Сварка разнородных металлов и сплавов
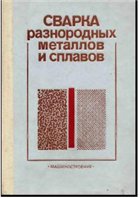
В. Р. Рябов, Д. М. Рабкин, Р. С. Курочко, Л. Г. Стрижевcкая
Машиностроение, 1984 г.
Сварка сплавов разных основ
СВАРКА СТАЛЕЙ С МЕДЬЮ И ЕЕ СПЛАВАМИ
При изготовлении испарителей, эжекторов, фурм доменных печей и конвертеров, кристаллизаторов, химической аппаратуры, электровакуумных приборов и во многих других случаях возникает необходимость соединения сталей различных классов с медью и ее сплавами —латунью, бронзой.
По вопросам сварки сталей с медью и ее сплавами опубликовано довольно большое количество работ [123, 145, 181, 185 и др.]. Это объясняется прежде всего разнообразием и трудностью задач, которые приходится решать в каждом конкретном случае. Помимо непосредственной сварки медных деталей со стальными, в целях экономии цветных металлов целесообразна наплавка меди, бронзы или латуни на стальные поверхности. В промышленности используют также стали, плакированные медью и ее сплавами, например биметалл сталь—латунь, в котором высокая прочность и достаточная пластичность сочетаются с коррозионной стойкостью, хорошей теплопроводностью и электропроводностью, высокими антифрикционными свойствами. Эти биметаллы могут подвергаться самым различным технологическим операциям —штамповке, гибке, сварке и др.
Из диаграммы состояния бинарной системы железо—медь следует, что железо с медью сплавляется во всех соотношениях. При этом максимальная растворимость меди в S-железе составляет 6,5 %, в у-железе 8 %, в «-железе 1,4 % при 850 °С. Медь растворяет в себе железо в следующих количествах: при температуре 1094 "С 4 %; при 650 "С 0,2 %. Рассмотрим характерные особенности взаимодействия этих двух металлов. При наплавке меди на аустенитную сталь 12Х18Н9Т и их сварке наблюдается проникание меди в сталь. Наличие ферритной фазы в стали уменьшает проникание в нее меди, а содержание феррита более 30 % в аустенитно-ферритной стали —полностью устраняет. Предварительный подогрев стали I2X18H9T до температуры 800 °С вызывает выделение ферритной фазы. Проникание меди при этом снижается Е6, 7].
Была высказана следующая гипотеза [7]: трещины при наплавке меди на сталь образуются в результате совместного действии жидкой меди, проникающей в микронадрывы, которые возникают при кристаллизации матричной фазы — стали (эффект Ребиндера), и термических напряжений растяжения. Необходимым условием возникновения этого эффекта является смачивание стенок капилляра. Из двух фаз, присутствующих в рассматриваемых сталях, жидкая медь смачивает аустенит (v-фазу) и не смачивает феррит (а-фазу). Определено, что расклинивающее давление жидкой меди на сталь равно ~25 МПа.
Проникание меди в сталь на глубину от нескольких микрометров до нескольких десятков миллиметров при наплавке, сварке и пайке отмечено в работах [16,35,128 и др. ]. При этом допустимая глубина проникания, не влияющая на механические свойства стали, ограничивается 0,3—0,5 мм. Считают, что на проникание меди в сталь при наплавке, сварке, пайке оказывают влияние следующие факторы: время контактирования расплавленной меди со сталью, с увеличением которого увеличивается глубина проникания; напряженное состояние металла при наплавке, сварке и пайке; структурное состояние, химический состав стали.
В работе [161 показано, что проникание сплава МНЖКТ5-1--0,2-0,2 в сталь 20, СтЗсп и т. п. на глубину 0,8 мм практически не влияет на статическую и циклическую прочность биметаллических образцов. В то же время при наплавке оловянной бронзы на сталь глубина проникания 2—13 мм существенно снижает временное сопротивление и сопротивление усталости биметалла [39, 164].
