Металлургия железа
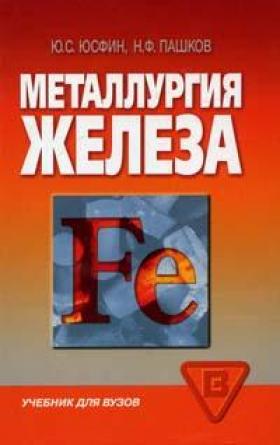
Юсфин Ю.С., Пашков Н.Ф.
"ИКЦ ""Акаддемкнига""", 2007 г.
При отнятии кислорода у оксида на поверхностиматериала происходит местное изменение соотношения Me—О. Первичный металл, оказавшийся свободным, выделяется в виде отдельных зародышей. Число и распределение последних зависят от структурыповерхности оксида. Для роста зародыша необходим транспорт металла от места отнятия кислорода к зародышу; он происходит путем диффузии ионов металла и электронов в решеткеоксида и по поверхности. Скорость отнятия кислорода, с одной стороны, и диффузия металла, с другой, определяют, имеется ли в области между первично образовавшимися зародышами перенасыщение металлом, необходимое для образования следующих зародышей, и соответственно растет ли плотность зародышей. Плотность и форма зародышей, а также тип их развития обусловливают превращениезародышей в плотный слой новой фазы, отделяющей основной оксид от газовой фазы, или в губку, через поры которой газ имеет непосредственный доступ к исходному веществу.
При восстановлении до металла чаще наблюдается образование пористой губки. Вюстит при восстановлениимагнетитаоксидомуглерода растет в виде беспористого слоя. При восстановлении пористых руд часто наблюдают игольчатые кристаллы металла, которые врастают в зерна оксида. Выделениеметалла в оксиде обусловливает появление напряжений, приводящих к разламыванию зерен и образованию новой поверхности. Образование и рост зародышей могут привести к изменениям объема и поверхности пор.
В общем случае при рассмотрении любого восстановления приходится решать два основных вопроса: во-первых, в какой средепроходит акт химического взаимодействия, приводящего к отнятию кислорода от оксида (от этого зависит та или иная последовательность отдельных стадий процесса); во-вторых, в зависимости от схемы процесса, какая стадия является самой медленной, определяющей общую скоростьпроцессавосстановления в целом. В общем случае взаимодействие, сопровождающееся отнятием кислорода от оксида металла, может происходить в газовой фазе, на границе металл—оксид или низший оксид—высший оксид. Иногда основное место взаимодействия меняется во время протекания реакции, еще более затрудняя ее анализ. Однако чаще всего полагают неизменным место отнятия кислорода от оксида; основные теориивосстановленияоксидовметаллов исходят из этого основного предположения. А.А. Байков одним из первых предложил цельную схемумеханизмавосстановления оксидов. Процесс состоит из двух стадий: диссоциацииоксидаметалла МеО и окисления восстановителя В кислородом оксида. Несомненные преимущества этой модели — простота и удобство для расчетов. Время возникновения теории — первое двадцатилетие XX века, но и сейчас эта схема широко применяется при расчетах расходов тепла при восстановительных процессах и составлении тепловых балансов этих процессов. Накопление экспериментальных данных привело к выводу о малой роли диссоциацииоксидов в процессе восстановления, так как реальные упругостидиссоциации оксидов, служащие, как известно, мерой их прочности, малы настолько, что ими можно пренебречь.
3.1. Железорудные материалы и их подготовка к процессу Выбор сырья для металлизации проводят в соответствии с требованиями, предъявляемыми к качеству металлизованного продукта со стороны его дальнейшего передела (доменное или сталеплавильное производство), а также с учетом физико-химических изменений, которым оно подвергается в процессе металлизации. Железорудные материалы для производства губчатого железа должны удовлетворять следующим основным требованиям: по возможности высокое содержание железа при низком содержании серы, фосфора, щелочей и примесей цветныхметаллов (медь, никель, хром, цинк, свинец и др.), оказывающих большое влияние на качество стали и технико-экономические показатели выплавки ее в электропечах; высокая газопроницаемостьшихты в восстановительном агрегате; высокая восстанови-мость; отсутствие склонности шихты к слипанию при достаточно больших температурах восстановления; высокая прочность при восстановлении. Химический состав. В связи с тем что процессыметаллизации при получении губчатого железа протекают при умеренных температурах (без расплавления), пустая порода и примеси в исходном сырье полностью переходят в металлизованный продукт. известно, что от содержания железа и кислой пустой породы в губчатом железе существенно зависит стоимость выплавки стали, так как они влияют на расход металлизованного продукта для выплавки 1 т стали, расходэлектроэнергии для расплавления образующегося шлака, расход извести, потери железа со шлаком. С этих позиций содержание железа должно быть максимальным, а содержание кремнезема — минимальным. Расчет и практика производства показали, что содержание железа в железорудных материалах желательно иметь в пределах >68—69%, а количество кислых оксидов не должно превышать 3% (в металлизованном 5%), так как в противном случае использование методов