Сварка порошковой проволокой
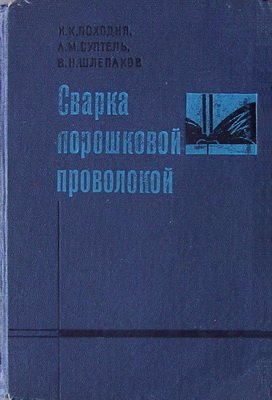
И.К. Походня, А.И. Суптель, В.И. Шлепаков
Наукова думка, 1972 г.
Сущность способа сварки порошковой проволокой. Порошковая проволока представляет собой непрерывный электрод трубчатой или другой, более сложной конструкции с порошкообразным наполнителем — сердечником. Сердечник состоит из смеси минералов, руд, ферросплавов металлических порошков, химикатов и других материалов. Назначение различных составляющих сердечника подобно назначению электродных покрытий — защита расплавленного металла от вредного влияния воздуха, раскисление, легирование металла, связывание азота в стойкие нитриды, стабилизация дугового разряда и др. Составляющие сердечника должны, кроме того, удовлетворять общепринятым требованиям, предъявляемым ко всем сварочным материалам: обеспечивать хорошее формирование швов, легкую отделимость шлаковой корки, провар основного металла, минимальное разбрызгивание металла, отсутствие пор, трещин, шлаковых включений и других дефектов, определенные механические свойства швов и сварных соединений и т. д.
Порошковые проволоки используются для сварки без дополнительной зашиты зоны сварки, а также для сварки в защитных газах, под флюсом, электрошлаковой. Проволоки, используемые для сварки без дополнительной защиты, называются самозащитными. Входящие в состав сердечника таких проволок материалы при нагреве и расплавлении в дуге создают необходимую шлаковую и газовую защиту расплавленного металла. В настоящее время наибольшее распространение получили порошковые проволоки для сварки в углекислом газе и самозащитные порошковые проволоки.
В зависимости от диаметра и состава порошковой проволоки сварка может осуществляться во всех трех пространственных положениях.
Азот в сварных швах на малоуглеродистых и низколегированных сталях — вредная примесь. Присутствие его вызывает снижение пластичности швов; при пересыщении сварочной ванны азотом повышается склонность металла шва к пористости.
Проблема предотвращения вредного влияния азота — одна из наиболее сложных проблем в металлургии сварки вообще и при сварке открытой дугой в особенности. Согласно современным представлениям азот в металле находится в виде атомов или группировок, содержащих атомы, а также в виде самостоятельных ни-тридных фаз. Растворению предшествуют поверхностные реакции и диссоциация молекул азота.
При сварке открытой дугой без дополнительной защиты зоны дуги заметное снижение содержания азота в металле швов достигается благодаря увеличению доли газообразующих и шлакообра-зующих составляющих в электродном материале [91, 95, 120]. Появление дополнительных количеств газа в зоне дуги и увеличение объема шлака приводят к снижению парциального давления азота у поверхности расплавленного металла и замедлению скорости его поглощения.
Таким образом, содержание азота в металле шва при дуговой сварке, по мнению большинства исследователей, определяется условиями насыщения металла азотом: температурой металла, пар-циальным давлением газа в атмосфере дуги, степенью диссоциации и возбуждения в дуге его молекул, а также кинетическими параметрами плавления и переноса расплавленного металла, в частности величиной поверхности взаимодействия с газами и временем.
При сварке порошковой проволокой характер плавления и переноса металла, температурные условия, формирование газошлаковой защиты и другие факторы, как было показано выше, отличаются от наблюдаемых при других способах сварки, что приводит к изменению условий взаимодействия металла с азотом. Рассмотрим особенности этих процессов.
Влияние условий сварки на насыщение металла азотом. Величина применяемых на практике напряжений дуги и сварочных токов для данной порошковой проволоки ограничена определенными пределами, т. е. для данной проволоки существует диапазон режимов, в пределах которого возможен нормальный технологический процесс сварки. Этот диапазон принято называть диапазоном рабочих режимов сварки. Нарушение его приводит к появлению дефектов в швах, резкому ухудшению технологических характеристик. Схематически такой диапазон представлен на рис, 48. Линии АБ и ВГ ограничивают пределы режимов сварки по напряжению дуги, линии АГ и БВ ~ по сварочному току. При пересечении диапазона линиями х — х' выделяется диапазон токов, которые могут быть использованы при данном напряжении, а линиями у — у' — диапазон напряжений для заданного тока.
