Прикладная электрохимия
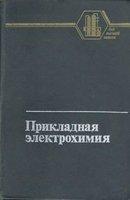
Томилов А.П.
Химия, 1984 г.
Немногим более половины производимого цинка получают пирометаллургическим способом, остальную часть — гидроэлектрометаллургическим способом. В России способ гидроэлектрометаллургии был впервые осуществлен в 1909 г. инженером Лащинским, которому принадлежит идея применения анодов из свинца. Увеличение за последние 40 лет почти в два раза мирового производства цинка следует отнести в основном за счет развития именно гидроэлектрометаллургического способа. В СССР цинк почти целиком производят этим путем.
Гидроэлектрометаллургическое получение цинка. цинк получают в гидроэлектрометаллургии главным образом методом электроэкстракции.
Обжиг концентратовсульфидных цинковых руд ведут при такой температуре (850—900 °С), чтобы основным продуктом был оксид цинка, а сульфат цинка образовывался в малом количестве. Сульфиды сопровождающих металлов — свинца, железа, кадмия, меди — также образуют оксиды. Нежелательный смешанный оксид ZnO-Fe2O3 (феррит) образуется при температурах около 600 "С; реакция интенсифицируется повышением температуры, но для ее протекания требуется определенное время, так как она связана с диффузией в твердом состоянии.
В настоящее время обжиг цинковых концентратов на всех заводах проводится в печах КС (см. рис. 4.2). Размер зерен 50—70 мкм. Доля концентрата, уносимого с газами и улавливаемого в виде пыли, достигает в производстве цинка 40—70% массы концентрата. Около 90% этого количества возвращается на выщелачивание. Содержание SO2 в газах печей КС высокое (7,5—9%), поэтому такие газы могут быть использованы для производства серной кислоты.
Тепло, выделяемое при окислительном обжиге, позволяет поддерживать температуру печи на уровне 900—950 "С, а в случае необходимости и выше. Имеются данные о том, что высокая скоростьпроцессаобжига в печах КС и отсутствие постоянного контакта между отдельными оксидамиметаллов сильно уменьшает образование ферритов, поэтому отпадает необходимость в специальных мероприятиях для возвращения ферритного цинка из кеков в растворы для получения цинка.
Для выщелачивания огарка используют отработанный кислый электролит (замкнутый процесс). Эта операция позволяет разделить компоненты огарка между раствором и остатком от выщелачивания. В зависимости от концентрации кислоты и температуры выщелачивания, а также от свойств отдельных оксидов распределение каждого из компонентов между раствором и остатком может быть различным. В остатке от выщелачивания находится обычно основная часть свинца, кальция, магния, алюминия в виде сульфатов и оксидов, а также диоксид кремния и ферритцинка (при содержании кислоты в отработанном электролите до 100 г/л), половина всей меди, золото и серебро.
Электролизеры работают без диафрагмы: выходцинка по току в кислом электролите достаточно высок и в разделении электродных пространств нет необходимости. Размерыэлектродов обычно составляют h-l= 1000x650 мм; ванны имеют уже установившиеся в практике высоту и ширину (I —1,5 м и 1 м), а длина зависит от числа электродов, т. е. от желаемой силы тока, и колеблется в пределах 2—3 м.
Усредненные показателиработы заводов, производящих цинк гидроэлектрометаллургическим способом: Вт=90%, U = =3—4 В (см. табл. 4.1); расходэлектроэнергии 3200— 3300 кВт-ч/т.
Чистота цинка, получаемого при электролизе, довольно высокая и может быть еще увеличена при более тщательной очистке электролита. Электролитический цинк отвечает маркам Ц0, Ц1, Ц2.
Получение цинка высокой чистоты. цинк марки ЦВ, содержащий 99,99% Zn, получают дистилляциейкатодных металлов. Для получения цинка еще более высокой чистоты (99,999%) разработан метод перечистки: электролитический металлрастворяют химически или анодно. При химическом растворении полученные электролиты подвергают глубокой очистке, электролиз проводят в электролизере с диафрагмой и с нерастворимыми анодами. При анодномрастворении осуществляют двух-стадийную очистку: вначале проводят анодноерастворение обычного промышленного металла и его катодное осаждение, а затем повторное переосаждение полученного металла.
Электролитическое получение порошка цинка. Порошок цинка нашел довольно большое применение в производстве изделий из полимерных материалов, в лакокрасочной промышленности, в гидрометаллургии для цементации меди и кадмия, золота, в качестве катализатора.
Определенное значение имеет электролитический метод получения порошка цинка.
Порошок цинка получают при электролизе щелочных цин-катных растворов. Наиболее дисперсные осадки со среднимразмером частиц 30—40 мкм получают из электролита, содержащего 0,050—0,1 моль/л Zn2+, 3,0 моль/л NaOH, 0,05 г/л олеата натрия или смесь 0,05 г/л олеата натрия и 3—5 г/л Жидкого стекла, при 20°С и iK=—1,5 кА/м2; продолжительность непрерывного электролиза до 60 мин. Катоды выполняют в виде цилиндрических стержней из титана, аноды из цинка И нержавеющей стали с индивидуальным питанием током.
Цинковую губку, снятую с катода, загружают на некоторое время в 0,5%-ный раствор жидкого стекла для стабилизации частиц или промывают этим раствором на фильтре. Затем губку промывают теплой и холодной водой для полного удаления Щелочи и сушат в вакуум-сушилках при 55—60 °С.