Жаропрочность сварных соединений
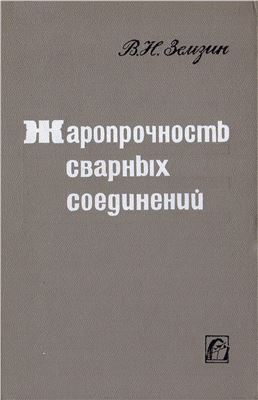
Земзин В.Н.
Машиностроение, 1972 г.
Жаропрочность сплава зависит и от его аллотропической модификации. Известно, что сплав с гранецентрированной кубической решеткой обладает более высокой температурой рекристаллизации, чем близкий по составу сплав, но с объемноцентрированной кубической решеткой. Это связано с большей плотностью гранецентрированной решетки и меньшем диффузионной подвижностью легирующих элементов и основы сплава. Поэтому аустенитные стали и сплавы па никелевой основе могут применяться как жаропрочные материалы при температурах на 100—200°С выше по сравнению с ферритными сталями.
По уровню прочности стали и сплавы, используемые при высоких температурах, могут быть в первом приближении разделены на следующие 5 групп. Ниже 300 – 350°С наибольшую прочность имеют простые конструкционные стали, обработанные на высокую прочность. Для работы при этих температурах, например барабанов котлов, нет необходимости в применении специальных теплоустойчивых сталей. Для работы в интервале 350—550° С оптимальными являются сравнительно слаболегированные теплоустойчивые стали перлитного и бейнитного классов. Для температур 500 - 600° С целесообразно использовать высокохромистые жаропрочные стали мартенситного класса на базе 12% хрома; при температурах 550—700°С — аустенитные жаропрочные стали, а при 650—900° С — сплавы на никелевой и кобальтовой основах.
При низких рабочих напряжениях максимальные рабочие температуры могут быть повышены. Так, например, в камерах сгорания газовых турбин аустенитная сталь Х18Н10Т применяется до температур 750—850°С, а сталь Х23Н18 — при температурах до 1100° С. Условием, определяющим выбор материала, является в данном случае уже не жаропрочность, а жаростойкость, т. е. способность материала сопротивляться окислении) при высоких температурах.
Упрочнение за счет легирования твердого раствора заметно ослабевает при нагреве выше 0,5—0,6 Тпл. Оно не позволяет также заметно повысить уровень жаропрочности сплава. В связи с этим стали и сплавы повышенной жаропрочности в основном являются в большей или меньшей степени пересыщенными твердыми растворами, способными к дополнительному упрочнению за счет дисперсионного твердения. Этот вид упрочнения может оказывать действие до 0,6 - 0,7 Тпл.
Степень упрочнения зависит от размера выделившихся фаз и их стабильности при высоких температурах. Чем сложнее состав и строение выделяющихся фаз и чем они больше отличаются от состава и строения исходного раствора, тем медленнее, как правило, протекают диффузионные процессы их образования и тем большее значение они имеют для повышения прочности металла . Особый интерес представляют собой фазы, в решетку которых в определенном соотношении входят несколько компонентов или вовсе не входит один из основных компонентов. Упрочняющая фаза должна быть возможно более тугоплавкой и ее собственная жаропрочность должна быть возможно выше.
Блокирование скольжения частицами вторых фаз действует значительно сильнее, чем блокирование растворенными атомами. Чем больше субмикронеоднородность и чем равномернее фаза распределена в объеме металла, тем полнее используются силы гни ни в кристаллической решетке и тем большие напряжения необходимы для их преодоления дислокациями. Фрагментация (дробление зерен и блоков, увеличение их разориентировки) основного твердого раствора, возникающая в результате легирования, термической обработки и пластической деформации, также способствует получению тонкой субмикроскопической структуры и более полному использованию межатомных связей.
В зависимости от условий работы при высоких температурах и прежде всего от длительности эксплуатации меняются принципы рационального упрочнения сплава за счет эффекта дисперсионного твердения. Для кратковременной работы желательно иметь в сплаве высокодисперсное, распределение второй фазы, получаемое обычной термической обработкой — закалкой с последующим отпуском при температуре, близкой к рабочей. При том сознательно идут на высокое содержание упрочняющей фазы г целью получения максимальной жаропрочности. Определяющим фактором выбора количества второй фазы является стабильность ее высокодисперсного состояния при требуемом сроке эксплуатации.