Зависимости содержания азота в металле наплавки от напряжения дуги для двух выбранных токов (пересечение диапазона линиями у — у') представлены па рис. 49. Приведенные зависимости для проволок различного состава и конструкций идентичны. Повышение напряжения дуги приводит к увеличению содержания азота в металле.
Взаимодействие с азотом металла, легированного титаном и алюминием. Легирование металла шва титаном и алюминием при дуговой сварке приводит к изменению прочности и пластичности металла шва, склонности к образованию кристаллизационных трещин и других свойств. Металл швов с высоким содержанием титана и алюминия обладает низкой ударной вязкостью. Высокое содержание этих элементов повышает склонность к образованию кристаллизационных трещин 1113]. При сварке под флюсом конструкционных углеродистых сталей обнаружено снижение ударной вязкости металла швов, содержащих свыше 0,4% титана 1142].
С выделением нитридов алюминия связывают хрупкость швов (43, 44, 45] при сварке под флюсом сталей, успокоенных алюминием. Благоприятное влияние титана и алюминия на свойства металла швов при сварке под флюсом наблюдалось при комплексном легировании небольшими добавками [14, 70, 170].
В условиях ручной дуговой сварки наблюдается большой угар титана и алюминия, содержащихся в покрытии. В металле шва обнаруживаются незначительные количества этих элементов, при этом его свойства оказываются достаточно высокими [84, 179].
Введение в проволоку для сварки в углекислом газе титана и алюминия в ряде случаев вызывает охрупчивание металла шва [41, 76].
Влияние титана, алюминия и азота на свойства швов, выполненных открытой дугой, оценивается противоречиво. В работе [28] легирование алюминием во всех случаях считается неблагоприятным. В то же время в работах [53, 94, 105] показана возможность получения швов с высокими механическими свойствами при легировании алюминием и титаном раздельно или комплексно.
Титан и алюминий, обладающие большим химическим сродством к азоту, способны связывать его в жидкой стали в прочные нитриды и таким образом предотвращать пересыщение металла азотом.
При сравнительно высоких скоростях кристаллизации сварочной ванны нитриды, как правило, не успевают всплыть и остаются в металле, существенно влияя на его свойства.
Являясь сильными раскислителями, титан и алюминий восстанавливают из окислов элементы, обладающие меньшим сродством к кислороду. Это также оказывает большое влияние на механические свойства швов.
6. Поведение водорода при сварке порошковой проволокой
Водород поступает в зону дуги из материалов сердечника или покрытия, флюса или защитного газа, из окружающего воздуха, а также с поверхности свариваемого металла. Насыщение металла водородом в процессе сварки может служить причиной пористости металла. При повышенном содержании водорода в стали часто возникают локальные пересыщения в микрообъемах металла, что служит причиной появления ыежкристаллитных трещин, Наличие водорода снижает показатели пластических свойств и сопротивление разрушению металла шва, а при испытаниях на длительную прочность приводит к возникновению трещин, снижая тем самым усталостные свойства стали. Присутствие водорода является одной из основных причин образования флокенов в сварных швах.
В условиях низких температур растворимость водорода в железе и стали мала и составляет для чистого железа при комнатной температуре 7-10~8% 1731. В то же время в стали и сварных швах всегда содержатся значительно большие количества водорода.
Растворенные в железе атомы водорода связаны со свободными электронами металла, часть водорода может быть в виде ионов. Лишь незначительное количество избыточного водорода находится в кристаллической решетке железа, большая часть его концентрируется в микропустотах металла в газообразном состоянии либо химически связана в соединения с примесями металла (24, 73, 159].
Растворимость водорода в жидком железе изучали многие исследователи [57, 73, 135, 159, 184]. Согласно расчетам и экспериментальным данным 157, 135] максимум растворимости достигается при температуре 2450° С. Понижение растворимости по мере приближения к точке кипения объясняется влиянием паров железа, уменьшающих парциальное давление водорода. Растворимость водорода в жидком железе при парциальном давлении водорода рн равном 1 атм, в интервале температур 1800—2270°К описывается уравнением [56].
