Жаропрочные стали
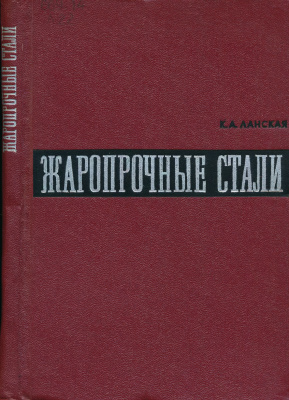
Ланская К.А.
Металлургия, 1969 г.
Для повышения свойств металлов в течение ряда последних лет в практике отечественной и зарубежной металлургии все чаще стали применять малые добавки бора, щелочноземельных и редкоземельных элементов (РЗМ).
Редкоземельные элементы делятся на цериевую (лантан, церий, празеодим, неодим, прометий, самарий, европий, гадолиний) и иттриевую (иттербий, диспрозий, гольмий, эрбий, тулий, скандий и иттрий) подгруппы.
Физической основой деления редкоземельных элементов на указанные группы является принцип максимальной мультиплетности заполнения 4f оболочки, у первых семи электронов от церия до гадолиния спины электронов параллельны между собой, а у последующих элементов от тербия до лютеция идет заполнение Af оболочки электронами с антипараллельными спинами [141].
В металлургии, при производстве стали, редкоземельные элементы вводят в металл в виде мишметалла, ферроцерия и других сплавов, в состав которых входят элементы цериевой группы, ферросплавов, специально приготовленных лигатур или чистых металлов.
Большое значение имеет применение малых добавок бора и редкоземельных элементов к жаропрочным металлам и сплавам, в частности к сталям, предназначенным для длительных сроков службы, так как для этих сталей и сплавов состояние границ зерен приобретает особо важное значение.
Из литературы известно, что малые добавки редкоземельных элементов улучшают деформируемость в горячем состоянии нержавеющих и жаропрочных сталей и сплавов, повышают их длительную прочность и сопротивление ползучести, увеличивают продолжительность службы сплавов омического сопротивления [48, 50, 142—146].
В этих же направлениях благоприятно влияют щелочноземельные элементы кальций и барий, а также бор.
Принято считать, что механизм влияния малых добавок бора и редкоземельных элементов проявляется в следующем:
1) в раскисляющем и рафинирующем действии благодаря их большому сродству к кислороду, азоту и водороду;
2) в десульфурации — очищении металла от серы;
3) в модифицировании сталей и сплавов (измельчении структуры);
4) в способности образовывать с вредными примесями (свинцом, висмутом, оловом и др.) тугоплавкие химические соединения;
5) в легировании сталей и сплавов, способствуя их упрочнению, повышению температуры рекристаллизации или изменению других свойств. Установлено [147, 148], что растворение малых добавок (например, бора в граничных зонах) дополнительно упрочняет границы зерен и замедляет диффузионные процессы в этих участках.
Несмотря на большое количество работ, освещающих влияние малых добавок и особенно РЗМ на разнообразные свойства сталей
и сплавов, до настоящего времени не выявлена в полной мере физикохимическая сущность процесса их влияния. Одной из основных причин этого явилось то обстоятельство, что ранее не определяли влияние остаточного содержания в стали малых добавок из-за отсутствия методик их определения химическим или каким-либо другим методом.
В то же время для использования в практике малых добавок одним из основных моментов является установление оптимальной добавки. В свою очередь содержания оптимальных добавок остаются справедливыми при строгом соблюдении технологии ведения плавки (определенном порядке раскисления металла, способе введения добавок, времени выдержки с момента введения добавок, температуре жидкого металла, а также составе шлака и т. д.).
Учитывая изложенное автор, совместно с Э. Н. Горчаковой [149, с. 333, 150] попытались уточнить механизм влияния малых добавок, разделив их действие, как раскислителей, как легирующих элементов, исключив их влияние, как модификаторов, десульфураторов и элементов, способствующих образованию тугоплавких соединений с вредными примесями. Результаты этих исследований приведены ниже.
