Медь и ее сплавы
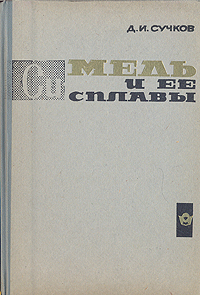
Сучков Д.И.
Металлургия, 1967 г.
Влияние различных примесей и добавок на свойства меди
Как видно на рис. 1, примеси всех элементов и особенно сильно Р, As, Sb, Al, Fe, Sn, снижают электропроводность меди.
Благоприятное влияние кислорода на электропроводность меди при содержании его в пределах 0,02—0,08% можно объяснить тем, что остающийся при плавке в меди кислород способствует более полному удалению водорода и других (окисляющихся) примесей из расплава.
Будучи почти нерастворимым в меди при комнатной температуре, весь содержащийся в меди кислород находится в 'виде обособленных шаровидных твердых и хрупких частичек СuО, образующих с медью эвтектику.
В структуре литой меди цепочки или тонкокружевные участки смеси Сu2гО + Сu располагаются между кристаллами Си, что снижает пластичность (обрабатываемость давлением) меди как в горячем, так и в холодном состоянии. Еще более разрушительное (влияние при обработке давлением оказывают местные скопления Сu2О, образующиеся в результате прорыва пленок закиси при разливке в формы.
Эталоны для определения количества Сu2О в литой меди металлографическим методом приведены на рис. 2.
Медь имеет сильно выраженное химическое сродство к кислороду. Поверхность только что залитой <в форму меди имеет красивый цвет морской воды. Буквально через несколько секунд поверхность жидкой меди теряет свой цвет и блеск, становится белой — матовой — покрывается пленкой закиси Си2О.
При нагревании слитков меди и при отжиге при температурах не выше 900° С кислород глубоко в медь не проникает.
Особенности технологии меди
Плавка и литье слитков красной меди, предназначаемых для обработки давлением, имеет следующие особенности.
Основная масса медных слитков для получения полуфабрикатов различного назначения отливается на добывающих и рафинирующих заводах.
Производство листов, лент, прутков, профилей, труб, проволоки, тонкостенных штампованных изделий и т. д. требует, чтобы исходный слиток был высокого качества. Очень жесткие, но обоснованные требования предъявляются к слиткам меди, предназначаемым для изготовления электрических проводов (шин, проволоки, троллейных проводов, соединителей и т. д.).
Отливка больших медных слитков топочной меди в прошлом проходила так: на полу литейного цеха лежала чугунная плита, на ней устанавливалась чугунная сборная бездонная форма, стенки которой смазывали или известковым молоком, или костяной мукой с водой, или органической смазкой. После высыхания смазки изложница заполнялась металлом; на нижней поверхности слитка, соприкасавшейся с чугунным поддоном, где смазка частично смывалась струей металла, наблюдались пузыри, а иногда и приварка, и тогда слиток с большим трудом Отрывали от поддона.
МЕДНОЦИНКОВЫЕ СПЛАВЫ
Медноцинковые, или латунные, сплавы имеют широкое и весьма разносбразное применение <в технике.
Латунь изготовлялась еще за 1500 лет до н. э. По сообщениям Аристотеля (4 в. до н. э.). латунь впервые начали готовить моссинэки, жившие на побережье Черного моря к западу от Трапезунда. По более поздним описаниям моссинэкская медь отличалась чрезвычайным блеском и белизной. При получении ее примешивали к меди особый сорт тамошней земли, которая плавилась вместе с медью. С уверенностью можно считать, что к меди добавляли галмей (или каламин) и получали при этом латунь.
До 1781 г. латунь готовили путем сплавления меди с цинковой рудой (галмеем) и древесным углем. Получение латуни путем сплавления меди и цинка было введено в производство лишь в 1781 г.
В России латунь, применяемую в технике, часто называли «желтой медью», потому что большая часть разновидностей технических латуней имеет желтый цвет разных оттенков.
