Холодная прокатка стальных труб
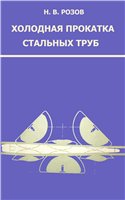
Н.В.Розов
Металлургия, 1977 г.
Холодная прокаткатруб в планетарных станах Планетарный стан имеет три опорных валка, расположенных под углом 120° друг к другу и вращающихся в направлении прокатки. На каждом опорном валке смонтировано по 12 прокатных рабочих роликов с короткими цапфами, которые имеют ручей цилиндрической формы. При вращении опорных валков ролики раскатывают трубу на цилиндрической оправке. Подача заготовки производится непрерывно, а поворот ее - в интервалах между обжатиями трубы. Основное преимущество этого способа заключается в применении стационарной рабочей клети и непрерывной подаче трубы, что позволяет значительно увеличить число оборотов опорных валков. При наличии большого количества роликов в каждом опорном валке производительность планетарного стана может быть в 2—4 раза выше, чем существующих валковых станов, несмотря на уменьшение подачи. К недостаткам стана необходимо отнести большую трудоемкость по смене рабочего инструмента. Стан предназначен для прокатки тонкостенных труб диаметром до 50 мм. Холодная прокатка труб в непрерывных станах Холодная прокатка труб происходит на длинной оправке в прокатных трехвалковых клетях — аналогично прокатке на непрерывном стане горячей прокатки. В связи с тем что деформацияметалла в холодном состоянии может быть значительно меньше, чем в горячем, число прокатных клетей увеличено с восьми до двадцати. Однако опыт показывает, что после про¬катки в таком стане труба получается граненой. Для устранения этого дефекта после прокатки в непрерывном стане осуществляют безоправочное волочение трубы. Помимо этого, при изготовлении тонкостенных труб усложняется операция снятия трубы с оправки. Настройка такого многоклетевого стана сложна, а смена рабочего инструмента еще более трудоемка, чем в планетарном стане. Поперечная холодная прокатка труб Этим способом изготовляют тонкостенные трубы (рис. 10) с соотношением толщины стенки к диаметру 1 : 200. Сущность поперечной холодной прокатки труб заключается в прокатке их профильными валками, расположенными под углом 120° друг к другу, на вращающейся цилиндрической или конической оправке с постепенной принудительной подачей заготовки в валки. Помимо продольного перемещения, заготовка получает также вращательное движение, которое сообщается ей или оправке, или валкам.
Основные виды термической обработки стали
В зависимости от состава стали и назначения труб применяется различная термическая обработка. Термической обработкой называют процессы, связанные с нагревом и охлаждением, вызывающим изменения внутреннего строения сплава, и в связи с этим изменения физических, механических и других свойств. Для труб предусмотрены следующие виды термической обработки: отжиг, нормализация, закалка, отпуск, а также двойная термическая обработка — закалка или нормализация с последующим отпуском. Термическая обработка стали производится для: а) устранения или уменьшения напряжений, полученных в процессе обработки металла давлением; б) устранения наклепа, полученного в процессе холодной обработки давлением; в) создания однородной структуры стали, которая обеспечивает более высокий уровень механических свойств и лучшую обрабатываемость; г) выравнивания химического состава; д) исправления крупнозернистой структуры, которая вызывает общее уменьшение вязкости, в частности резкое падение ударной вязкости, и перевода ее в мелкозернистую; е) увеличения твердости и прочности стали при закалке; ж) получения определенной заданной структуры (котельные трубы, подшипниковые и др.).