Влияние малых добавок на свойства проверяли из хромомолибденованадиевой стали 12Х1МФ и хромоникельниобиевой стали ЭИ694, выплавку которых осуществляли в 10- и 30-кг высокочастотных печах. При этом подбор шихтовых материалов проводили так, чтобы они содержали минимальное, практически не влияющее количество цветных металлов и, кроме того, минимальное количество серы. Такой подбор шихтовых материалов давал возможность исключить влияние малых добавок как модификаторов, десульфураторов и элементов, способствующих образованию тугоплавких соединений с вредными примесями. Обязательным условием при выплавке было введение всех добавок в хорошо раскисленную сталь и осуществление выплавки в одинаковых условиях. Стали раскисляли кремнием, марганцем и никельмагниевой лигатурой. Все добавки вводили в печь под шлак за 2—3 мин до выпуска металла из печи. Расчетные количества малых добавок, вводимых в сталь, были следующие, % (вес.):
В Ca Ba Zr Ce La Nd
0,005 0,05 0,05 0,03 0,01 0,01 0,01
0,1 0,5 0,5 1,0 0,5 0,5 0,5
Церий вводили в виде мишметалла или ферроцерия; бор — в виде ферробора; цирконий — в виде 33- или 46%-ного силикоциркония; кальций — в виде силикокальция; барий — в виде алюминиебариевой лигатуры и металлического бария; лантан металлический вводили только в аустенитную сталь ЭИ694; неодим — в виде металла.
Мишметалл, как известно, представляет собой смесь элементов цериевой подгруппы и содержит 40—60% Ce, 22—30% La, 15— 18% Nd, 8—10% других РЗМ. Чистота металлического церия, лантана и неодима составляет 98—99%, остальное железо, а также другие РЗМ. Ферроцерий содержит 90-96% Ce, остальное железо.
Для успешного выполнения поставленных задач химиками и спектралыциками были разработаны новые точные методы определения малых добавок: химический, спектральный и спектрохимический [151, 152].
В табл. 22, 23 приведены расчетное и фактическое содержание малых добавок, полученных при выплавке перлитной стали 12Х1МФ и аустенитной стали 1Х14Н16Б (ЭИ694).
Из данных таблицы вытекает следующее:
1) при введении в сталь из расчета до 0,06% бора бор в большей степени усваивается в аустенитной, чем в перлитной стали. С увеличением расчетного количества бора более 0,06% усвояемость его уменьшается. При введении в сталь бора в количестве 0,5% бор практически усваивается полностью;
2) фактическое содержание кальция в металле независимо от расчетной добавки примерно одинаковое в обеих сталях и не превышает 0,03%;
3) барий независимо от того, в каком виде его вводили в сталь (в виде алюминиебариевой лигатуры или металлического бария), не обнаруживается в металле;
4) цирконий в обеих сталях усваивается практически полностью, за исключением максимальной добавки. В последнем случае усвояемость соответствует 80%.
Определение фактического содержания циркония и лантана показывает, что церий в больших количествах усваивается аустенитной сталью, чем перлитной. В стали 12Х1МФ содержание лантана составляет приблизительно 40% от фактического содержания церия. Лантан в небольших количествах больше усваивается перлитной сталью. В аустенитной стали в небольших количествах он не обнаруживается.
Для того чтобы уточнить влияние только лантана, в сталь 1Х14Н16Б (ЭИ694) был введен металлический лантан из расчета 0,1 и 0,5%. При введении металлического лантана из расчета 0,1% он усваивается в меньшем количестве, чем при введении мишметалла, исходя из расчета церия тоже на 0,1%.
При расчетной добавке лантана 0,5% его усвояемость соответствует 50%.
Неодим усваивается примерно одинаково как перлитной, так и аустенитной сталью. До 0,1% усваивается примерно 70—90%, а при введении расчетной добавки 0,5% усваивается 25% неодима, т. е. в два раза меньше, чем металлического лантана.
Установив остаточное содержание малых добавок в металле, легче оценить их влияние:
во-первых, как элементов раскислителей. При этом для оценки раскисляющей способности воспользовались двумя основными критериями:
а) влиянием малых добавок на содержание газов;
б) влиянием малых добавок на содержание неметаллических включений;
во-вторых, как элементов, легирующих сталь и тем самым оказывающих влияние на критические точки, величину зерна, механические, жаропрочные и другие свойства. В этом случае интересно установить, влияют ли малые добавки на твердый раствор или образуют самостоятельные фазы.