ПОРИСТОСТЬ ШВОВ ПРИ СВАРКЕ ПОРОШКОВОЙ ПРОВОЛОКОЙ
7. Условия зарождения и развития пор в сварных швах
Пористость — один из наиболее распространенных дефектов сварных швов при дуговой сварке. Образование пор является следствием выделения газов из металла при кристаллизации сварочной ванны. Выделение газов происходит при снижении растворимости или протекании в жидком металле химических реакций. Для описания механизма зарождения и развития пор при сварке сталей целесообразно использовать кинетический метод.
В общем случае процесс образования пор можно разделить на две стадии — зарождение и развитие газового пузырька. Для зарождения пузырька необходимы, по крайней мере, три условия: ]) перенасыщение жидкого металла газом; 2) наличие центра; 3) определенная выдержка элементарного объема жидкого металла (инкубационный период) при соблюдении первых двух условий, так как скорость образования газового зародыша критического размера конечна (1331. Развитие пузырька происходит во времени и определяется скоростью атомарной и конвективной диффузии, концентрацией газа в металле (степенью перенасыщения), а также скоростью его десорбции. Сформулированные условия зарождения и развития пузырька вытекают из общих принципов теории фазовых процессов [133].
Перенасыщение жидкого металла газами. Перегретый металл капель и ванны, взаимодействуя с активизированными дугой водородом и азотом, при определенных парциальных давлениях этих газов в атмосфере дуги адсорбирует их в количествах, значительно превышающих стандартную растворимость водорода и азота в металле.
Выше {см. параграфы 5 и 6) отмечалось, что растворимость водорода и азота в жидком железе достигает максимума при температуре 2300—2400" С и снижается с уменьшением температуры металла. В результате этого при охлаждении жидкого металла может быть достигнуто значительное перенасыщение сварочной ванны газами во всем ее объеме.
10. Самозащитная порошковая проволока
К самозащитной порошковой проволоке предъявляется ряд требований, ог выполнения которых зависит возможность ее широкого производственного применения. К числу этих требований относится обеспечение высокой производительности процесса, широкого диапазона рабочих режимов сварки, хорошего формирования швов и отделимости шлаковой корки, малых потерь металла на разбрызгивание, высоких механических свойств металла шва, благоприятных гигиенических характеристик и др. Помимо этого, проволока должна быть технологичной в изготовлении.
Общим для всех видов порошковой проволоки требованием является обеспечение равномерности плавления сердечника и оболочки. Для проволоки трубчатой конструкции выполнение этого требования можно обеспечить увеличением доли металлических порошков в сердечнике, выбором легкоплавких композиций шлакообразующей части, уменьшением толщины оболочки.
Ограничение количества газообразующих материалов, которые можно ввести в сердечник, и их неблагоприятное расположение по отношению к металлу оболочки не позволяют при сварке проволокой трубчатой конструкции достичь хорошей защиты расплавленного металла от воздуха. Использование проволоки двухслойной конструкции позволяет эффективно защитить расплавленный металл от воздуха и обеспечить высокие механические свойства металла шва.
Металлургические процессы при сварке открытой дугой порошковой проволокой определяются композицией сердечника. Как показали исследования процессов, происходящих при нагреве и плавлении сердечника, большие объемы и равномерное выделение газов из сердечника и раннее образование шлакового расплава улучшают условия защиты зоны дуги от воздуха. Композиция сердечника проволоки должна обеспечивать сочетание защитных свойств с благоприятными сварочно-технологическими свойствами, хорошей рафинирующей способностью шлаков, достаточной раскисленностью и легированием металла, высокой стойкостью против трещин и пор. Разработанные составы сердечников порошковой проволоки промышленных марок являются оптимальными, в той или иной мере удовлетворяющими перечисленные выше требования.