При термической обработке стали необходимо строго следить за температурой. При недостаточном нагреве превращения могут пройти неполностью. При нагреве, значительно превышающем заданную температуру, можно получить перегрев. При этом сталь приобретает крупнозернистую структуру и пониженные механические свойства. При нагреве до температуры, близкой к температуре начала плавления, по границам зерен стали появляются окислы железа, которые делают сталь очень хрупкой. В этом случае говорят, что сталь получила пережог. Пережог является неисправимым браком. Термическая обработка состоит из следующих этапов: 1) нагрева до заданной температуры; 2) выдержки При заданной температуре для выравнивания температуры по всему объему изделия; з) охлаждения с различной для каждого вида термической обработки скоростью. Основное различие между отдельными видами термической обработки определяется температурой нагрева и скоростью охлаждения. Различают предварительную, промежуточную и окончательную термическую обработку труб. Предварительной термической обработке подвергают трубную заготовку из некоторых легированных и высоколегированных сталей для придания ей пластичности. Промежуточной термической обработке независимо от марки стали подвергают трубы после холодной прокатки для снятия свойств металла, приобретенных в результате наклепа. Окончательную термическую обработку труб для придания им необходимых механических свойств проводят после последней операции прокатки перед сдачей труб заказчику. Основные виды термической обработки стали следующие. Отжиг — нагрев металла выше критической точки Л3 (линия GS на рис. 24) на 30—50°С в интервале температур превращений, выдержка при этой температуре с последующим медленным охлаждением по определенному режиму. В результате отжига снижается твердость металла, повышается вязкость, снимаются внутренние напряжения и устраняется структурная неоднородность. Нагрев до температуры на 30—60°С выше критической приводит к образованию в стали структуры аустенита. При последующем охлаждении происходит структурное превращение аусте_ шита в перлит и феррит или перлит. Нормализация — нагрев стали до температуры выше А3 на 30—50°С, выдержка при этой температуре и последующее охлаждение на воздухе. Нормализацией достигается улучшение микроструктуры стали, уменьшение внутренних напряжений и повышение механических свойств стали. Закалка — нагрев стали до температуры в интервале превращений или чаще выше его (на рис. 24 заштрихован), выдержка при этой температуре и последующее быстрое охлаждение в воде, масле или другой среде. Отпуск — нагрев металла в закаленном состоянии до температуры ниже интервала превращений (ниже линий GS), выдержка при этой температуре и охлаждение. Отпуском достигается повышение вязкости стали при сохранении прочности и упругости, а также уменьшение внутренних напряжений и снятие наклепа. Нагрев углеродистой стали при отпуске до 350—400°С и последующее охлаждение позволяют получить в структуре высокодисперсную смесь карбидных частиц (образующихся при распаде мартенсита) и феррита. Получающаяся структура называется трооститом. При более высокой температуре отпуска 500—550°С цементитные частицы при распаде мартенсита получаются крупнее. Поэтому образующаяся смесь феррита и цементита, которая называется сорбитом, менее дисперсна, чем троостит. При температуре отпуска выше 550°С частицы смеси феррита и цементита укрупняются и при 600—650°С сталь имеет структуру перлита. Указанные выше температуры приведены для углеродистых сталей. Легирующие элементы значительно влияют на физические, химические и механические свойства стали. Введение легирующих элементов (хром, никель, марганец и др.) в сталь изменяет положение критических точек. В связи с этим меняются и режимы термической обработки легированных сталей. В случае понижения критических точек температуры нагрева стали при отжиге, закалке и других термических операциях должны быть ниже. Некоторые элементы (например, хром), наоборот, повышают критические точки. Введение того или иного элемента меняет чувствительность к перегреву (хром, марганец), уменьшает или увеличивает рост зерна и т. д. Таким образом, влияние легирующих элементов на структуру стали при термической обработке различно. Поэтому надо строго придерживаться того режима термической обработки, который назначается для каждой стали. При термической обработке требуется равномерный нагрев труб по длине и сечению точно до заданной температуры. Время пребывания труб в печи определяется графиками термической обработки, которые разрабатываются на основе исследований и результатов практической работы. Ими необходимо руководствоваться при работе в цехе. Разогрев кромок свариваемой трубной заготовки производят до сварочной температуры с оплавлением металла в точке схождения кромок 5. После нагрева кромки сдавливаются обжимными валками 4 и происходит сварка кромок с образованием трубы. Процесс контактной электросварки труб сопротивлением заключается в подаче сварочного тока к кромкам трубной заготовки, разогреве кромок в месте их соприкосновения до сварочной температуры и в сдавливании трубной заготовки, вследствие чего осуществляется сварка кромок. Сварочный ток подводится от вторичной обмотки вращающегося сварочного трансформатора (рис. 19) через электродные кольца /, разделенные изолятором 2. В месте схождения кромок электрическое сопротивление наибольшее, поэтому в этом месте происходят интенсивное выделение тепла и разогрев стыка до сварочной температуры. 'В сварочном трансформаторе ток, подводимый к первичной обмотке, преобразуется в ток большой силы, но меньшего напряжения. Величина трансформации тока выражается коэффициентом к, который может быть равным 40 и более. Например, ток первичной обмотки трансформатора с напряжением 60— 200В может трансформироваться в сварочный ток напряжением 1,5—5,0 В и силой 38000 А. Сдавливание разогретых кромок производится сжимающими валками 5. С трубоформовочного стана заготовка 6 поступает в стан для сварки труб сопротивлением в формовочные валки 3, в которых имеется .направляющая шайба 4, обеспечивающая поступление заготовки в сварочные валки вверх стыком. После сварки труба 7 правится на правильной головке, входящей в состав трубоэлектросварочного агрегата. Сварку труб в среде инертных газов применяют для изготовления труб из высоколегированных сталей и сплавов, в первую очередь для нержавеющих труб, используемых в химической промышленности. В нашей стране этим способом изготовляют трубы наружным диаметром 6—102 мм.