Азотирование и карбонитрирование
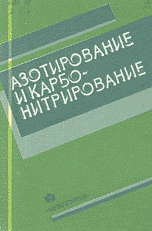
Чаттерджи-Фишер Р., Эйзелл Ф.-В.
Металлургия, 1990 г.
Азотирование проводится преимущественно в интервалетемператур 500 - 600 °С, а ионное азотирование - при температуре даже ниже 500 °С. Карбонитрирование проводится преимущественно при 570 - 580 "С, а иногда при температурах до 610 °С. Для процессаазотирования характерны следующие стадии:
Подвод азота из соответствующей среды к поверхности детали;
Образование пограничного слоя у поверхности детали, где на межфазной границесреда - металл происходит диссоциацияазот содержащей среды и адсорбцияповерхностьюатомов азота;
Проникновеннее (абсорбция) атомовазота через поверхность в материал детали;
Диффузия атомовазота в поверхностный слой детали по границам зерен и через зерна. Первые две стадии зависят от количества азота, достигшего поверхности детали и продиссоциировавшего там. В случае применения азотсодержащей среды в виде газообразного аммиака последний при каталитическом воздействии поверхности железа диссоциирует по реакции
3 NH3 » 3 Н2 + 2 N.
В расплавах солей атомыазота образуются в результате распада цианатов 2CNO- + 02 >> 2N + СО + СО2.
В процессекарбонитрирования в порошке азот выделяется из используемого в этом случае цианамида кальция, который в присутствии водяного пара, образующегося из добавляемого активатора, поставляет аммиак, в результате чего возникают условия, аналогичные газовому азотированию.
В течение ионных процессовазотирования и карбонитрирования выбитые из поверхности детали атомы железа взаимодействуют с ионами азота с образованием нитрида железа. Последний адсорбируется поверхностью детали и диссоциирует с выделениематомов азота.
При карбонитрировании к перечисленным реакциям добавляются реакциивыделения углерода, зависящие от типа использованной углеродсодержащей среды.
В процесседиффузии при науглероживании из-за постоянного изменения концентрацииуглерода в аустените возникает функциональная зависимость между поверхностнойконцентрациейуглерода и активностью углерода, меняющейся от нуля до предела насыщения. Последний определяется зависящей от температурырастворимостьюуглерода в аустените. При азотировании, напротив, вследствие образующихся уже через несколько минут нитридовазотныйпотенциал в материале изменяется скачкообразно. Учитывая, что дальнейшее поглощение азота посл.е возникновения соединенийжелезо - азот происходит не через твердый раствор, химический потенциал соответствует содержанию азота в имеющихся нитридах и имеет постоянную величину, на которую не оказывает влияния изменение содержания азота в среде, используемой для обработки. Отсюда вытекает, что процессазотирования не может быть описан с помощью концентрационных кривых потенциала и представлен в соответствии с правилами равновесия.
На практике процессазотирования регулируют с помощью материального баланса. В случае расплавов солей с этой целью перед началом обработки добиваются достаточно высокого содержания цианата. При газовом азотировании в среде аммиака, регулируя расход и давление в печи в зависимости от температуры, устанавливают соответствующую степень его диссоциации. Функциональной корреляции между содержаниями азота в насыщенной среде или в обрабатываемом материале и азотным потенциалом, используемым для управления процессом азотирования, экспериментально установить до сих пор не удалось, так же как еще не удалось достаточно полно выявить термодинамикупроцесса [7]. Вследствие этого определяющий уровень азота для управления процессамиазотирования или карбонитрирования пока не установлен. На практике при газовом азотировании и карбонитрировании используют величину так называемого потенциалаазотирования К, представляющего собой соотношение парциальных давлений непродиссоциировавшего аммиака и выделившегося в процессе его диссоциации в пространстве печи водорода (см. гл. 2).
Что касается диффузииазота в поверхностный слой материала на третьей стадии процессаазотирования (см. выше), то до настоящего времени имелось всего лишь несколько результатов исследований [8], вследствие чего невозможно привести достоверных количественных данных.
Упрочнение поверхностного слоя при азотированииприводит к повышению и циклической прочности сталей. Согласно данным [2Б], это обусловлено дисперсионным твердением диффузионного слоя (27]. В случае углеродистых сталей это объясняется выделением нестабильных а"-нитридов из пересыщенного азотом после быстрого охлаждения (закалки) до комнатной температуры феррита, а в случае легированных сталей - выделением мелкодисперсных нитридов легирующих элементов в диффузионном слое уже в процессеазотирования или карбонитрирования. Оба типа выделений за счет "внутреннего трения" препятствуют скольжению дислокаций, возникающих и перемещающихся в результате пластических знакопеременных деформаций при циклической нагрузке [28].
На образцах и деталях из стали, металлокерамики и чугуна было установлено, что повышение предела выносливости составляет примерно от 20 до 200 % [29]. Повышение усталостнойпрочности зависит от типа циклической нагрузки, формы и размеров детали, коэффициентаконцентрации напряжений к, природы материала детали и его исходного состояния, а также от условий карбонитрирования. В случае углеродистых сталей к этим факторам добавляет- ся влияние времени выдержки и скоростиохлаждения на состояниеазота в растворе и тем самым на дисперсионное твердение диффузионного слоя.
На рис. 32 показана зависимость предела выносливости при циклическом изгибе с кручением о_1 от прочности сердцевины для надрезанных («к = 2) и гладких образцов из углеродистой и легированной улучшенной стали в состоянии после карбонитрирования и закалки в воду, а также в некарбонитрированном улучшенном состоянии. В то время как в некарбонитрированном состоянии с ростом прочности сердцевины отмечается рост усталостнойпрочности кал надрезанных, так и гладких образцов, в случае карбонитрирования она повышается лишь для гладких образцов. Усталостнаяпрочность надрезанных образцов почти не зависит от прочности сердцевины. Это можно объяснить с помощью разработанной Кржиминским [26] и подтвержденной результатами последних исследований (например, в работе [30]) моделью изменения величины критического касательного напряжения в карбонитрированных деталях (рис. 33)-Согласно этой модели, разрушение гладких образцов начинается от имеющихся на поверхности зародышевых трещин, когда нагрузка превысит критическую [31]. В этом случае допустимую нагрузку можно увеличить путем повышения прочности сердцевины, вследствие чего повышается и прочность поверхности1.
В надрезанных образцах касательные напряжения как на поверхности, так и в подповерхностном слое могут превышать критические. В первом случае величину допускаемых нагрузок можно увеличить путем повышения твердостиповерхности посредством применения легированных сталей с высоким содержанием нитридообразующих элементов, во втором - путем повышения прочности сердцевины и (или) увеличения глубины азотирования. Если трещина зарождается в подповерхностном слое, то глубинуазотирования целесообразно увеличивать путем продления времени выдержки при карбонитрировании.
На рис. 34 показана зависимость предела выносливости при изгибе гладких и надрезанных образцов из углеродистой улучшаемой стали С45 от времени выдержки при жидкостном карбонитрировании. В случае гладких образцов Усталостнаяпрочность с увеличением выдержки (глубины азотирования) возрастает, а у надрезанных образцов, начиная с времени выдержки ~ 2 ч, она практически не изменяется. Согласно вышерассмотренной модели {см. рис. 33), большая глубинаазотированияприводит к повышению прочности лишь подповерхностного слоя. Очевидно, в случае надрезанных образцов трещина после 2-ч обработки все равно зарождается на поверхности; этого невозможно избежать даже при увеличении глубины азотирования. В случае гладких образцов по мере увеличения