ
Применяемые в литейном производстве сплавы можно разделить на пять групп: 1) чугуны н стали — сплавы железа с углеродом и другими элементами; 2) бронзы и латуни — сплавы меди с различными элементами; 3) сплавыалюминия с различными элементами; 4) сплавымагния с различными элементами; 5) сплавы на основе цинка, олова, свинца и других металлов.
К важнейшим сплавам для изготовления отливок относятся сплавы первой группы; около 75% всех отливок (по массе) изготовляется из чугуна и около 20% — из стали. На долю остальных четырех групп сплавов приходится небольшая часть общей массы отливок.
Алюминиевые, магниевые и медные сплавы имеют исключительно важное значение для многих отраслей промышленности: авиационной, автомобильной, судостроительной, приборостроительной и других.
Г л а в а II
ФОРМОВОЧНЫЕ МАТЕРИАЛЫ И СМЕСИ
Материалы, применяемые при изготовлении форм и стержне! называются формовочными материалами. Свойства формовочных стержневых смесей, изготовляемых из разных формовочных материалов оказывают решающее влияние на качество отливок.
Формовочные материалы подразделяются на основные и вспомогательные. К основным материалам относятся пески и глины, к вспомогательным — связующие, применяемые, главным образом, для приготовления стержневых смесей» противопригарные материалы (каменный; уголь, припылы, краски, натирки), клей, замазка и др.
I. ФОРМОВОЧНЫЕ ПЕСКИ
Формовочные пески и глины являются осадочными горными породами, образовавшимися в результате разрушения изверженных пород под воздействием солнечного тепла, морозов, дождей.
Основная часть формовочных песков состоит из кварца кремнезема, имеющего высокую температуруплавления (выше 1750° С). В зависимости от содержания кремнезема и глинистой составляющей (так называются зерна с поперечником менее 0,022 мм) формовочные пески по ГОСТ 2138—74 делятся на кварцевые и глинистые (табл. 1).
Глинистые пески классов Т, П, Ж и ОЖ в смеси с кварцевым песком широко применяются при изготовлении формовочных и стержневых смесей для отливок из сплавовцветных металлов.
По зерновому составупески делятся на группы в зависимости от величины входящих в них зерен (табл. 2).
Для определения группы песка его нужно просеять через стандартный набор сит и выяснить, на каких трех смежных ситах останется наибольшая сумма остатков (в массовых единицах), называемая основной фракцией. Зная, на каких ситах располагается основная фракция песка, его можно отнести к группе, которая определяется средним номе-
2. ФОРМОВОЧНЫЕ ГЛИНЫ
Глины, применяемые в качестве минеральных связующих в формовочных и стержневых смесях, классифицируются по минералогическому составу, по пределупрочности во влажном и сухом состояниях и по термохимической устойчивости. Классификацияглин по минералогическому составу приведена в табл. 3.
Для определения прочности во влажном и высушенном состояниях применяются стандартные образцы, изготовляемые из кварцевого песка средней зернистости с добавкой глины и воды.
При испытаниисмеси с бентонитовыми глинами применяется кварцевый песок с добавкой бентонита и воды.
б. ИЗГОТОВЛЕНИЕ ОБОЛОЧКОВЫХ СТЕРЖНЕЙ
Этот способ изготовления стержней и форм основан на применении в составе смесей в качестве связующего материала порошкообразных или жидких фенольных смол (пульвербакелит и др.)? способных под
воздействием тепла плавиться и равномерно распределяться в слое песка. При дальнейшем нагревании смола твердеет и прочно связывает зерна песка. Высокая прочность отвержденной смеси позволяет применять стержни в виде оболочек с толщиной стенки от 6 до 15 мм (в зависимости от габаритов стержня). Оболочковые стержни изготовляются из мелких кварцевых песков, обладают высокой газопроницаемостью и обеспечивают получение чистых гладких полостей. Оболочковые стержни можно применять в сочетании с обычными песчаными.
Оболочковые стержни могут быть различной конфигурации и могут применяться для широкой номенклатуры отливок (рис. 6). Примерный составсмеси (массовая доля, %): кварцевый песок мелкий —100; сверх 100%: пульвербакелит — 4,5, ацетон — 1,2.
Смесь может быть приготовлена в любых бегунах. Вначале перемешивают сухой холодный песок с пульвербакелитом; затем небольшими порциями добавляют ацетон. После заливки ацетона образуются комки, которые подсыхают и затвердевают. При дальнейшем перемешивании они растираются и получается однородная сыпучая смесь. Стержневые ящики изготовляются из чугуна или алюминиевого сплава.
Технологический Процесс изготовления оболочковых стержней с помощью стационарного бункера (рис. 7) состоит из следующих операций:
1) нагрев в лечи стержневого ящика 3;
2) нанесение на рабочую поверхность ящика разделительного состава (4-процентный раствор термостойкого синтетического каучука в уайт-спирите);
3) установка ящика на деревянный поддон 2. В центре поддона имеется отверстие, закрываемое крышкой 7;
4) открывание задвижки 4; при этом смесь из бункера 5 поступает в ящик 5, и после заполнения ящика задвижку закрывают;
5) выдержка смеси в ящике в течение 12—15 с. За этот промежуток времени образуется оболочка толщиной 6—7,5 мм; для получения более толстых оболочек увеличивают время выдержки;
6) удаление из ящика неспекшейся смеси, для чего открывают крышку 7 поддона 2; неспекшаяся смесь ссыпается в бункер 1% откуда она с помощью элеватора 6 возвращается в бункер 5;
7) упрочнение оболочкового стержня дополнительной тепловой обработкой; для этого стержневой ящик с оболочкой помещают на 1,5—2 мин в электропечь, нагретую до 300—350° С;
8J извлечение стержневого ящика из печи, раскрывание его и удаление стержня.
Применение оболочковых стержней обеспечивает сокращение расхода формовочных материалов, высокую точность размеров, не требует каркасов и сушильных плит и во многих случаях снижает стоимость стержней.
6. ИЗГОТОВЛЕНИЕ СТЕРЖНЕЙ В ГОРЯЧИХ ЯЩИКАХ
Процесс изготовления стержней с отверждением в горячих ящиках находит все более широкое применение в литейном производстве.
К основным преимуществам процесса относятся: повышенная точность стержней; значительное сокращение цикла изготовления стержней; отсутствие необходимости в фасонных и гладких сушильных . плитах, а также в сушильных печах; благоприятные условия для комплексной механизации и автоматизации стержневых работ и т. д.
Однако, учитывая большую сложность стержневой оснастки, данный Процесс рентабелен только при крупносерийном и массовом производстве.
. Сущность процесса
Сущность технологического процесса изготовления стержней. отверждаемых в горячих стержневых ящиках, заключается в следующем. Стержневой ящик, нагретый до температуры 200—250° С, устанавливается на стержневую машину и способом наддува заполняется специальной быстротвердеющей смесью. При контакте со стенками ящика смесь прогревается за счет теплопроводности и затвердевает. . Через 15—20 с на стержне образуется прочная корка и он может быть извлечен из ящика. Полная сушка во всем объеме протекает на воздухе 8а счет аккумулированного стержнем тепла.
Схема технологического процесса изготовления стержней в нагреваемой оснастке дана на рис. 8.
В качестве основной составляющей смеси применяется кварцевый песок по ГОСТ 2138—74 (см. гл. II, табл. I).