ВЛИЯНИЕ МИКРОЛЕГИРОВАНИЯ НА ГАЗОНАСЫЩЕННОСТЬ И НЕМЕТАЛЛИЧЕСКИЕ ВКЛЮЧЕНИЯ
Стали и сплавы, как правило, содержат некоторое количество нежелательных примесей, попадающих в них из шихтовых и огнеупорных материалов или образующихся в процессе выплавки — главным образом раскисления, а также получившихся от взаимодействия жидкого металла с атмосферой. Эти примеси в значительной мере способствуют снижению пластичности при высоких температурах — увеличению хрупкости и преждевременному разрушению стали. К наиболее нежелательным примесям относятся кислород и кислородные включения, а также сера и сернистые включения. Азот является нежелательной примесью в том случае, когда он находится в стали в виде крупных скоплений нитридов или карбо- нитридов. Азот, растворенный в аустенитных хромоникелевых сталях, играет положительную роль, способствует частичной замене никеля. Растворимость кислорода и серы в стали мала вследствие их большого сродства к металлическим составляющим стали и сплавов — они образуют преимущественно неметаллические включения. Водород, присутствующий в стали, чаще всего находится в твердом растворе. С. М. Баранов [153] считает, что водород относится к числу поверхностно активных примесей. Повышенное содержание его в жидком металле изменяет первичную кристаллизацию, приводит к усилению дентритной ликвации и возникновению видманштетто- вой структуры. Влияние водорода на развитие хрупкости металлов отмечалось многими исследователями.
Газы в сталях и сплавах могут также находиться в виде пузырей.
Уменьшение содержания газов и неметаллических включений, способствующее повышению качества сталей и сплавов, — одна из основных задач металлургов. Исследование условий образования и распределения включений в металле, влияния на свойства проводится металлургами в течение многих лет, и в этой области имеются уже большие успехи [154—156 и др.].
Использование в настоящее время в металлургии вакуумной выплавки, вакуумирования стали при разливке, электрошлакового переплава, обработки синтетическими шлаками позволило обеспечить в металле минимальное количество неметаллических включений и газов. Ho не меньший интерес представляет повышение чистоты металла при введении в него РЗМ и других элементов.
Из сравнения теплот образования различных соединений бора, бария, кальция и РЗМ, которые являются показателями, определяющими ход реакций (табл. 24), видно, что при взаимодействии РЗМ
с расплавами сталей в первую очередь образуются окислы, а затем сульфиды. Характерным для соединений РЗМ — окислов и сульфидов — является высокая тугоплавкость. Большинство окислов РЗМ имеет температуру плавления 2200—2300° С, а сульфидов 2000— 2200° С. Учитывая такую способность РМЗ, можно считать, что окислы и сульфиды РЗМ находятся в твердом состоянии и могут являться центрами кристаллизации.
Теплоты образования соединений РЗМ с цветными металлами (Sn, Pb, Bi и др.) не известны, но, судя по температурам плавления этих соединений, можно считать, что связывание легкоплавких примесей в тугоплавкие соединения (например, CeSn2, tпл - 1400° С; La2Pb, tплl - 1315° С; Ce4Bi, tпл -1630° С) происходит при температурах выпуска и в первоначальный момент кристаллизации стали. Благодаря разности удельных весов жидкой стали и образовавшихся соединений РЗМ и пониженной растворимости РЗМ в жидкой стали соединения могут частично всплывать и, таким образом, сталь очищается от газов и вредных примесей. Однако сравнительно малая разница между удельными весами окислов РЗМ, сульфидов РЗМ и жидкой стали — существенный недостаток окислов и сульфидов РЗМ по сравнению с окислами других раскислителей (например, удельный вес окислов титана равен 4,26 г/см3, окислов лантана 6,7 г/см3) — это не может обеспечить быстрого всплывания неметаллических включений на поверхность ванны. Поэтому для наиболее полного удаления окислов РЗМ необходима определенная выдержка с момента введения РЗМ до начала затвердевания.