В условиях длительной работы жаропрочных материалов высокое содержание второй фазы неизбежно вызовет ее коагуляцию и уменьшение прочности сплава. Кроме того, резко снижается длительная пластичность за счет интенсивного развития межзеренного разрушения. Исходя из этого для сплавов, предназначенных к длительной работе, принимают обычно материалы с меньшим количеством избыточной фазы. При использовании для этой пели материалов, предназначенных для краткосрочной службы, удается повысить их длительную прочность и пластичность при переходе к ступенчатой термической обработке 1501, отличающейся и обычной введением после закалки промежуточных режимов парения при температурах на 100—200° С выше рабочей в целях прохождения процессов коагуляции избыточной второй фазы. Применение этого вида старения позволило использовать для длительной работы в энергетических стационарных установках ряд сплавов на никелевой основе, разработанных для авиационных газовых турбин кратковременного действия. Эта операция явилась полезной и для стареющих алюминиевых сплавов в случае их применения при высоких температурах.
Мели вторая фаза не обладает растворимостью в основном металле, то очевидно, что при ее введении мы не получим эффекта дисперсионного упрочнения. Наоборот, при низкой температуре плавления этой фазы и появлении эвтектик, образуемых ею с основой сплава, наблюдается обычно резкое снижение уровня жаропрочности, сопровождаемое повышенной хрупкостью. С указанным явлением необходимо считаться при оценке влияния таких примесей, как S, Р, Sn,-Pb, Sb и других, образующих легкоплавкие эвтектики по границам зерен. Их вредное влияние повышается обычно с переходом к более жаропрочным сплавам. В условиях сварки оно, как правило, усиливается и приводит к межзеренному растрескиванию в околошовной зоне. В связи с этим одним из требовании, предъявляемых к выбору высокожаропрочных сталей и сплавов для сварных конструкций (например, сплавов па никелевой основе), является введение при их выплавке технологии очищения границ от легкоплавких фаз.
Для теплоустойчивых и жаропрочных сталей перлитного, бейнитного, мартенситного и аустенитного классов, а также для сплавов на никелевой основе в настоящее время находят основное применение карбидное и иптерметаллидпое упрочнения. При реализации эффекта карбидного упрочнения основными легирующими элементами являются в сталях с решеткой а — Fe хром, молибден, ванадий и иногда ниобий; в аустенитных сталях — хром, молибден, титан и ниобий. Эффект карбидного упрочнения определяется стойкостью карбидов и наибольший при использовании карбидов типов TiC, NbC и VC, в состав которых не входит основной элемент — железо. За счет карбидного упрочнения может быть сохранена удовлетворительная длительная жаропрочность сталей с решеткой α —Fe до 550.....570 С, а аустенитных сталей до 650° С. В сплавах на никелевой основе карбидное упрочнение не используется ввиду его нестабильности при температурах выше 650 С
В сплавах па никелевой основе и аустенитных сталях повышенной жаропрочности основное использование находит иптерметаллидпое упрочнение фазами типа NitMe (γ' и β) переменного состава, близкого к составам Ni;, (Ti, Al), Ni;iTi и NijAl. Эти фазы имеют однотипную с твердым раствором граиецентрированную кубическую решетку типа Сп3А1 с упорядоченным расположением атомов, но с несколько отличными от твердого раствора параметрами. Это упрочнение является более стабильным по сравнению с карбидным, что позволяет использовать сплавы на никелевой основе для кратковременной работы до 850 950 С, а для длительной — до 800—850°С. Для аустенитных сталей этот тип упрочнения можно применять до температур 700 750' С. Наиболее эффективным является введение в эти сплавы одновременно с Ti и А1 также Мо и W, как элементов, замедляющих интенсивность диффузионных процессов и тем усиливающих упрочняющее действие дисперсных фаз.
Структурные превращения при высоких температурах в зависимости от легирования сплава и его исходного структурного состояния могут иметь разный механизм и приводить к разным последствиям. В большинстве своем они могут быть отнесены к диффузионным процессам, интенсивность которых с повышением температуры меняется по экспоненциальному закону, а времени — но закону квадратичной параболы. В перлитных и аустенитных сталях при длительном температурном воздействии наблюдаются следующие структурные превращения:
1) сфероидизация перлита и коагуляция частиц карбидной фазы;
2) графитизация — для перлитных сталей, не содержащих хрома;
3) образование новых и перерождение старых фаз — химических соединений (σ-фазы и других);
4) перераспределение легирующих элементов между твердым раствором и карбидной фазой.
Детальное рассмотрение процессов, определяющих структурную нестабильность, приведено в главах, посвященных соответствующим классам сталей и сплавов.