Высокая прочность и коррозионная стойкость специальных латуней являются главной причиной того, что эти латуни находят широкое применение в качестве заменителей оловянистых бронз даже при изготовлении статуй. Состав статуйных латуней колеблется в пределах, %:
Си.....72—88
Zn.....25—10
Sn.....0—3,0
Pb.....0—3,0
Большой популярностью в качестве заменителя оловянистых бронз пользуется латунь марок ЛК80-3 и ЛКС80-3-3. Эта латунь отличается высокой жидкотекучестью, дает плотное литье с чистой поверхностью; применяется в судостроении.
По зарубежным данным латунь, содержащая 42% Си; 16% Si; 41% Zn; 1,0% Pb, с успехом применяется для литья под давлением. Примесь железа в этих латунях вредна, по-видимому, вследствие возможного образования твердых и хрупких интерметаллических соединений железа с кремнием и цинком.
При изготовлении из специальных латуней литых фасонных деталей, работающих в соприкосновении с морской водой, необходимо иметь в виду, что по имеющимся данным эти латуни при наличии внутренних напряжений обладают чувствительностью к морской воде, что может привести к их преждевременному разрушению. Особенная склонность к коррозии наблюдается у латуней со структурой р. Осторожный отжиг литых деталей с медленным нагревом примерно до 300° С может снять остаточные напряжения и устранить отмеченный недостаток.
Особенности плавки
и литья медноцинновых сплавов
Безвозвратные потери цветных металлов
Недостаток цветных металлов для полного покрытия всех потребностей промышленности СССР, сложность извлечения из руд с относительно малым процентным содержанием в них металла делают эти металлы дефицитными и дорогими. Перед добывающей и обрабатывающей цветные металлы промышленностью, перед всеми потребителями полуфабрикатов и изделий встает очень важная задача — всесторонней экономии цветных металлов и снижения их стоимости.
Особая ответственность в этом деле ложится на литейное производство.
По зарубежным данным, при плавке в печах «Аякс— Фиатт» разных латунных сплавов, содержащих 72—57% Си, при разных вариантах плавки с разными видами шихты и поверхностной защиты металла (древесный уголь, соляной флюс, флюс с бурой)
Влияние примесей и добавок других элементов на свойства бронзы
Если в сплав со структурой однородного твердого раствора вводится новый компонент, это вызывает те или иные изменения в структуре и тесно связанные с ней изменения свойств. Ниже рассматривается влияние некоторых добавок и примесей.
Фосфор
Фосфор впервые начали вводить в бронзы во Франции в 1854 г.
Фосфор часто вводят в качестве добавки в оловянистые бронзы, но в небольших количествах, редко превышающих 1%. Эти добавки могут применяться с различной целью. Во-первых, фосфор вводят как раскислитель, восстанавливающий закись меди по формуле:
2Р + 5Сu2О = Р2О5 + 10Cu.
Но фосфор не может восстанавливать SnO2 вследствие высокой химической стойкости этого соединения. По этой причине фосфор как раскислитель при изготовлении бронз можно применять лишь в случае ведения плавки на шихте из свежих металлов, когда вначале плавится одна чистая медь. В этот период плавки в меди образуется Си2О. Перед введением в расплав Sn медь надо раскислить, для чего в расплав вводится фосфор обычно в виде лигатуры, содержащей 12—14% Р, остальное — медь. При обычной плавке медь содержит до 0,2% кислорода. Чтобы связать этот кислород и выделить его из расплава в виде Р2О5, по расчетам требуется ввести 155 г Р на 100 кг Си, если к этому прибавить не менее 20% Р на неизбежный угар его, то необходимое количество фосфора будет равно ~ 180 г. Для этого на каждые 100 кг Си надо ввести 1250 г лигатуры, содержащей -14% Р.
Бесполезный угар фосфора при использовании его в качестве раскислителя получается наименьшим, если фосфор вводить после удаления шлака с 'поверхности расплава. Это можно объяснить тем, что плавающий поверх металла флюс или шлак затрудняет тесное соприкосновение лигатуры с металлом: последняя плавает на поверхности и это усиливает потери Р в результате его окисления и улетучивания (температура кипения фосфора 280,5° С).
Неметаллические включения
В основном неметаллические включения — это оксиды доходящие до 98%, сульфиды, фосфиды, силициды, а также попадающие в расплав и задержавшиеся в нем частички огнеупорной футеровки печей, тиглей, ковшей.
