Справочник по холодной штамповке
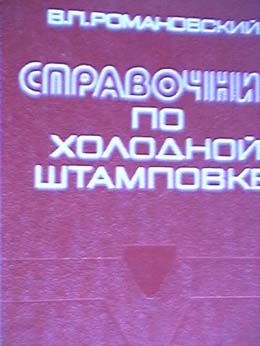
Романовский В.П.
Машиностроение, 1979 г.
Типовыми крупногабаритными деталями, получаемыми методомвытяжки тонколистового металла, являются так называемые облицовочные детали кабин и кузовов автомобилей, детали мотоциклов и мотороллеров и т. п. (рис. 144). Эти детали отличаются сложной и несимметричной пространственной формой, а технологический процесс их изготовления имеет некоторые специфические особенности.
При вытяжке деталей сложной и несимметричной пространственной формы величина деформацииметалла различна в разных местах заготовки.
Для того чтобы обеспечить получение детали сложной пространственной формы из плоской заготовки, необходимо создать разные условиятеченияметалла по контуру заготовки: в одних участках облегчить перемещение металла из-под прижимного кольца, а в других участках затормозить его путем применения вытяжных или тормозных ребер и порогов на матрице или прижимном кольце. В большинстве случаев
вытяжные штампы для крупных кузовных деталей снабжены одним, а в некоторых местах двумя и даже тремя рядами вытяжных ребер.
Сильный прижим и торможение заготовки увеличивают сопротивлениетечениюметалла из-под прижимного кольца и способствуют лучшему обтягиванию металла по формепуансона и распространению деформации по всей площади заготовки. При этом происходит более полное использование пластичностиметалла в результате деформациисредней части заготовки за счет уменьшения толщины последней.
В начале процессавытяжки деталей сложной формыпуансон соприкасается с заготовкой лишь в отдельных местах, а большая часть заготовки находится вне контакта с, рабочими частями штампа. Эта „свободная" поверхность заготовки, подвергаясь тангенциальному сжатию, легко образует гофры и волны при вытяжке. Тангенциальное сжатие можно уменьшить путем значительного увеличения растягивающих напряжений.
На рис. 145 показано влияние вытяжных ребер на распределение напряжений во фланце. Сплошные линии соответствуют распределению напряжений без ребер, а штриховые — распределению напряжений в результате натяжения двумя ребрами, В результате напряжения тангенциального сжатия значительно уменьшены.
Применение вытяжных ребер Препятствует возникновению гофров или складок вследствие того, что ребро, образованное на фланце заготовки, обладает большей жесткостью и большей устойчивостью на продольный изгиб.
При вытяжке деталей сложной формыметаллфланца не вытягивается полностью из-под прижимного кольца, а остается до конца вытяжки и в дальнейшем удаляется обрезкой, Поэтому в данном случае необходимо предусматривать технологические припуски значительных размеров, что приводит к нежелательному увеличению расхода металла.
Повышение растягивающих напряжений при вытяжке деталей сложной пространственной формы позволяет значительно уменьшить упругие деформации после вытяжки и в особенности после обрезки фланца.
Асимметричность и сложность формы деталей и неравномерность деформации по различным участкам заготовки не позволяют применить для оценки степенидеформациикоэффициентывытяжки цилиндрических деталей.
Как правило, вытяжка деталей сложной пространственной формы производится за одну операцию из-за высоких требований к качеству поверхности и недопустимости появления на ней следов от предыдущей вытяжки.
Ввиду большого разнообразия формы облицовочных деталей автомобилей и их непрерывного изменения до настоящего времени не создано единого метода технологических расчетов. Однако в результате проведенных исследований вытяжки автокузовных деталей и на основании обобщения производственного опыта созданы соответствующие технологические рекомендации.
С целью типизации процессовштамповки кузовных деталей в ряде стран установлена технологическая классификация деталей сложной пространственной формы. В США Комитет по штампуемости разработал классификацию деталей по технологической сложности формообразования. Установлено семь технологических групп, иллюстрированных примерами деталей. Первая группа — детали, изготовляемые гибкой и отбортовкой, вторая — гибкой с неглубокой вытяжкой, третья, четвертая и пятая — глубокой вытяжкой деталей различно, го параметра, шестая и седьмая — вытяжкой с интенсивным складно, образованием.
Технологическая сложность деталей оценивается относительным удлинением в наиболее деформируемом участке заготовки. Эта оценка недостаточно правильна, так как при вытяжке деталей сложной формы возникает не одноосное, а двухосное растяжение. Как пока, зал А. Д. Томленое, в этом случае создается повышенная устойчивость пластической деформации, осуществляемой при значительном уменьшении толщины материала. В результате критическая величина интенсивности деформаций, при которой происходит потеря устойчивости, в два раза выше, чем при одноосном растяжении.
Построение вытяжных переходов для крупных деталей сложной формы производится в следующей последовательности (145]:
1) определение положения детали в штампе;
2) технологическая корректировка формы детали в вытяжном переходе;
3) определение величины и расположения технологических припусков;
4) определение формы и расположения технологических вырезов — окон;
5) выбор формы прижимной поверхности вытяжного штампа;
6) установление количества и расположения тормозных ребер (порогов);
7) определение способа фиксации вытяжного перехода в обрезном штампе.
Положение детали в штампе должно быть оптимальным и должно удовлетворять следующим условиям: беспрепятственный вход пуансона в матрицу; получение возможно меньшей глубины вытяжки; увеличение площади соприкосновения пуансона с заготовкой, для чего необходимо, чтобы прижимная поверхностьматрицы соответствовала нижней, поверхности пуансона-, отсутствие перетягивания металла
через вершинупуансона на другую сторону; равномерное распределение давления прижимного кольца на матрицу.
Форма вытяжного перехода должна по возможности полностью соответствовать форме готовой детали. В случае недостаточно технологичной формы детали в форме вытяжного перехода должны быть предусмотрены некоторые изменения, улучшающие условия формообразования. С этой целью отдельным участкам придается положение, наиболее благоприятное для вытяжки, а также производится смягчение резкихпереходовформыповерхности путем увеличения радиусов закругления (если это необходимо).
Величина и расположение технологических припусков зависят от требуемой степени торможения заготовки под прижимом, от формы и расположения прижимной поверхности, от условий выполнения последующей обрезки.
На рис. 146 приведены различные способы повышения интенсивности торможения фланца заготовки под прижимом: а — увеличение усилия прижима; б — увеличение ширины фланца; в—применение вытяжных (тормозных) ребер применение перетяжных порогов.
Первый способ наиболее распространен, но не всегда достигает цели; второй способприводит к повышенному расходу металла; третий и четвертый способы наиболее целесообразны.