бездоменного получения металла становится экономически невыгодным. Пустая порода большинства руд и окатышей состоит, в основном, из кремнезема. При выплавке стали в электропечахосновностьшлака (СаО + MgO)/(Si02) поддерживают в пределах 1,5—2,0, вводя для офлюсования пустой породы известь. При увеличении содержания кремнезема в пустой породерезко возрастают расходыэлектроэнергии и извести, снижается скоростьплавления шихты, увеличиваются потери железа со шлаком, осложняются уборка и вывоз шлака, поэтому для получения губчатого железа стремятся использовать богатое железорудное сырье с низким содержанием кремнезема. Из применяемых в мире окатышей для прямого получения железа наиболее высокое содержание оксидакремния отмечено в окатышах ОЭМК. При современных средствах обогащения возможно получение Лебединского концентрата с содержанием 0,4—0,6% кремнезема, однако при этом затраты на обогащение значительно превышают экономию на электроплавку. Тем не менее очень низкое содержание кремнезема может привести к разрушению, разбуханию и слипанию шихты при восстановлении, что снижает эффективность процесса. В связи с этим возникает проблема использования в качестве шихты для металлизации офлюсованных железорудных материалов. Присутствие в шихтовых материалахоксидовкальция и магния повышает их восстановимость и прочность при восстановительно-тепловой обработке, уменьшает разрушение при низких и склонность к слипанию при высоких температурах, улучшает условиянауглероживания окатышей в процессе их металлизации. Требования к основности различаются в зависимости от свойств исходных железорудных материалов и типа процесса металлизации. Так, если для установок Мидрекс значение основности специально не оговаривается (обычно оно составляет 0,5—0,8), то для установок ХиЛ оно должно быть >0,9. Для процессаметаллизации в условиях Оскольского электрометаллурптческого комбината основность окатышей из богатого Лебединского концентрата рекомендуется > 1,0-1,2. При определенных условиях может возникнуть целесообразность получения и применения легированных металлизованных окатышей. Идея добавки в шихту окатышей легирующих добавок представляется интересной, так как дает возможность более равномерно распределить эти добавки в массе стали, их применять эти добавки в виде оксидов, которые подвергнутся восстановлению вместе с железом в восстановительном агрегате, что значительно снизит цену на эти легирующие добавки. Учитывая тот факт, что в процессевосстановления вгхедные примеси практически из шихты не удаляются, следует восстанавливать железорудные материалы с минимальным содержанием вредных примесей (сера, фосфор, медь, мышьяк и др.). Верхний предел их содержания определяется маркой выплавляемой стали и типом сталеплавильного процесса, однако, в любом случае содержание серы и фосфора не должно превышать 0,015—0,02%. Серу в большей степени можно удалить при производстве окисленных окатышей из железорудного концентрата. При восстановлении из железорудных материалов удаляется 40—80% S в виде соединений H2S и COS, что в некоторых случаях, когда для конверсии используется колошниковый газ, может привести к отравлению катализатора. В этом случае технологический газ для очистки от серы перед подачей в реформер приходится пропускать через губчатое железо, используя его как охлаждающий газ. Фосфор при окислительном обжиге не удаляется, поэтому для металлизации можно применять лишь руду с низким содержанием фосфора. В окатышах ОЭМК содержится ~ 0,01% Р. Наличие оксидов щелочно-земельных металлов (Na20, К20) нежелательно (допускается до 0,02%), так как они способствуют разбуханию и разрушениюматериалов в процессевосстановления и тем самым ухудшению газопроницаемостистолбашихты и показателейпроцесса металлизации. Содержание двухвалентного железа в окисленных окатышах ОЭМК в среднем составляет 0,35%, однако бывают случаи, когда в пульпу для окомкования добавляется неконтролируемое количество шламов с установок металлизации, в которых содержатся металлическое железо и до 10% углерода, в результате чего в обжигаемых окатышах создаются восстановительные условия и магнетит не окисляется. Тогда содержание двухвалентного железа поднимается до 1 % и выше и обязательно наблюдается резкое снижение степени металлизации. Фракционный состав железорудных материалов играет большую роль в процессах прямого получения железа в шахтных печах. В большинстве случаев, в частности при металлизации в шахтных печах, стремятся к получению окисленных окатышей с большей пористостью, обеспечивающей высокую окисленность их на стадии обжига и высокую восстановимость на стадии металлизации. При восстановлении высокоокисленных (гематитовых) окатышей образуется мелкопористая структура, в результате чего зерна гематита восстанавливаются полностью до железа. При восстановлении зерен магнетита, присутствующего в окатышах при неполном окислении, вокруг них образуется плотная металлическая оболочка, что препятствует их дальнейшему восстановлению.