Общее количество неметаллических включений в окисленной бронзе доходит до 0,4—0,5%. в раскисленной (точнее, в рафинированной) бронзе оно снижается до 0,0042%.
Есть предложение производить очистку бронзы от окисных включений пропусканием жидкого металла через раскаленный (до 800—900° С) плавленый магнезит, что позволяет почти полностью удалить из расплава относительно крупные окисные включения.
Опыты по применению магния в качестве раскислителя оло-вянистой бронзы (79% Си; 8,5% Zn; 9,5% Pb; 3,0% Sn) дали отрицательные результаты. Сплав содержал легкоплавкую составляющую из Mg и РЬ, вредно действующую на механические свойства.
По Хансену температура плавления Mg2Pb равна 550° С, а температура плавления эвтектик составляет примерно 475° С — Mg — Mg2Pb и около 250° С — Mg2Pb — Pb.
Ударная вязкость при наличии в структуре хотя бы незначительных количеств эвтектик не может быть удовлетворительной.
По другим данным раскисление магнием (добавка 0,05% Mg от веса плавки) латуней и литейных бессвинцовистых бронз значительно улучшает механические свойства (сплав раскисляется, газонасыщенность его уменьшается, улучшаются показатели о„ и 6).
Мюллер, изучая влияния присадок к меднооловянистым бронзам, сделал следующие выводы:
1) усадка бронз может быть уменьшена в результате присадки цинка;
2) присадки Со, Al, Fe, Ni увеличивают усадку;
3) присадки Со, Ni, Мп несколько увеличивают прочность бронзы;
4) присадки Sb и Zn понижают прочность оловянистой бронзы;
5) обрабатываемость резанием бронзы с присадками Sb, Pb улучшается, а с присадками Ni и Мп затрудняется.
Имеются данные Роаста о том, что в многосвинцовистых бронзах (например, 70% Си; 6% Sn; 3% Zn; 21% Pb) даже малейшие содержания А1 и Si делают бронзу совершенно непригодной к употреблению.
Для улучшения структуры слитка (измельчения зерна) и придания большей однородности и обрабатываемости давлением
Литейные сплавы оловянистых бронз
В зависимости от назначения отливаемых деталей и условий, в которых они работают, оловянистые бронзы можно разделить на несколько групп.
Установление оптимального состава бронз для литья предметов различного назначения началось в древние времена.
Для изготовления режущего и колющего оружия применяли бронзу с высоким содержанием олова (в большинстве случаев 13—15% Sn).
Для литья таких предметов, как кольца, браслеты, монеты, от которых требовалось высокое сопротивление изнашиванию от истирания, применяли бронзу с. 8—12% Sn. Кроме достаточно высокой твердости и вязкости, эти бронзы имеют красивый цвет: с 8% Sn — красновато-желтый; с 10% Sn — оранжево-желтый; с 14% Sn — желтый. Полированные бронзы этого состава по цвету и блеску напоминали золото.
Позднее при изготовлении бронзовых кованых полос для метательных машин («катапульт»), от которых требовалась особенно высокая упругость, Филон Византийский советовал применять бронзу с содержанием 3—4% Sn.
Необходимо отметить, что современная стандартная бронза Бр. ОЦ 4-3 для плоских и цилиндрических пружин содержит также 3—4% Sn. Другая бронза Бр. ОФ 4-0,25 применяется для изготовления пружинящих трубок для манометров.
С развитием культуры и техники своеобразная специализация бронз разного состава становилась все более и более определенной.
Пушечные бронзы
На первой стадии применения пушки изготовляли из чугуна и из кованого железа, на их стволы часто надевали для прочности кольца. Позднее, в XVI столетии, пушечные стволы стали отливать из бронзы. Со средины прошлого столетия пушечные стволы начали изготовлять из стали. От пушечной бронзы требовалась высокая твердость; хорошее сопротивление изнашиванию от истирания, достаточно высокая вязкость, чтобы ствол не разрывало при выстреле, максимально высокая плотность литья (отсутствие скрытых внутренних дефектов).
Кроме того, металл должен быть достаточно стойким против коррозии.
Опытным путем было установлено, что наиболее подходящим материалом для пушек может служить бронза, содержащая 89— 91 ч. Си и 11—9 ч. Sn. Иногда в нее вводили для повышения жидкотекучести до 2% Zn.
