Высокочастотная термическая обработка
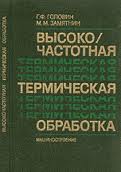
Головин Г.Ф., Замятнин М.М.
Машиностроение, 1990 г.
2.2. ЗАКАЛКА ИЗДЕЛИЙ ИЗ ЧУГУНА
Структурные превращения в металлической основе серого или ковкого чугуна при нагреве имеют те же закономерности, что и в стали. Следовательно, при применении быстрого индукционного нагрева имеют место процессы, описанные в гл. 2. Однако в структуре чугуна находится свободный графит, который при нагреве может служить источником углерода, что вносит некоторые особенности в закалку.
ЗАКАЛКА ПЕРЛИТНОГО И ПЕРЛИТНО-ФЕРРИТНОГО ЧУГУНА.
Для закалки чугуна с перлитной структурой металлической основы при нагреве необходимо обеспечить превращение перлита в аустенит. В сером чугуне из-за наличия в составе металлической основы до 2—2,5%Siинтервал критических температур перемещается в область более высоких температур, причем и в равновесных условиях нагрева превращение перлита в аустенит происходит не при постоянной температуре, а в интервале температур (в зависимости от состава чугуна). На тройной диаграмме состояний сплавов железо—цементит—кремний критический интервал температуры превращения перлита в аустенит при 2—3% Siсоставляет 800— 850 °С. Следовательно, температура закалки серого перлитного чугуна должна быть выше 850 °С. Если учесть влияние скорости нагрева, принимая во внимание общие закономерности фазовых превращений при быстром нагреве, то при поверхностной индукционной закалке может быть принята температура нагрева, равная 850—900 °С.
Мартенсит, полученный после закалки металлической основы, имеет безыгольчатое строение. При быстрых нагревах возможно сохранение рисунка перлита. Переходная зона очень небольшая, что связано с узким интервалом перлитного превращения. Распределение микротвердости металлической основы по глубине закаленного чугунного изделия подтверждает это положение: высокая твердость на границе мартенситного слоя резко падает до исходной.
Образование игольчатого мартенсита, вызванное чрезмерно высокой температурой нагрева, обычно сопровождается появлением участков аустенита, сосредоточенных по границам графитовых включений. При нагреве до высоких температур графит частично растворяется в аустените, насыщая его до концентрации, превышающей концентрацию углерода в эвтектоиде, что способствует сохранению остаточного аустенита. Поэтому в структуре желательно иметь некоторое количество феррита, сосредоточенного, как это обычно и наблюдается, по границам графитовых включений. В исходной структуре перлитного чугуна практически можно допустить 5—10% феррита. Такое количество феррита не требует специального повышения температуры нагрева для выравнивания концентрации углерода в аустените. Однако и в этом случае в закаленной структуре трудно избежать появления отдельных участков остаточного ауетенита, количество которых до 5—10% можно допустить без ущерба для качества закалки.
При наличии феррита больше 10% практически исключается возможность применения поверхностной закалки. Гомогенизация аустенита у серого чугуна с такой структурой достигается при повышенной температуре, зависящей от скорости нагрева. Применение сравнительно больших скоростей нагрева неизбежно при поверхностной закалке, поэтому и температура нагрева должна быть высокой. Это приводит к опасности образования трещин. Последнее усугубляется еще тем, что в чугуне с повышенным количеством феррита часто наблюдается неблагоприятное распределение графитовых включений (междендритный или сетчатый графит), что, в свою очередь, способствует возникновению трещин при быстром нагреве и охлаждении. Нежелательной является также розеточная форма графита. Скопления графитных включений в виде розеток обычно располагаются на фоне феррита. При закалке в этих местах образуются мягкие пятна.
Так как структура серого чугуна в значительной мере зависит от размеров изделия и условий изготовления отливки, трудно заранее точно определить нужный химический состав. Для большинства деталей машиностроения, имеющих сравнительно небольшие размеры, суммарное содержание углерода и кремния должно быть в пределах 4,7—5,5%. В этом случае обеспечивается получение необходимой структуры металлической основы. Количество связанного углерода не должно быть меньше 0,6%.
Качество произведенной термической обработки характеризует распределение твердости по сечению закаленного слоя, полученное при замере микротвердости металлической основы. Усредненная твердость с учетом влияния графитовых включений значительно ниже: обычно она составляет 44—52 HRQв зависимости от количества, формы и величины графитовых включений. Крупные хлопья графита наиболее сильно снижают значения усредненной твердости.
Структура высокопрочного чугуна отличается от структуры обычного серого чугуна характером графитовых включений, которые имеют глобулярную форму. Это обусловливает меньшую склонность такого чугуна к растрескиванию при термической обработке: допустимы более высокие температуры и большие скорости охлаждения, чем при закалке обычного литейного чугуна. Феррит в исходной структуре металлической основы высокопрочного чугуна окаймляет графитовые включения. При нагреве под закалку насыщение ферритных участков происходит не только за счет углерода аустенита, но и за счет включений графита. В переходной зоне, где закалка неполная, включения графита окаймляются сначала слоем мартенсита, а затем феррита. В закаленном слое мартенсит имеет безыгольчатое или мелкоигольчатое строение. Усредненная твердость закаленного высокопрочного чугуна обычно находится в пределах 52—57 HRC3.
При закалке деталей сложной формы из серого и высокопрочного чугуна встречаются затруднения. Местные чрезмерные перегревы в выточках, вблизи отверстий, в топких сечениях и т. п. неизбежно приводят к образованию трещин и даже к оплавлению кромок. Технология изготовления таких деталей строится с учетом этих особенностей.
Закалка ферритного и ферритно-перлитного чугуна. Из ферритных и ферритно-перлитных чугунов закалке с применением высокочастотного нагрева подвергаются ковкий и высокопрочный чугун.
Для получения высокой твердости закаленного слоя в твердом растворе необходимо иметь около 0,45—0,6% С. Поэтому в процессе нагрева добиваются растворения свободного графита в аустените и образования в железе твердого раствора углерода нужной концентрации. Благодаря округленной и гнездообразной форме графита в высокопрочном и ковком чугуне снижается склонность к образованию трещин при закалке. Это дает возможность осуществлять закалку таких сортов чугуна от повышенных температур и позволяет иметь в исходной структуре металлической основы повышенное количество феррита. Отметим, что, несмотря на округленную форму графита, высокопрочный чугун все же склонен к образованию закалочных трещин. Наличие в структуре фосфидной эвтектики — твердой и хрупкой составляющей с низкой температурой плавления — повышает опасность образования трещин. Содержание фосфора свыше 0,2% следует считать недопустимым.
При поверхностной закалке ферритного чугуна для растворения необходимого количества графита требуются высокие температуры, близкие к температурам начала плавления чугуна. Такой нагрев неизбежно приводит к значительной неравномерности концентрации углерода в металлической основе и скоплению масс остаточного аустенита возле включений графита. Для того чтобы уменьшить возможность образования структуры с большим количеством остаточного аустенита, а значит, иметь равномерное распределение углерода в твердом растворе нужной концентрации, приходится уменьшать скорость нагрева. Это, по существу, приводит к невозможности получения у деталей из ферритного чугуна небольших слоев поверхностной закалки — прогрев производится на относительно большую глубину.