При исследовании влияния проникания медного сплава в сталь толщиной 30 мм с ав — 900-^1000 МПа на свойства биметаллических образцов в качестве наплавляемого металла применяли проволоку из сплава МНЖКТ5-1-0,2-0,2 диаметром 2 мм. Наплавку выполняли сжатой дугой на обратной полярности с токоведущей присадочной проволокой на режиме: ток в цепи вольфрамовый электрод —изделие 200—220 А, в цепи вольфрамовый электрод —присадочная проволока 80—100 А, амплитуда колебаний сварочной головки 20 мм, частота колебаний 35—40 в минуту, скорость наплавки 6—7 м/ч. Наплавка сжатой дугой была выбрана потому, что она обеспечивает отсутствие включений железа и кристаллизационных прослоек в наплавленном металле, что может иметь место при других способах наплавки, когда происходит расплавление стали.
Установлено, что проникание медного сплава в высокопрочную сталь на глубину 1,2 мм практически не сказывается на статической и циклической прочности при растяжении, статическом и ударном изгибе биметаллических образцов, а также на прочности сцепления наплавленного металла со сталью. В качестве примера на рис. 59 приведены результаты испытания на установке ГРМ-1 при пульсирующем растяжении с частотой 400—600 циклов в минуту.
Сварка и наплавка трением. Возможность получения качественного соединения меди и медно-никелевого сплава с различными углеродистыми сталями показана в работе [177]. Для сварки трением меди МЗр, М2, медно-никелевого сплава МН95-5 (95 % Си, 5 % Ni) со сталями 20, 45 и 60 использовали серийное оборудование (МСТ-31, МСТ-23, MCT-200I).
Один из основных параметров, определяющих качество сварного соединения, — максимальная температура в стыке. Последняя зависит от скорости скольжения и состава свариваемых металлов. Так, при сварке трением стали 20 с той же сталью максимальная температура составляет —1200 "С, при сварке стали с медью ~700—800 °С и при сварке меди с медью ~400 "С. Во всех'случаях максимальная температура в стыке ниже температуры плавления более легкоплавкого металла. Увеличение скорости вращения приводит не только к повышению максимальной температуры в стыке, но и к возрастанию градиента температур.
При отработке режимов сварки цилиндрических образцов различных диаметров удалось получить соединения с механическими свойствами, соответствующими свойствам отожженной меди (табл. 19).
Для получения стабильного качества режимы сварки (давление при нагреве рп, время нагрева и давление проковки рпр) варьировали в широких пределах. Металлографические исследования показали, что образование соединения происходит за счет совместного перемешивания поверхностных слоев меди и стали.
Контактная сварка. Сварку стали 10 с латунью Л63 выполняли на контактных машинах МТПК.-251 и КТ-801. Стальные образцы (толщиной 1,2—1,6 мм) перед сваркой обезжиривали, а латунные (толщиной 1,2—1,6 мм) механически зачищали.
При сварке меди и ее сплавов требуются определенные технологические приемы, обеспечивающие высокую концентрацию теплоты в месте контакта деталей [128 ]. Один из этих приемов — установка теплового экрана, например молибденовой пластины толщиной 0,6 мм, между латунным листом и медным электродом для создания необходимой концентрации теплоты в месте контакта деталей, при этом рост ядра точки ускоряется примерно на 20 %.
Образцы, выполненные точечной сваркой с помощью молибденового экрана, при испытании на разрыв во всех случаях разрушались с вырывом точки из латунной или стальной пластины, что свидетельствует об удовлетворительном качестве сварного соединения.
Сварка взрывом. Изучены строение и свойства биметалла сталь 16ГС + медь М1б, полученного сваркой взрывом [1611; толщина плакирующего слоя составляла 4—10 мм. Для назначения оптимальных режимов последующей (после сварки) горячей прокатки для листов заданных размеров необходимо знать закономерности изменения строения и физико-механических свойств при нагреве биметаллических заготовок в процессе сварки взрывом. Образцы для испытаний вырезали из различных участков по длине и ширине двухслойной заготовки.
