Выплавка чугуна в мощных доменных печах
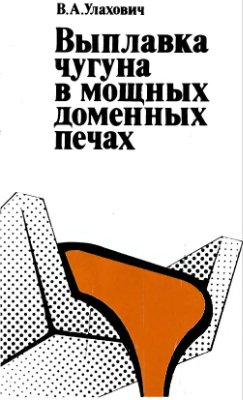
Улахович В.А.
Металлургия, 1991 г.
ОСВОЕНИЕ РАБОТЫ КРУПНЕЙШЕГО АГЛОМЕРАТА ПО ВЫПЛАВКЕ ЧУГУНА
Технологию выплавки чугуна на мощной доменной печи в значительной мере определял, требования конвертерного производства к его качеству. Первоначально в проекте закладывали требования по повышенному содержанию марганца в чугуне, что базировалось на существовавших в то время представлениях о необходимости поддержания его концентрации в чугуне на уровне 0,6-1,0 %.
Однако проведенные исследования [29] показали, что выплавка марганцовистого чугуна связана с большими потерями в аглодомен- ном производстве, которые не компенсируются улучшением показателей конвертерной плавки. В связи с применением мощных миксеровозов (600-т) и сохранением физического нагрева чугуна появилась возможность отработки технологии выплавки конвертерной стали из низкомарганцовистого чугуна (с содержанием марганца 0,15- 0,25 %). Доменные печи комбината выплавляли чугун с естественным содержанием марганца 0,20-0,25 %. Для повышения его концентрации в чугуне ввиду дефицита богатого марганцевого сырья были предложены бедные марганцевые руды, в частности чиатурская марганцевая руда IV сорта с содержанием марганца ~ 20 %.
Анализ показал, что предложенная марганцевая руда по своим физическим свойствам непригодна для ввода в доменную шихту из-за большого количества мелких частиц, поэтому ее вводили в агломерационную шихту. Доля марганцевой руды в железорудной части аглошихты в опытных спеканиях составила 4 %. Содержание марганца в агломерате при ее вводе в шихту повысилась с 0,17 до 0,72 %. Наличие в руде большого количества крупной фракции (до 20 % фракции > 8 мм) и кремнезема (от 23 до 39 %), а также повышенная ее влажность (до 12-15 %) и изменение свойств (в том числе химического состава) неблагоприятного отразилось на качестве агломерата: содержание железа снизилось почти на 2 %, ухудшилась прочность агломерата и возросли колебания химического состава.
Опытные плавки провели на доменной печи № 4 2700 м3 [77]. Содержание марганца в чугуне возросло с 0,22 до 0,65 %. При работе на марганцовистом агломерате производительность печи уменьшилась на 2,4 %, а расход кокса возрос на 13 кг/т чугуна, увеличились колебания химического состава чугуна, особенно по содержанию серы и марганца. Установлено, что использование в агломерационной шихте бедной марганцевой руды значительно ухудшает не только показатели работы печи, но и качество чугуна. Это объясняется, помимо затрат тепла на восстановление марганца, резким снижением содержания железа в агломерате, а также ухудшением качества агломерата по прочности и стабильности химического состава. При этом ~ 30 % Мп теряется со шлаком в виде его закиси. Исследования показали, что по своим свойствам агломерат, полученный с использованием марганцевой руды, не пригоден для мощной доменной печи, а качество чугуна по колебанию химического состава не удовлетворяет требованиям конвертерного производства. На основании полученных данных пришли к выводу о необходимости разработки технологии и освоении выплавки конвертерной стали из низкомарганцовистого чугуна с предъявлением повышенных требований по физическому нагреву.
С целью сохранения физического тепла чугуна и своевременного обеспечения им мощных конвертеров для его транспортировки применили большегрузные передвижные миксеры вместимостью 600 т, что позволило уменьшить понижение температуры за время транспортировки вдвое. Кроме того, для удовлетворения требований сталеплавильщиков разработали технологию, обеспечивающую повышенный физический нагрев чугуна на выпуске из печи (до 1500-1520 Ό, что было достигнуто путем уменьшения высокотемпературных свойств железорудного сырья, оптимизацией шлакового режима и параметров комбинированного дутья. На основании всестороннего исследования шлакового режима установили, что лучшей десульфурационной способностью и жидкотекучестью, а также устойчивостью обладают шлаки с содержанием 10-11 % MgO и CaO/Si02 = ~ 1,05 при естественном содержании 8-10 % Al2O3. Такие шлаки обеспечивают достаточный физический прогрев продуктов плавки. Результаты исследований использовали при подборе шлакового режима доменной печи № 5.
С пуском мощной доменной печи сырьевые условия на комбинате значительно изменились. Ранее доменные печи работали в основном на местном агломерате основностью 1,15-1,35 (при доле магнезиального ковдорского концентрата в агломерационной шихте 30-35 %) с небольшими добавками привозных окатышей и кусковой руды. С вводом печи резко возрос дефицит подготовленного железорудного сырья, который стал покрываться окатышами Костомукшского ГОК основностью 0,5. Более качественный агломерат агломерационного цеха № 3 направили на доменную печь № 5, при этом доля окатышей составила 30-35 %.