11. Порошковая проволока для сварки в углекислом газе
Углекислый газ является эффективным средством зашиты от влиянии воздуха жидкого металла при дуговой сварке. В настоящее время сварка в углекислом газе — наиболее распространенный способ механизированной сварки. Он отличается высокой производительностью (в несколько раз превышающей производительность ручной дуговой сварки), дешевизной, простотой, возможностью выполнения сварочных работ в различных пространственных положениях в широком диапазоне толщин свариваемых сталей. Сварка в углекислом газе широко применяется при изготовлении металлоконструкций из малоуглеродистых конструкционных и легированных сталей.
При сварке сталей общего назначения в качестве электродного материала обычно используется проволока сплошного сечения, легированная марганцем и кремнием, чаще всего марки Св-08Г2С.
Наряду с перечисленными выше преимуществами сварки проволокой Св-08Г2С в углекислом газе следует отметить и существенные недостатки — повышенное разбрызгивание электродного металла и посредственный внешний вид швов, выполненных проволокой диаметром 1,6—2,0 мм в диапазоне наиболее употребляемых сварочных токов (250—400 а), повышенную прочность металла шва и в ряде случаев недостаточную его пластичность.
Неблагоприятные сварочно-технологические свойства проволоки Св-08Г2С в значительной степени связаны с крупнокапельным переносом электродного металла и неустойчивостью дуги при сварке на малых плотностях тока. При увеличении плотности тока резко возрастает коэффициент наплавки и ухудшается формирование швов. Уменьшить размеры капель электродного металла и повысить устойчивость горения дуги можно при использовании проволоки малого диаметра (0,8—1,2 мм).
Мелкокапельный и даже струйный перенос электродного металла удается получить при нанесении на поверхность проволоки активирующих веществ 116, 42]. Однако широкого промышленного применения активирование проволоки пока не получило из-за неблагоприятной формы и ухудшения механических свойств сварных швов.
Одним из наиболее эффективных средств улучшения процесса сварки в углекислом газе является применение порошковой проволоки. При введении в сердечник материалов с низким потенциалом ионизации повышается устойчивость горения дуги даже при применении проволоки больших диаметров (3—4 мм и выше). Подбором композиции шлака можно достичь благоприятного переноса электродного металла и обеспечить минимальное его разбрызгивание.
16. Специальные случаи применения порошковой проволоки
К специальным относятся случаи применения порошковой проволоки, когда условия сварки и требования к сварному соединению вызывают необходимость применения специальной аппаратуры и техники сварки, а часто и порошковой проволоки с особыми Свойствами.
Ниже рассмотрены примеры специального применения порошковой проволоки.
Сварка вертикальных швов с принудительным формированием. Вертикальные швы на металле средней толщины (8—30 мм) свариваются в основном вручную покрытыми электродами. В последнее время все большее распространение получает полуавтоматическая газоэлектрическая сварка тонкой проволокой со свободным формированием шва. Принудительное формирование кристаллизующейся поверхности сварочной ванны позволяет резко поднять силу тока, увеличить скорость подачи электродной проволоки и повысить производительность процесса. Этот метод в сочетании с электрошлаковым процессом получил большое распространение в промышленности и строительстве.
Электрошлаковой сваркой соединяют в основном металл толщиной 20—30 мм и более. Для меньших толщин электрошлаковый процесс не всегда целесообразен.
Для устойчивости электрошлакового процесса нужна шлаковая ванна определенного объема. При малой толщине металла это требует значительного увеличения зазора между кромками. Так, например, при сварке листов толщиной б = 18 мм зазор составляет ^25—30 мм. В связи с этим приходится тратить большое количество ""присадочной проволоки, скорость сварки снижается. Основной металл, находясь длительное время в непосредственном контакте со шлаковой ванной, перегревается, его механические свойства ухудшаются. Для восстановления же этих свойств в некоторых случаях требуется дорогостоящая термообработка соединений. Часто ее осуществить нельзя, поэтому приходится отказываться от электрошлаковой сварки.
Дуговая сварка под флюсом вертикальных швов с принудительным формированием распространения не получила из-за неустойчивости процесса, большого разбрызгивания, сложности дозировки флюса, шунтирования дуги шлаком, вызывающего непровары и пр.
В ИЭС им. Е. О. Патона разработан новый способ электродуговой сварки вертикальных швов с принудительным формированием порошковой проволокой [98].