Ковка и объемная штамповка стали
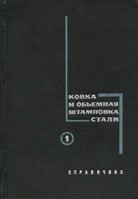
ред. Сторожев М.В.
Машиностроение, 1967 г.
Механизацию процессов в кузнечном производстве условно подразделяют на три степени: высокую, среднюю и низкую.
При высокой степени механизации все основные и вспомогательные операциипроцесса изготовления поковки выполняют при помощи специальных механизмов, управляемых рабочим на каждом отдельном участке ковочного агрегата. При среднейстепени механизации больший объем (по трудоемкости) основных и вспомогательных операций изготовления поковки выполняют при помощи специальных механизмов, управляемых рабочим на каждом отдельном участке ковочного агрегата, а меньший — вручную.
При низкой степени механизации — больший объем (по трудоемкости) основных и вспомогательных операцийпроцесса изготовления поковки выполняют вручную или при помощи примитивных средств механизации.
СВОБОДНАЯ КОВКА
Нагрев заготовок. Посадка заготовок в нагревательную печь и вынос заготовок из печи осуществляется с помощью транспортных устройств и посадочных приспособлений; транспортного мостового электрического крана, ковочного мостового электрического крана, ковочного поворотного электрического крана, посадочной машины, ковочного манипулятора, посадочной вилки, патрона, клещей и цепей к ним.
Выбор средств механизации зависит от технологии и организации производства поковок, типа нагревательной печи и веса заготовок. Так, при обслуживании толкательных печей подача заготовок в зону действия толкателя осуществляется при помощи поворотного электрического крана и подвесных клещей; нагретая
заготовка выдается из печи на приемное устройство толкателем, затем манипулятором подается к прессу. В тех случаях, когда нет манипулятора, следует применять ковочный поворотный электрический кран, снабженный подвесными клещами.
Для посадки заготовок впечь с выдвижным или с вагонеточным подом, а также для выноса нагретых заготовок из печи применяют транспортный мостовой электрический кран, причем захват заготовки и перенос ее осуществляется при весе заготовки до 60 т подвесными клещами и для заготовок весом более 60 т — подвесными цепями.
В тех случаях, когда транспортного мостового крана нет, посадка заготовок в печь и вынос их из печи производится ковочным мостовым краном.
Ковка на гидравлических ковочных прессах. При ковке на гидравлических прессах подлежат механизации следующие технологические и транспортные операции: посадка заготовки в нагревательную печь, вынос заготовки из нагревательной печи и подача ее к прессу, биллетировка и оттяжка хвоста, ковка заготовки, удаление поковки от пресса и посадка ее в термическую печь, удаление от пресса метал-лоотходов.
Рекомендуемые средства механизации в агрегатах ковочных прессов приведены в табл. 1.
Значения коэффициентовпроизводительности Кп и трудоемкости КТ приведены в табл. 2.
Рекомендуемая грузоподъемность основных средств механизации в прессовых кузнечных цехах при изготовлении поковок разных конфигураций приведена в табл. 3.
КИСЛОРОДНАЯ РЕЗКА
Условия резки
Газовой резке поддаются лишь те металлы, которые удовлетворяют следующим основным условиям.
1. Температура воспламенения металла должна быть ниже температурыплавления (условие возможности осуществления процесса). За температуру воспламенения принимают температуру, при которой металл интенсивно окисляется струей кислорода, действующей на его нагретую поверхность. Высококачественная газовая резка возможна при сгорании металла в твердом состоянии. Сталь, nbsp; содержащая углерода более 0,7%, при резке одновременно горит и расплавляется, вследствие чего полость раздела получается широкой, а поверхность неровной.
2. Окислы металла должны быть жидкотекучими и обладать более низкой температурой плавления, чем металл (условие, обеспечивающее выдувание шлака из полоски раздела в жидком состоянии).
3. Теплота, выделяющаяся при сгорании металла, вместе с теплотой подогревающего пламени должна быть достаточной для поддержания нагрева на уровне температуры воспламенения в течение всего периода резки (условие, необходимое для беспрерывности процесса резки).
4. Теплопроводностьметалла должна быть возможно ниже (условие, способствующее локализации тепла в зоне реза).
5. В металле должно быть ограниченное содержание элементов, ухудшающих процесс резки.
Высоколегированные хромистые, хромоникелевые, вольфрамовые и другие стали не удовлетворяют перечисленным условиям и поддаются лишь кислородно-флюсовой резке.
Процесс кислородно-флюсовой резки отличается от кислородной тем, что в зону раздела кроме режущего кислорода вводится флюс (обычно железный порошок). Флюс, сгорая, повышает температуру в полости раздела; а продуктыгорения флюса, переходя в шлаки, снижают температуруплавления последних, благодаря чему они в жидком виде легко удаляются кислородной струей.
Влияние процессарезки на структуру металла
Структура металла вдоль линии реза отлична от структуры основного металла. В малоуглеродистых сталях в зоне перегрева наблюдается рост зерна, а у кромок реза видманштеттова структура. Участки более удаленные от линии реза, но расположенные в зоне термического влияния, приобретают сравнительно мелкозернистое строение, подобно структуре нормализованной стали. При резке малоуглеродистой сталиструктурные изменения, как правило, не оказывают существенного влияния на качество металла.