История пушечной бронзы с прекращением литья бронзовых пушек не кончилась. В текущем столетии сплавы того же или близкого к нему состава широко используют в машиностроении. За рубежом — это группа сплавов под названием гунметалла, в СССР —это бронзы: Бр. ОЦ10-2; Бр. ОЦ8-4; Бр. ОЦС6-6-3; Бр. ОЦС5-5-5; Бр. ОЦС6-6-3 и др.
Машинные бронзы
При изготовлении литых деталей машин бронза — весьма подходящий материал: она придает деталям изящный вид, сообщает им высокую коррозионную стойкость. Практическую ценность придают этим бронзам их высокие антифрикционные свойства, особенно в тех случаях, когда изготовленные из них детали работают на износ от истирания в паре со стальными частями. В подобных случаях из бронзы делают те детали, которые при износе сменять проще, скорее и выгоднее, чем работающие с ними в паре другие детали (тяжело нагруженные валы прокатных станов, двигателей и т. д.).
Чисто оловянистые бронзы в этой группе отсутствуют; в подавляющем большинстве эти бронзы, содержащие олова не более 10%, содержат цинк и свинец. Высокооловянистые бронзы, содержащие до 20% Sn, применяют только для изготовления деталей, работающих на истирание под о.чень большой нагрузкой: подпятники тяжелых кранов, разводных мостов, зеркала золотников паровых машин и т. п.
От машинной бронзы требуется хорошая обрабатываемость резанием, высокая плотность отливок — гидроплотность
Колокольная бронза
Небольшие колокола употребляли при религиозных обрядах еще в древнем Египте. Сравнительно большие колокола начали появляться в IV—VI столетиях новой эры. Первые колокола в Англии были отлиты в X столетии. Сохранился колокол с пометкой 1296 г. Есть колокола весом до 16—17 т.
Бронза для колоколов должна обладать достаточно высокой твердостью, чтобы давать хорошее звучание, при многочисленных ударах языка о края колокола бронза не должна давать заметных деформаций, не должна быть хрупкой, не должна выкрашиваться при ударах.
Содержание олова в этой бронзе выше, чем в пушечной. Примеси, или присадки других элементов, особенно таких, которые приводят к образованию новых обособленных фаз, бесполезны, а часто даже вредны. В XX столетии установлен такой состав колокольной бронзы: 20—23% Sn и 80—77% Си. Количество посторонних примесей (Pb, Fe, Ni и др.) зависит от чистоты исходных металлов, входящих в шихту (в старых колоколах больше примесей, чем в новых, содержание свинца в них доходит до 4%, а серебра до 1%).
Колокольную бронзу, как и пушечную, плавили в пламенных печах на дровяном топливе. Благодаря высокому содержанию олова его угар при плавке был очень велик. Для уменьшения безвозвратных потерь металла от окисления и улетучивания плавку вели с малым избытком воздуха. Для отливки больших колоколов строили особую печь. Незадолго до отливки печь нагревали в течение нескольких суток, пока она не приобретала нужную температуру. Для удаления дымовых газов в своде такой печи делалось отверстие. Распределение пламени в печи регулировалось шибером, помещенным в этом отверстии. Готовность печи к плавке определялась по ее накалу.
При загрузке шихты сначала загружали в печь старую бронзу вместе с необходимым количеством меди. С современной точки зрения это можно признать допустимым только в том случае, если в составе шихты находится очень мало чистой меди. Если свежая медь количественно превалирует над старым металлом (ломом), то сначала надо загрузить чистую медь, расплавить ее, раскислить образовавшуюся Сu2О фосфором.
Олово вводится только после полного расплавления основной шихты. Расплав хорошо перемешивают, и литейщик берет из печи небольшую пробу металла, после охлаждения ломает пробу и по виду излома судит о качестве сплава. Колокольная бронза указанного выше состава имеет в изломе желтовато-серый цвет и плотное мелкозернистое строение. При комнатной и при высоких температурах она хрупкая и даже упомянутая выше закалка мало уменьшает эту хрупкость. Несмотря на это, из слитков такой бронзы путем осторожной ковки под молотом изготовляют