При изучении строения биметалла при температуре 20 °С установлено наличие плотного соединения слоев биметалла (лишь в 3 % образцов были обнаружены поры и микротрещины в зоне сварки). Предел прочности при срезе составлял 153—310 МПа, при отрыве 234—342 МПа; более 80 % образцов выдержали испытания на изгиб, пластические свойства биметалла после сварки низкие (6 = 8,0-^ -J- 17,5 %). Металлографическое исследование образцов выявило типичную для сварки взрывом картину на контактирующих поверхностях: волнообразная граница раздела слоев с отдельными участками, где движение металла в момент сварки носило турбулентный характер [1611.
Микрорентгеноспектральный анализ показал, что в зонах перемешивания, расположенных во впадинах волн, содержится 40—50 % Си и 45—55 % Fe, а в зонах, расположенных на гребнях волн, 55— 65 % Си и 30—40 % Fe. Поскольку взаимная растворимость меди и железа в твердом состоянии в равновесных условиях невелика, образование фазы, содержащей столь значительные количества железа и меди, возможно лишь при расплавлении соприкасающихся при взрыве участков и последующей их закалке за счет высокой скорости теплоотвода [38].
Одночасовой отжиг при температуре 700 или 900 °С приводит к росту относительного удлинения до 25 % при соответственном снижении временного сопротивления до 380—420 МПа. При этом уменьшаются различия в свойствах образцов, вырезанных из разных зон двухслойной заготовки. Изменение свойств биметалла после отжига связано с развитием рекристаллизации как в основном, так и в плакирующем слоях. В стали и меди обнаружены участки рекристаллизованных зерен, пластически деформированные зоны и участки с равновесной структурой.
Диффузионная сварка. Одним из наиболее перспективных способов соединения разнородных металлов давлением является диффузионная сварка в вакууме, которая обеспечивает получение вакуумно-плотных, термостойких, вибропрочных сварных соединений при сохранении высокой точности геометрических размеров и форм изделий (табл. 20) [58).
Микроструктурный анализ соединений, сваренных по разработанным оптимальным режимам, показал отсутствие непроваров, микротрещин и других внутренних дефектов.
Сварка плавлением. Коррозионно-стойкая сталь типа 18-8 с однофазной аустенитной структурой при наплавке на нее меди и сплавов на медной основе обладает повышенной склонностью к образованию макротрещин Е6, 7], чему способствует проявление так называемого адсорбционно-расклинивающего эффекта. Для устранения появления трещин рекомендуется предварительно наплавлять на сталь подслой аустенитно-ферритного металла или применять промежуточную вставку [128]. Кроме этих вариантов, в работах [1, 2]описаны эксперименты по непосредственной сварке стали с медью.
В связи с необходимостью расширения области применения сварных соединений стали с медью и ее сплавами, в частности при изготовлении изделий, работающих в условиях циклического нагружения, проведены исследования прочности таких соединений [2]. Проводили сравнительную оценку циклической прочности разнородных сварных соединений стали 12Х18НШТ, содержащей 2,5 % ферритной фазы, с медно-никелевым сплавом МНД5-1 и с медью МЗр. На торцы стальных пластин толщиной 10 мм аустенитно-ферритной проволокой 08Х19Н9Ф2С2 предварительно наплавляли три слоя (каждый толщиной 1,5—2,5 мм). Наплавленные поверхности подвергали механической обработке для подготовки V-образных кромок к сварке. При этом следили за тем, чтобы в процессе механической обработки не был удален третий наплавленный слой. Сварку необходимо производить по этому третьему слою. Другие пластины подготовляли к сварке без предварительной наплавки торцов. Затем производили аргонодуговую сварку стальных пластин с пластинами из сплава МНЖ5-1 и медью присадочной проволокой из сплава МНЖКТ5-1-0,2-0,2.
Результаты испытания образцов на усталость при циклическом растяжении, выполненном на вибраторе в условиях постоянства амплитуды нагрузок, представлены на рис. 60 [2]. Циклическая прочность (на базе 2-105 циклов нагружений) сварных соединений меди МЗр и сплава МНЖ5-1 со сталью, выполненных без предварительной наплавки, такая же, как прочность сварных соединений сплава МНЖ5-1 со сплавом МНЖ5-1 и меди с медью.