Высокопрочные стали
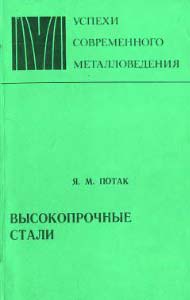
Потак Я.М.
Металлургия, 1972 г.
СТРУКТУРА И СВОЙСТВА СТАЛИ Н18К9М5Т (ВКС-210, МС-200, ЭП637)
Высокопрочная сталь Н18К9М5Т с пределом прочности после старения σΒ= 1,95 — 2,2 Гн/м2 (195— 220 кГ/мм2) находит наиболее широкое применение. Сталь содержит <ι0,03% С, около 18% Ni, 9% Со, 5%' Мо, 0,7% Ti. В ряде стран применяют аналогичные стали, а также стали с несколько меньшим содержанием кобальта, молибдена и титана и соответственно меньшей прочностью. Содержание кремния и марганца в сталях ограничено (0,1%), а содержание серы и фосфора не более 0,010% каждого элемента. Во всех странах сталь типа Н18К9М5Т выплавляют или переплавляют в вакуумных печах.
Мартенситное превращение стали Н18К9М5Т после закалки с 820°С начинается при 150—160°С и заканчивается при 40—30°С. Исследования С. С. Рыжак показали, что тепловой стабилизации при закалке во время изотермических выдержек аустенита выше Ми и в области температур Ми—Мк сталь ,не подвержена; мартенситное превращение протекает при этом полностью [27, с. 3}.
Очень небольшое количество (10—12%) аустенита можно застабилизировать путем закалки в интервале Мн—Мк и немедленного (без охлаждения до комнатной температуры) переноса в печь при 400—500°С Указанное количество остаточного аустенита (стабильного при комнатной температуре) на механические свойства стали почти не влияет. Интересно отметить, что при изменении в широких пределах содержания аустенита в закаленной высоконикелевой мартенситно-стареющей стали, осуществленном путем повышения содержания легирующих элементов, твердость ее без старения почти не менялась.
Упрочнение при старении стали Н18К9М5Т происходит без инкубационного периода с большой скоростью. Даже 15-сек нагрева при старении достаточно для скачкообразного изменения всех свойств: твердость резко возрастает при падении коэрцитивной силы и электросопротивления.
(Пластическая деформация после закалки перед старением вызывает некоторый прирост твердости после старения, однако он равен упрочнению матрицы до старения. Упрочнение в результате пластической деформации сохраняется после старения до 500°С, старение при более высокой температуре способствует нивелированию эффекта дополнительного упрочнения матрицы.
Μ. Е. Блантер и Л. А. Ковалева [106} отмечают, что предварительная пластическая деформация стали типа НШК8М6Т или В18К8М6Ю вызывает ускорение старения, что объясняется повышенной энергией кристаллической решетки в деформированном состоянии. Величина прироста прочности в результате старения при 4750[С у деформированной стали, по данным этих исследователей, получилась несколько ниже, чем у недеформированной, и поэтому предел прочности после оптимального старения предварительно деформированных и недеформированных сталей оказался почти одинаковым.
При длительных выдержках при 500—525°С начинается разупрочнение стали, не сопровождающееся, однако, увеличением электросопротивления. Это свидетельствует отом, Что начало разупрочнения не является результатом растворения упрочняющих фаз.
Изменение механических и физических свойств при старении стали Н18К9М5Т показано на рис. 36. Лучшее сочетание прочности и ударной вязкости достигается после низкотемпературного старения, однако это находится в противоречии с требованием получения максимальной коррозионной стойкости. Фазовый состав сталей Н18К8М5 и Н18К8М5Т после закалки с 820°С и перестаривания был изучен в работе [9, с. 26].. Установлено, что в обеих сталях после старения при 540—640°С происходит выделение высокодисперсной упрочняющей фазы (FeNiCo*Mo; в стали Н18К9М5Т после отпуска при 600—640°<С (более низкие температуры отпуска не исследовали) образуется также фаза Ni3Tiс гексагональной решеткой.
Обратное превращение в стали Н18К9М5Т начинается при нагреве ее на 500°С с выдержкой 1—3 ч и заканчивается при 720°С
Изучение структуры стали Н18К9М5Т после нагрева в начальной области обратного превращения показало, что образование аустенита происходит в виде прослоек толщиной 0,05—0,1 мкм по границам зерен и кристаллов мартенсита. При повышении температуры нагрева и увеличении времени выдержки аустенита становится больше при росте толщины прослоек. При содержании аустенита до 30%' и более он выделяется в виде видманштеттовой структуры.
После нагрева стали в нижнетемпературной части двухфазной зоны α+γ при 500—680°С образуется аустенит, обладающий высокой стабильностью при комнатной и криогенных температурах. Стабильность такого аустенита объясняется тем, что он значительно обогащен никелем, содержание которого доходит до 25—35%, и обеднен кобальтом (3,4—4,0%) по сравнению со средним содержанием этих элементов в стали [9, с. 26]. В результате высокого содержания никеля стабильный аустенит, образовавшийся в начальной стадии обратного превращения, ферромагнитен. При повышении температуры нагрева в области α+γ содержание никеля в аустените и точка Кюри снижаются.
При нагреве под закалку во время прохождения двухфазной области α+γ образуется аустенит различного химического состава по никелю и кобальту: в низкотемпературном районе области а+у более богатый никелем и более бедный кобальтом, а в высокотемпературном районе области α + γ — наоборот, более бедный никелем и богатый кобальтом.
Для выравнивания состава аустенита, достаточного для того, чтобы температура конца мартенситного превращения была выше комнатной и чтобы образовалась полностью мартенситная структура, необходимо при закалке нагревать сталь не менее, чем до800°С и выдерживать ее 30мин.
При более низкой температуре закалки или недостаточной выдержке в стали может сохраняться до 20— 30% остаточного аустенита. При этом температура начала мартенситного превращения будет более высокой, гак как в структуре стали после недостаточной гомогенизации наряду с аустенитом, более легированным никелем, сохранится менее легированный никелем аустенит.