Введение в доменную шихту частично офлюсованных окатышей с немагнезиальной пустой породой потребовало повышения основности агломерата и доли ковдорского концентрата в аглошихте для сохранения оптимального шлакового режима. В настоящее время основность агломерата составляет 1,4-1,5 при основности костомукшских окатышей ~ 0,8. В качестве кислого флюса, а также добавки при нехватке подготовленного сырья используют криворожскую кусковую руду класса К. Химический состав железорудных материалов приведен в табл.14.
Для приема и хранения окатышей построили в комплексе доменной печи № 5 и ввели в эксплуатацию механизированный склад с транспортерной подачей окатышей на доменные печи 4 и 5, а также тракт подачи окатышей на доменные печи 1-3. Реконструировали бункерную эстакаду этих печей с установкой третьего конвейера. Проведенные реконструированные мероприятия позволили создать надежную технологическую схему по обеспечению существующих доменных печей окатышами. Большой объем реконструктивных работ в сжатые сроки выполнили на Костомукшском ГОК по повышению основности окатышей с 0,5 до 0,8 и богатства железорудного концентрата с 65,7 до 67,5 %. При этом, что особенно важно, основность окатышей повысили в основном за счет снижения кремнезема в концентрате. Необходимость повышения основности окатышей обусловлена не только ограничением возможностей увеличения основности агломерата, а, главным образом, улучшением их высокотемпературных свойств. Этому способствовало и снижение в них содержания SiC>2. Так, в окатышах основностью 0,5, концентрация кремнезема составляла 7,5- 8,0 %, а при основности 0,8-0,9 она снизилась до 5,0-6,0 %. Большое внимание уделяли подбору режимов обжига окатышей с целью более эффективной десульфурации, так как в связи с минералогическими особенностями железорудного сырья десульфурация протекает медленно и в окатышах содержится повышенное содержание серы. Несмотря на увеличение основности концентрацию серы удалось сохранить на прежнем уровне (0,07-0,08 %).
Оценили также содержание щелочей в окатышах, так как известно, что с повышением основности пустой породы щелочи меньше связываются кремнеземом и больше участвуют в циркуляционных процессах в доменной печи. Для мощной доменной печи этот вопрос представляет особый интерес в связи с отрицательным влиянием щелочи, как агрессивного вещества, в отношении кокса (повышает его реакционную способность и снижает прочность). Кроме того, щелочи ухудшают газопроницаемость шихтовых материалов. Из табл. 14 видно, что концентрация щелочей в окатышах примерно в 1,3 раза выше, чем в агломерате. Это обусловило увеличение их поступления в доменную печь. В табл. 15 приведен батане щелочей для условий работы доменной печи № 5. Приход щелочей составил 3,14 кг/т чугуна, что не превышает общепринятых критических значений (5,0-5,5 кг/т чугуна) , при превышении которых негативное воздействие щелочей на процесс становится ощутимым.
Анализ свойств агломерата при восстановительной обработке показал, что наиболее устойчивая шлаковая связка у агломерата с основностью 1,20-1,35. С целью уменьшения разупрочнения агломерата при повышении его основности оптимизировали температурно-тепловой уровень процесса спекания.
Наряду с высокотемпературными характеристиками большое внимание уделяли физико-механическим свойствам железорудных материалов в холодном состоянии, в значительной мере определяющих распределение их на колошнике доменной печи и газодинамический режим. В современном производстве при транспортерной подаче сырья к доменным печам часть операций по формированию свойств шихтовых материалов может выполняться на конвейерном тракте с перегрузочными узлами. В связи с этим при разработке технологии оптимизация металлургических свойств доменного сырья по фракции и прочности выполняли с учетом стабилизирующих нагрузок на трактах подачи.
Выполненные исследования показали, что снижение верхнего предела фракции скипового агломерата до 40-25 мм обеспечивает наилучшие прочностные свойства его насыпной массы. Разрушаемость такого агломерата в доменной печи при восстановительно-тепловой обработке также минимальная. Рациональное сочетание операций дробления и грохочения на агломерационной фабрике с механической обработкой на тракте и отсевом мелочи непосредственно на печи обеспечило снижение верхнего предела его фракции до 25-40 мм при одновременной стабилизации агломерата. Несмотря на относительно высокое содержание мелочи в скиповом агломерате (10-20 %) мощная доменная печь работает форсированно, что свидетельствует о стабилизации прочностных характеристик агломерата в процессе транспортировки и минимальном его разрушении при загрузке и опускании в печи. Повышенное содержание мелочи в скиповом агломерате связано с недостаточной эффективностью грохочения грохотов ГОСТ-62 из-за ненадежной их конструкции (которая постоянно совершенствовалась) и наличия в бункерном агломерате большого количества мелочи.