Резка высокоуглеродистой и легированной стали сопровождается образованием в зоне термического влияния структур с повышенной твердостью вследствие закалки. Глубина зоны термического влияния возрастает с увеличением содержания углерода в стали (табл. 25). Изменение твердостистали зависит также и от способарезки (табл. 26). Для уменьшения отрицательного влияния (закалка кромок, трещинообразование) огневой резки применяют сопутствующий подогрев и замедленное охлаждение. Сопутствующий подогрев осуществляется пламенем дополнительных сопел 2 (рис. 20), концентрически расположенных относительно мундштука /. Благодаря сопутствующему подогреву уменьшается скоростьохлаждения зоны термического влияния, а вместе с тем и степень закалки стали. скоростьохлаждения уменьшают также и тем, что разрезанные части металла раздвигают не сразу после окончания процесса резки, а через некоторое время, благодаря чему уменьшается интенсивность теплоотдачи. Снятие напряжений и уменьшение твердости достигается в необходимых случаях соответствующей термообработкойметалла после резки.
Технология резки
Подготовка поверхности металла.
Очистку производят обогревом пламенем резака (без подачи режущего кислорода) узкой полосы (30—50 мм) поверхности вдоль намеченной линии резания с последующей зачисткой ее металлической щеткой.
Начало резки. Резку следует начинать с ребра или кромки металла. Если операцию необходимо начинать внутри контура (например, при вырезке заготовки из листа), рекомендуется в начальной точке реза подготовить отверстие, что при ручной резке и толщине листа до 50—75 мм выполняют резаком, а при машиннойрезке и толщине листа свыше 20 мм — сверлом на стационарном сверлильном станке или переносной дрелью (диаметр отверстия не менее 6—8 мм в зависимости от толщины листа).
Время подогрева металла пламенем резака до начала резки зависит от толщины и химического составастали (табл. 27). Поддержание резака на определенной высоте при разрезке достигается закреплением его на тележке (при ручной резке) или с помощью суппорта (при машинной резке). Ориентировочно расстояние мундштука от поверхностиметалла h определяют по формуле [9]
h = 2 + 0,0156 мм,
где б — толщина металла в мм.
При резкестали толщиной более 100 мм кислородом низкого давления данным ВНИИ автогена расстояние h следует определять по формуле
h = 4+ 0,056.
Положение резака в процессе резки.
В целях повышения производительности при ручной прямолинейной резке
полосовой и листовой стали толщиной до 20—30 мм рекомендуется [4 ] пламя направлять под углом 60—70° (рис. 21, а). При вырезке детали из поковки (листа) по криволинейному контуру резак устанавливают перпендикуляр-
но поверхности разрезаемого металла. Резкупроката круглого сечения производят по схеме, изображенной на рис. 21, б.
Ширина реза и чистота его поверхности. На ширину реза и чистоту его поверхности оказывают влияние толщина металла и способрезки (табл. 28). В зависимости от толщины 6 металлаширина реза определяется приблизительно по формуле
Ь= 2+ 0,036.
Чем толще металл, тем менее чистой получается поверхность реза (больше неровностей). При прочих равных условияхмашиннаярезка обеспечивает получение реза меньшей ширины и с более чистой поверхностью, чем при ручной разрезке. Следует также учитывать, что на выходной стороне ширина реза на 10—50% больше ширины на входе. скоростьрезки (перемещения резака) должна соответствовать скоростивыгоранияметалла в полости реза. Малая скорость перемещения резака вызывает оплавление кромок, а большая не обеспечивает сквозного прорезания металла. На скоростьрезки оказывает большое влияние чистота кислорода. Ориентировочные технические скоростимашиннойрезки в зависимости от толщины металла и вида операции приведены в табл. 29. Скоростнаямашиннаярезка позволяет повысить указанные скорости в 2— 3 раза.
Горючее и аффективная мощность пламени
Для питания подогревающего пламени применяется газообразное или жидкое (превращаемое перед сжиганием в пары) горючее. Для резки пригодны газы, имеющие при нормальных условиях (при температуре 20° С и давлении 760 мм рт. ст.) низшую теплотворную способность не менее 2400 ккал/м3, температуру пламени при сгорании в смеси с кислородом не ниже 1800° С и содержание балласта не более 35%.
ВЫБОР СПОСОБА РЕЗКИ
И ДОПУСКИ НА ДЛИНУ
ЗАГОТОВКИ
Самым высокопроизводительным и дешевым способом является резка на ножницах и прессах. В кузнечных цехах с крупносерийным и серийным производством этот способ является основным. Он выгодно отличается и тем, что не вызывает дополнительных потерь металла на прорезку. Существенным недостатком его является искажение формы торцовой части заготовки.
В кузницах мелкосерийного и индивидуального производства, применяющих прокат крупных сечений, развита кислородная резка. Основным недостатком огневой резки является дополнительная потеря металла на прорезку. Хорошее качество реза и сравнительно высокая точность обеспечиваются при резкепроката на пилах и других отрезных станках. Однако относительно низкая производительность, высокая стоимость и кратковременная стойкость режущего инструмента (особенно дорогостоящих сегментов), а также потериметалла на прорезку ограничивают применение данного способа. Резку на пилах и других отрезных станках рекомендуется применять лишь в тех случаях, когда к заготовке предъявляются повышенные требования в отношении качества реза и допусков на длину. В кузницах применяется также резка на пилах и в тех случаях, когда усилие пресс-ножниц недостаточно для резкипроката крупных сечений.
Допуск на длину заготовки при равных производственных условиях зависит от размеровсеченияпроката и номинальной длины заготовки. Наиболее отвечающей экономичному расходованию металла является структура допуска с преобладанием отрицательного отклонения или в крайнем случае с равными предельными отклонениями от номинала (симметричный допуск). Односторонние допуски с положительными (плюсовыми) отклонениями следует применять лишь в исключительных, обоснованных технологическим процессом, случаях. Допуски на длину заготовок при резке на ножницах приведены в табл. 42, на прессах в штампах — в табл. 43, а на дисковых пилах, ленточных и ножовочных механических станках — в табл. 44.